The challenge of high costs and product yield has garnered significant attention from semiconductor manufacturers.
Various factors influence product yield, with contamination being one of the most critical. Industry experts estimate that contamination accounts for approximately 50% of production loss. Impurities present in specialty semiconductor process gases can adversely affect the yield and performance of final electronic devices.
Consequently, the semiconductor industry necessitates continuous monitoring of bulk nitrogen, argon, hydrogen, oxygen, helium, and carbon dioxide to identify undesirable contaminants, particularly oxygen and moisture, before they compromise wafer quality.
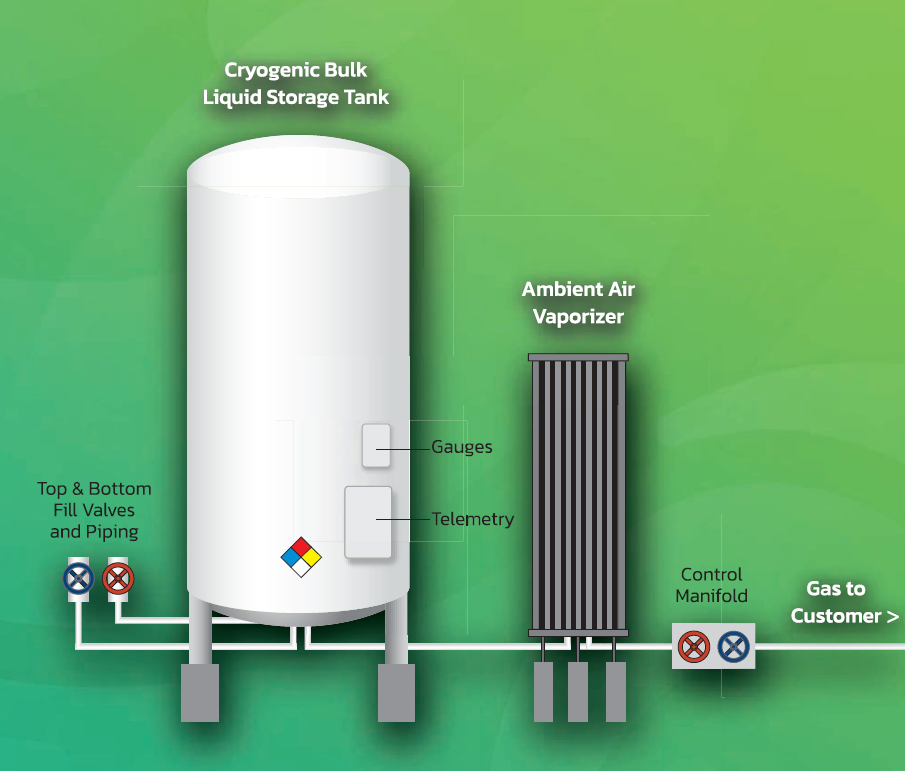
Image Credit: ASTG
The Solution
ASTG offers a comprehensive range of fixed gas analytical systems. These systems can be utilized for spot-checking manufacturing issues as well as for "battery-limit" testing of entire facilities.
ASTG’s systems are engineered using ultra-high purity engineering techniques, which are innovated by ASTG scientists and engineers to meet the complex requirements of customers.
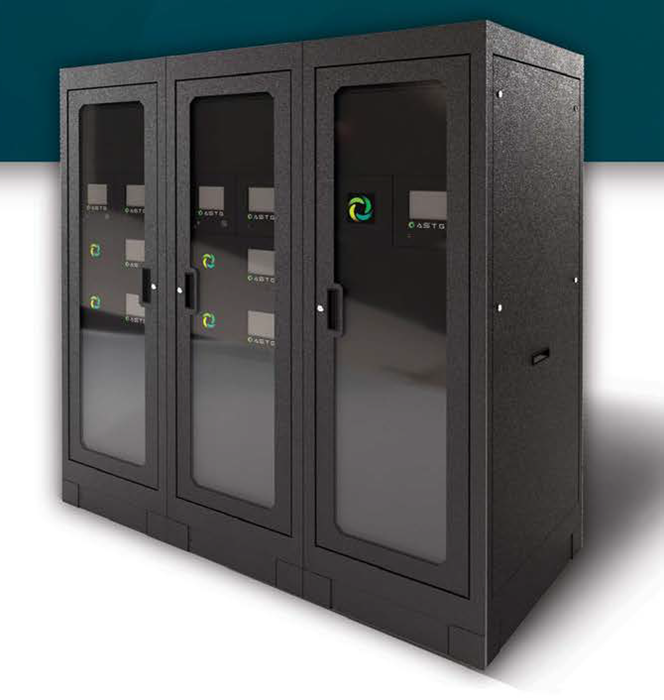
Image Credit: ASTG
Portable Task Specific Carts Systems — for Verification & Validation
Key Features
- Moisture + Oxygen
- On-Board support gas systems
- PLC Control with HMI Features
- N2, Ar, O2, He, H2, CO2, and Spec Gases
Advantages
- Low volume, zero dead-leg sample system
- Electro-polished and orbitally welded
- Class 1 Division 1 and 2 are available
- Onboard control and data acquisition
- Onboard life and hazard safety systems
- Easy start-up and maintenance
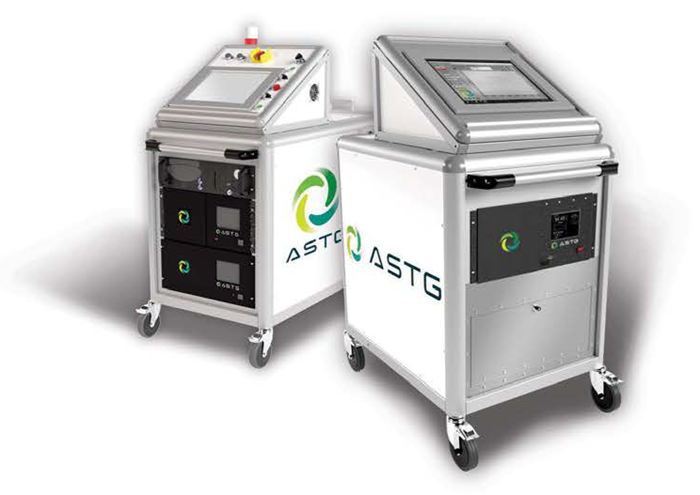
Image Credit: ASTG
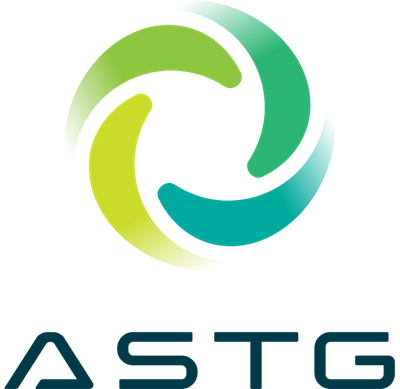
This information has been sourced, reviewed and adapted from materials provided by ASTG.
For more information on this source, please visit ASTG.