What are structural fiber-reinforced polymer composites (FRP)?
Structural fiber-reinforced polymer (commonly known as “FRP,” or sometimes as “fiberglass”) refers to a composite material comprised of a polymer resin matrix that is reinforced by embedded glass (or carbon) fibers. The attributes of the component are influenced by the manufacturing technique, along with factors such as the type, arrangement, quantity, and positioning of the fibers within the composite.
This variability allows for tailored configurations within components of identical dimensions. Such flexibility proves particularly advantageous based on the intended application and desired performance traits. Nonetheless, it is imperative to have confidence in your composite’s manufacturer, given the disparities in quality among different composites.
Various manufacturing approaches can be employed for crafting structural composites. Among these, the pultrusion process stands out for its consistent outcomes in high-volume production, and it remains one of the most cost-effective methods for forming structural FRP components.
Can you tell us about some of the uses and applications of FRP composites?
FRP composites find application across both architectural and industrial domains. They frequently serve as substitutes for traditional materials like wood, steel, or aluminum, replacing I-beams, wide flange beams, angles, channels, tubes, and similar structural shapes. FRP composites also stand in for metal plates, offering a versatile range of uses.
The adaptability of FRP allows it to be used in applications such as:
- Walkways (including grating, handrails, and structural components)
- Platforms
- Enclosures
- Stair structures
- Pedestrian walkways
- Handrails and fencing
A comprehensive collection of case studies showcasing pultruded FRP applications can be explored on the Strongwell website.
Image Credit: Strongwell
Strongwell is recognized as the world’s leading pultruder of FRP. Can you tell us more about how the pultrusion process works?
Pultrusion is a manufacturing process aimed at producing continuous lengths of reinforced polymer structural shapes featuring a consistent cross-sectional profile.
The process involves pulling raw materials — an amalgamation of liquid thermosetting resin and reinforcing glass fibers — through a heated steel forming die employing a continuous pulling mechanism.
The result is a sturdy, structural composite well-suited for its intended use. While many are acquainted with the extrusion process involving the pushing of pellets or chopped fibers through a die, pultrusion distinguishes itself by employing uninterrupted lengths of reinforcements that are consistently pulled through the die.
How does FRP compare to traditional structural materials? What benefits do FRP composites offer over their alternatives?
FRP presents numerous features that enhance its appeal as an option. Some of the most significant include:
- High Strength: Pultruded FRP exhibits equal or greater strength than structural steel pound-for-pound.
- Lightweight: Strongwell’s pultruded FRP shapes weigh approximately 75-80% less than steel and 30% less than aluminum. This weight reduction reduces transport expenses, simplifies installation, and lower overall weight of the assembled structure.
- Corrosion Resistance: When appropriately saturated with the correct resin and cured, FRP remains unaffected by a wide range of corrosive environments. FRP does not rust or decay. It proves to be an exceptional choice across various corrosive environments. Strongwell provides a comprehensive Corrosion Resistance Guide to assist users with corrosion-related inquiries.
- Low Conductivity (Heat and Electrical): Fiberglass FRP serves as an excellent insulator, displaying minimal thermal and electrical conductivity. This quality positions it as a preferred option for applications involving temperature sensitivity or electrical concerns.
- Electromagnetic Transparency: Fiberglass allows radio waves, microwaves, and other electromagnetic frequencies to pass through, making fiberglass-based FRP highly suitable for cellular applications.
Image Credit: Strongwell
In terms of installed cost, how can the utilization of FRP save money concerning construction budgets? how do FRP composites assist businesses in diminishing project timelines and alleviating the demand for highly skilled workers?
One of the primary advantages of opting for pultruded FRP, something that installers promptly acknowledge, is the simplicity of fabrication and installation processes. Due to the lightweight nature of FRP, there is a reduced requirement for specialized lifting equipment at the job site.
Similarly, the handling process is more convenient compared to traditional structural materials. Assembling FRP generally revolves around bolted or bonded connections, eliminating the need for welding or obtaining hot work permits and requiring a reduced number of skilled laborers on-site.
In cases where on-site fabrication goes beyond mere assembly, standard carpenter’s tools equipped with carbide bits and diamond grit blades can fulfill tasks such as cutting and drilling.
This approach diminishes the risk of on-site injuries or work downtime frequently associated with traditional materials and installation equipment. In short, construction timelines are reduced, equipment needs are streamlined, and the dependence on specialized labor is mitigated. These combined factors result in substantial time and cost savings for construction projects.
How do you see the future of FRP composites evolving over the next ten years?
FRP composites are not new. Strongwell has been pultruding fiberglass-reinforced composites since 1956. Back then, simple channels, ladder components, and similar items were the primary shapes being manufactured. Over the following years, the push for more environmentally friendly structural materials will compel specifiers and designers to examine composites more closely.
This will also be driven by the increasing requirements for structures to have greater durability in harsher environments. More engineering schools are now offering courses in composites, and degrees in composites engineering and related fields are on the rise.
This is encouraging the next generation of engineers to realize that there are alternative structural materials to consider in designs instead of only resorting to them when traditional materials fall short.
Although materials like steel, wood, aluminum, and concrete have their place in many applications, more and more engineers understand that vastly superior materials are available. They are applying this knowledge by proposing designs that incorporate composites more extensively than ever before.
Image Credit: Strongwell
Where can our readers find further information?
The previously mentioned case studies serve as enlightening examples for individuals contemplating the use of structural FRP, demonstrating its potential. Another great resource is Strongwell’s page on “Why fiberglass”, which expands on much of this interview’s content.
Readers are encouraged to explore the product literature section on the Strongwell website to access more comprehensive information about FRP.
Lastly, for those interested in delving deeper into structural FRP, Strongwell offers free professional development sessions, both online and in-person, allowing engagement with their technical team. These online and in-person sessions can be scheduled by filling out the Contact Us form on the Strongwell website.
About Randy Montgomery
Randy Montgomery serves as the Manager of Industrial Products at Strongwell. In this role, he leads a dedicated team responsible for drafting, detailing, and estimating, all of which play a crucial role in advancing and supporting various
fabricated projects. Montgomery’s affiliation with Strongwell dates back to 1992, when he embarked on his journey as a Drafting Coordinator. Prior to becoming an integral part of Strongwell’s composites sector, Montgomery garnered extensive experience within the steel industry, where he held positions ranging from Structural Detailer and Estimator to Project Manager, a career path he began in 1978.
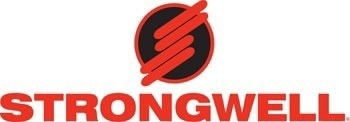
This information has been sourced, reviewed and adapted from materials provided by Strongwell Corporation.
For more information on this source, please visit Strongwell Corporation.
Disclaimer: The views expressed here are those of the interviewee and do not necessarily represent the views of AZoM.com Limited (T/A) AZoNetwork, the owner and operator of this website. This disclaimer forms part of the Terms and Conditions of use of this website.