Can you give a brief summary of Carbolite and the company’s focus?
Carbolite is a part of Verder Scientific Group – a group of companies with more than 1,000 employees working in 22 offices around the world. Verder Scientific sets the gold standard in R&D solutions and quality control in analytical laboratories, research institutions and cutting-edge manufacturing companies.
Verder’s solutions cover sample preparation, characterization and heat treatment, through to hardness testing and elemental analysis. Each Verder Scientific company works to deliver tangible benefits to its customers’ processes, outcomes, profitability and sustainability.
What sort of products and solutions does Carbolite offer?
Carbolite offers a comprehensive portfolio of furnace systems able to operate at temperatures from ambient up to 3000 °C.
These systems can be grouped into four key types: ovens running up to 700 °C, hot wall chamber furnaces, tube furnaces running up to 1800 °C, and vacuum furnace systems running up to 3000 °C.
Carbolite continually invests in product development and has recently launched a new split tube, a gradient tube and a rotating tube furnace, and a number of custom-designed solutions developed and manufactured according to customers’ specific requirements.
What roles do furnaces play in the development and manufacture of batteries, and how have these roles shifted over time?
Before discussing battery materials themselves, it is important to summarize the characteristics of a good battery. Materials must be pure and homogenous in order to ensure the creation of an efficient power source and a longer-lasting cell.
The end product should be lightweight, and this requires a good crystal structure that permits the ions to effectively pass between the anode and cathode layers.
Using the most appropriate electrolyte will improve energy density and battery capacity. Most importantly, however, it is essential to only utilize safe materials to ensure no risk to the battery’s end user.
Typical applications of furnaces and ovens include material synthesis, de-binding, calcination, graphitization and material drying.
Machine learning has also become a key tool in this process, with the development of numerous databases enabling viable material combinations to be sourced and compared using a computer and AI.
These databases also help manufacturers select appropriate additives.
These additives are vital to the performance and stability of batteries’ anode and cathode material, helping to protect these from corrosion, improving electrical performance and limiting the growth of dendrites (needle-like and treelike materials with the potential to destroy cell membranes).
What are the primary components of batteries, and what techniques are typically used to manufacture these?
A battery is generally comprised of a steel- or aluminum-based casing, with cathode materials that are generally made up of LCO, NCA, NMO, LFP or LMO.
The battery’s anode is generally manufactured from graphite, but it is anticipated that new developments in the field of silicon and other materials will lead to these options expanding and diversifying.
A battery’s electrolytes are key to its conductivity. The anode and cathode materials in lithium-based batteries tend to be copper and aluminum, while the separator membrane is largely made up of polymers. Additives such as carbon black may also be included.
Virtually every material used in batteries must be manufactured via a specific process. For example, graphitized carbon material generally starts with a highly disordered arrangement that becomes more ordered up to 2000 °C.
The final re-arrangement takes place between 2800 °C and 3000 °C, so called Graphitization, and this process is key to ensuring that the distances between the graphite layers are optimized and that ions are allowed to move freely between those.
Off-gassing and pyrolysis typically occur between 200 °C and 900 °C, though the point at which they take place is highly variable within this range. Off-gases formed during this process must be removed to ensure the furnace maintains a safe and pure atmosphere.
Some residue binding occurs as the carbonization temperature starts, particularly from gases like hydrogen. This residue binding often tends to result in carbon-nitrogen-based compounds being expelled.
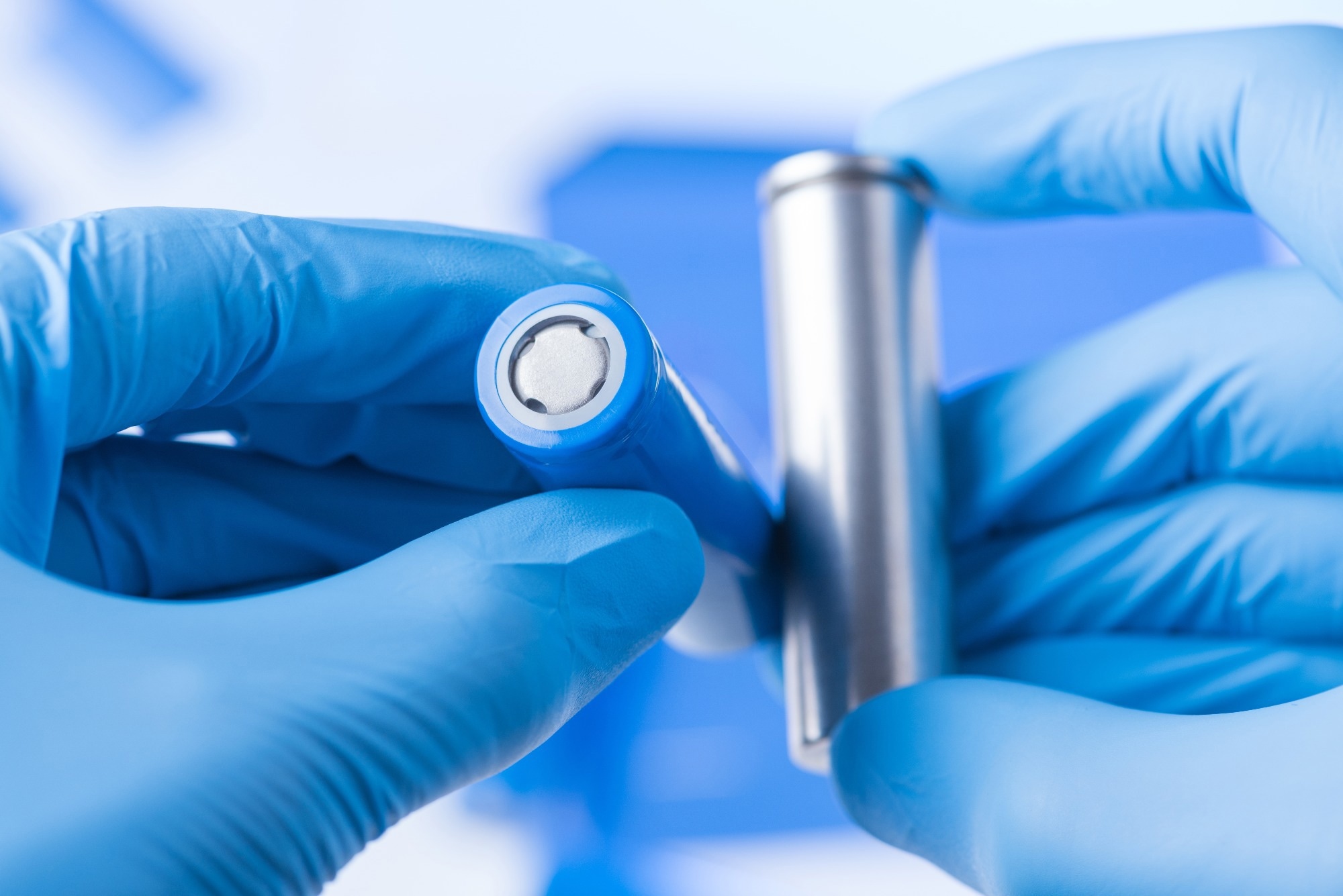
Image Credit: nevodka/Shutterstock.com
What type of furnace systems are best suited for each stage of this process?
The majority of weight removals during the carbonization process occur at relatively low temperatures. Carbolite offers hot wall systems that are ideally suited to this stage.
Small tube furnaces may also be used, but these furnaces can only process a small sample of material, and there is no way of handling condensables adequately. These are highly flexible, low-cost systems, and are well suited for R&D for heat treatments up to 1800 °C.
Carbolite offers larger systems up to 1300 liters in size, which are primarily configured for pyrolysis work. These systems are easy to clean and can accommodate any off-gas that burns cleanly through the afterburner, with H2O, CO2, and some NOx left over as residual off-gases.
Graphitization necessitates the use of a high-end, precision system. To accommodate this, we offer advanced systems that can accommodate both off-gassing and residual elements. These robust systems feature graphite heating elements and felt insulation and can operate at temperatures up to 3000 °C.
By using a combination of thermocouple controls at lower temperatures and optical parameters, we are able to ensure optimal temperature accuracy throughout the process. This system also features an afterburner system that can effectively deal with any off-gases.
What type of systems and processes are involved in the manufacture of more specialized or unique battery materials?
Over the coming years, nickel is anticipated to become an increasingly important battery material, primarily because cobalt and nickel are the key compounds in lithium-ion batteries, and manufacturers are working to reduce their reliance on cobalt due to its associated environmental and humanitarian issues.
There is, therefore, a requirement for nickel to become more highly concentrated in battery cells in order to enhance their energy density.
Large-scale nickel production is achieved via the flotation process - a physical and chemical process that takes place in water.
This process involves a soap being introduced into the water with a number of additional additives, resulting in specific ores floating on the water’s surface.
These ores must be removed from the nickel before iron and nickel ores are roasted in air and then melted together with sodium sulfide, resulting in only nickel sulfide remaining.
The extraction and purification of nickel are done via the Mond process. This process can be implemented at a smaller scale using furnaces or at an industrial scale using large towers.
A see-saw furnace is generally employed in switching between roasting and calcination. Nickel sulfide is oxidized with air in the calcination phase into nickel oxide and sulfur dioxide. In the reduction phase, the nickel oxide is reduced with coke to raw nickel.
A batch system can also be employed where the TSO oscillates and agitates the sample. The system offers excellent mixing capabilities, ensuring a good degree of gas diffusion into the raw material and a perfect treatment of all particles over time.
The TSR rotating tube furnace can also be employed for continuous processing. This model enables the angle of inclination to be adjusted, helping to control the material’s speed as it flows through the furnace.
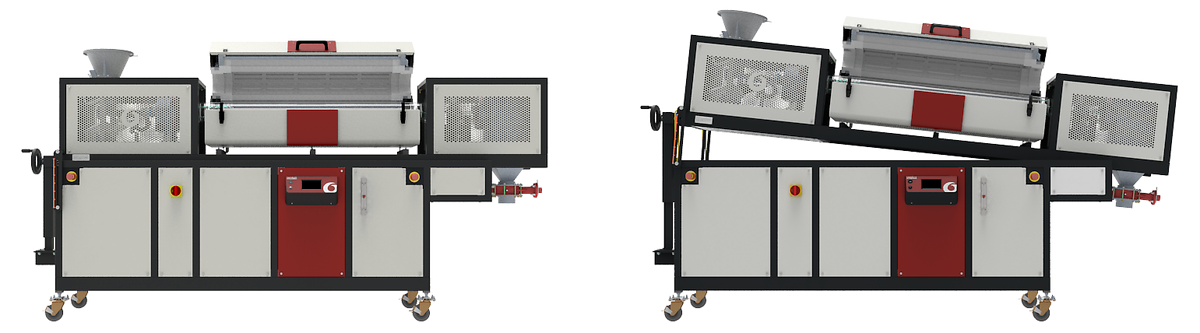
Image Credit: Carbolite
This furnace also allows the gas type to be controlled, meaning the material can be processed in an inert gas while simultaneously controlling the rotation speed.
The temperature can be divided into multiple zones, allowing a gradient to be implemented through the furnace. Materials can be fed in batches, but a continuous feed system is also available with a range of hopper and feed assemblies.
When the Mond process is used at smaller scales, ‘unpures’ are used, necessitating the use of a gradient inside the furnace. It is also important to note that at lower temperatures, radicals will react with carbon monoxide, prompting the carbon monoxide to become gaseous.
This is due to nickel’s complex material being nickel tetra carbonyl, which will decompose to pure nickel as the carbon monoxide is expelled. This process is cyclical whereas CO acts as a catalyst.
Beyond nickel, what other potentially useful battery materials exist?
Nickel is key to battery performance, but there has been substantial research into carbon nanotubes (CNTs), graphene, silicon and other new materials.
Silicon graphite composites are able to provide a higher density and a higher capacity, and the use of pure silicon can increase battery capacity tenfold due to lithium’s storage limitations. Silicon is able to store more than many other materials, but swelling remains a critical issue.
As silicon starts to swell, there is an increasing risk of the battery being destroyed or even exploding. Composite materials provide a potential means of mitigating this issue, prompting research into coated silicon composites.
Other materials, such as niobium titanium oxides and niobium tungsten oxides, include large clouds of electrons surrounding the oxygen, ensuring that the lithium can move quickly and easily through the batteries.
A solid-state battery has the potential to be charged within six minutes and has enough capacity to power a car for approximately 320 km.
There has been limited research into the lifetime of these materials, but examples have already demonstrated that niobium tungsten oxide-based materials are able to accommodate around 5,000 charging cycles, and niobium titanium oxide based-material can accommodate around 20,000 cycles and double capacity.
How has the development of silicon graphite composites impacted their potential for use in battery materials?
A furnace was recently sent to a company that specifically works with silicon graphite composites. They were introducing carbon into the furnace as powdered or flaked graphite and carbon before melting and pyrolyzing this together with silicon to generate a composite.
The furnace employs a tray and direction system with quartz crucibles. The composite material is inserted into the furnace and heat-treated under inert gas, with the initial heating step occurring at around 300 °C before the temperature is increased to around 600 °C to begin a pyrolysis step.
Off-gases are removed using an afterburner.
The core sintering process requires temperatures of up to 1000 °C to ensure that coating takes place. This can be achieved in a standard CWF furnace or other small-scale furnaces.
This particular process is still in the early stages of development, but pre-testing has already demonstrated promising results.
It is advisable to employ a specialized furnace for pyrolysis, and furnaces with smaller exhausts are unsuitable due to the risk that the binder and pyrolysis materials could condense and block the gas outlet, resulting in over-pressuring and other safety issues.
Where can people learn more about Carbolite’s range of furnaces and their application in battery material production?
Anyone with a specific process that they would like to review with the team at Carbolite can do so at any of its test centers present in its major markets around the world.
The team is always happy to work in partnership with customers to explore their processes and provide advice and support.
It is recommended that anyone who is working with battery materials get in touch. Carbolite has more than 80 years of specialist knowledge, allowing the company to offer a comprehensive portfolio of high-quality equipment.
About Fabian Uhlemann-Kölly 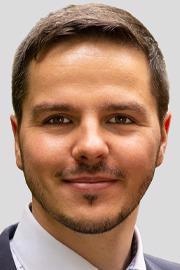
Fabian graduated in 2013 with a degree in metal-organic LED chemistry. After graduating Fabian was involved in further research projects around silicon high temperature chemistry.
In 2016, Fabian joined Carbolite in Neuhausen, Germany and initially worked as a Product Manager. In early 2020 Fabian joined the Export Sales Department of Carbolite GmbH supporting and helping to grow the presence of Carbolite in countries around the world.
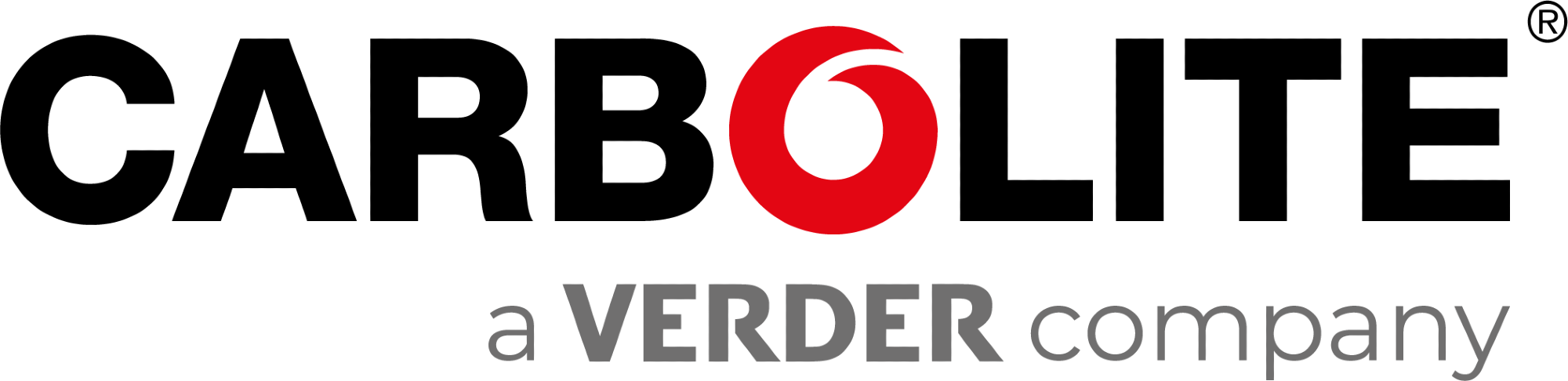
This information has been sourced, reviewed and adapted from materials provided by CARBOLITE.
For more information on this source, please visit CARBOLITE.
Disclaimer: The views expressed here are those of the interviewee and do not necessarily represent the views of AZoM.com Limited (T/A) AZoNetwork, the owner and operator of this website. This disclaimer forms part of the Terms and Conditions of use of this website.