3D printing has taken off as a niche manufacturing method, enabling consumers to design and build their own goods. As such, it now holds an important place in the manufacturing industry.
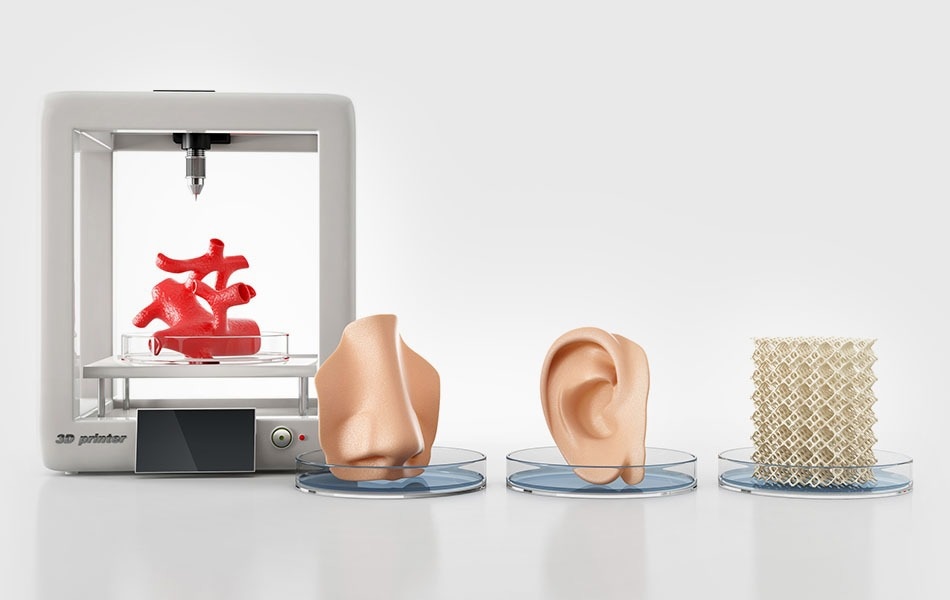
Image Credit: Stable Micro Systems Ltd
Objects can be built in almost any format the consumer desires, and it has moved on from the early limitations of certain polymer groups as the building material. Now it is a potential tool in many industries, including bone and organ replacements, meat manufacture and even customizable bakery.
Stable Micro Systems manufactures instruments that measure the tensile and compressional properties of 3D printed parts. As with any manufacturing innovation, the end product must go through a quality control process to assess its physical properties. A Texture Analyser is a crucial part of this procedure, giving a reliable way to test the mechanical properties of 3D printed objects by applying a choice of compression, tension, extrusion, adhesion, bending or cutting tests to measure a product’s physical properties e.g. tensile strength, flexural modulus, fracturability, compressibility, to name but a few.
To read the full length article on this topic, click here.
Example of how 3D printing materials can be tested – Extrusion
The printability of materials used in extrusion-based 3D printing is one of the most important properties especially when fabricating objects with architectural complexities. This parameter is influenced by several factors (temperature, components, and additives) which makes thorough evaluation and classification challenging. Interest in 3D printing for biomedical applications is now increasing and the pharmaceutical industry is starting to explore how 3D printing can help us to deliver better medicines. Achieving reproducibility in the 3D printing of biomaterials requires a robust polymer synthesis method to reduce batch-to-batch variation as well as methods to assure a thorough characterization throughout the manufacturing process. Particularly biomaterial inks containing large solid fractions such as ceramic particles, often required for bone tissue engineering applications, are prone to inhomogeneity originating from inadequate mixing or particle aggregation which can lead to inconsistent printing results. The production of such an ink can be optimized to assure homogeneous and reproducible printing results by using a TA.XTPlusC Texture Analyser to perform extrusion force measurements to predict the printability of inks. To read an example publication of this texture analyzer application at ETH Zurich, click here.
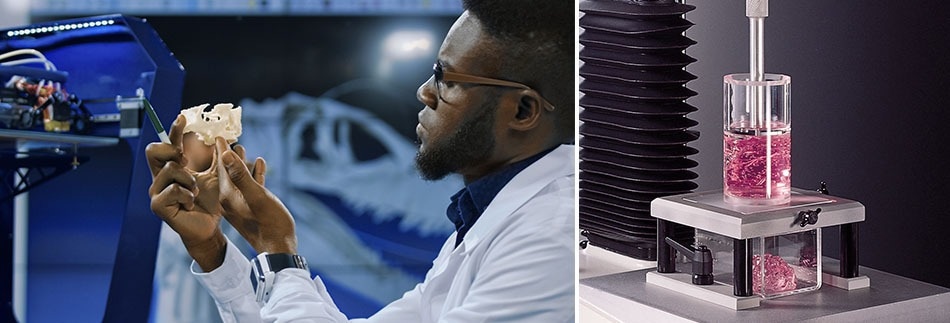
Forward extrusion test on a Texture Analyser. Image Credit: Stable Micro Systems Ltd
Example of how 3D printing materials can be tested – Compression
Due to the low price of 3D printing equipment and its versatility, materials such as antioxidant PLA composites containing lignin can be used in hospitals to print wound dressings for patients on demand. 3D printing can also potentially benefit plastic and reconstructive surgeries by fabricating patient-specific tissue replacements with tissue-like functions and mechanical properties. A Texture Analyser can be used to perform compression testing on samples to characterize their mechanical properties which are important for their structural integrity. To read an example publication of this Texture Analyser application at the University of Nottingham, click here.
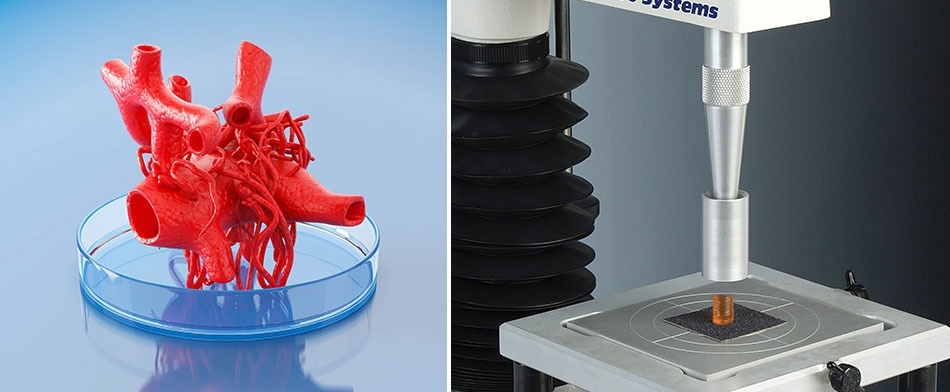
Unconfined compression on a Texture Analyser. Image Credit: Stable Micro Systems Ltd
Example of how 3D printing materials can be tested – Flexure and Bending
3D printing provides a new approach to fabricating drug-eluting implantable medical device products because it permits a flexible manner to extrude complex and customized shapes of tissue scaffolds. Considering the simplicity, it can be easily transferred to a clinical setup, where implants could be designed on demand to fulfil patients’ needs after surgery. These implants may be suited for the delivery of drugs for localised treatment. For example, chemotherapy agents, antibiotics or local anaesthetics. Alternatively, they could be tailored by coating them for prolonged drug delivery for the treatment of chronic conditions.
Compared with other printable biomaterials, polyurethane elastomers have several merits, including excellent mechanical properties and good biocompatibility. However, some intrinsic behaviour, especially a high melting point and slow rate of degradation, hamper their application in 3D printed tissue engineering. The development of a 3D printable amino acid modified biodegradable waterborne polyurethane means that the flexibility of this material endows better compliance with tissue during implantation and prevents high modulus transplants from scratching surrounding tissues. Using a Texture Analyser to perform flexibility (three-point bend) measurements on 3D printed samples allows assessment of whether this can be used as an alternative biomaterial for tissue engineering with low-temperature printing, biodegradability and compatibility. To read an example publication of this texture analyser application at the University of Science and Technology Beijing, click here or click here to see similar work at Queen’s University Belfast.
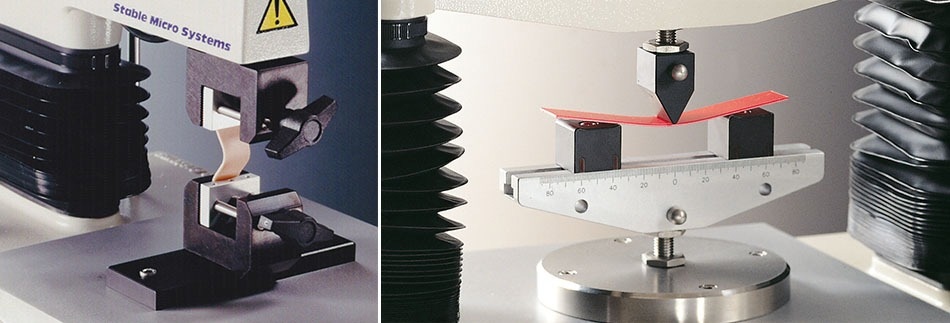
Flexibility and 3 point bend testing on a Texture Analyser. Image Credit: Stable Micro Systems Ltd
Example of how 3D printing materials can be tested – Puncture, Elongation and Tension:
Orodispersible films (ODFs) are promising dosage forms for children or elderly people who may face swallowing problems with solid oral dosage forms. By printing active pharmaceutical ingredients onto orodispersible films, the flexibility of drug dosing is increased and provides potential for personalised medicines. Warfarin is an example of a narrow therapeutic index drug that requires personalised dosing which is currently not achieved by marketed products. Extrusion 3D printing can be utilised to produce transparent, smooth and thin, yet flexible and strong orodispersible films containing therapeutic doses. Using a Texture Analyser, the films can have their burst strength and flexibility properties measured as part of their all-important physical characteristics that could impact on their usability.
To read an example publication of this texture analyser application at the Heinrich Heine University Dusseldorf click here, or click here for similar work carried out at Åbo Akademi University.
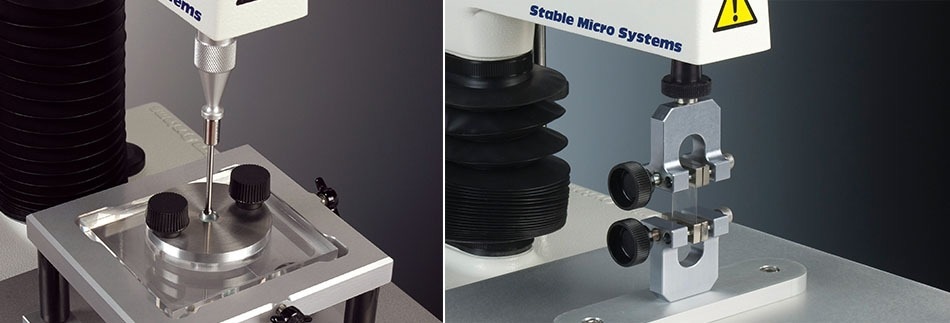
Burst strength, tensile strength and film flexibility on a Texture Analyser. Image Credit: Stable Micro Systems Ltd
How a Texture Analyser can assess base powder flowability
Texture Analysis can also be put to use at other stages in the 3D printing process, not just for the measurement of final product properties. For example, the properties of the base powder used in Selective Laser Sintering affect the sintering process as well as the properties of the final product. Powder flow is one of these properties. As each new layer of powder is swept onto the sintering bed, the layer should be uniform and of the correct thickness and distribution. A Powder Flow Analyser (PFA) is a very useful add-on to a Plus Texture Analyser to help measure these flow properties.
The PFA proves an accurate and reliable method of measuring the flow characteristics of dry and wet powders, with capability to measure cohesion, caking and speed flow dependence as well as bulk density and other properties. It can be rapidly fitted to a TA.XTPlusC Texture Analyser, enabling manufacturers to assess and avoid typical problems such as batch and source variation of ingredients, caking during storage/transportation and problems with discharging from hoppers or bins, as well as 3D printing-specific powder properties. The powder is conditioned at the beginning of each test to eliminate any variations in loading and the precision-engineered, patented blade is then rotated through the sample, causing controlled flow.
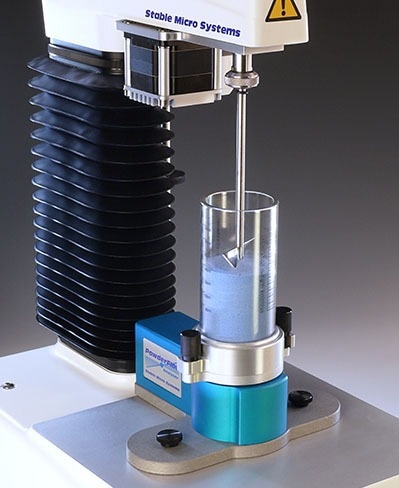
Image Credit: Stable Micro Systems Ltd
The Need to Measure Dimensional Profiles
If you’ve designed a product and then you print it, one concern will be whether what has been printed is what you designed. In many cases you’ll need your printed object to be dimensionally accurate and iterations of printing your design are almost inevitable to adjust the printing settings to obtain a product that is dimensionally accurate. Accurate digital assessment of physical dimensions thereby becomes a necessity. A Volscan Profiler provides such a solution – a benchtop laser-based scanner that measures the volume, density and dimensional profiles of solid products. The rapid 3-dimensional digitisation of products enables the automatic calculation of several detailed dimension-related parameters, the results of which may be mathematically manipulated for immediate use or future retrieval in a variety of data formats for your printed objects.
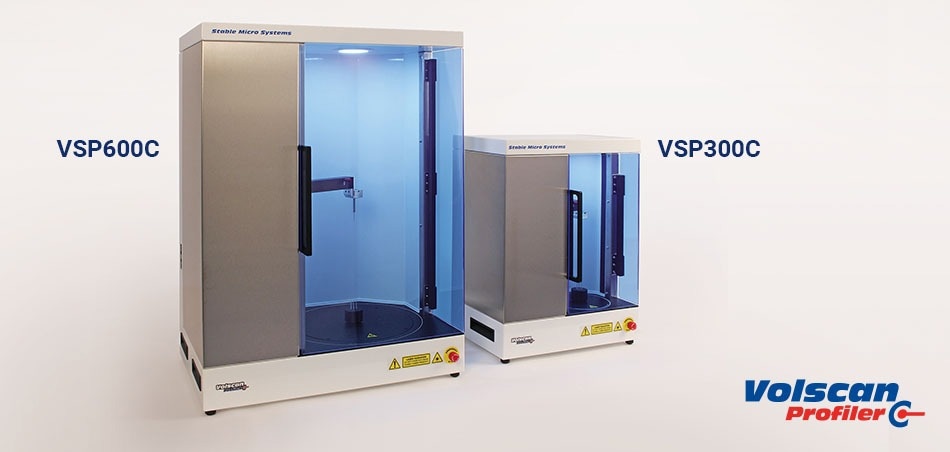
Volscan Profiler models for measurement of Volume, Density and Dimensional Profiles. Image Credit: Stable Micro Systems Ltd
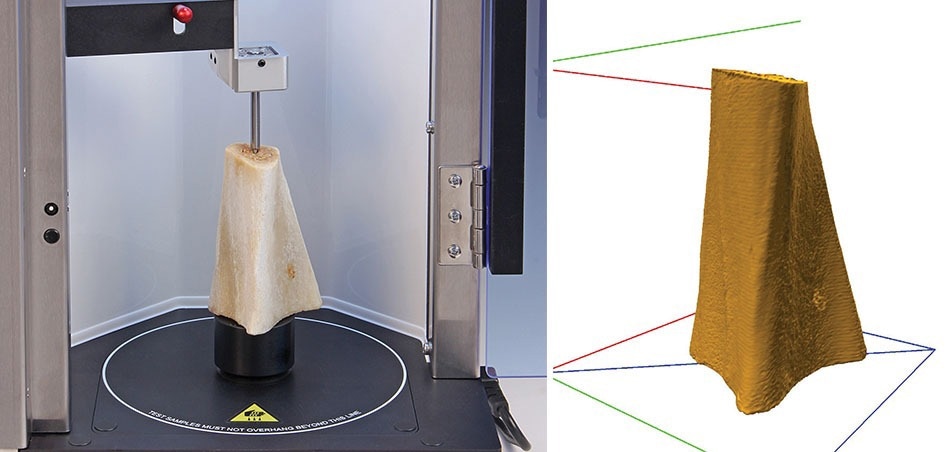
Bone sample ready for scanning and an archived scan of sample. Image Credit: Stable Micro Systems Ltd
The medical industry is becoming heavily reliant on the TA.XTplusC Texture Analyser as a tool for the measurement of all types of physical/mechanical properties.