Please could you introduce yourselves and your role at AIMPLAS?
Nora Lardiés (NL): I am Nora Lardies, and I have a Ph.D. in Chemistry. I have been with AIMPLAS since 2009, and I currently work at the Technological Center of Plastics. I started off in the Composites department before moving to the Chemical Recycling department. My main areas of focus at the company relate to the chemical recycling of plastic composites.
Juliette Thomazo (JT): My name is Juliette Tomazo. I work at AIMPLAS in the Synthesis department. I first worked in the Chemical Technology department, having started in 2020. Afterward, I moved to the Department of Synthesis to work on bio-based thermosetting of composites. This covers the introduction of polymers to bio-based resources which is better for both the environment and end of user due to a reduction in toxic elements typically found in these kind of materials.
AIMPLAS offers development solutions to companies in the plastics sector. Could you explain this in further detail?
NL: AIMPLAS consists of a team of 230 people and around 70% of our income is predominantly generated through research projects. These include national and regional projects, as well as European and even South Americas initiatives. Another service that we offer is technological support services, for example, testing plastics and giving technical advice to companies. We also offer training solutions through courses we have designed.
JT: We also host events where we present general ideas surrounding the challenges faced in the plastic sector. This gives customers the opportunity to come and ask questions or offer their points of view regarding the role of plastics and composites in different sectors.
NL: And to add to that, when it comes to testing, we are the leading laboratory in Spain with the most accredited certificates for testing in the plastics industry.
JT: For example, we have certifications related to mechanical testing processes for renewables in the industry. We work with various companies and contribute to recyclability processes. We also have some certifications in areas of biodegradability.
How do you help a client to get to the research and testing stage and achieve their objectives?
JT: The main goal is to add value for the benefit of society and help with the research and development of new plastics and composites. This is due to the fact some companies don't have the time and resources to conduct such research. However, it is extremely important in both the short- and long-term future to be able to offer recyclable plastic groups, bio-based plastics and to find appropriate solutions to improve across the industry.
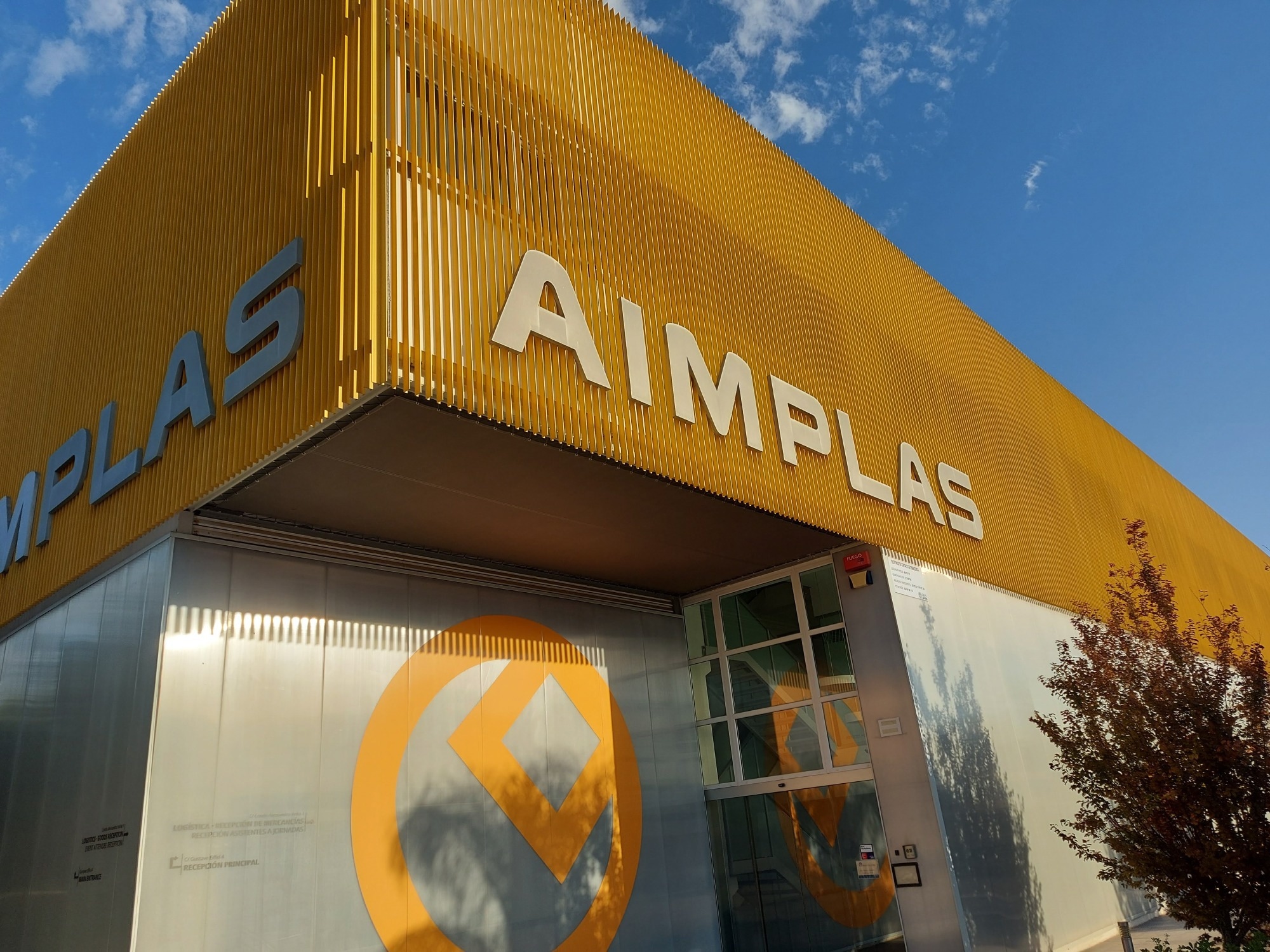
Image Credit: AIMPLAS
NL: We work from a huge facility in Valencia, where we can replicate the same processes used across industry. At the Valencia facility, the laboratory can accommodate a wide range of pilot schemes; for example, a company can come to us and say, "Ok, I want to try this new material, how will it behave? Would you use an injection or extrusion machine?" Or, for example, in the case of composites, we can offer RTL or protrusion process because it's a different method to the way thermoplastics are processed. We are well equipped to work with all kinds of plastics, composite, thermoplastics, bio-waste, and everything in-between. We have a huge facility for that. It's not only advice we offer, but hands-on help to develop our clients' projects.
Which specific industries are the most significant for you?
NL: Our work is spread out across both thermoplastics and composites. This is because thermoplastic are still in high demand in the packaging industry. At AIMPLAS, we have a department that is solely dedicated to working with the packaging industry. There is another major sector where both thermoplastics and composites are key, which is agriculture construction.
AIMPLAS also helps companies to secure funding. What are some of the ways that you approach this?
NL: Yes, we do. We assess the different goals that companies come to us with, or we approach companies to see if they want to investigate a certain area of the industry, for example in recyclability or bio waste materials, and we help them to find the best way to secure the means to do that.
As we work with a large number of clients and institutions, we are able to build a diverse consortium that serves as a funding database. For example, regarding our European projects with several partners or even smaller ones, when the project is just with one company, we help them to find the right funding consortium. We can help write applications and complete the documentation that is required for each call. If the project gets approval, then the money goes directly to the company. Whether AIMPLAS is involved in the project as a partner, or not at all, we will still prepare all documentation, and the companies pay us for the job because we help them secure funding.
JT: Companies don't always have the time to do everything they need to do. They may say, "We will not research or investigate this area because we need to write everything ourselves for the application.” This means both the company and the industry could lose out on valuable insights, so we are here to assist and help the company have better access to research possibilities.
You previously mentioned there are some significant challenges in the plastics sector. Can you give me some examples of those?
JT: One example is concerning bio-based thermosets, which is an important and emerging area of the industry. Thermoset plastics are a particular type of material that possess some interesting properties. After the polymerization process it becomes insoluble and infusible, which means that the polymerization is irreversible. Our aim is to try to re-supply the composite or also to have bio-based material in order to facilitate the recyclability of this kind of product. We try to include recyclable material or also bio-based and natural polymers in all products.
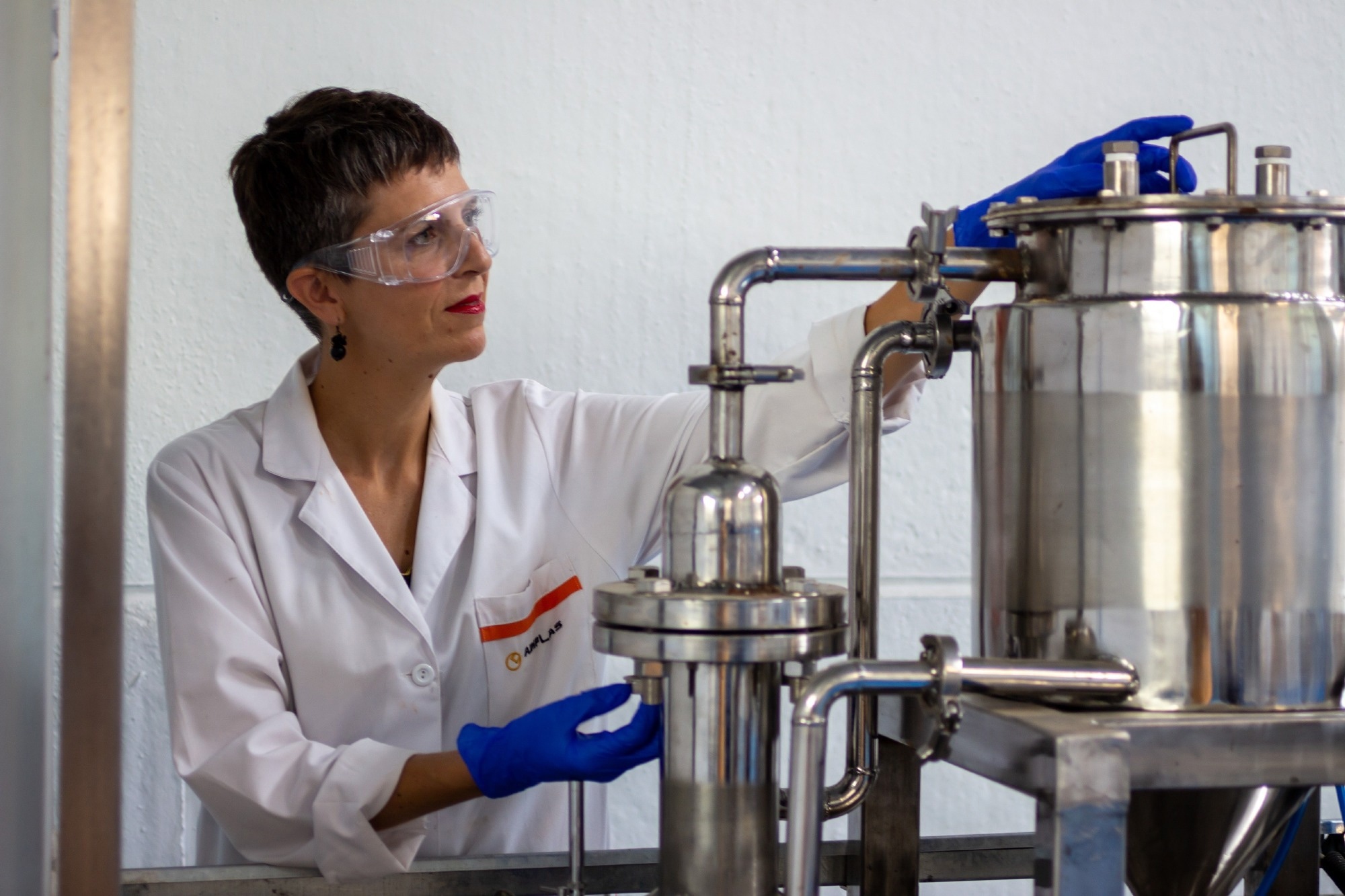
Image Credit: AIMPLAS
NL: Yes, particularly where composites are concerned, it's crucial to reduce the carbon footprint and automate processes. This is very important, for example, to improve the footprint of the automotive industry by reducing energy consumption with process alignment. Recyclability is also a key issue because, until now, mechanical recycling was practically the only way to recycle, i.e., just put it in that green bin there...
Ninety perecent of composites go to landfill sites, and that’s a pity, so we at AIMPLAS are trying to target the chemical recycling processes. For that reason, it's really important to find economically sustainable processes in order to recycle these composites.
JT: Another challenge concerns synthesis, as the challenge there is to have the same properties across materials. For example, polyester resins contain perfect molecules for achieving consistency, but they are also very toxic, and sometimes the biomass resources are not accessible. Therefore, we need to try to find a solution. This is a major challenge because we need to have a safe material with precise mechanical properties, which can be very difficult to achieve. So, we test different kinds of biomass resources.
Why do you think it's important for AIMPLAS to attend trade shows like JEC World, and what do you hope to gain from being at the show?
NL: We come to meet new potential customers, build networks, and hopefully create new project opportunities. To let the plastics and composite sector see what we are doing and exchange knowledge. The industry now is looking for ways to recycle composites and biocomposites and from AIMPLAS we can help companies in this subject because we have been working in these chemical recycling technologies and we have the right facilities for that, although those are new technologies.
JT: We also want to show that AIMPLAS can make it possible to introduce new processes and create innovative products while developing new recycling methods and, in the case of polyester, safely reintroducing monomers to make new products with the same properties.
How do you imagine the company will grow and evolve in the coming years?
NL: We are trying to encourage a circular economy. We are also building a new pilot plant and maintaining our focus on chemical recycling to make things more circular. The company vision is that by 2028 we will double the number of staff as we are a company that is growing rapidly. Back in 2020, we were around 150 people and now around 230, so we are on track.
JT: We are also developing synthesis areas and focusing on regulations. In plastics, these change a lot and very quickly. So we are here to help companys keep track of regulations and to develop new products in accordance.
NL: We also want to have more income from testing and expand our global network. Early on, we were focused on Spain and Europe, but moving forward, we’re also going to start building networks in the USA.
More from JEC: How 5M Continues to Grow in the Transport and Space Sectors
About Nora Lardiés and Juliette Thomazo
Dr. Nora Lardies Miazza Ph.D. in Chemistry by the University of Zaragoza since 2005 during this time she stayed at the University of Manchester and Eli Lilly and Company (Estados Unidos). After that she worked as a post-doctoral researcher in conductive polymers at the Institute of Molecular Science during two years between 2007 and 2009; this year she joined AIMPLAS as a researcher. Since then she has been involved in technical assistance evaluation and processing technologies of composite materials: optimisation of techniques development of new materials improvement of properties. Dr. Lardies was coordinator of the FP7 european project COALINE (regarding pultrusion process) and Retos Colaboration Project EOLO+ (antierosion coating and reduction of weight in wind Blades). Since January 2020 she is working at the chemical recycling area in AIMPLAS coordinating projects like FOAM2FOAM (circular economy in polyurethane foams through chemical recycling) ELIOT (End of life for biomaterials) EROS (circular economy in composites: from wind sector and aeronautic to the ceramic industry and transport) RECITURF (recycling of artificial turf by biological processes and solvolysis).
Juliette Thomazo- -Jegou has obtained her master’s degree in engineering specializing in material science in the Graduate school of Engineering of Rennes (ESIR- University of Rennes 1) and her master’s degree in management specializing in the development of international projects in the graduate school of management of Rennes (IGR- University Rennes 1) in 2020. During this period, Juliette Thomazo- -Jegou has studied the synthesis, the material’s design, the physical, mechanical, and chemical characterization of materials (polymers, nanomaterials, biomaterials, ceramics, metals and alloys, and glasses). During her studies, Juliette Thomazo- -Jegou has completed several internships, one of them in the Chemical Technology Institute (ITQ) under the supervision of Dr. Francesc X. Llabrés i Xamena. During this period, she obtained a training in the development of sustainable Metal Organic Frameworks (MOF) for the heterogenous catalysis. In 2020, she completed another internship in AIMPLAS under the supervision of Dr. Rafael Alonso Ruiz and she worked on the development of new anti-mite solutions using nanotechnology. From February 2021 to December 2022, Juliette Thomazo- - Jegou is working in AIMPLAS as a researcher in the Chemical Technology group working on biobased thermosets composites and also on encapsulation. Since January 2023, she is working in the Synthesis department on biobased polymeric materials.
Disclaimer: The views expressed here are those of the interviewee and do not necessarily represent the views of AZoM.com Limited (T/A) AZoNetwork, the owner and operator of this website. This disclaimer forms part of the Terms and Conditions of use of this website.