Following JEC World 2023, AZoM catches up with Dr. Humphrey Carter from Compo Tech PLUS, spol. s r.o. to discuss the technology the company has been promoting this year.
Please can you introduce yourself and your role at CompoTech?
I am Dr. Humphrey Carter EngD., Head of Business Development, and I'm based in the UK for CompoTech. My role is wide-ranging, divided between the technical, sales, and marketing areas of the business. With a technical background, I am working closely with customers on the initial design and concept stage of enquires. This helps me keep my finger on the pulse of our technical developments and is useful to the other parts of my roles.
For the marketing elements, I am distilling the technical highlights and projects into relatable interests and clear messages for the broad range of our customers across the industries we serve. I also manage the content across different media, web and social, and target events.
Could you describe the types of composite products that CompoTech produces as a manufacturer?
Our composite products are dictated by our advanced winding technology, which is 6-axis robot-assisted automated filament placement and winding. We have developed our own machine and control software from the start of CompoTech nearly 30 years ago. Through continued development of process and composite production, we can offer this technology now to our customers in addition to producing the composite parts.
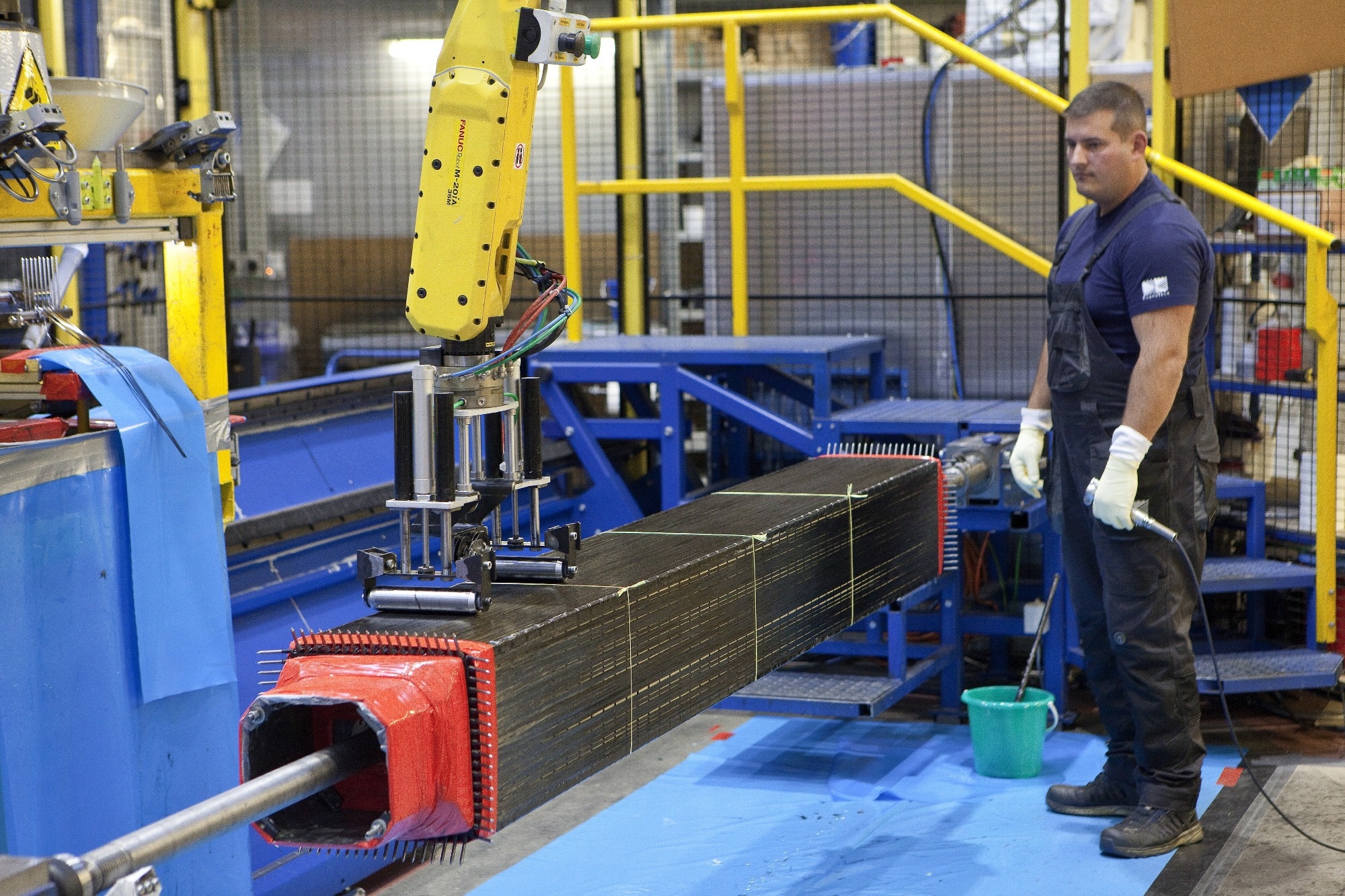
Image Credit: CompoTech
How does CompoTech support its customers from initial design to final application? Can you walk us through this journey?
Our typical customer, especially in industrial applications, is coming from a non-composite background. There is a lot of understanding and explaining of the basics of composite design and working through the feasibility of their project coming from metallics design. How best to approach the design and optimization before then looking at the FEA, which can give key performance numbers regarding stiffness, strength and natural frequencies of a structure?
Why do you think it is important to be involved in all aspects of the design to installation pipeline?
We are keen to highlight when working with machine producers that the design of the composite and machine need to be considered together so that the carbon fibre structure is not an afterthought to the design. It means we can work together to design all the attachments required for such a structure used in the machine, and the machine can be designed for lightweight and highly stiff moving parts. This, in turn, allows lighter motors, rails, and/or actuators to be used. Ultimately the most beneficial and efficient use of the composite material and gains in the machine's productivity can be made this way.
Could you tell us more about your research and development team and activities within CompoTech? What kind of capacity do you have?
Out of a team of 60, we have roughly a third involved in design, engineering, and development. We pride ourselves in the innovation and research we put into our projects with our customers and industrial partners and our collaborative work with universities. In fact, this year, we have six funded projects awarded to us for various applications.
Our R&D team works in both the finite element analysis as well as the structural testing to verify our results. We also work very hard with our winding technology and software to be able to improve the manufacturing process. We are constantly working to improve our processes and develop the design and structures that we produce with our technology to be able to offer optimal high-performance parts with automated manufacturing.
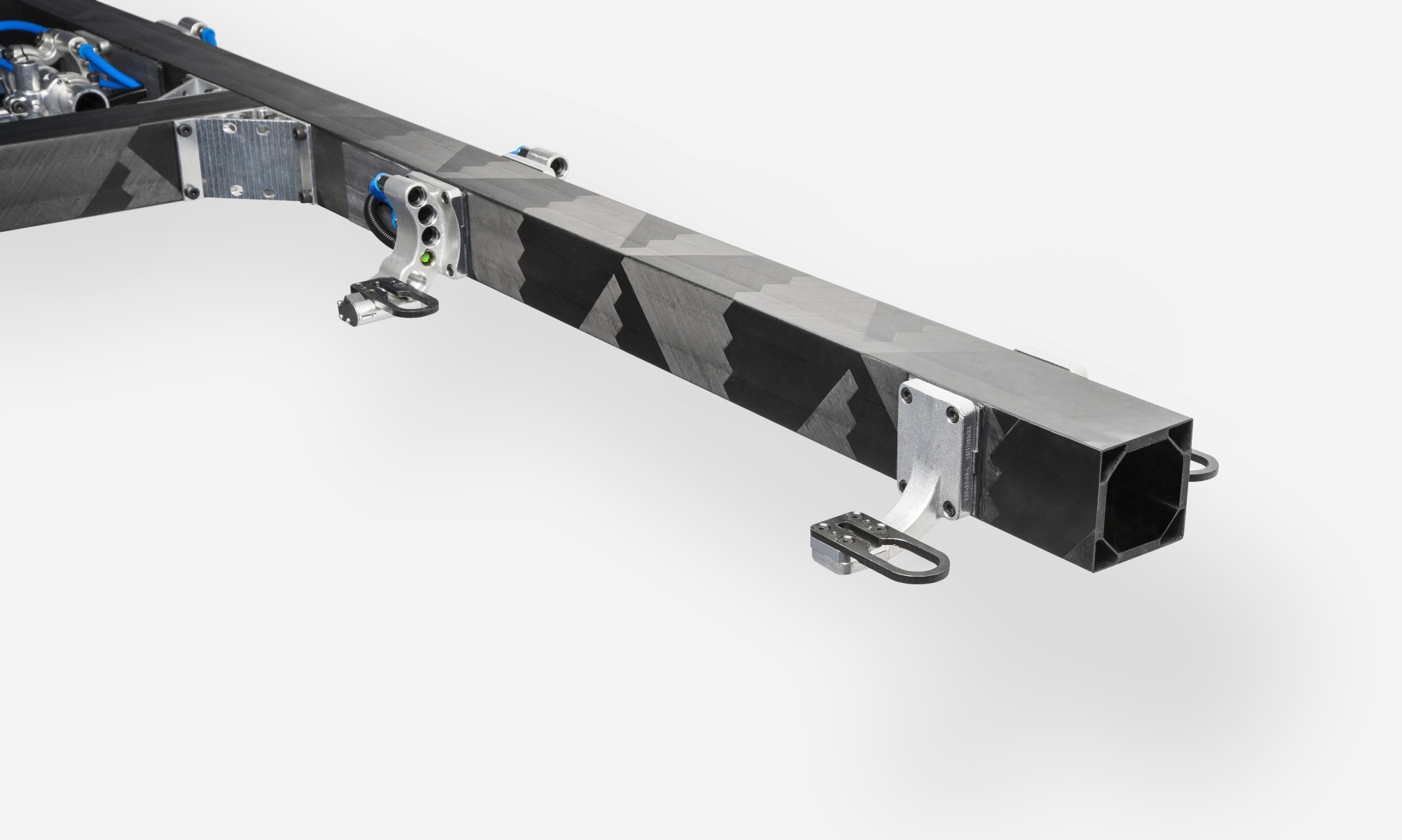
Image Credit: Bilsing Automation
Which industries do you work with most closely?
We work across all industries, but our niche area of composites development is in applications for machine tools and automation. We are producing gantry structures for laser cutters and other 2-axis machines, axis structures for milling machines and automation, as well as end-of-arm tooling for automation robots and carbon fibre tool structures such as milling heads and boring tools. However, we also apply technology from these developments into other areas such as automotive, aerospace, and, as you might expect with filament winding technology, marine structures for yachts have been historically, and still today, a key market for us.
Why should people pay attention to the composite sector?
CompoTech is in quite unique position, with our experience in the machine tool sector working closely with customers not familiar with composite materials. We see many questions, scepticism and misconceptions regarding the design and possibilities. With a little bit of awareness, we see customers pay more attention and not just to the composite part but to the overall design outcome. We also try to limit expectations in that composites are not the magic ingredients that can achieve everything at the same time.
However, in all sectors, especially in this environment with a race to net zero and drive for sustainability, composites and, more specifically, carbon fibre composites should receive attention through their capacity for lightweight structures. The relative density of the material, with considered design for the fibre directions, can improve the overall economic and ecological lifetime cost.
You recently exhibited at JEC World – The Leading International Composites Show. Why is it important for CompoTech to engage with events like this?
I think coming together in one place as a whole supply chain of composite technology from design, materials, production, and application is possibly unique to the composites sector and vital to the industry. For CompoTech, we have shown some parts new to the industry that can open up possibilities. For example, a part we developed for industrial application can be regarded in a new application through different eyes. This last edition was also our chance to show our Advanced Winding Technology, which was well received.
You were also a finalist for the JEC World Innovation Awards this year with your Integrated Loop Bike Frame. Could you please tell us more about this technology?
Our Intergrated Loop Technology (ILT) uses the automated fibre placement process to create a structure and connection in one process. In the case of the bike frame, this means the axial fibre is placed along a top tube or down tube and continues, with some clever tooling, around a loop for the headtube as an integrated connection between the two components. It means the connection is optimized for the fibre used and reduces the requirement for the large amounts of machining and manual labour used in the hand lamination of joints.
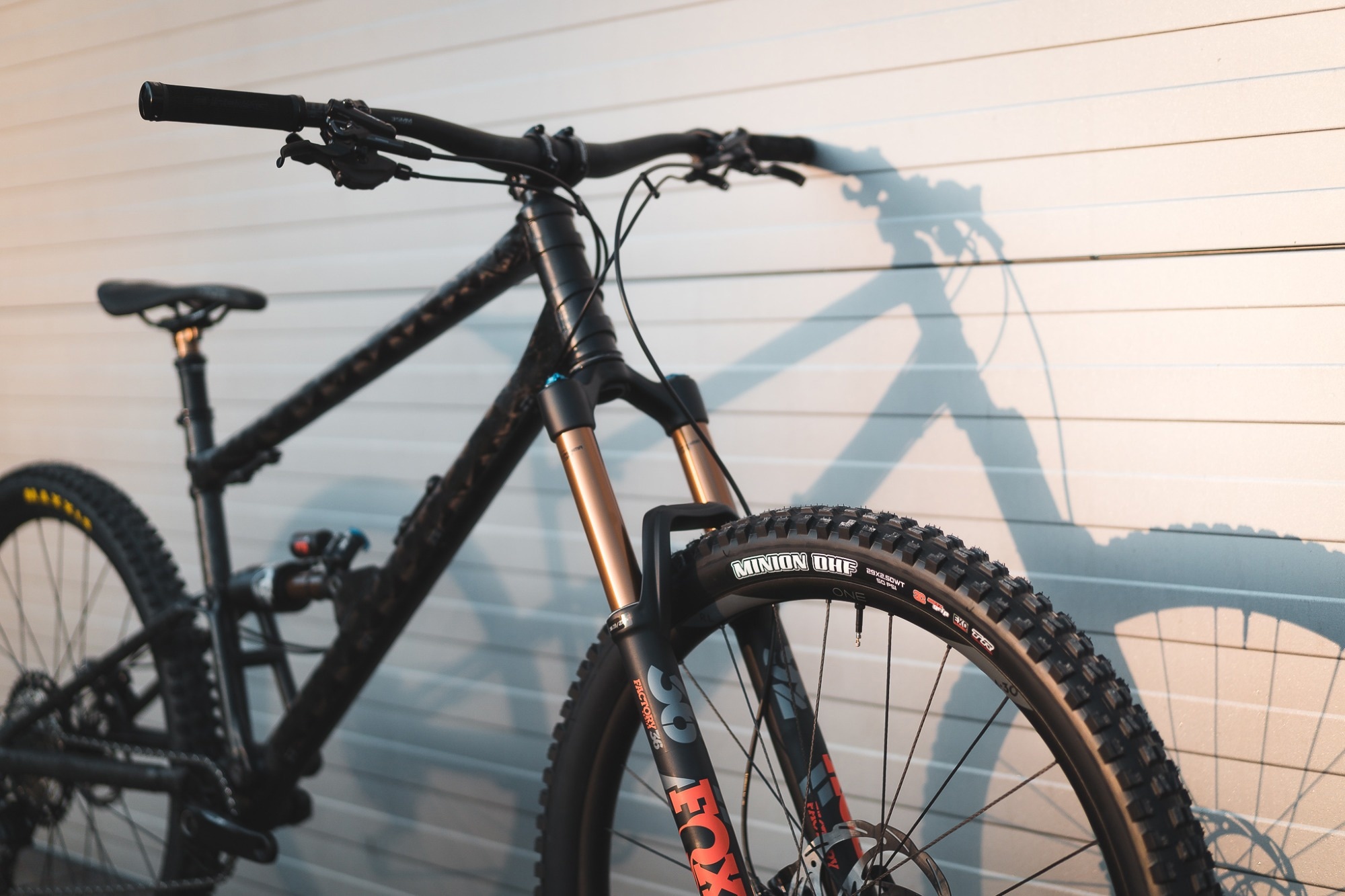
Image Credit: CompoTech
We also use this technology in other applications where a bushing or fixture is integrated into the ends of the main fibre wound structure. Handling manipulation assemblies or other automation structures with articulating connections is one area where we are finding success with this technology.
Do you have any other exciting developments on the horizon?
As mentioned, we have a few development projects. We are working on applications in hydrogen storage with linerless tanks, aero structures, and telescopic structures, as well as the development of logistics pallets. We are working with partners in the laser cutting sector to model the performance of carbon gantries so that the carbon structure and laser control software can be optimized for the highest performance.
We are also working on our own process developments to be more automated on either side of the winding stage. We will turn our ILT bike frame project, called CDuro, into a small-scale production mountain bike with direct sales. And on top of this, we are developing our own winding design software, which will integrate with our control software for the advanced winding technology.
About Dr. Humphrey Carter
Dr. Carter's background is in engineering, having studied a mechanical engineering master's and then an Engineering Doctorate looking at epoxy nanocomposites at Southampton University and Industrial partnership with Gurit on the Isle of Wight.
His first contact with CompoTech came as an undergraduate ERASMUS exchange student at Czech Technical University in Prague in 2002. He has been full-time at CompoTech now since 2010 but is based in the UK, working on both the technical development and bringing in new projects in diverse applications for marine, industrial machinery, agricultural machinery, formula one and hydraulic cylinders. Today his role is more predominantly business development. Humphrey is also a keen cyclist, kitesurfer and sailor. He finds that there is often application of composites in these pastimes and being able to combine work and passion offers a lifestyle balance that benefit both.
Disclaimer: The views expressed here are those of the interviewee and do not necessarily represent the views of AZoM.com Limited (T/A) AZoNetwork, the owner and operator of this website. This disclaimer forms part of the Terms and Conditions of use of this website.