Several sectors are looking at novel uses for otherwise difficult to recycle end-of-life plastics, adapting and repurposing these for use in other industries and products, even where these cannot be recycled conventionally.
This interview with Dr. Ellie Fini - Associate Professor at Arizona State University, Senior Sustainability Scientist at the Global Institute of Sustainability and Innovation, and the Director of the Innovation Network for Materials, Methods, and Management – looks at novel work being undertaken to utilize essentially otherwise unusable end-of-life plastics as aggregates in construction materials.
This work aims to leverage plastics’ longevity and wear resistance to provide positive benefits to construction applications, such as roads, walls and other infrastructure.
The interview explores Dr. Fini’s team’s work, their approaches to developing applicable materials and how the team characterized and verified the materials’ performance and suitability for demanding roadbuilding applications.
Please could you start by outlining the scale of the issue surrounding end-of-life plastics and why it is so important to address this issue?
We come across waste and end-of-life plastics every day, but many consumers do not think about what happens to these plastics at the end of their lives, such as where the plastics end up, how long they take to degrade and their impact on people and the planet.
For example, around 19% of the plastic produced worldwide ends up in the ocean, poisoning fish and even entering the fish that we consume and digest.
In terms of where end-of-life plastics go at the end of their lives, only around 12% are recycled, and almost 40% are in landfills. Some plastics are incinerated, some are lost throughout the process and some are sent to other countries to be processed.
Plastic is primarily petroleum-based, and there has been significant research around returning the plastic to its original building blocks to be used again. There is an urgent need to switch from sending end-of-life plastics to landfills and use these in different applications.
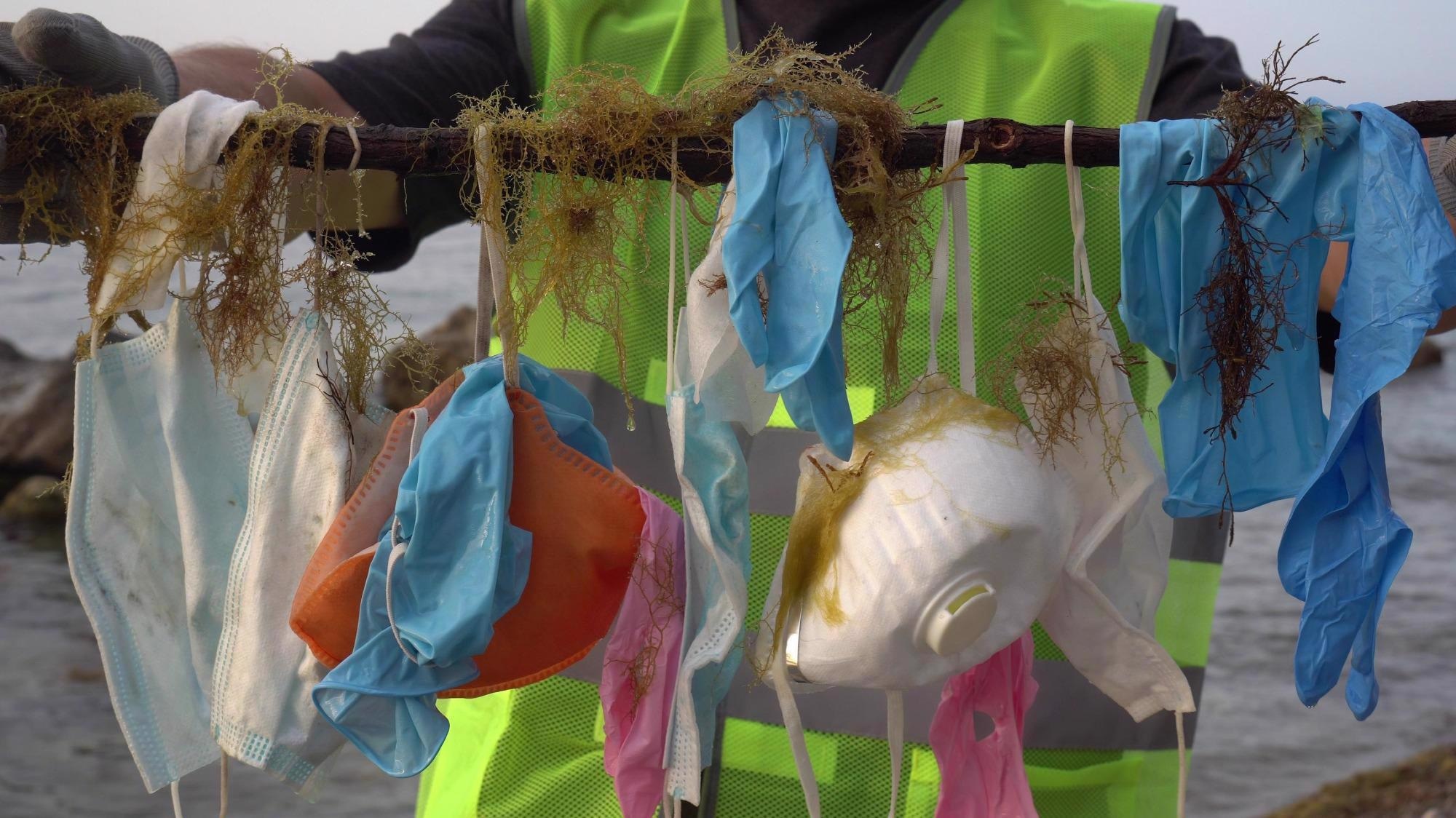
Image Credit:Shutterstock/Fevziee
What are some of the existing barriers to recycling and re-using plastics in new applications?
Some plastics are quite hard to recycle. Methods are available to make crude oil using pyrolysis or terminal chemical liquefaction, but this requires a lot of heat, energy and processing time. Other methods include biodegradation using microbes and fungi or using microwave UV and other radiation to degrade the plastic.
Another promising method is a surface treatment. Many people - including a Post-Doc in my group - are trying to use surface treatment to enable plastic to be used in other formats. This work is being done in collaboration with Thermo Fisher Scientific and will be published soon.
Plastics such as PET and HDPE can be recycled, but the recycling of plastics such as PVC and LDP is limited. Polystyrene and polycarbonate are much harder to recycle and use in different applications.
These plastics are commonplace in many facets of daily life. For instance, PET is used in bottled water, while soap bottles are mostly made from HDPE, and plumbing pipes are made from PVC. These are all regarded as plastics, but they are very different types – so much so that it may not be fair even to use the general term ‘plastics’ for all of them.
This level of variation affects recycling, particularly in terms of breaking the plastic down into its original monomer and polymerizing this again to make new products.
Returning the plastic to its monomer is not always straightforward, and sometimes the process of creating the monomer degrades the whole thing. Methods such as pyrolysis and thermochemical reproduction will reduce plastics to oil, but at that point, most plastic turns to a heavily degraded oligomer.
How does your current project help address this issue of plastic degradation during recycling?
Our goal is to convert end-of-life plastics into new products while making sure that we minimally degrade the plastics. We are not breaking this back down to monomers. Instead, we are using these plastics as a compatible product for construction.
Most roads, walls and floors are made up of aggregates and some glue, which could be the cement that holds things together. Road applications tend to use stone aggregates such as granite, limestone and sand, plus a bond, generally asphalt.
If granules made out of plastics are compatible with the rest of the construction materials, these could play a role as a building block for construction. Using end-of-life plastics this way means they will not be released into the environment, and the construction application can benefit from the plastics’ durability.
One of the reasons we are dealing with this vast plastic problem is because plastics take such a long time to degrade –between 100 and 300 years. We thought that if we could use these plastics as granules in roadbuilding, it may improve the durability of the road.
Our work involves mixed plastics, which are typically very hard to deal with because each of these plastics is different and must be recycled differently. Also, these plastics tend to be colored, and most recycling companies prefer not to deal with colored plastics.
Colored plastics pose less of an issue in construction materials because very few people require external walls to be precisely colored to certain specifications.
The mixed plastic is treated on the surface with oil to make it compatible with the rest of the building material. For example, we treat the plastic with waste vegetable oil, and we apply a small amount of radiation before grinding the plastic into granules. This product can be directly added to the construction of concretes or asphalt roads.
In America alone, we have four million miles of roads. If we can safely use end-of-life plastics in the road construction business and improve the durability of roads, this would be quite the win.
To this end, my team has developed oil-treated plastic granules (OTPG). These granules have been designed for use in construction materials, such as asphalt or concrete.
The OTPG process seems uncomplicated, but there is a lot of science behind it to ensure we get the proper surface properties. It will be straightforward in terms of scale-up and application because the supply of raw materials is abundant.
The plastic is not treated initially; it enters the process as-is. We treat it with oil, grind it to the correct size, and hybrid-treat this with carbon to further improve its compatibility with typical construction materials.
The treatment is essential, and it is not possible to grind mixed plastic and add this to construction material.
This is due to the problem of segregation because plastic is not inherently compatible with cement or asphalt. As you mix and place it down, the plastic will shift to one side, and the rest of the material will shift to the other. This has no use in construction materials, which must maintain a homogenous mix. Oil treatment and carbon coating help to ensure this homogenous mix.
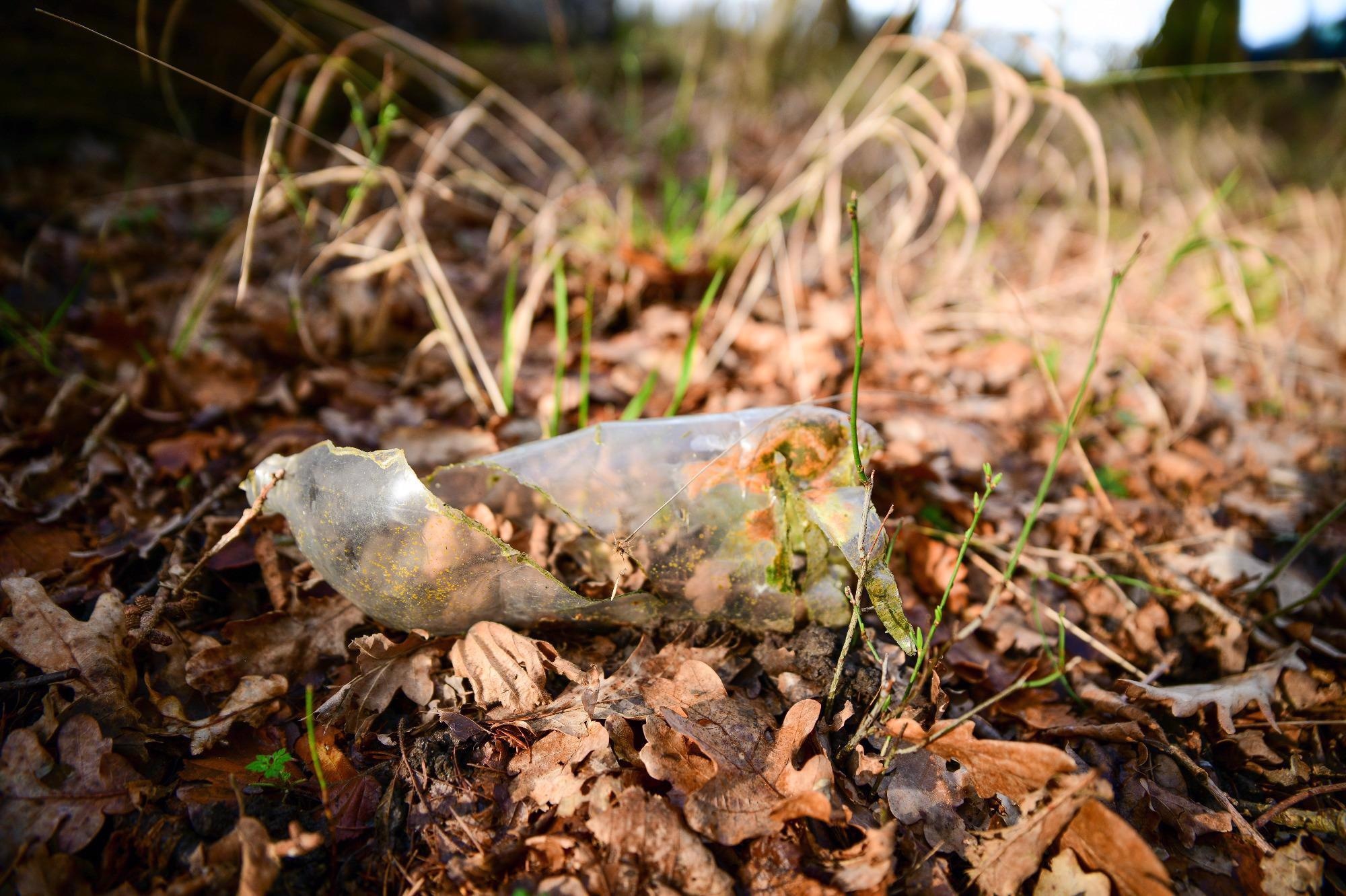
Image Credit: Shutterstock/Oxford_shot
What role does analytics play in this work, and what tools have enabled the characterization of OTPG and related materials?
We acquired and analyzed a series of Raman spectra with the help of colleagues from Thermo Fisher Scientific. They are also co-authors of the paper.
We observed that the ratio of the 1095 nm to 1115 nm peak is 1.3 for non-treated plastics and 1.6 for all treated plastics. We also saw a shift in this, which indicates crystal in a structure.
Our goal was to determine what happens to the plastic structure itself, analyze the composite and explore the new, non-traditional role of these new granules. This was important because typical buildings never use plastic granules. We had to determine the exact properties of these granules to predict their behavior in the target construction application.
One of the most important characteristics is the granules’ surface properties. As plastic is not naturally compatible with construction material, we need to change the surface energy from 91 before treatment to 142 after treatment.
This 55% increase in the surface energy and dispersive forces shows that the interaction would be enhanced if we mixed the plastics with other construction materials. This provided strong evidence that if we could increase surface energy by this much, we could ensure that the rest of the material would not segregate.
We evaluated the degree of segregation using the separation index (SI) measure. The untreated plastics directly added to asphalt exhibited an SI of 130, which was too high and would lead to high segregation. The oil treatment provided an SI of 18, while the hybrid treatment resulted in an SI of 25.
The SI for the carbon-treated plastics were slightly higher because the carbon coating covers some of the biomolecules and reduces their efficacy, but this still performs well.
We also had to perform a range of characterizations in terms of performance. We tested the asphalt’s viscosity in line with the ASTM standard, which road authorities also use for quality control.
We tested the viscosity of the neat plastic, even though we knew this was unsuitable for use in road applications because it tended towards segregation. Its viscosity was around 6000. When we applied the oil-treated biograft, we found that the viscosity reduced significantly.
There are other tests required by road authorities, for example, applying torque to the asphalt and measuring its shear resistance. It is also essential to meet resistance to rutting, cracking and fatigue specifications.
Could you expand on the importance of evaluating rutting resistance and how this is tested in road applications?
Rutting resistance is vitally essential for materials used on roads. As vehicles repeatedly pass over roads, the road eventually becomes fatigued. It is important to maintain good resistance against that repeated loading.
Rutting can cause sagging areas on the roads, which depress under heavy traffic. Excessive rutting is dangerous because it can cause hydroplaning in wet weather and uneven road surfaces.
To assess this resistance, we employed a standard used in super rutting specifications to measure the ideal specification and compared this against different samples. Using this method, we determined that the treated asphalt exhibited comparable rutting resistance to the untreated asphalt.
It was also necessary to evaluate the asphalt for fatigue resistance, and it was determined that the carbon-treated material was able to last more cycles before cracking or rutting, exhibiting 50% more stiffness and resistance to rutting compared to the untreated sample.
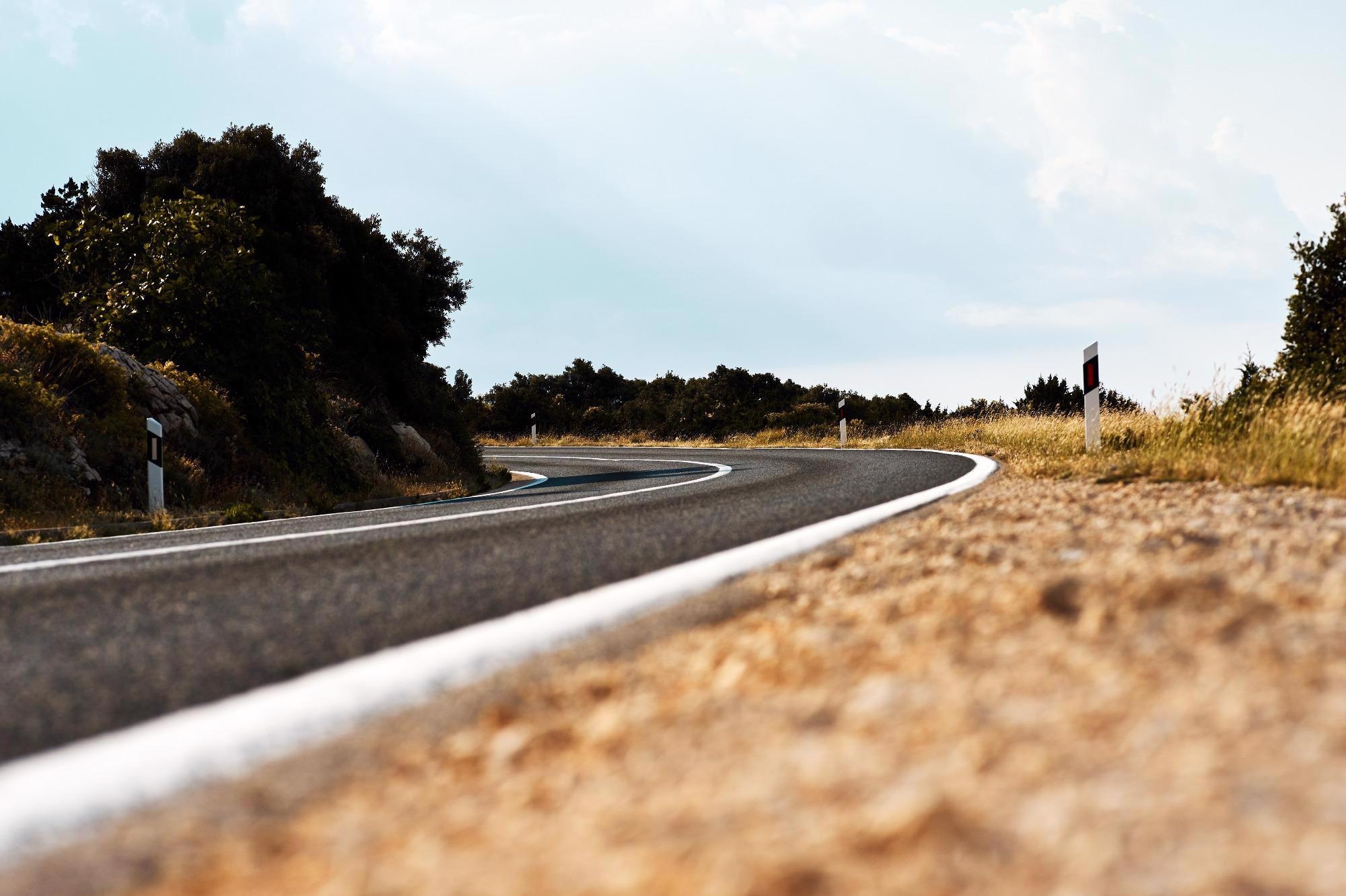
Image Credit:Shutterstock/nadia_if
What impact do weather and environmental conditions have on the potential uses of OTPG in road applications, and how are these conditions assessed?
We had to consider how rutting fatigue was affected by temperature and how this was different between seasons and in other climates.
We tested the materials at subzero temperatures to evaluate this, testing samples at -12 °C and measuring the stiffness. This was in line with an AASHTO standard test used by road authorities throughout America.
The test looks at two parameters, highlighting that road materials should exhibit low stiffness in order to ensure resistance to cracking at subzero temperatures. We determined that the hybrid-treated samples performed well and were able to rapidly relax to release stress accumulated during cold temperatures rather than cracking.
This test was repeated at higher temperatures to represent summer temperatures, and it was determined that the hybrid-treated sample performed best in this instance.
Temperature and environmental conditions can also impact the long-term aging of materials, and because OTPG materials would be embedded in roads for many years, it was important to ascertain if this would age the same way as untreated asphalt.
To evaluate this, we performed an accelerated aging test in the lab whereby we exposed the plastics to harsh UV ultraviolet radiation for around 200 hours. This was designed to simulate a region with long, hot summers which may damage or age roads.
This test determined that regardless of the type of plastic used, the treated asphalt aged much less than the untreated asphalt. We also did another test in the lab without UV radiation to evaluate the impact of thermal oxidation, achieving similar results.
With results showing that the OTPG-treated asphalt exhibited improved resistance to temperature and exposure to UV light, we wanted to understand exactly why the addition of plastic helped from the perspective of its chemical structure.
We know that as asphalt ages, it becomes grayish, indicating that some of the material is running away during the road’s use, potentially entering the environment or atmosphere. We did a study to see which molecules were doing this in the OTPG-treated samples to see if it was possible to reduce this.
This work is still ongoing, but results have suggested that the addition of oil-treated PET to asphalt keeps these molecules in the road by maintaining good interaction energy with them. Overall, we found that including the PET or end-of-life plastics in asphalt roads helps maintain their working life, providing that the plastics are compatible.
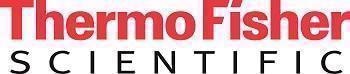
This information has been sourced, reviewed and adapted from materials provided by Thermo Fisher Scientific – Materials & Structural Analysis.
For more information on this source, please visit Thermo Fisher Scientific – Materials & Structural Analysis.
Disclaimer: The views expressed here are those of the interviewee and do not necessarily represent the views of AZoM.com Limited (T/A) AZoNetwork, the owner and operator of this website. This disclaimer forms part of the Terms and Conditions of use of this website.