Introduction
Alumina, among advanced structural ceramics, has excellent properties such as high melting temperature, high wear resistance, and chemical stability. However, it has lower values of flexural strength and fracture toughness than other structural ceramics such as silicon nitride and silicon carbide. Research on the improvement of mechanical properties such as fracture toughness or strength has progressed. The approach has been to try to control microstructure such as grain size and grain boundary phase [1, 2], or to add secondary phases (for example, spherical particles, platelets, fibres or whiskers) [3, 4]. Especially, it has been reported that nanosized silicon carbide particle-reinforced alumina composites improved mechanical properties such as flexural strength (350 - 1050 MPa) and fracture toughness (3.5 - 4.7 MPa.m1/2) compared to monolithic alumina [5-6]. The characterization of many kinds of ceramic nanocomposites such as Al2O3/SiC, Si3N4/SiC and MgO/SiC [5, 7] has been investigated. However, a few investigations on the tribological properties of nanocomposites have been performed [8, 9].
Many researchers reported that wear rates of alumina were associated to grain size [10-12]. Two different wear mechanisms in alumina were suggested. One is brittle fracture (for example, grain pull-out and microchipping). Another is plastic deformation.
Cho et al. [11] suggested that smaller grain sizes provided higher wear resistance, because of the transition time from mild wear and severe wear increases with decreasing grain size. Xiong et al. [12] reported that wear of alumina decreases with increasing grain size. Contact geometry differences resulted from the variations in real contact pressure. Therefore, the generation of fine wear debris was affected by difference in real contact area. In the case of coarse-grained alumina, fine wear debris was not generated, and the worn surface of alumina displayed intergranular cracking. However, for fine-grained alumina, fine wear debris on the worn surfaces was observed. Also, the worn surface showed transgranular cracking. Because of the generation of fine wear debris, the entrapped wear debris increases the real contact area between the pin and the disk, which increases the wear rate.
In this study, alumina with 5 vol% of nanosized silicon carbide was sintered by a hot pressing method at 30 MPa for 1 h in an argon gas atmosphere. Hot pressing temperature was varied from 1500ºC to 1800ºC. Tribological properties versus hot pressing temperature were investigated. The wear mechanism of alumina-silicon carbide nanocomposites can be explained by observing the worn surface by scanning electron microscopy and transmission electron microscopy.
Experimental Procedures
A high purity alumina (α-Al2O3, AKP-53, 100-300 nm, Sumitomo Chemical Ltd., Japan) powder and nanosized silicon carbide (β-SiC, UF0754, 70 nm, Ibiden Co., Japan) powders were used in this study. Nanosized silicon carbide of 5 vol% was mixed with alumina in ethanol using alumina balls, and ball-milled in a plastic pot for 24 h. The slurry was dried using a rotary evaporator. Dried mixed powders were ball-milled in a pot for 12 h. The powder mixtures were compacted in a graphite mold coated with BN, and hot pressing was carried out at 30 MPa for 1 h in an argon gas atmosphere. Hot pressing temperature was varied from 1500ºC to 1800ºC.
Friction and wear tests were performed using a Plint Tribometer (TE77, Plint & Partners Ltd., U.K.) on a reciprocating ball-on-plate tester.
Before each wear and friction test, the surface of specimen was polished using a 0.5 μm diamond suspension. The ball used for friction and wear test was a commercial silicon nitride bearing ball (NBD200, 12.7 mm in diameter, CERBEC, Saint-Gobain Advanced Ceramics, U.S.A.). The testing conditions were in air, at 10 N, 0.068 m/sec, for 60 min of sliding time, and at room temperature. After completing each wear test, wear volume was measured using a profilometer (Form Talysurf Plus, Rank Talyor Hobson Co., U.K.). The profilometer was utilized to measure 4 points of wear track perpendicularly to sliding direction, and a planimeter was used to calculate wear area. Wear tests were repeated at least five times. A scanning electron microscope (SEM, JEOL-6400, JEOL, Japan) and a transmission electron microscope (TEM, H-8100T, Hitachi, Japan) were employed to examine the worn area on the surface of alumina and alumina-5 vol% silicon carbide nanocomposites.
Results and Discussions
Table 1 shows mechanical properties of alumina and alumina-5 vol% silicon carbide nanocomposites. As sintering temperature of alumina-5 vol% silicon carbide nanocomposites was increased, relative density was close to the theoretical density, and grain size of nanocomposites was increased as shown in Figure 1. Hardness and flexural strength decreased because of increasing grain size with increased sintering temperature. Hardness of nanocomposites sintered from 1500˚C to 1800˚C decreased from 19.4 GPa to 17.5 GPa. Also, fracture strength decreased from 943 MPa to 670 MPa. As sintering temperatures increased, fracture toughness of nanocomposites decreased in spite of increasing grain size, as shown in Figure 1. Fracture toughness of nanocomposite sintered at 1600˚C and 1800˚C were 3.9 MPa.m1/2 and 2.5 MPa.m1/2, respectively. The fracture mode of nanocomposites was of the transgranular type as shown in Figure 2. For coarse-grained nanocomposites, the fracture mode was still transgranular because crack propagation by crack deflection and crack bridging did not occur.
Table 1. Test samples and their mechanical properties.
Alumina
|
1600
|
99.8
|
15.6
|
4.0
|
405
|
Nano-composite (5 vol% SiC)
|
1500
|
98.4
|
19.4
|
2.9
|
943
|
1600
|
99.7
|
20.3
|
3.9
|
1052
|
1700
|
99.8
|
18.2
|
2.9
|
690
|
1800
|
100.0
|
17.5
|
2.5
|
670
|
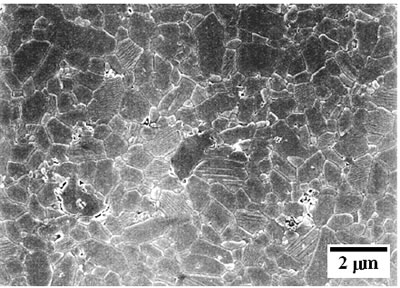
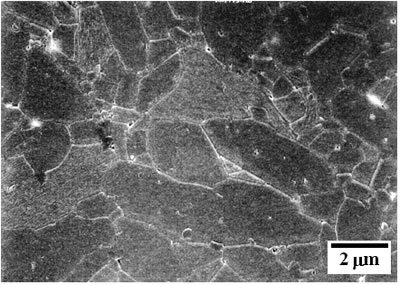
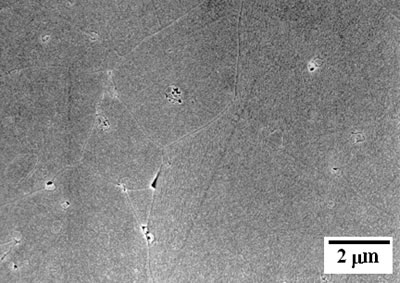
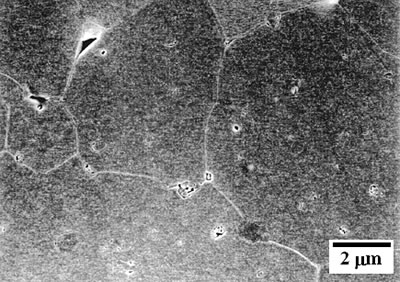
|
Figure 1. SEM micrographs of the etched surface of alumina – 5 vol% silicon carbide nanocomposites as function of the sintering temperature at 30 MPa for 1 h in Ar atmosphere; (a) 1500oC, (b) 1600oC, (c) 1700oC, and (d) 1800oC.
|
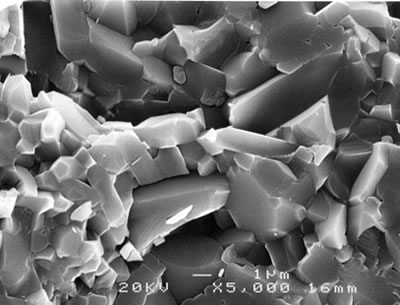
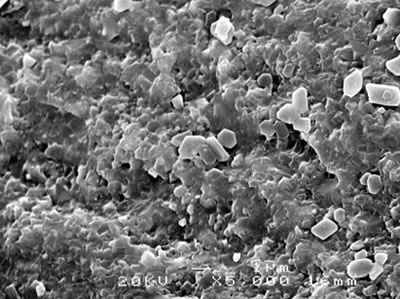
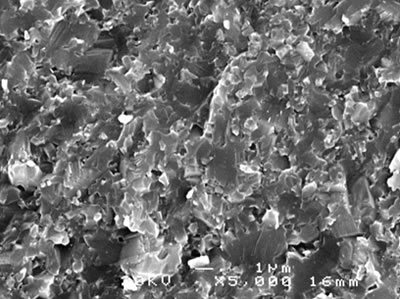
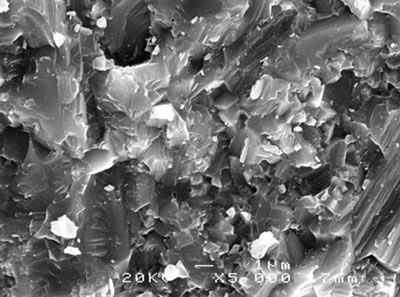
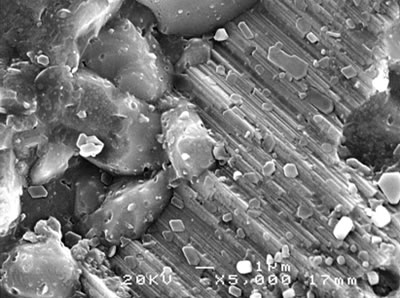
|
|
Figure 2. SEM micrographs of the fracture surface of monolithic alumina (a) and alumina - 5 vol% silicon carbide nanocomposites (b-e) sintered at various temperatures; (a) monolithic alumina (1600oC), (b) 1500oC, (c) 1600oC, (d) 1700oC and (e) 1800oC.
|
|
|
|
|
|
|
|
|
Figure 3 shows the wear volume of monolithic alumina and of alumina-5 vol% silicon carbide nanocomposite at various sintering temperatures tested in air. As the sintering temperature of alumina-5 vol% silicon carbide nanocomposite increased, the grain size of the nanocomposites increased, and wear volumes decreased with increasing grain size. Also, wear behavior of alumina-5 vol% silicon carbide nanocomposite was associated closely to physical properties such as hardness, fracture toughness and fracture strength, but it has no close connection with the variation of density for full density specimens above 98% of relative density. It is more dependent on grain size than on relative density. However, high wear volume of monolithic alumina was considered to cause fracture mode of intergranular type. In the case of intergranular fracture, wear particles were generated due to grain chipping or pull-out along the grain boundary. As shown in Figure 4(a), wear behavior of monolithic alumina shows some micron-sized chipping due to intergranular fracture along grain boundaries. However, the wear behavior of nanocomposites shows microchipping and microcracks due to transgranular fracture. Also, the wear volume of nanocomposites was lower than that of monolithic alumina. The wear morphology of nanocomposites as shown in Figure 4(b-e) reveals the typical abrasive wear with shallow scratches compared to alumina. As the sintering temperature of the nanocomposites was increased, the abrasive grooves on the worn surface were observed to be wider and deeper in the nanocomposites. Also, the wear behavior of alumina and nanocomposites showed microchipping and abrasive grooves. The wear of alumina occurred by brittle fracture and subsurface damage. The shear stress generated a microcrack at the grain boundary and the crack propagated through several alumina grain boundaries. Finally, when the crack reached the surface wear debris from several grains was removed. Therefore, the smaller grain size provided the higher wear resistance, because coarse-grained specimens generated larger wear debris fragments.
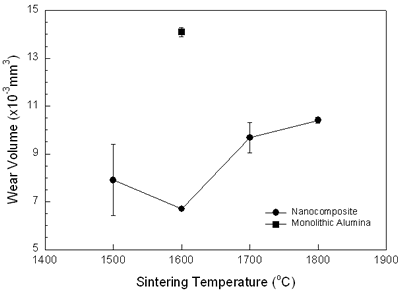
|
Figure 3. Variations of wear volume with the sintering temperature.
|
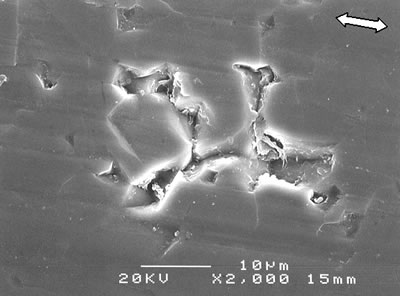
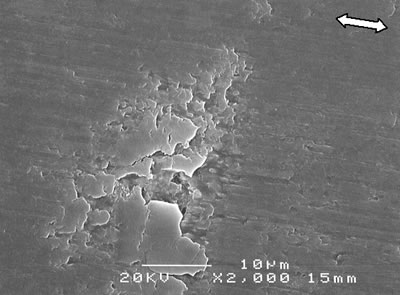
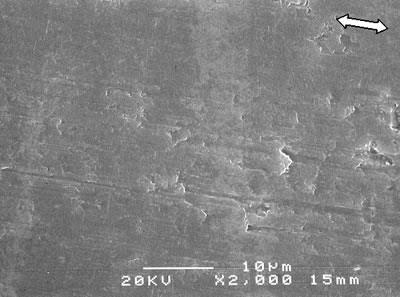
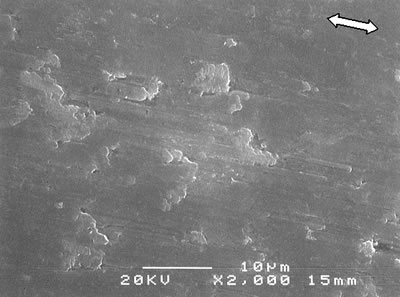
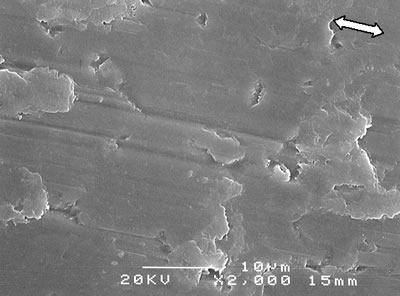
|
Figure 4. SEM micrographs of the worn surface of monolithic alumina (a) and alumina - 5 vol% silicon carbide nanocomposites (b-e) sintered at various temperatures; (a) monolithic alumina (1600oC) and (b) 1500oC, (c) 1600oC, (d) 1700oC and (e) 1800oC (←→ : the sliding direction).
|
Figure 5 shows transmission electron micrographs of worn surfaces of monolithic alumina and alumina-5 vol% silicon carbide nanocomposite. Dislocations generated during sliding are observed on the worn surface of both materials along the sliding direction. Monolithic alumina showed higher density of dislocations than the alumina-5 vol% silicon carbide nanocomposite, as shown in Figure 5. Dislocations accumulated along the grain boundaries. As shown in Figure 5(a), dislocations in monolithic alumina existed inside the grains, and grain boundaries impeded the movement of dislocations. In the case of nanocomposite (Figure 5(b)), dispersed silicon carbide within the alumina grains prevented the movement of dislocations. Improvement of wear resistance of the nanocomposites is associated with pinning of dislocations by the nanosized silicon carbide particles. Moreover, the microcracks that were generated during the sliding, run through inside the alumina grains as shown in Figure 5(b). Niihara and Sasaki, et al. [13, 14] reported that transgranular fracture of alumina grains has been well known in nanocomposites. Significant microcracks and plastic deformation on the worn surface of ceramic materials were commonly observed. Further, microcracking is observed in both alumina and alumina-silicon carbide nanocomposites, and the formation of dislocations due to plastic deformation can be observed on the wear tracks.
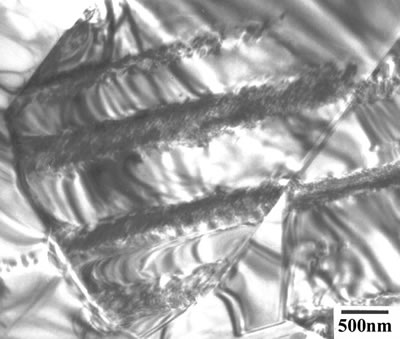
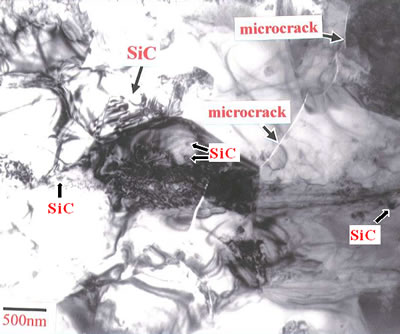
|
Figure 5. TEM micrographs of the worn surface of (a) monolithic alumina and (b) alumina - 5 vol% silicon carbide nanocomposite.
|
Conclusions
As sintering temperature increased, grain size of nanocomposites was increased. Therefore, hardness and flexural strength decreased because grain size increased. Also the wear volume of the nanocomposites increased.
For coarse grain size specimens of alumina-5 vol% silicon carbide nanocomposite, fracture of the transgranular type was not affected by the large grain size because crack deflection and crack bridging did not occur. In the case of monolithic alumina, chipping occurs along the grain boundary. Also, there is accumulation of dislocations inside single grains along the sliding direction. However, alumina-5 vol% silicon carbide nanocomposite shows abrasive wear as scratches and show interference of dislocations by silicon carbide particles in the alumina matrix grains. Also, the alumina-silicon carbide nanocomposites show more wear resistance due to the microcrack pinning by the nanosized silicon carbide particles. However, in the case of alumina-5 vol% silicon carbide nanocomposites, the effect of microcrack pinning was reduced due to the coarsening of the alumina matrix. Therefore, as sintering temperature increased, wear volume of nanocomposites also increased.
References
1. P. Stanley, “Probabilistic Basis for Designing with Ceramics”, Brit. Ceram. Proc., 49 (1993) 167-173.
2. J. D. Birchall and D. R. Stanely, “Advanced Structural Ceramics-Critical Needs”, Brit. Ceram. Proc., 49 (1993) 127-164.
3. X. Yang and M. N. Rahaman, “SiC Platelet Reinforced Al2O3 Composites by Free Sintering of Coated Powders”, Brit. Ceram. Proc., 50 (1994) 702-709.
4. C.L. Hu and M. N. Rahaman, “SiC-Whisker-Reinforced Al2O3 Composites by Free Sintering of Coated Powders”, J. Am. Ceram. Soc., 76 [10] (1990) 2549-2954.
5. K. Niihara, “New Design Concept of Structural Ceramics - Ceramic Nanocomposites”, J. Ceram. Soc. Jpn., 99 [10] (1991) 974-982.
6. J. Zhao, L. C. Stearns, M. P. Harmer, H.M. Chan and G. A. Miller, “Mechanical Behavior of Alumina-Silicon Carbide Nanocomposites”, J. Am. Ceram. Soc., 76 [2] (1993) 503-510.
7. M. Sternitzke, “Review: Structural Ceramic Nanocomposites”, J. Eur. Ceram. Soc., 17 (1997) 1061-1082.
8. R. W. Davidge, P. C. Twigg and F. L. Riley, “Effects of Silicon Carbide Nanophase on the Wet of Alumina,” J. Eur. Ceram. Soc., 17 (1996) 799-802.
9. J. Rodríguez, A. Martín, J. Y. Pastor, J. L. Lorca, J. F. Bartolomé and J. S. Moya, “Sliding Wear of Nanocomposites,” J. Am. Ceram. Soc., 82 [4] (1999) 2252-2254.
10. R. W. Davidge and F. L. Riley, “Grain-Size Dependence of the Wear of Alumina”, Wear, 186-187 (1995) 45-49.
11. S.J. Cho, B. J. Hockey, B. R. Lawn and S. J. Bennison, “Grain-Size and R-Curve Effects in the Abrasive Wear of Alumina”, J. Am. Ceram. Soc., 72 [7] (1989) 1249-52.
12. F. Xiong, R. R. Manory, L. Ward, M. Terheci and S. Lathabai, “Effect of Grain size and Test Configuration on the Wear Behavior of Alumina”, J. Am. Ceram. Soc., 80 [5] (1997) 1310-1312 .
13. K. Niihara, K. Izaki and T. Kawakami, “The Silicon Nitride-Silicon Carbide Nanocomposites with High Strength at Elevated Temperatures”, J. Mater. Sci. Lett., 10 (1990) 112-114.
14. G. Sasaki, H. Nakase, K. Suganuma, T. Fusita and K. Niihara, “Mechanical Properties and Microstructure of Si3N4 Matrix Composite with Nano-meter Scale SiC Particles”, J. Ceram. Soc. Jpn., 100 [4] (1992) 536-540.
Contact Details
|