Computed Radiography (CR) is a digital imaging technology where phosphor imaging plates replace conventional radiographic film. After the imaging plates are exposed to radiation, the CR scanner utilizes a focused laser to read the data from the imaging plate and transfer it to software that provides an image on a computer.
CR was introduced as a novel technology in the mid-1970s, with advancements made with the technology throughout the 1980s. This led to CR being embraced by the medical market at this time, although these CR scanners were crude by today’s standards and typically could only produce low-resolution images.
This was due to multiple factors, including the laser spot size, the design of the scanner, and the technology of the imaging plates used, which had large grains of phosphor.
As technology advanced, CR became employed in industry to replace film radiography in some limited applications. Code-quality images, however, were not possible until scanner technology improved and better imaging plates became available.
Laser Spot Size
Many early industrial CR scanners had a laser focused to deliver a spot size of 50 microns at the imaging plate. This releases an optimum amount of signal from the exposed plate and creates a high signal-to-noise ratio (SNR) and good contrast.
However, this leads to limitations regarding the basic spatial resolution (SRB) of the scanner, as well as the size of indications that may be imaged.
Among the developments to CR scanners during the 2000s was a smaller laser spot size. When employed with higher-resolution imaging plates, this smaller laser spot enabled the detection of smaller indications, allowing weld-quality images to be produced.
However, the smaller laser spot size reduces the signal released from the imaging plate. This limits the signal-to-noise ratio (SNR) and image contrast, and subsequently also limits the utility of the scanner for specific applications.
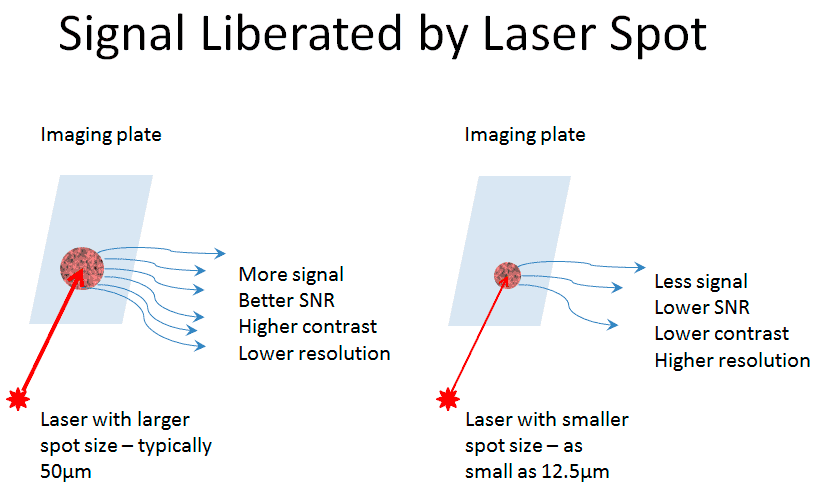
Image Credit: DÜRR NDT GmbH & Co. KG
While laser spot size directly impacts the basic spatial resolution and contrast of an image, other aspects of the system can also influence the final image quality.
High-Resolution Requirements
Scan resolution or image resolution are measures of the sample size of the scanner and the size of each pixel in the final image file. Although this impacts the quality of the final image, it is not essential to the system’s capacity to image small indications.
Basic spatial resolution (SRB) is a definitive measure of the ability of the entire imaging system to resolve fine details.
A smaller laser spot is required to attain a greater SRB and enable the imaging of smaller indications. There are systems available with small laser spot sizes that are specifically developed to facilitate the highest possible resolution.
For the highest basic spatial resolution to be achieved, the choice of the laser spot and resolution of the scanner must be correct, in addition to the imaging plate itself.
For instance, scanning with a laser spot size of 50 microns and with an image resolution of 20 microns/pixel is futile. It produces a large image file but does not offer the required level of detail due to the large laser spot size.
However, scanning with a 12.5-micron laser spot and with a 100 microns/pixel resolution is also unsuccessful, leading to a low contract image and low resolution.
If the laser spot is sufficiently small to support it, choosing a high scan resolution offers a high basic spatial resolution that may be measured as part of the system’s classification to standards, including ISO 16371-1:2011, EN 17484-1:2005, and ASTM E2446-05 (2010).
At present, only two CR scanners are available with a sufficiently small laser spot to deliver the highest basic spatial resolution.
Both scanners have been BAM-certified to provide a 30 micron/pixel basic spatial resolution and qualify for system class imaging plate 1/30 or imaging plate Special/30 by the above standards.
High Contrast Requirements
For some applications, image contrast may be the priority over pure image resolution. In these circumstances, a larger laser spot is advantageous because it gathers more data from the imaging plate by stimulating a larger area of the phosphor.
In informational radiography applications, such as the evaluation of erosion/corrosion or wall loss, shot time and efficiency, are more important than image resolution. A scanner with a larger laser spot can reduce the required dose on the imaging plate and subsequently accelerate the entire process.
Scanner Design
The laser spot size of conventional CR scanners is fixed by the system’s optical hardware design. As a result, the user must form a decision between resolution and contrast when they acquire the system, which cannot later be changed.
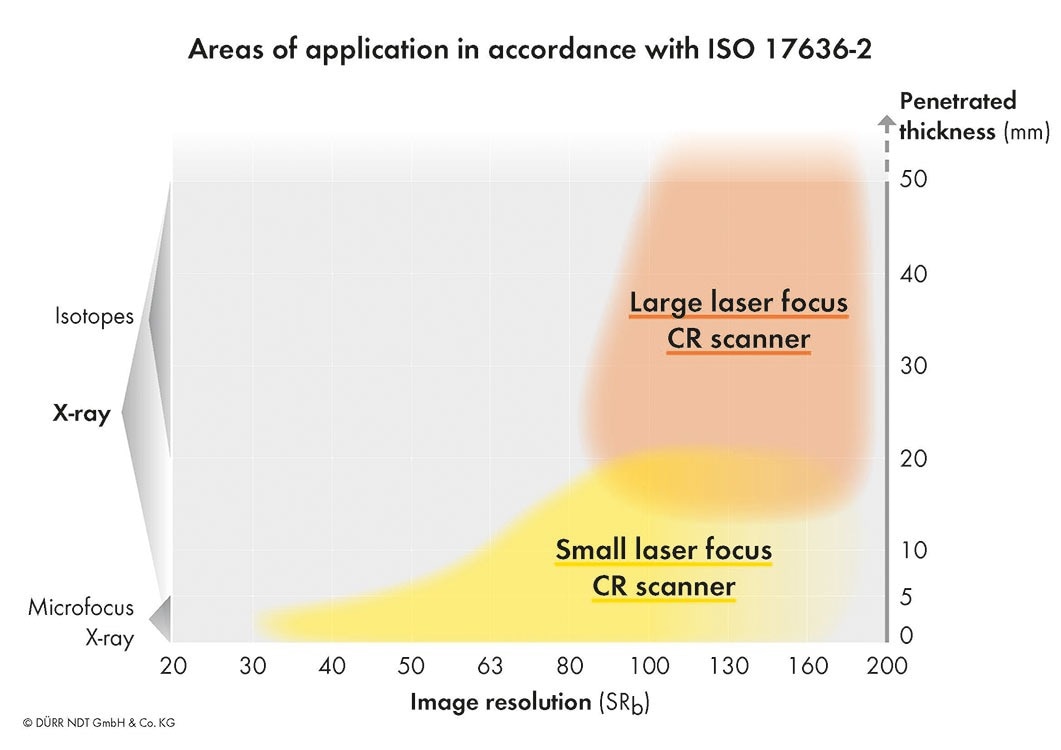
Image Credit: DÜRR NDT GmbH & Co. KG
If the user has a high-resolution system and wins an informational RT job, then the scanner system likely cannot offer the most efficient or effective results.
However, if the user only has a high-contrast system, they cannot compete for high-resolution work since the system is unable to perform to the required level.
To overcome this, most CR manufacturers produce a system that fixes the laser spot to be an intermediate size, usually 25 or 30 microns.
Although this is acceptable for many applications, it does not meet the high-resolution requirements that are typical in military or aerospace. It also cannot offer the efficiency and low-dose response that makes informational radiology tasks straightforward and profitable.
The ideal solution is to have a CR scanner with an adjustable laser spot size that can address the variety of applications that a typical user might encounter. Surprisingly, only one CR scanner manufacturer has designed such a system.
Revolutionary New CR Scanner Technology
The CR scanner that addresses the above challenges has a variable laser spot size that may be adjusted to fulfill the needs of the current application.
The scanner has three laser focus settings – 50, 25, and 12.5 microns – and addresses both high-contrast and high-resolution needs, in addition to offering a mid-range setting that can be used with many general-purpose radiography applications.
An iris diaphragm sits inside the laser tube to adjust the laser beam diameter using a simple software setting in the same manner as other scanner control parameters.
This allows the perfect laser spot to be selected for each object and application type, delivering optimum results for any radiography requirement.
This flexibility and convenience results in only one piece of hardware being required to address multiple radiography applications, decreasing the user’s investment and widening the range of jobs that a crew with a single piece of equipment can accommodate.
This can enhance the image quality and profitability, and subsequently improve the customer’s satisfaction.
The scanner can easily address the highest resolution applications when the laser spot is set to 12.5, and as mentioned above, is certified by BAM to have the highest basic spatial resolution in the industry of 30 microns.
Selecting a larger laser spot size in the software automatically alters the diaphragm and produces a 25-micron or 50-micron laser spot. This delivers the higher contrast needed for general-purpose applications or for imaging thicker specimens with isotopes.
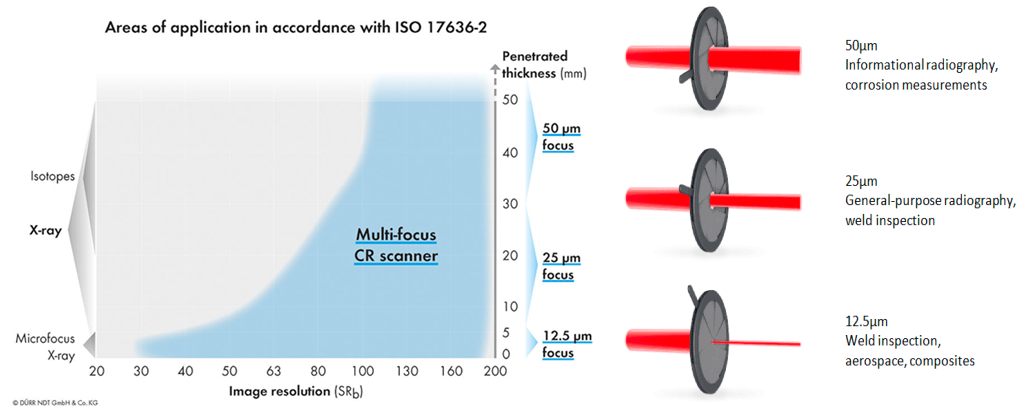
Image Credit: DÜRR NDT GmbH & Co. KG
Figure 3 displays the areas of application that are addressed by various laser spot sizes. It can be observed that an adjustable laser substantially increases the utility of the scanner.
There is a specific signal-to-noise ratio (SNR) required to test different material thicknesses to either Class A or Class B accuracy, according to the ISO 17636-2 standard.
Since the SNR differs with laser spot size and dose on the imaging plate (and subsequently exposure time), being able to adjust the laser spot enables the user to easily optimize the inspection parameters while satisfying the requirements of the standard.
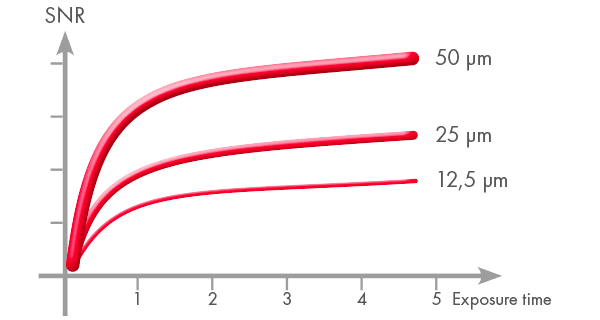
Image Credit: DÜRR NDT GmbH & Co. KG
Using a fixed laser spot size may not provide the SNR required by industry standards for every application. The CR system’s lack of flexibility may compromise the ability of the user to successfully address and win multiple jobs.
Conclusion
The continuing advancements within CR technology have led to the development of a unique system that can be optimally utilized in multiple applications.
This enables the user to closely match the performance of a scanner to industry standards and real-world needs, delivering an efficient and economical solution that is unparalleled in the CR field.
Acknowledgments
Produced from materials originally authored by Steve Jelfs from DÜRR NDT, Germany.
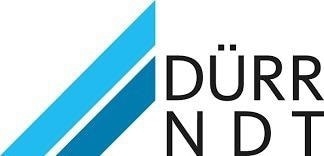
This information has been sourced, reviewed and adapted from materials provided by DÜRR NDT GmbH & Co. KG.
For more information on this source, please visit DÜRR NDT GmbH & Co. KG.