Pressure sensors are one of the most widely commercialized microdevices, engineered to detect changes in air, gas, or liquid pressure for monitoring and control purposes.
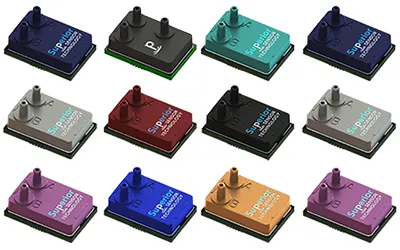
Image Credit: Superior Sensor Technology
The basic function of a pressure sensor is straightforward. It gauges the force applied by a substance across each square inch of surface area and translates this physical measurement into an electrical signal. The specific method for achieving this conversion varies based on the technology used in the device.
Despite their straightforward function, they have a broad range of applications, ensuring the reliability of air and gas supplies in life-critical scenarios, aiding in the diagnosis of pulmonary conditions, supporting aviation instrumentation, facilitating clean room research, and beyond.
Before exploring the operation of pressure sensors, it is important to clarify some terminology. Pressure sensors are frequently referred to as pressure transducers or transmitters, though these terms are not entirely interchangeable.
Despite their common use in pressure monitoring and control, each device has distinct characteristics. The key distinction lies in their output signals: transmitters generally produce a current output, whereas transducers generate a voltage output. Both types of devices can be classified as pressure sensors, which encompass the technology responsible for making the measurements.
With this distinction established, the next section of the article will examine the components involved in pressure measurement.
1. Sensing Element
The force applied by a medium is typically gauged through physical displacement. This process necessitates a sensing element that interacts with the environment being measured. Various designs are available, with the pressure-sensing diaphragm being one of the most prevalent. This component consists of a circular plate on one side exposed to the medium under measurement and the other connected to a cavity.
When pressure—whether from air, gas, or liquid—is applied, the diaphragm bends, and the degree of bending corresponds to the pressure level. The material used for the diaphragm is crucial as it influences the sensor's sensitivity, precision, and ability to withstand different conditions.
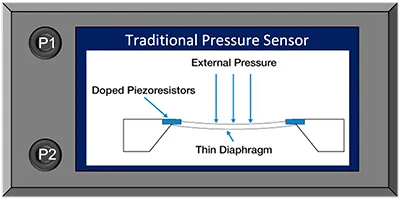
Figure 1. Pressure sensing element. Image Credit: Superior Sensor Technology
2. Conversion to Electrical Signal
The mechanical deformation of the diaphragm is translated into an electrical signal via multiple mechanisms. Different kinds of pressure sensors employ different technologies. Below are three examples:
- Piezoresistive: Piezoresistive technology involves attaching strain gauges to a diaphragm to generate an electrical signal. When the diaphragm deforms under pressure, the strain gauges experience a change in resistance. This variation in resistance can be detected and linked to the level of pressure applied.
- Capacitive: The diaphragm functions as one of two capacitor plates in capacitive sensors. As the diaphragm moves, the distance between the capacitor plates changes, altering the capacitance. This change in capacitance translates pressure into a measurable readout.
- Piezoelectric: When subjected to mechanical stress, some materials produce an electrical charge. These materials, including quartz and some ceramics, are used in piezoelectric sensors to generate a voltage that is proportionate to the pressure applied.
3. Signal Processing
Once mechanical deformation is converted into an electrical signal, it needs further processing due to its typically weak and noise-prone nature. To enhance signal clarity and reliability, the signal is amplified and filtered.
Advanced signal processing techniques are employed to ensure precise and consistent output. Even minor disturbances, such as those from external fans or motor noise, can significantly impact measurement accuracy.
Consequently, robust noise reduction features are essential, particularly in noisy industrial environments. The refined signal is then converted into a standardized output format—such as voltage, current, or digital data—facilitating integration with other systems.
High-quality pressure sensors are designed for rapid response to pressure changes, with some achieving response times as brief as one millisecond, which is vital for real-time monitoring and control.
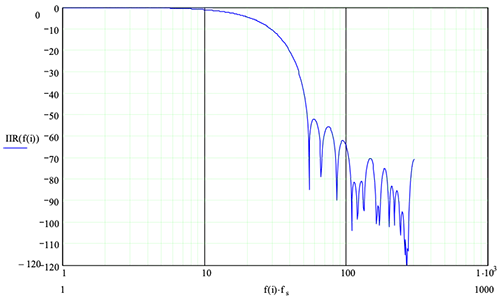
Figure 2. Signal processing example. Image Credit: Superior Sensor Technology
4. Differential Measurement
This article has covered a general method for measuring pressure that can be used for both absolute and gauge pressure measurements. These can be described as single-point methods in the sense that they all compare the signal from a sensor to an external reference.
Absolute pressure utilizes perfect vacuum pressure as a reference, whereas gauge pressure uses atmospheric pressure. In contrast, differential measurement compares the pressure difference between two points in a system.
This ability is critical for applications where relative pressure measurement yields more information than absolute pressure, like monitoring cabin pressure in aircraft by comparing it to external atmospheric pressure. Other applications for differential pressure sensors include:
- Smart Homes: In smart homes, pressure sensors optimize HVAC systems, detect occupancy, and enhance security systems.
- Medical Devices: Pressure sensors monitor airflow and air pressure in devices like sleep apnea machines to regulate treatment.
- Wind Turbines: Pressure sensors monitor wind speed and structural health, helping optimize energy output and ensuring the safe operation of the turbines.
Closing Thoughts
Due to their accuracy and adaptability, pressure sensors are essential components in many contemporary technologies. Pressure sensors are used in a wide range of applications, from ensuring the comfort and safety of aircraft passengers to optimizing energy production in wind turbines.
Their ability to translate physical pressure into precise electrical signals makes a wide range of applications that improve efficiency, safety, and functionality across multiple industries possible.
Superior Sensor Technology prides itself on the knowledge it has to create cutting-edge pressure sensors for a diverse range of industries. The company’s commitment to innovation ensures the unparalleled accuracy, reliability, and performance of its sensors.
Whether you are involved in critical aerospace, healthcare, renewable energy, or smart home technology applications, Superior Sensor offers solutions designed to meet the highest standards of precision and durability.
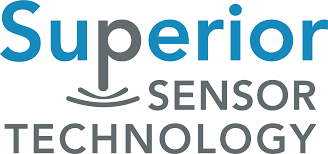
This information has been sourced, reviewed and adapted from materials provided by Superior Sensor Technology.
For more information on this source, please visit Superior Sensor Technology.