Diaphragm pumps are positive displacement pumps that employ displacement chambers or contracting and expanding cavities to move fluids via a flexing or reciprocating diaphragm.
Basic diaphragm pumps are comprised of a diaphragm, displacement chamber, a driving mechanism and two valves, though current industrial diaphragm pumps may utilize multiple chambers and numerous diaphragms.
Diaphragms are composed of a flexible or elastomeric material that is held in place between an attached flange and the displacement chamber holding the fluid, or between the displacement chamber and a secondary chamber which holds a driving fluid such as hydraulic oil or air.
The displacement chamber features two check valves designed to allow flow in from the intake and out from the exhaust port. These check valves are flapper valves or spring-loaded ball valves and will typically be made from an identical material to the diaphragm.
Diaphragm pumps push fluid out of the displacement chamber by flexing the diaphragm via a drive mechanism, for example, hydraulic fluid, air pressure, reciprocating piston or solenoid.
As the diaphragm flexes, it causes alternating pressure increases and decreases in the chamber, moving media into and out of the diaphragm pump.
The use of diaphragm pumps continues to increase due to their high reliability versus alternative pump types. Diaphragm pumps contain a relatively small number of moving parts, no shafts or bearings requiring sealing from the media, and no parts in sliding contact.
There is no need to use sealing or lubricating oils with diaphragm pumps, meaning that there is no risk of oil vapors leaking into and contaminating pumped media. Moreover, as they do not use oil, they typically are seal-free, which helps to minimize cleaning requirements and maintenance downtime.
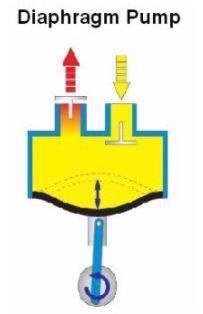
Figure 1. Schematic of a mechanically driven diaphragm pump. Image Credit: NASA
Diaphragm pumps are able to handle liquids, gases, slurries or gas-liquid mixtures via a reciprocating diaphragm, but the material selected for the diaphragm material must be inert – or at least chemically resistant - to the media being pumped.
Diaphragm pumps can transport media that is thin to highly viscous, with even abrasive slurries posing minimum issues because the diaphragm isolates the media from the pump’s internal mechanisms.
These factors have helped diaphragm pumps become a key process tool in industries working with paints, coatings, pigments, colorants, foods, beverages, chemicals, adhesives, pharmaceuticals, wastewater and biological materials such as blood, plasma and cells.
Flexible Membrane Performance and Less Unplanned Maintenance
Having a better understanding of the diaphragm’s performance requirements and stresses can help in choosing the optimal material to increase pump reliability, effectiveness and life.
Diaphragm membranes are typically required to withstand millions to tens of millions of flex cycles, so materials offering long flex life are key to ensuring predictable performance. This enables users to better plan scheduled maintenance shutdowns and eventual membrane replacement.
The use of diaphragm materials with shorter flex lives will likely result in pump failure, triggering costly unplanned shutdowns.
Pump failure has the potential to cause a host of problems downstream in a production plant.
For example, sudden loss of fluid flow may cause damage to valuable capital equipment in chemical process plants, paper mills, pharmaceutical factories, power generation facilities and semiconductor wafer fabrication sites. There is also the potential for the loss of a full production batch.
Repairing or replacing highly specialized production equipment may take days or even weeks, leading to further production losses.
The long life and high durability of CHEMFILM® flexible barrier materials have been found to extend the mean time between required maintenance cycles, therefore reducing the need for unplanned shutdowns.
Ensuring Smoother Flow
Ensuring reduced pulsations and smooth flow is a key factor in certain diaphragm pump applications, for instance, the precision dispensing and metering of coatings, adhesives, dyes, lubricants or active pharmaceutical ingredients.
A number of pump OEMs recommend the use of pulsation dampeners in order to better manage pulsing and surging. It is possible to reduce the intensity of pulsations and attain a more continuous flow with an increased number of smaller displacement diaphragm flex cycles per unit time.
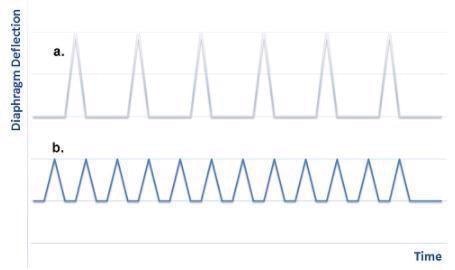
Figure 2. A higher flex life material enables increased diaphragm flex frequency in (b.). which can reduce pulsation to provide smoother flow compared to lower-frequency flex cycles in (a.). Image Credit: IEEE GlobalSpec
It is important to note, however, that this increased number of flex cycles necessitates the use of a material with even higher flex life performance properties versus conventional diaphragm materials.
Electric-operated diaphragm pumps employ a small electric motor and cam setup to reciprocate a piston and flex the diaphragm.
These devices are therefore able to generate higher cycling and reduced pulsation in comparison with pumps driven by pneumatic or hydraulic fluids. These applications can benefit considerably from the installation of a high flex life diaphragm barrier.
Facilitating Easier Cleaning
It is important to consider a pump’s ease of cleaning and its non-stick characteristics when working with production lines that run a range of chemicals, coatings, pigments or drugs on the same line.
These lines must be purged of media or cleaned in order to prevent cross-contamination.
The use of Flex Barriers with low surface energy can prevent media from sticking or chemically bonding, allowing users to employ more efficient clean-in-place procedures.
Flex Barriers offering high smoothness coupled with crack and void-free surfaces ensure more straightforward and faster maintenance due to fewer surface inhomogeneities (cavities or protuberances) where dirt or media may lodge or otherwise build up.
Enhancing material smoothness will also prompt a reduction in the coefficient of friction, further improving pump cleanliness and flow.
Abrasion resistance is key in applications pumping pastes, slurries, grease or pigment-filled resins or paints. It is also vital that the diaphragm material offers excellent chemical resistance to acidic, alkaline and solvent media.
Reducing Dangerous Diaphragm Leaks
Permeability should be considered when choosing an appropriate Flex Barrier for a pump diaphragm. Depending on the thickness, density or chemical nature of the flex film, vapors may permeate or otherwise pass through a pump diaphragm.
Corrosive or toxic chemicals dissolved in the media could leak into the hydraulic system or surrounding air, posing a considerable hazard to staff and equipment.
Diaphragm pumps and diaphragm valves are considered to be ‘leakless’ under EPA Leak Detection and Repair (LDAR) guidelines.
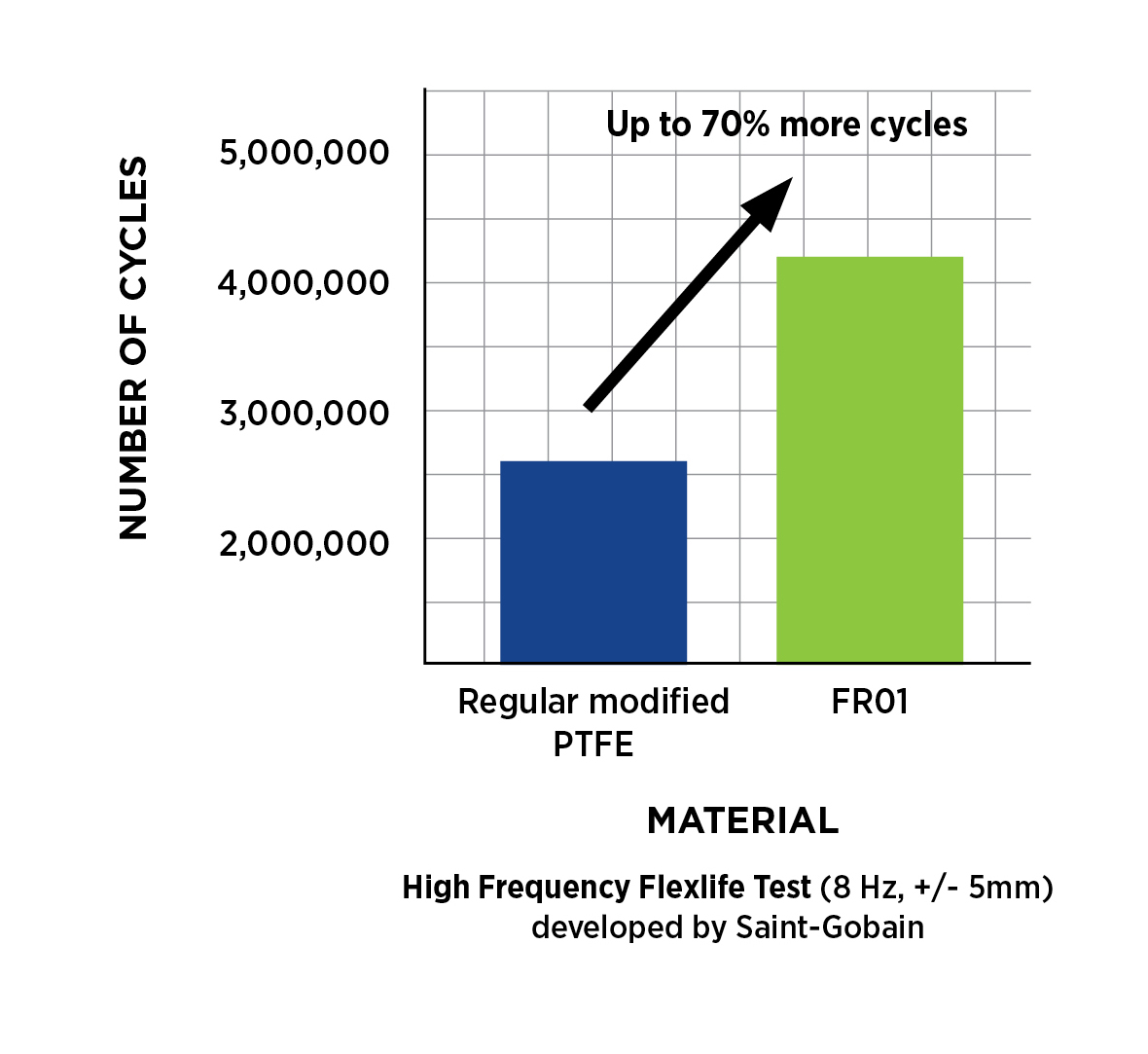
Figure 3. Improved flexlife performance of CHEMFILM® Flex-Barrier materials compared to conventional PTFE. Image Credit: Saint-Gobain FILMS & FABRICS
However, if volatile organic compounds (VOCs) or vapors successfully pass through to the atmosphere outside the pump, this could result in the need for costly repair actions. A diaphragm may allow leaks if its poor flex life causes it to rupture prematurely.
There is a risk of a highly permeable diaphragm material allowing water vapor to pass through it, or it may allow contamination from the environment into the pumped media. Water or vapor present in a pneumatic system or hydraulic fluid could pass through the membrane, resulting in process media contamination.
A flex barrier material that offers low permeability and low mean time between failures remains a viable option in preventing the release of media into the environment or vice versa.
Ensuring Food and Drug Regulatory Compliance
A flex barrier should conform to hygienic regulations and sanitary standards. This is of particular concern for diaphragms employed in pharmaceutical, dental, medical and electronic equipment.
Diaphragms used with foods and beverages are required to comply with the U.S. Food and Drug Administration 21 CFR 177 standards, while diaphragms used with drugs or active pharmaceutical ingredients are required to comply with United States Pharmacopeia Convention (USP) Class VI standards.
It is especially challenging to manufacture flex barrier or pump diaphragm materials that offer the optimal combination of low permeability, high flex life, low friction surface energy and appropriate regulatory compliance.
CHEMFILM® Flex Barriers
CHEMFILM® Flex Barrier materials are comprised of a range of film and laminate constructions produced using premium high molecular weight fluoropolymer resins.
CHEMFILM® is an ideal solution for chemical process applications such as pump diaphragms, tank linings, valve diaphragms and check valve flappers.
These applications typically require rapid transport and high cycling, as well as a wide operating temperature range, chemical resistance and stress crack resistant performance.
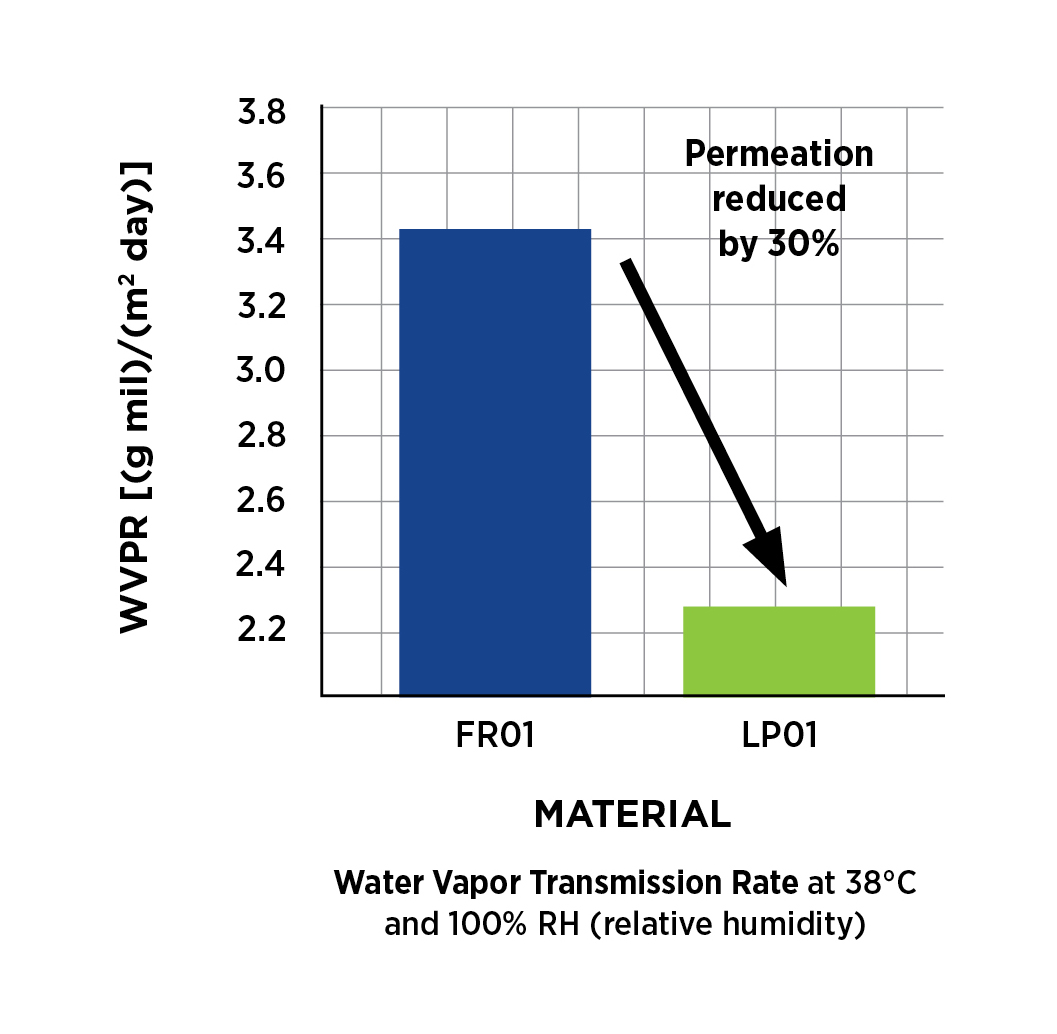
Figure 4. Improved permeability of CHEMFILM® flex-barrier with PFA barrier layer. Image Credit: Saint-Gobain FILMS & FABRICS
CHEMFILM® materials are able to meet and frequently exceed industry requirements for fluorocarbon resin sheets and film. They also align with specifications such as ASTM D-3368.
Saint-Gobain employs specialized surface treatments alongside a proprietary lamination process to ensure that CHEMFILM® Flex Barriers offer low permeability, high flex life, high smoothness and a low coefficient of friction.
The use of appropriately processed high molecular weight fluoropolymer such as polytetrafluoroethylene (PTFE) and perfluoroalkoxy (PFA) copolymer resin ensures exceptional stress crack resistance and extended flex life.
The low surface energy of fluoropolymers also offers excellent anti-stick characteristics and extremely high chemical resistance, even when working with highly aggressive chemical media.
CHEMFILM® materials possess an operating temperature range of -425 °F to 500 °F (-254 °C to 260 °C), meaning that they can be effectively utilized in cryogenic and high temperature applications.
Figure 3 details the enhanced flex life of the CHEMFILM® material versus a traditionally modified PTFE.
In this example, CHEMFILM® products demonstrate an increased lifespan of approximately 70% when tested using Saint-Gobain Specialty Film’s internal high-frequency flex life tests. These tests have been specifically developed to simulate diaphragm material flex life performance.
CHEMFILM® Flex Barriers exhibit virtually universal resistance to highly aggressive media and chemicals, for example, aromatic or chlorinated hydrocarbons, caustics, acids, ketones and acetates.
Resins employed in the production of CHEMILM® Flex Barrier materials conform to the key regulations relating to pharmaceutical, food and beverage, sanitary and medical applications.
These include FDA 21 CFR 177.1550, (EC) No. 1935/2004, (EU) No. 10/2011, (EC) No. 23/2006 (GMP), USP Class VI and 3-A Sanitary Standard.
CHEMFILM® materials also align with REACH ((EC) No. 1907/2006) and RoHS (2011/65/EU) regulations, confirming that they do not contain any hazardous or prohibited compounds which could limit the materials being used in electronic products.
There is significant variation in the permeability of polytetrafluoroethylene materials, and their performance is highly dependent upon selecting the most optimal material grade and ensuring correct flex barrier construction.
The CHEMFILM® Flex Barrier (LP01) offers increased permeability versus a traditionally modified PTFE material, but the use of an additional PFA barrier offers the potential to mitigate this issue, reducing permeability by 30%.
Saint-Gobain Speciality Films works closely with its customers to address application-specific requirements.
The company’s experienced engineers continue to develop the CHEMFILM® Flex Barriers to increase their permeability and flexing properties. The combination of these two properties is key to achieving longer life in very aggressive conditions.
Summary
The use of CHEMFILM® Flex Barriers within a new diaphragm pump design or upgrade to an existing pump offers users a tangible decrease in the total cost of ownership.
The CHEMFILM® Flex Barrier material offers longer diaphragm life than other materials, leading to reduced numbers of required shutdowns for maintenance or diaphragm replacement.
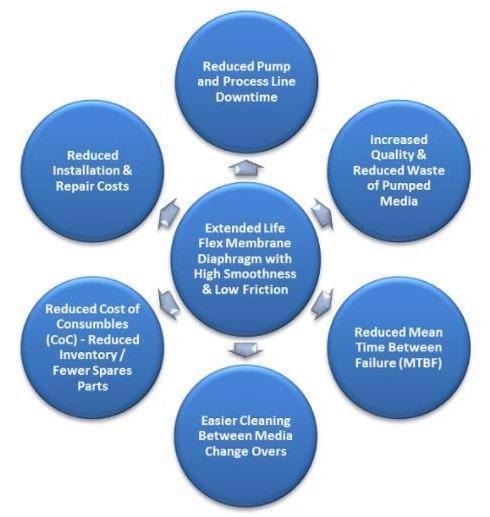
Figure 5. Utilizing CHEMFILM® flex-barriers in new diaphragm pump designs or upgrading existing pumps can minimize the total cost of ownership. Image Credit: IEEE GlobalSpec
Reduced shutdown requirements also lower the cost of the consumables due to a decreased requirement for spare parts or replacement diaphragms.
The low friction and high smoothness of a CHEMFILM® diaphragm surface help facilitate straightforward cleaning between process runs of different chemicals, paints, foods or pharmaceutical ingredients.
The high cleanliness and improved durability afforded via the use of CHEMFILM® improves the quality of the media due to a reduced contamination risk.
The robustness, reduced downtime, lower maintenance requirements, and higher cleanliness provided by CHEMFILM® Flex Barriers results in a notable overall increase in process yields and productivity.
Acknowledgments
Produced from materials originally authored by IEEE GlobalSpec.
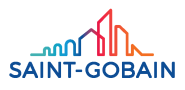
This information has been sourced, reviewed and adapted from materials provided by Saint-Gobain Tape Solutions.
For more information on this source, please visit Saint-Gobain Tape Solutions