In the manufacturing, sale, purchase, or transfer of petroleum products, knowledge of the water content in lubricating oils, additives and similar products is crucial to estimate their performance and quality.
The presence of moisture in lubricating oils could result in premature corrosion and engine wear while increasing the debris load, leading to diminished lubrication and premature plugging of filters.
Moisture can also hamper the influence of additives and encourage the growth of deleterious bacterial organisms. Knowing about the water content can ensure safe operation and prevent damage to infrastructure.
This article outlines the easy determination of moisture in petroleum samples by coulometric Karl Fischer titration according to the three procedures outlined in ASTM Method D6304. A comparison between the procedures is supplied to establish which procedure is most suitable for different sample types.
Moisture Determination According to ASTM D6304
ASTM Method D6304 is made up of three procedures for establishing moisture in petroleum samples by coulometric Karl Fischer titration. Procedure A details a direct injection where a measured quantity of the sample is directly introduced into the coulometric Karl Fischer titration cell.
For samples that do not interfere with the Karl Fischer reaction but are soluble in the titration solvent, this procedure is recommended.
In order to analyze samples that do not readily dissolve in Karl Fischer reagent, including samples with components that are expected to interfere with the Karl Fischer reaction or viscous samples, Procedures B and C can be utilized.
Additionally, Procedures B and C can be employed to establish water content in samples that can also be analyzed by Procedure A. The sample is heated in a closed system to release moisture in both Procedures B and C, which is transferred to the coulometric Karl Fischer cell via an inert carrier gas and titrated.
The table below (Table 1) shows a comparison between the different procedures.
Table 1. Comparison of the different ASTM D6304 procedures. Source: Metrohm AG
Factor |
Procedure A |
Procedure B |
Procedure C |
Analysis technique |
Direct injection |
Oven evaporator |
Water evaporator |
Required sample
solubility in KF reagent |
Good |
Independent |
Independent |
Suitable for samples
with matrix interference |
No |
Yes |
Yes |
Automation possibility |
No |
Yes |
No |
Automatic reagent exchange |
Yes |
Yes |
Only titration cell |
Reagent exchange frequency |
When phase separation occurs, KF reagents are exhausted, or when sample represents ¼ of the volume in the cell |
When KF reagents are exhausted |
When KF reagents are exhausted |
Sample type |
Liquid samples e.g., diesel fuel, aromatics, jet fuel |
All petrochemical samples with thermal decomposition >100 °C |
All petrochemical samples with thermal decomposition >90 °C |
Sampling
For precise and accurate water determinations, gathering a representative product sample for moisture analysis is vital. Sample collection should be carried out according to ASTM Practices D4057 and D4177 and handled and mixed in accordance with Practice D5854.
During sample collection and analysis, care must be used to avoid moisture contamination coming from the sample container, the atmosphere, or transfer equipment.
When the solubility limit is exceeded, water in hydrocarbon samples can readily separate into two phases. The water solubility is dependent on the water concentration, sample matrix and temperature.
Before withdrawing an aliquot from the sample, container samples must be mixed thoroughly. The sample is unsuitable for testing the water content if phase separation happens after mixing. In order to minimize any water separation, samples should be analyzed for moisture straight after mixing or homogenizing.
The analyst should either utilize the complete portion of the test specimen for the analysis or dispose of the excess once a sample is taken from the original container. To avoid sample contamination, the portion that was removed from the sample container should not be put back into the original sample container.
Direct Injection (Procedure A)
For low viscosity samples without expected interferences, like aromatics, diesel fuel, or jet fuel, the direct sample injection into the titration cell (Procedure A) is recommended.
An aliquot of known volume or mass is injected into the conditioned titration cell of a coulometric Karl Fischer apparatus, where it is automatically titrated and the results should be calculated as volume or mass percent.
Technique D6304 allows the utilization of coulometric generator electrodes with and without diaphragm, as seen in Figure 1. The titration cell is conditioned prior to titration of the sample. This ensures that no environmental moisture is present within the titration cell before titration.
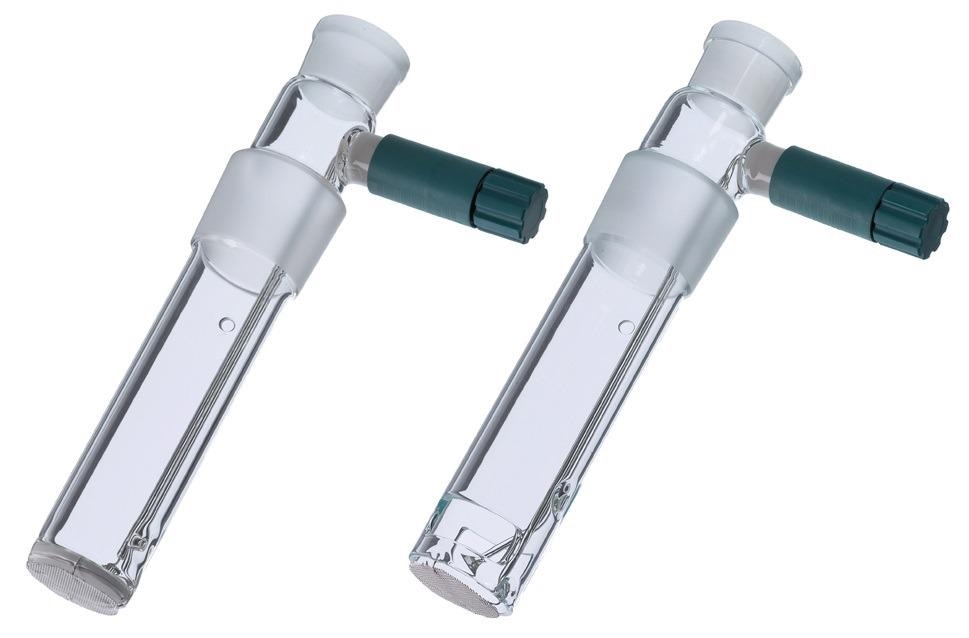
Figure 1. Coulometric Karl Fischer Generator electrode with diaphragm (left) and without diaphragm (right). Image Credit: Metrohm AG
Conditioning, or titrating the titration cell to dryness, is performed while stirring. This conditioning step must be performed prior to each determination. The titration can start when the titration system is conditioned.
It is necessary to rinse the syringe with each new sample one or two times prior to injecting into the titration cell in order to acquire good precision. To achieve this, a small amount of sample is aspirated into the syringe and discarded again. This procedure ensures the removal of any water adhering to the syringe.
Next, a sample for the analysis is aspirated into the same syringe and weighed on the balance. An appropriate amount of sample which contains at least 50 µg water is injected into the titration cell and the syringe is weighed again to establish the exact sample size.
To introduce the sample into the Karl Fischer cell, Disposable syringes may be employed if there is no interaction between the sample and the syringe material. A disposable syringe should be employed for each sample.
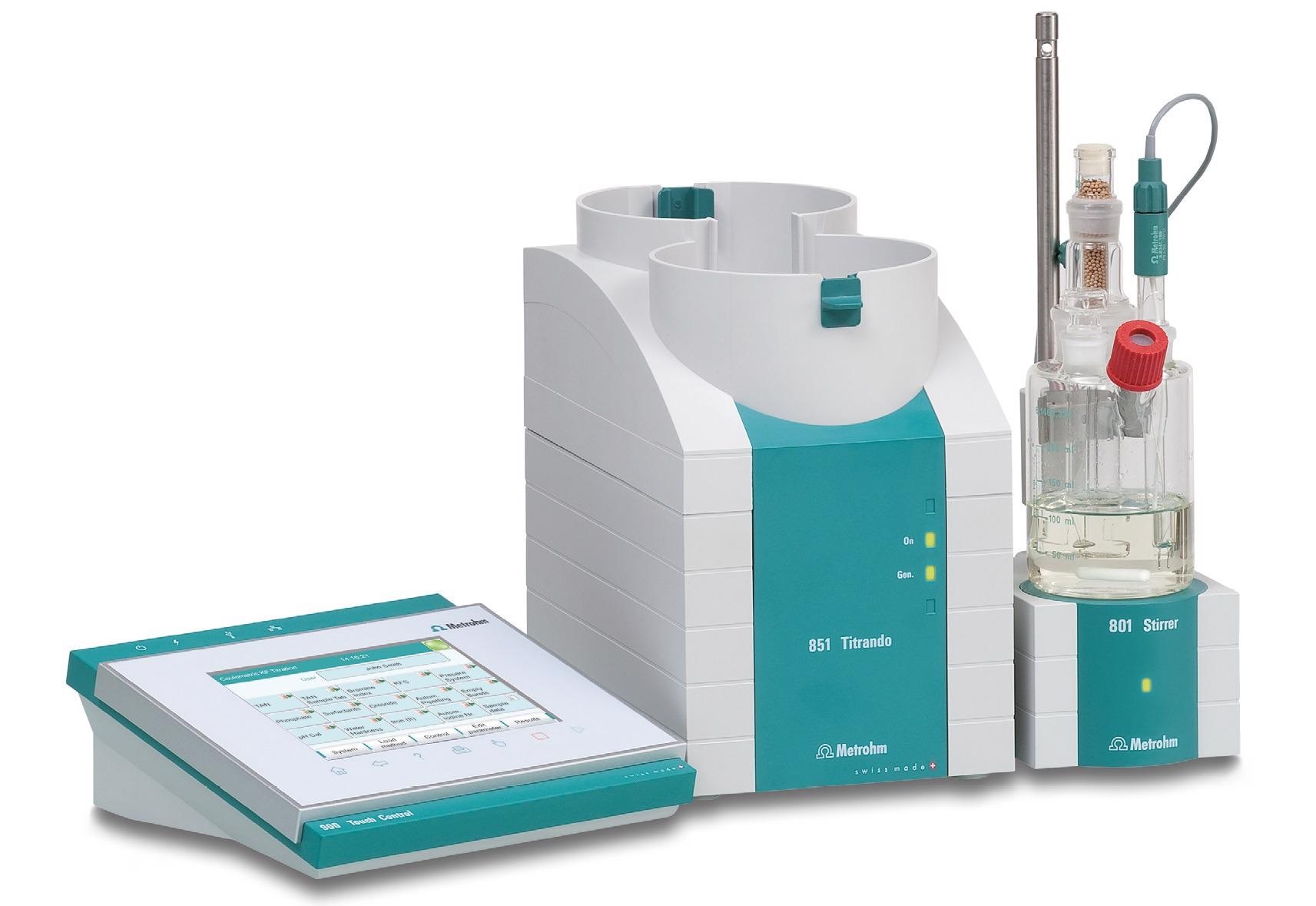
Figure 2. A coulometric Karl Fischer titration system suitable for ASTM D6304 Procedure A. Image Credit: Metrohm AG
It is crucial to inspect the titration cell when utilizing direct injection. This is to ensure the sample does not separate into layers and is properly dissolved.
The volume of Karl Fischer reagent, the volume and type of sample material injected and the sample solubility in the reagent all dictate the number of samples which can be analyzed without phase separation.
A good rule to use is that the reagent in the anode compartment should be exchanged when the volume of sample injected into the cell is higher than 1/4 of the total volume in the titration cell. Depending on the sample composition, Karl Fischer reagents may be altered with toluene or other solvents.
Most reagent manufacturers outline acceptable solvents and the volume which can be added to the anode solution to ensure the release of all moisture and to enhance sample solubility, stopping contamination of the Karl Fischer cell.
Samples that may need a co-solvent to enhance solubility usually also contribute to clogging or coating the diaphragm of the generator electrode. Procedures B and C of ASTM D6304 should be used to analyze these sample types.
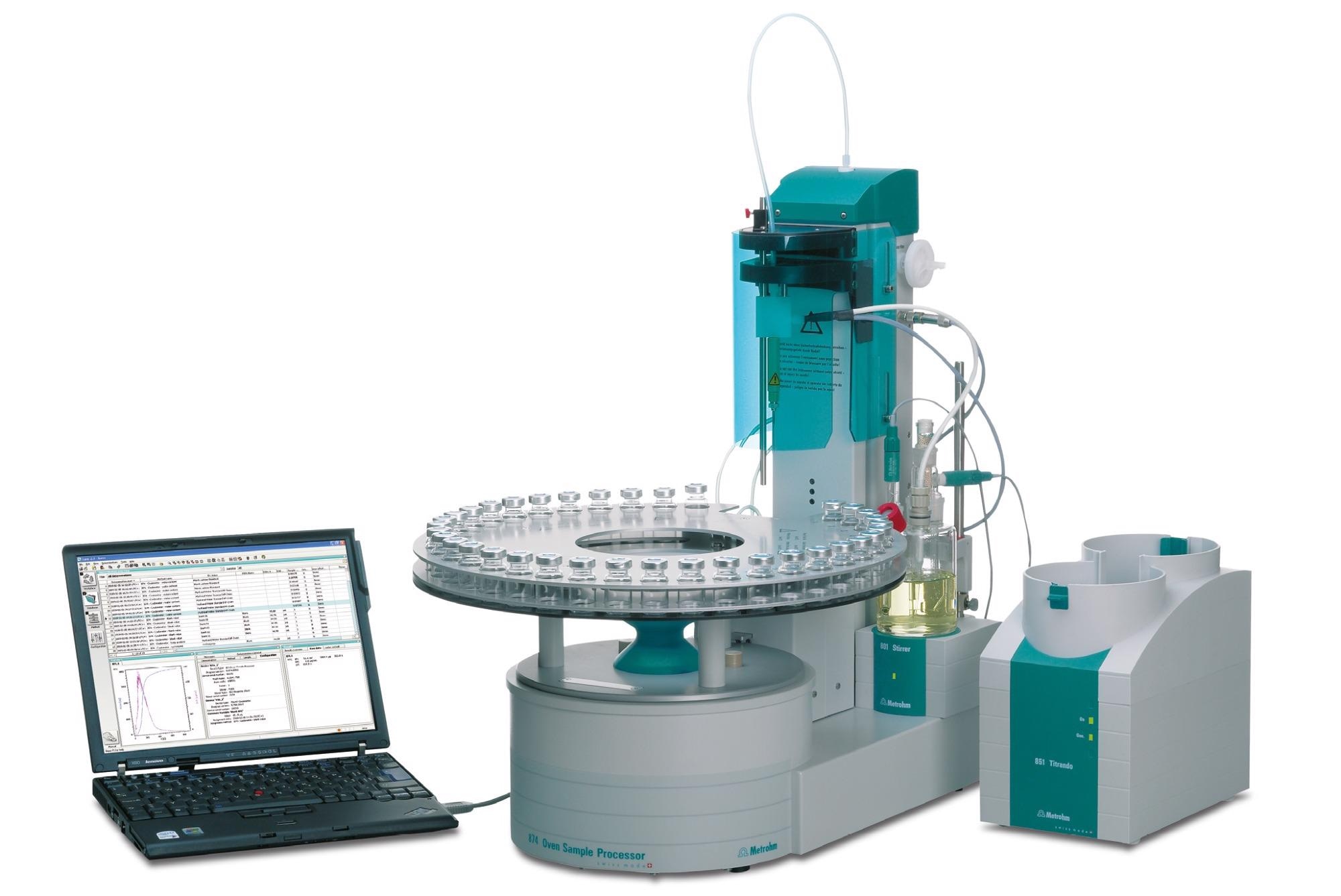
Figure 3. An oven evaporator with a coulometric Karl Fischer titration system suitable for ASTM D6304 Procedure B. Image Credit: Metrohm AG
Evaporation Techniques (Procedures B & C)
An oven (Procedure B) or water evaporator accessory (Procedure C) can be employed to analyze samples that do not readily dissolve in Karl Fischer reagent, samples with components that are expected to interfere with the Karl Fischer reaction and viscous samples.
Oven Evaporator (Procedure B)
The oven evaporator is an auxiliary device that heats the sample in a heating chamber. The water in the sample vaporizes and is carried off by a dry non-reactive (inert) carrier gas via a heated tube into the Karl Fischer titration cell.
The vaporized water is titrated there while the sample and contaminants stay in the sample vial. The Metrohm 860 KF Thermoprep, 874 Oven Sample Processor and 885 Compact Oven Sample Changer can be used for ASTM D6304 Procedure B.
The 874 Oven Sample Processor is able to carry out a temperature gradient test to establish the best temperature for removing water without degrading the sample.
In the Appendix of test technique ASTM D6304, a detailed description to help with the selection of the appropriate temperature can be seen.
In Procedure B (Figure 4), to extract any water present into the headspace of the vial, a representative portion of the sample is placed into a sealed glass vial and heated in an oven.
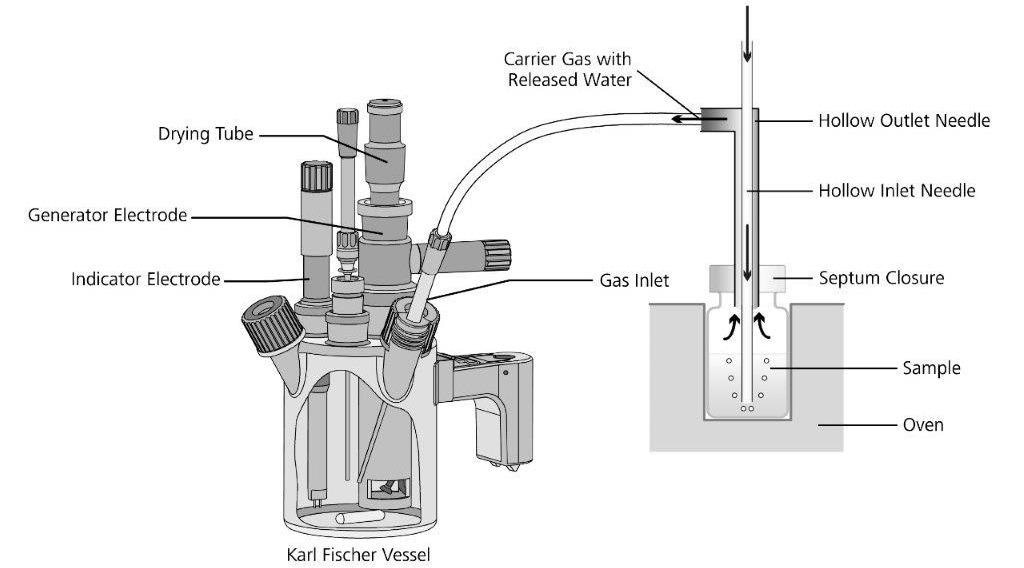
Figure 4. Operating principle of the oven evaporation technique. Image Credit: Metrohm AG
Next, the vaporized water in the headspace is carried into the conditioned Karl Fischer titration cell via a dry carrier gas where it is titrated.
Conditioning of the titration cell is needed to remove any ambient moisture within the system, as with Procedure A. Conditioning or titrating the titration cell to dryness is performed under stirring in the so-called conditioning position. Before every determination, this step must be performed.
Initially, the oven is heated up to the defined temperature. The first measurement can begin after this temperature is reached and the titration system is conditioned. A blank value is established by utilizing empty sample vials prior to a titration series.
This is necessary because the sample vial also contains atmospheric humidity in addition to the water in the sample. In the calculation of the water content, the blank value is considered (subtracted).
It could be necessary to correct the blank value by employing a relative blank for the sample determination if large sample sizes are utilized.
The dried carrier gas is passed through the sample vial and transfers the released water into the titration cell for the sample analysis.
According to the temperature stability of the sample, the oven temperature may be varied. The optimal sample size is dependent on the water content of the sample.
The absolute amount of water transferred to the titration vessel should be in the range of 300–5000 μg. If the absolute amount of water for a sample cannot be decreased (e.g., smaller sample size), also larger amounts of water (>5000 μg) can be established by utilizing the oven method.
A co-solvent may be employed for samples that do not release their water readily, like crude oil. Co-solvents like toluene enhance water extraction from the sample, leading to higher reproducibility and faster analysis time.
It is necessary to fill the sample vials utilized for blank determination with the same amount of co-solvent as employed for the sample determination in instances where a co-solvent is employed. The carrier gas transports the released water into the titration cell. So, the gas which is utilized is not very important.
Yet, the thermal stability of organic substances at higher temperatures is usually poor when using dry air as carrier gas because of reactions with oxygen. Inert gases, e.g., nitrogen, provide more reliability and flexibility.
Measurements in liquid samples (fuel, oil, solvents) should be performed by utilizing gas flow rates of 80 mL/min or higher. It is also recommended that the inlet needle is immersed in the sample and the gas is permitted to flow through the sample.
Water Evaporator (Procedure C)
During the water evaporator procedure, an aliquot of sample is transferred into a heated chamber that contains toluene (Figure 5). The water vaporizes together with toluene in an azeotrope distillation. The azeotrope vaporizes and is transferred into the Karl Fischer titration cell via a dry non-reactive carrier gas.
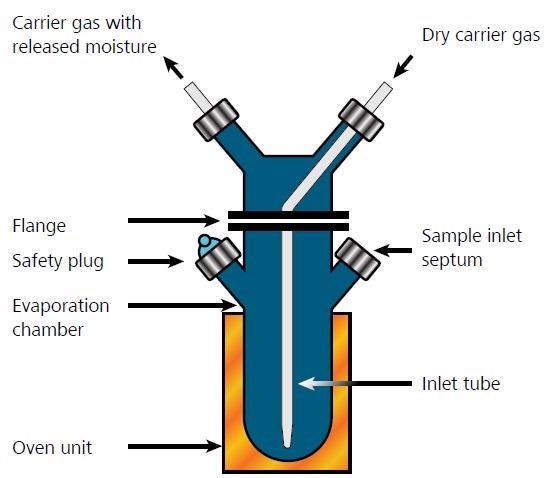
Figure 5. Operating principle of oil evaporator. Image Credit: Metrohm AG
Conditioning of the titration cell is needed to remove any residual moisture within the system, as with Procedures A and B. This conditioning step must be performed prior to each determination.
The first measurement can begin once the oven is heated up to a defined temperature and the titration system is conditioned. For the sample analysis, the dried carrier gas is passed through the distillation chamber and transfers the azeotrope into the titration cell. The temperature of the oven is set depending on the solvent employed.
The carrier gas transports the azeotrope into the titration cell. As with Procedure B, the gas which is employed is not very important. Although, as the oxygen content of dry air can negatively influence the thermal stability of organic substances at a higher temperature, inert gases (e.g., nitrogen) provide more reliability and flexibility.
Procedure A, B, Or C? Comparison of Pros and Cons
All three procedures that have been outlined above have benefits and drawbacks. This section looks at the performance of the three procedures under the aspects mentioned in Table 1.
Sample Solubility Influences Cleaning Frequency
The frequency of reagent exchange and cleaning of the Karl Fischer titration cell is directly influenced by the solubility of the sample in Karl Fischer reagents. Phase separation within the cell will occur if samples are not soluble in Karl Fischer reagents.
The Karl Fischer reagent must be replaced if this happens.
In order to remove sample buildup or undesirable coatings, occasional cleaning of the electrodes and cell may be needed. Due to the time required to dry the cell fully and remove moisture from newly added Karl Fischer reagents, the reagent exchange and cleaning can be time-consuming.
Poorly soluble materials may need more frequent reagent exchange, which can result in more chemical usage and costs. Therefore, Procedure A is only recommended for samples that have an acceptable solubility within Karl Fischer reagents, like aromatics or jet and diesel fuels.
Procedures B and C are more suitable for heavier distillates, crude oil samples and lubricants, which have limited solubility in Karl Fischer reagents, as they are independent of sample solubility and cell contamination is decreased greatly.
Only the evaporated water together with the carrier gas is transferred into the titration cell, so phase separation can no longer happen and the frequency of reagent exchange is reduced greatly. This leads to a lower cost per analysis and higher efficiency.
Matrix Interference and Side Reactions
Additives in lubricants and base oils in the sample or even the sample itself may be subject to side-reactions with the Karl Fischer reagents.
Direct injection into the titration cell according to Procedure A may lead to an apparent higher water content from side reactions for these samples.
The sample does not come into contact with the Karl Fischer reagent in Procedures B and C, so both procedures are unaffected by possible matrix interferences. These procedures can supply more reliable results for samples that cause side reactions or matrix interferences.
Automation for Efficiency and Lower Costs Per Analysis
Modern laboratory analysts are tasked with carrying out a number of different tests. If the operator has to spend a lot of time on a single analysis and is bound to the system, lab efficiency decreases and affects operating costs.
Procedure B can be fully automated by utilizing the 874 Oven Sample Processor. The analyst simply weighs the samples into the sample vials, seals them tightly, places them on the sample rack and starts the analysis series. So Procedure B provides simple, walk-away automation.
Automated Reagent Exchange Decreases Instrument Down Time
The titration cell is contaminated when phase separation happens, or the Karl Fischer reagent is exhausted, so it is necessary to exchange the reagent within the titration cell. Opening the Karl Fischer cell for reagent exchange introduces moisture into the titration cell, which has to be titrated prior to introducing a sample.
Automated reagent exchange takes away the depleted reagent and replaces it with a new reagent without opening the KF cell. This decreases the amount of time required to dry the titration cell before sample addition greatly and minimizes user exposure to reagents.
Although it is possible to automatically exchange the reagents in the titration cell, for Procedure C, the evaporation chamber has to be manually emptied.
Summary
According to ASTM D6304, the ideal procedure for moisture determination is strongly dependent on the sample. When selecting the right procedure, the sample viscosity and matrix are crucial. Procedure A is the best option for a sample with low viscosity, such as jet fuel or aromatics.
An efficient moisture determination can be performed by utilizing a Metrohm 851 Titrando with the equipment for the automatic reagent exchange. Procedures B and C are the solutions for samples that are not suitable for Procedure A, like lubricants with additives or base oil.
Compared to Procedure C, Procedure B has the benefit that no cleaning of the evaporation chamber is needed. Procedure B can also be fully automated, supplying a simple walk-away solution for the determination of moisture.
It is possible to analyze samples according to Procedure B fully automatically by utilizing an 874 Oven Sample Processor combined with an 851 Titrando. It is also still possible to analyze samples by a direct injection according to Procedure A with the 851 Titrando alone. This enables the user to employ the system with maximal flexibility.
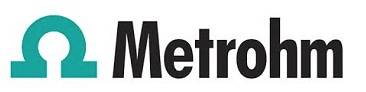
This information has been sourced, reviewed and adapted from materials provided by Metrohm AG.
For more information on this source, please visit Metrohm AG.