In this interview, AZoM speaks to Instron's Phil Levesque and Charlie Pryor about the importance of mechanical testing for electric vehicle batteries.
Please can you provide a brief overview of the mechanical testing requirements in the EV battery industry and how they have evolved?
Most mechanical testing in the EVB industry includes tensile, peel, and compression testing. Tensile tests primarily involve testing current collector foils (aluminum and copper), separator film, and weld strength.
Peel testing primarily encompasses testing the electrode adhesion to each current collector (anode and cathode) and can be performed in various ways.
Compression testing primarily involves foam, cell-level, and separator film puncture testing. There are destructive tests, such as nail penetration, and non-destructive tests, such as swell testing, for cell-level testing. In addition to these mechanical tests, several electrical tests are performed, including testing resistivity, impedance, and voltage, and more elaborate tests such as electrochemical impedance spectroscopy (EIS).
These electrical tests are performed while a cell or battery material is undergoing mechanical testing, while the cell is in use, or is being charged/discharged.
The highest testing volumes generally pertain to quality control testing of thin foil, current collectors, and separator film.
Testing volumes for quality control materials are significant, but Instron has also collaborated with EVB suppliers to develop tests for many R&D applications, such as weld testing, anode and cathode adhesion testing, and puncture testing.
Tests originating at the R&D level are often incorporated into a company’s quality control assessment of materials, components, or cells.
Many battery materials have evolved over the last several years to optimize parameters such as energy density and safety, but the testing applications have not changed significantly.
The most significant change to testing programs has come from maximizing throughput and repeatability of results.
Companies ramping up production quickly begin to understand how much effort is required to complete adequate quality control testing. Therefore, any way that Instron can help improve throughput while reducing operator variability in testing is important.
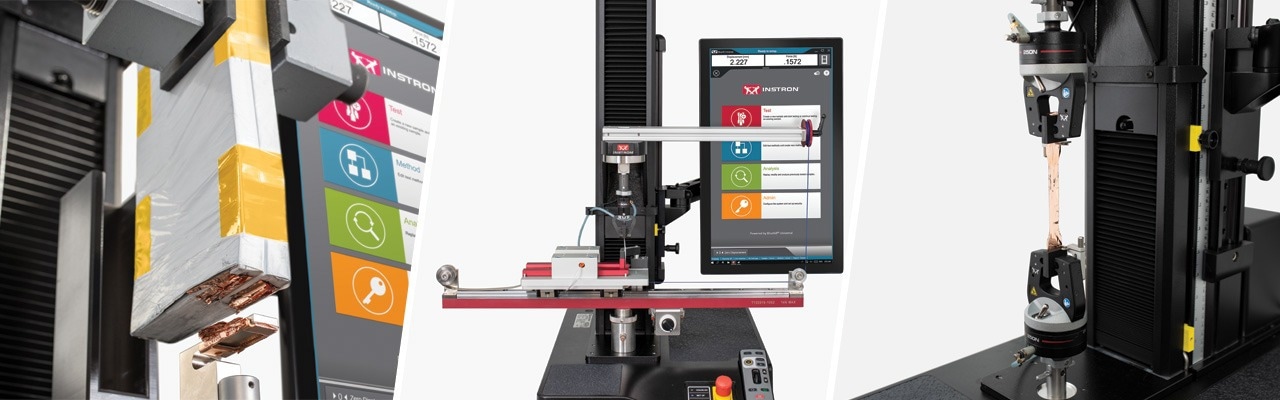
Image Credit: Instron
How has increased demand influenced the design of these batteries?
In general, the need for an increased EV range has driven the diversification of battery technologies and improved performance. To achieve greater range in vehicles, manufacturers are compelled to enhance the battery's energy density and, to limit volume, employ thinner materials. This introduces new failure modes and manufacturing challenges that battery manufacturers and their suppliers must address to uphold the high levels of quality necessary for battery operation and safety.
What are the pros and cons of both electrical and mechanical testing?
Performing both types of testing simultaneously enhances the customer’s testing capabilities and the value of the data obtained from a seemingly simple uniaxial testing machine.
It is a two-pronged approach that can provide valuable data and potential key indicators of deficiencies in the manufacturing process. Ultimately, this leads to the earlier exclusion of inadequate materials or cells and prevents them from making it to the end of production.
Combining electrical characterization equipment with a mechanical tester that can acquire all the data in a synchronized manner presents several advantages.
First, the correlation between mechanical and electrical events or changes in conditions can be made much more evident.
A simple overlay of plots and data allows users to fully appreciate the effect of the change in any one condition, regardless of whether it is a change in mechanical forces, electrical state, or even temperature. This form of enhanced testing increases the value of the collected data and comes with the added benefits of acquiring time-synced and centrally managed data. The benefits can even extend to reducing the number of specimens to be prepared for testing.
Ultimately, varying a cell or pack's mechanical and electrical conditions will better replicate its real-world use scenarios and highlight its potential failure modes.
What is static mechanical testing (as opposed to dynamic)?
Mechanical testing can commonly be referred to as static or dynamic testing. Static mechanical testing is generally performed at slower speeds and strain rates, with a lower testing frequency. It is also generally unidirectional.
On the other hand, dynamic testing is done primarily at faster speeds and higher frequency and is sometimes performed in multiple directions. Test durations are generally much longer for dynamic tests than static tests, as with fatigue testing.
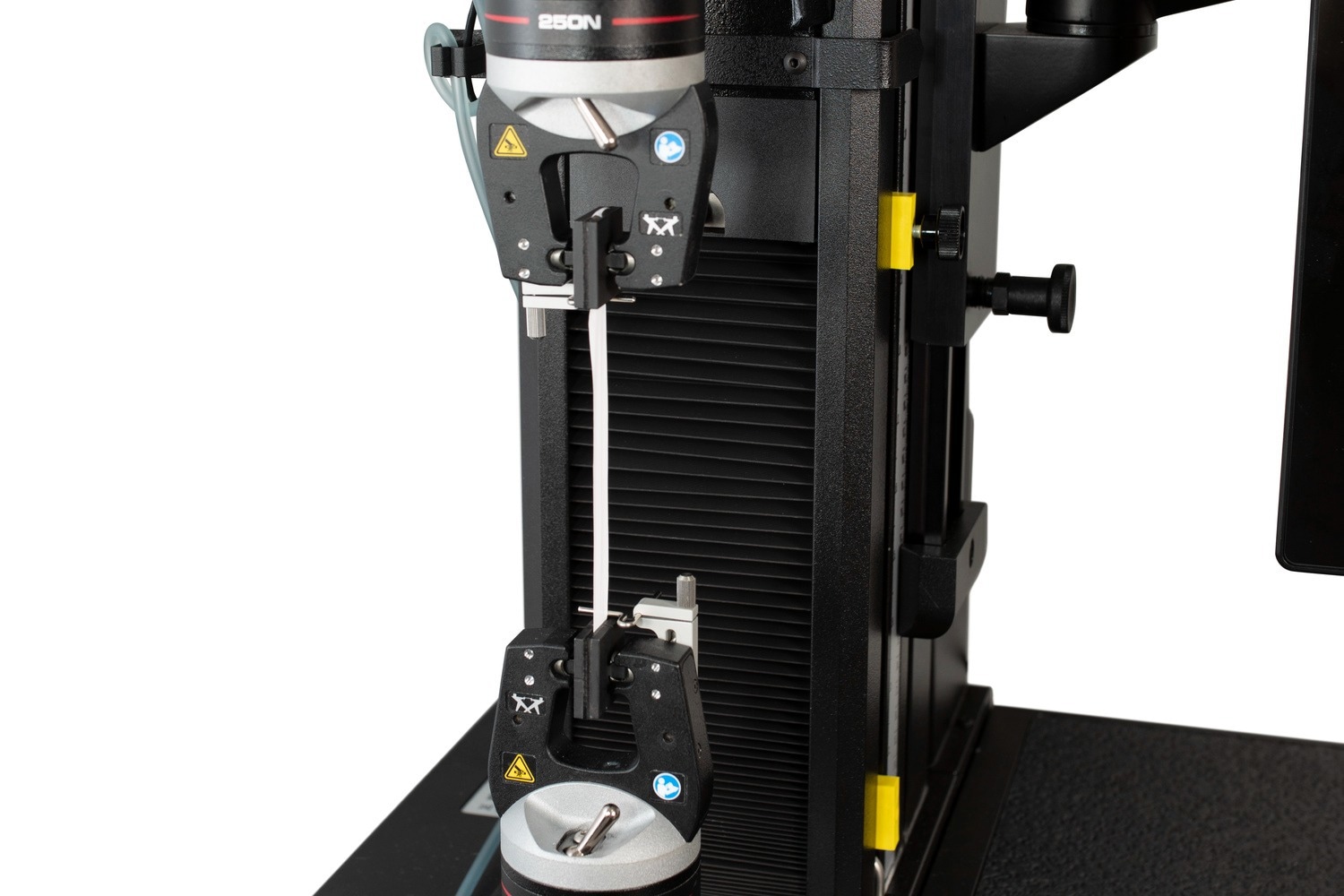
Image Credit: Instron
Can you describe the range of this testing methodology? For instance, which battery components can be tested?
Virtually any part of a battery can be tested mechanically. The range extends from full cells, modules, and packs to the individual materials that constitute the inner workings of a battery. Nearly all components of these assemblies, both internal and external, undergo testing to ensure the quality and safety of the cells produced.
The companies and their customers determine the frequency and throughput of each test.
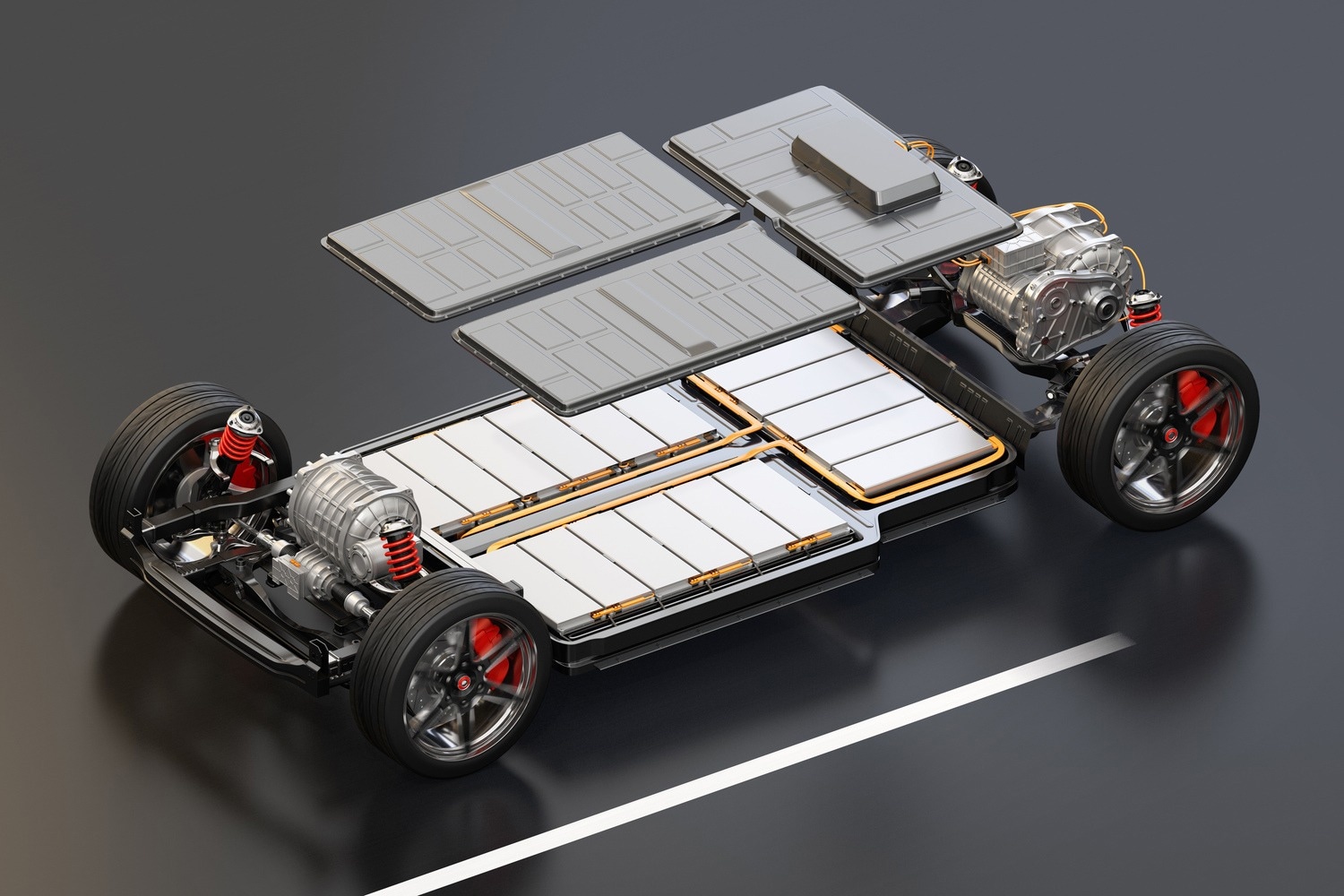
Image Credit: iStock
How has EV battery technology evolved since its inception, and how has it affected mechanical testing requirements?
Batteries have evolved significantly over the past few years. Their energy density has increased, their volumes have expanded, and their management systems have evolved.
Simultaneously, expectations regarding their performance have also risen. Various battery types have emerged, with three main Li-ion battery types now prevailing.
Solid-State Batteries (SSB) are currently under active development. While these may not be immediately poised for mass production by multiple manufacturers, they appear to represent the next generation of battery technology.
Material testing requirements have evolved in response to these new technologies and their changing material properties. Specimens must now be handled differently, alignment has become more crucial than ever, and gripping is a vital aspect of the testing solution.
Required accuracy levels have also increased significantly. These changes extend to manufacturers, who now require systems and labs to test a wide array of materials, including adhesives and welds used in cell fabrication and characterization.
This is where universal testing machines prove their value as versatile tools capable of conducting tests for various applications.
Can you describe the challenges that have arisen as a result of this evolution?
A recent challenge within the industry is the repeatability and throughput of testing. Many companies are grappling with scaling up their production to meet the high demand for EV batteries while facing operator turnover and training challenges.
Additional challenges are associated with ensuring safety while testing various assemblies and materials. As technology has advanced, material behavior has evolved, necessitating the performance of additional tests.
How does Instron address the evolving challenges in the EV battery industry?
The key for us has always been to work closely with customers. We build lasting relationships with manufacturers of all sizes by listening to their needs, understanding their application requirements, involving them in the design and decision-making process, applying our decades of material testing know-how and expertise, demonstrating our capabilities to them, being flexible in our designs, and exchanging information with them for the benefit of both parties. We stay up-to-date on technological news and trends, follow standard updates, and strive to stay ahead of the game regarding technology shifts and trends.
What specific advancements or innovations in mechanical testing equipment and techniques have been developed to meet the evolving needs of the EV battery industry?
Instron has collaborated with multiple battery manufacturers to develop customized fixturing and aids to meet the demand and throughput requirements. These include specimen preparation, alignment devices, and fully customized fixturing for various applications.
With an understanding of battery testing applications and the market, Instron has worked to create fixturing that optimizes throughput and minimizes operator variation between tests. For instance, Instron has designed a customized fixture for tack testing (a type of electrode adhesion testing) that allows operators to set up a single specimen but obtain five tests, one after another, without additional preparation between tests.
Tack Testing Fixture - Testing the Adhesion of Electrodes
Instron has also provided ways to improve specimen insertion and alignment of delicate materials such as separator film and foils.
When done manually, many operators can have difficulty inserting and aligning these delicate materials in the testing space, leading to poor throughput and repeatability.
Instron places significant emphasis on the safety of operators and equipment during the development of customized fixturing. Instron frames are also available with safety features, such as operator protection workflow, collision mitigation, specimen protection functionality, and smart-close air kits.
With the rapid pace of technological advancements in the EV battery industry, how do you anticipate the future of mechanical testing evolving, and how is Instron prepared to adapt to those changes?
The technological advancements we are witnessing are changing elements such as the thickness of films and foils while introducing new materials into cell, module, and pack fabrication.
This is primarily undertaken to enhance energy density but also introduces new failure modes, necessitating new approaches to testing materials and assemblies.
We are addressing these emerging challenges by designing our systems to be modular and flexible, allowing for the use of various fixtures. Furthermore, we can develop and integrate new fixtures into existing systems and incorporate third-party instruments to expand their capabilities further.
We are mindful that different customers may require varying levels of throughput and testing assistance. To address this, we have developed different solutions for manual specimen loading and integrated assisted operation using devices such as cobots. We also offer fully automated systems where operators are entirely removed from the testing process.
While technological changes are undoubtedly creating the need for new products and capabilities, it is evident that automation and in-line testing will play a critical role in enabling testing to keep pace with production.
As increased adoption of electric vehicles (EVs) drives investments in EV and battery production facilities, production volumes will inevitably rise, demanding increased testing throughput.
We currently offer automation solutions that can assist manufacturers in testing more specimens within a given timeframe, delivering better repeatability and throughput than manual operators, all within a footprint scarcely larger than a standalone frame.
Operators are thus freed up to focus on more critical tasks than loading and unloading specimens.
Moreover, the system features such as specimen measurement devices and customer database connections significantly enhance material traceability and simplify data management.
We are continuously enhancing the capabilities of our automation systems. We will continue to deploy them globally to support our customers in completing their testing and achieving their production and quality objectives.
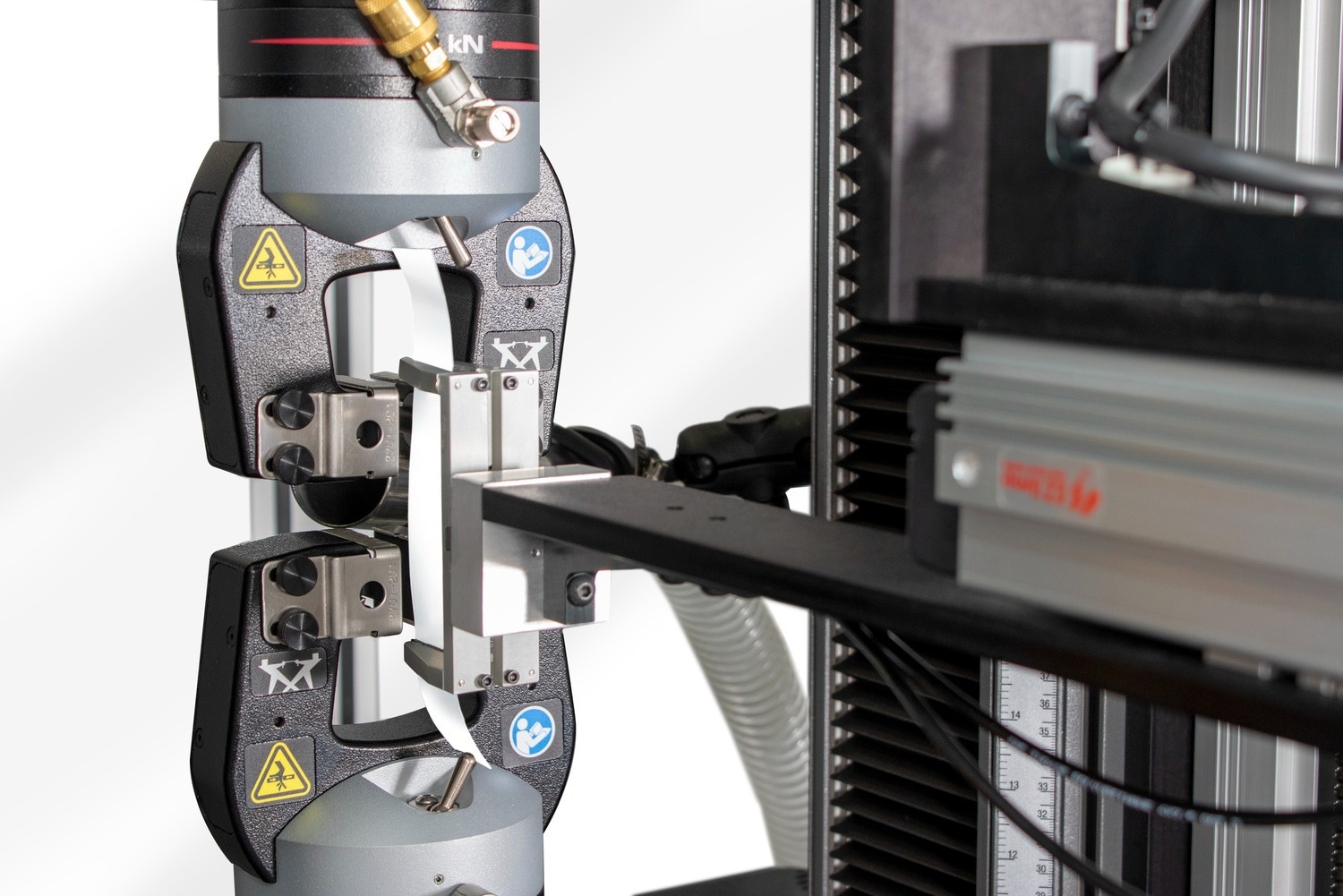
Image Credit: Instron
About the speakers
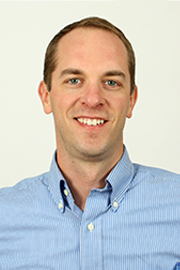
Phil Levesque serves as the Strategic Marketing Manager at Instron, where he focuses on developing solutions for emerging and fast-growing technologies, specifically in the field of electric vehicle battery testing.
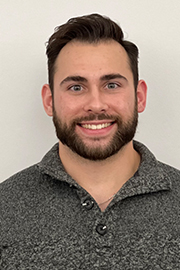
Charlie Pryor is a Senior Application Engineer at Instron with a specialty in electronics and battery materials and technology testing, dedicated to optimizing test setups and processes for materials testing professionals.
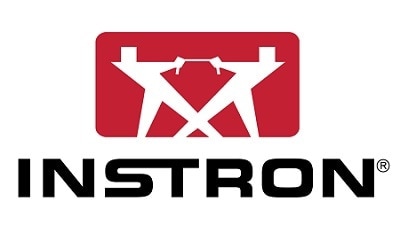
This information has been sourced, reviewed and adapted from materials provided by Instron - USA.
For more information on this source, please visit Instron - USA.
Disclaimer: The views expressed here are those of the interviewee and do not necessarily represent the views of AZoM.com Limited (T/A) AZoNetwork, the owner and operator of this website. This disclaimer forms part of the Terms and Conditions of use of this website.