Polymers are ubiquitous in modern society. Many different types of polymers are found in the production of film and foam as well as paint and coating. Rubber, composite materials as well as textiles and fibres are also created from polymers.
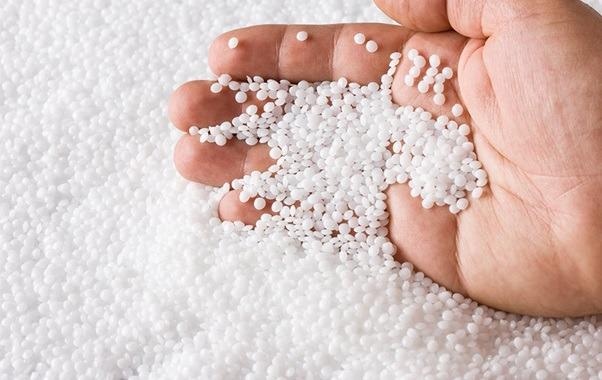
Image Credit: Stable Micro Systems Ltd
However, they must be suitable for their intended use, regardless of whether they are functional or cosmetic. Their research, development, and quality control processes are heavily reliant on the measurement of mechanical properties in order to be successful. While many polymers are used as engineering materials, natural polymers such as gluten, pectin, and gelatin can also be found in foods, wood, and other materials, and they must be tested to the same extent as engineering polymers.
Polymer manufacturers at every level of the supply chain, from raw material suppliers and manufacturers to those of finished products, are concerned about product performance. An application's optimal material can be determined through quality control testing, as well as parts' strength and durability under various stress conditions in development.
Polymers are typically classified into one of three broad groups: thermoplastics, thermosets and elastomers.
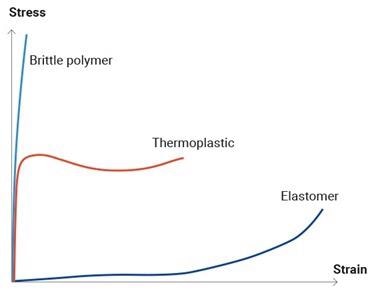
Sketch graphs showing some typical polymer deformation behaviours. Image Credit: Stable Micro Systems Ltd
Polymer Test Types
Polymers have such a wide range of properties and applications that test types are broader than the traditional tensile and bend tests usually used for engineering materials. As with any sample type, there are industry specifications that must be complied with. Many manufacturers, particularly those in consumer, automotive, medical and aerospace industries, choose to test their samples according to standard methods. Tests used to investigate polymer properties include standard configurations such as flexural, compressive and tensile in their pure form, although many tests include a combination of stress states. These include indentation and imitative measurement. Imitative measurements provide the possibility to assess samples in a manner in which they are perhaps subjected to in real-life and are not bound by the restricted form specified in a standard method, thereby providing testing flexibility and potentially more meaningful results.
Stable Micro Systems manufactures instruments that measure the tensile and compressional properties of polymers. A Texture Analyser gives a reliable way to test the mechanical properties of items by applying a choice of compression, tension, extrusion, adhesion, bending or cutting tests to measure a product’s physical properties (e.g. tensile strength, flexure force, brittleness, compressibility) to name but a few.
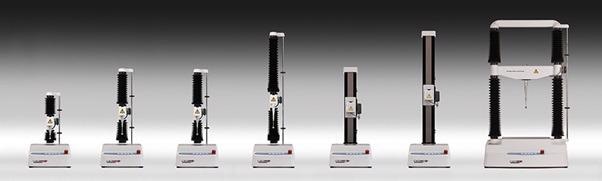
A range of Texture Analysers varying in maximum force capacity. Image Credit: Stable Micro Systems Ltd
Tension (e.g. ASTM D638, ISO 527, ASTM D882, ASTM D412)
Tensile testing is widely-used in the materials industry due to its simplicity. Stress and strain can be calculated using the sample’s geometry in a more reliable way than in other tests such as flexure or compression. ‘Tensile testing’ generally refers to the placement of a sample between two Tensile Grips, which are then pulled apart at a constant speed until either a target distance is reached or the sample breaks. However, samples may be put into a tensile state in other tests; the puncture of a thin film sample clamped around its edge puts the material into a state of biaxial tension. This type of testing can still give information on the tensile properties of a material that for practical reasons might not be suited to being clamped between two grips.
At its most basic, a tensile test can be used to measure breaking force (N) and elongation at break (mm). However, stress-strain graphs can be plotted if accurate dimensional measurements are made. These can give information on yield strength, tensile strength (at break), elastic modulus (often a secant or tangent modulus rather than Young’s modulus due to the typical polymer S-shaped curve), tensile strain at any point, yield strain and strain at break.
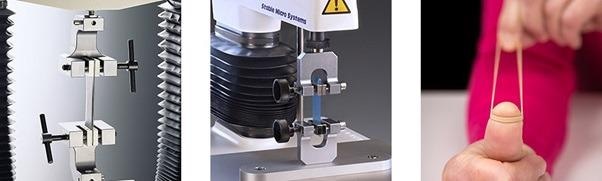
Examples of Tensile Grips depending on sample type and maximum force range. Image Credit: Stable Micro Systems Ltd
Puncture
In some cases, variations on tensile testing can be simpler than the traditional, two grips method, while still providing the results needed by the manufacturer or researcher.
The Film Support Rig allows the measurement of the mechanical properties of fine films. Prior to performing the test, the sample is placed over a hole in a raised Perspex platform. A top plate prevents the sample from slipping during testing. The test is then carried out as the arm of the Texture Analyser brings a 5mm stainless steel ball probe down into the aperture. The sample is placed into a state of biaxial tension. The maximum force to rupture the film is recorded and is referred to as the burst strength of the sample. The resilience and relaxation properties of the film can also be measured.
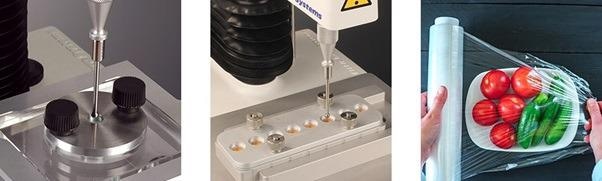
Film Support Rig and Indexable Film Support Rig. Image Credit: Stable Micro Systems Ltd
Compression (e.g. ASTM D695, ISO 604)
Compression testing is useful for the evaluation of a material’s behaviour under a uniaxial compressive load. This may be used to calculate fundamental material properties providing a sample of appropriate geometry is used (e.g. a solid circular or rectangular section prism, or a section of pipe). This type of test is particularly useful for the measurement of materials that are naturally used in compression, such as those used in the building industry (polymer concretes or foams). This type of test is also extremely useful for the assessment of non-fundamental properties, when a simple measurement of crushing force is helpful.
Compressive testing is generally used for stiffer, self-supporting samples, such as thermoplastic polymers destined for injection moulding, or thermosetting polymers.
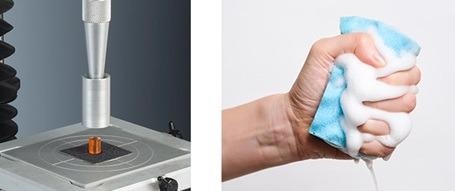
Typical compression testing using cylinder probe. Image Credit: Stable Micro Systems Ltd
Indentation and Penetration
Indentation (e.g. ISO 7619-1)
Indentation testing is a widely-used method for mechanical characterisation of many materials, including polymers. The most important parameter drawn from an indentation test is hardness, commonly described as a material’s resistance to local surface deformation. It is a very useful test for monitoring the quality of irregular objects, such as the consistency and stickiness of soft foods. However, this test setup can also provide useful stress-strain data if the sample has a flat surface and a homogeneous structure, providing accurate measurements are made during the test.
Polymers are generally indented using a ball indenter (Brinell hardness) or a Shore durometer using a Texture Analyser. Diamond-shaped Vickers indenters may also be used by some polymer researchers.
Shore durometers are used to determine indentation hardness of materials by using a measurement of resistance to deformation. A and D are the two most commonly used scales.
The majority of Shore hardness testing is carried out on standard and vulcanised rubber, thermoplastic elastomers, gels and plastics.
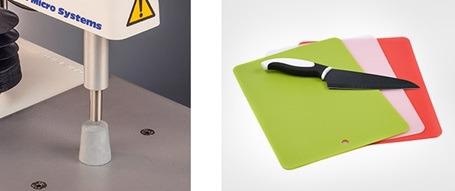
Typical Shore Hardness probe. Image Credit: Stable Micro Systems Ltd
Non-Standard Penetration: Viscous Polymer Measurement
The properties of viscous semi-solid polymers have faced increasing attention in recent years due to the much increased popularity of ‘play slime’ designed for children. The hardness and stickiness of these products are of particular importance, and can be measured using the Mini Stickiness System. This is based on the principle of subjecting a viscous polymer sample (or other viscoelastic semisolid) to shear while minimising the exposure of the cut surface to the atmosphere. A retaining plate is placed over the sample with limited compression of the piece being incurred because the height of the lid is predetermined by the size and shape of the sample. A narrow blade is driven through a slot in the retaining plate to shear through the sample and after a given distance of travel is withdrawn. The intimate contact between sample and blade limits the potential for changes in sample rheology through exposure to the atmosphere.
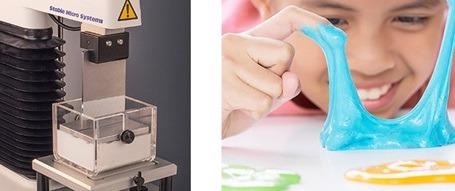
Mini Stickiness System. Image Credit: Stable Micro Systems Ltd
Flexure (e.g. ASTM D790, ISO 178)
Flexural testing, commonly referred to as ‘three-point bend testing’, involves a long sample placed on two supports (or “rollers” due to their curved surface) a set distance apart, with a third roller moving down to contact the sample halfway between these supports. In some situations, two rollers are lowered onto the sample to instigate four-point bend testing. The loading arm moves down at a constant speed to bend the sample. If the sample is sufficiently brittle and the force required within the limit of the load cell, fracture will occur. Different samples will give different load-distance responses – stronger and stiffer samples show higher forces, brittle samples break before any plastic deformation occurs and tough samples show a large area under the curve corresponding to a large amount of energy required for deformation.
It is a very useful test for monitoring quality of irregular objects, such as the snap of a biscuit or the toughness of a dog chew. However, this test setup can also provide useful stress-strain data if the sample has a uniform rectangular or circular cross-section, providing accurate measurements are made of the sample dimensions.
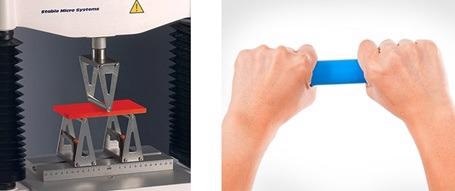
Typical Three Point Bend Test. Image Credit: Stable Micro Systems Ltd
Sliding Friction (e.g. ISO 8295, ASTM D1894)
Sliding friction is an important measurement for many polymeric materials, particularly those in film form used in packaging, but any semi-rigid to rigid polymer may be measured in this way.
Measurements of frictional properties may be made on a film or sheeting specimen when sliding over itself or over another substance. The coefficients of friction are related to the slip properties of plastic films that are of wide interest in packaging applications. The coefficient of friction is defined as the ratio of the frictional force to the force, usually gravitational, acting perpendicular to the two surfaces in contact. This coefficient is a measure of the relative difficulty with which the surface of one material will slide over an adjoining surface of itself, or of another material. The static or starting coefficient of friction is related to the force measured to begin movement of the surfaces relative to each other. The kinetic or sliding coefficient of friction is related to the force measured in sustaining this movement.
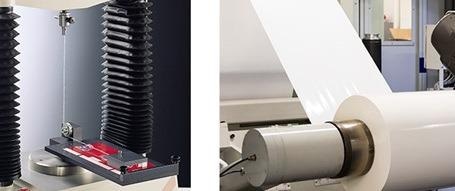
Coefficient of Friction Rig. Image Credit: Stable Micro Systems Ltd
Stable Micro Systems are able to assist with many polymer applications well beyond the realms of the standard methods outlined in this article, including imitative, empirical and applied methods, so your product can be tested in the way in which it was intended to be used.
Here is a summary of typical texture analysis tests that can be performed on materials such as polymers or watch this to see the highlights: https://www.youtube.com/watch?v=D1cNQP--CZw.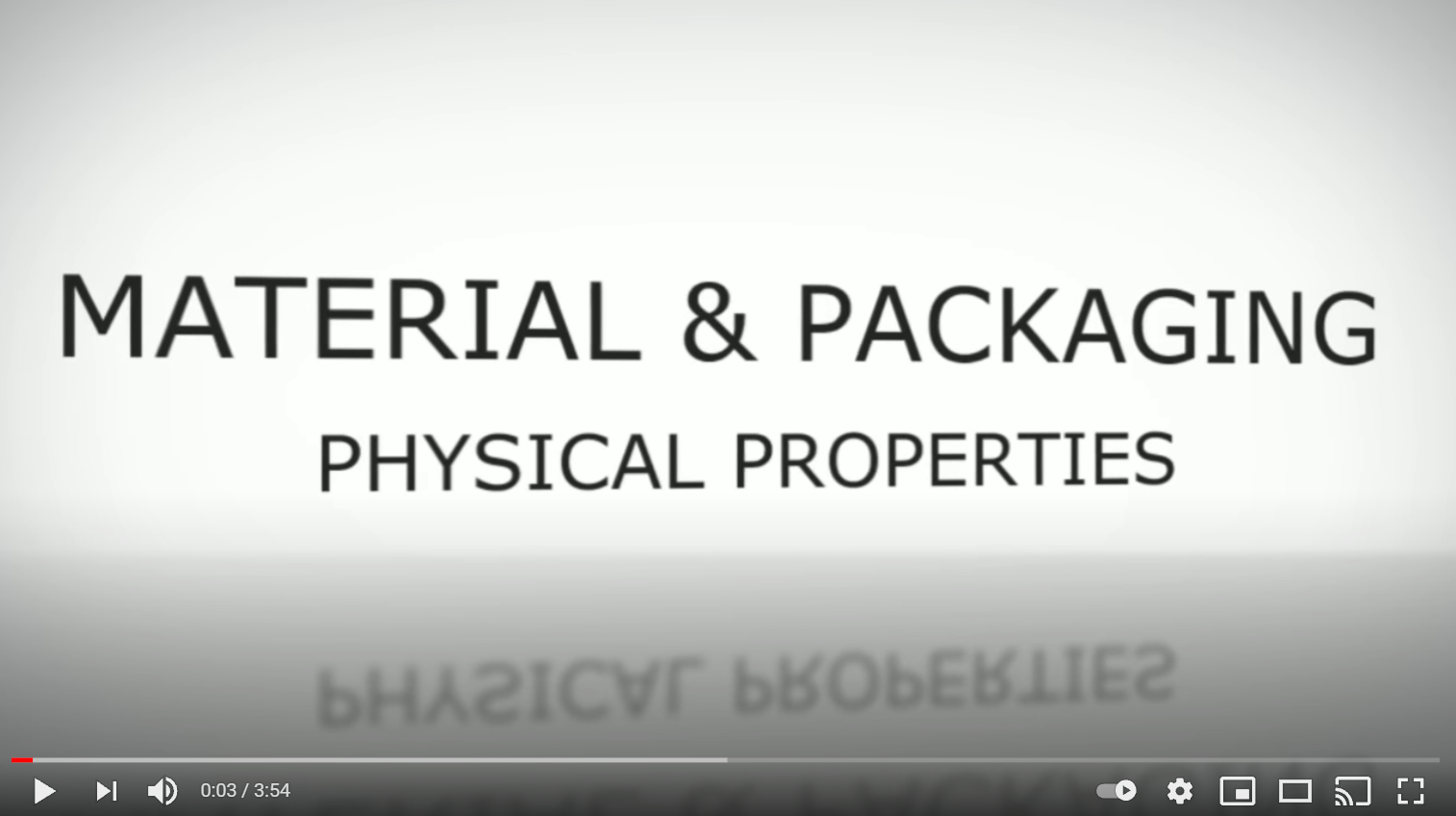

This information has been sourced, reviewed and adapted from materials provided by Stable Micro Systems Ltd.
For more information on this source, please visit Stable Micro Systems Ltd.