Atomic emission spectroscopy (AES) using a rotating disc electrode (RDE) has been a successful technique applied to condition monitoring (oil analysis) programs for decades. However, in recent years the AES technique has become less effective as an early detection diagnostic technique. The reasons for the reduction in the effectiveness of the AES technique are primarily due to fine filtration and the morphology of particles that are generated at the onset of some types of failures in complex mechanical systems.
Rotrode Filter Spectroscopy (RFS)
Rotrode Filter Spectroscopy (RFS) is an analytical technique that has been developed to enhance the sensitivity of the RDE/AES technique in order to overcome these limitations.
Features of Automated Rotrode Filter Spectroscopy (A-RFS)
Automated rotrode filter spectroscopy (A-RFS) is a sample preparation device designed for the AES that concentrates large and small wear metal debris in a graphite filter electrode. When the graphite filter electrode is analyzed using AES, sensitivity is increased by a factor of 80-100 and particle size detection is improved by a factor of 10.
Increasing Limit of Detection in RDE/AES Analysis Technique
For example, the limit of detection of iron for conventional RDE/AES is 600 parts per billion. This limit of detection is reduced to 6 parts per billion by applying the A-RFS sample preparation technique. When the sample is prepared by the A-RFS device the particle size detection capability of AES is extended from 8-10 micrometers to greater than 70 micrometers. By concentrating 5 ml of oil sample (fifty times the volume analyzed by conventional RDE/AES analysis), all particle debris (metallic and non-metallic) becomes trapped within the outer circumference of the graphite filter electrode. This process eliminates the major limitations (gravity, oil, resonance time) of conventional RDE/AES analysis.
Efficient vaporization of all particles (large and small) is achieved using the total energy produced by the excitation source to reach vaporization temperatures in excess of 5,600 degrees Celsius. This is particularly important when alloy identification (such as M50) is necessary and damaging contaminants, such as silicon containing particles are present.
Advantages of Rotrode Filter (RF) Analysis in Aerospace Applications
When applied to helicopter engines, transmissions and gearboxes, rotrode filter (RF) analysis can enhance the effectiveness of AES to detect the harmful effects of lubricant contamination and component damage. The A-RFS is shown in operation next to the atomic emission spectrometer in Figure 1.
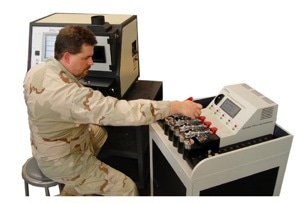
Figure 1. A-RFS Device in Operation
Case Study - RFS Analysis in The United States Army Oil Analysis Program (AOAP)
The United States Army Oil Analysis Program (AOAP) has successfully used the AES technique as their primary condition monitoring technique for several decades. To fully understand the capability of rotrode filter spectroscopy, the AOAP initiated a pilot program to apply RFS analysis to helicopter engines, transmissions, and gearboxes.
This case history will provide one example of how the RFS technique enhanced the AES capability to identify a failure that was not apparent using conventional RDE/AES or particle counting. For security reasons, the name and location of the Army base, plus the helicopter and component serial numbers have been withheld.
Enhancing AES Instrumentation
The location of the A-RFS field evaluation program was chosen by the AOAP based on the availability of rotary aircraft and a fully staffed laboratory with complete analytical capabilities. The site chosen for the RFS field evaluation has an enhanced AES instrument that includes the element vanadium and the A-RFS sample preparation device.
The element vanadium is essential in the detection of M50 and M50 NiL bearing alloys. In addition to RDE/AES and RF/AES capability for wear metal, contaminant and additive analysis, the AOAP laboratories have a LaserNet FinesÆ particle counter and shape classifier, ferrography to separate ferrous wear debris by particle size for shape analysis, a viscometer, titrators and FT-IR spectrometer to measure the physical properties of the lubricant and water in oil. These instruments provide a comprehensive evaluation of the mechanical integrity of the component as well as the serviceability of the lubricant.
Results from Conventional Rotating Disc Atomic Emission Spectroscopy (RD/AES) Analysis
From the RDE/AES data ( the analysis of the subject component based on conventional rotating disc atomic emission spectroscopy (RD/AES)) , it is apparent iron was increasing from an initial concentration of 11 ppm to a concentration of 30 ppm for sample number 0177A. After a review of sample 0177A, an oil drain and flush were recommended. Continued review of the main transmission after the drain and flush recommendation indicated an accelerating concentration of the element iron only. The concentration of iron, however, remained within the NORMAL guideline of < 81 ppm and the trend never exceeded the limit of > 24 ppm in 10 hours of operation. In accordance with RDE/AES analysis alone, the main transmission of this helicopter was operating within technical order guidelines.
ISO Classification for Particle Count Analysis
Interpreting the LaserNet FinesÆ particle count data, it produced an ambiguous assessment of the condition of this component. The particle count was elevated and contained particles in excess of the filtration rating, but did not exceed ISO classification to warrant component removal. A significant reduction in NAS and ISO classifications can be observed after the drain and flush maintenance recommendation based on the analysis of sample 0177A. Continued particle count analysis of this component never exceeded the ISO classification code necessary to support removal from service. Due to the labor intensive nature of ferrography, the production and analysis of a ferrogram would not normally be ordered by the data analyst without some evidence of an abnormal condition from at least one of the primary analytical instruments.
Conditions for Performing Ferrogram Analysis
The laboratory recommendation to perform a ferrogram is generally based on an abnormal indication from one or more other analytical instruments or visual debris suspended in the sample bottle. In this case history, both the RDE/AES and LaserNet FinesÆ produced results that were interesting, but not outside of normal operating guidelines. Fortunately, this helicopter was located within the geographical area covered by the AOAP laboratory where rotrode filter spectroscopy was being field tested.
Results from Rotrode Filter Spectroscopic Atomic Emission Spectroscopy (RF/AES) Analysis
This section of the case history contains the rotrode filter spectroscopic analysis of the same helicopter main transmission. Figure 4 below is the RFS component history record and consists of a single page record because all other analytical data is stored on the RD/AES component history record.
The Effect of Iron, Silver, Aluminum, Copper and Magnesium on Rate of Wear
Comparing the RF/AES data to the RDE/AES data, it reveals the true magnitude and rate of the wear being generated within this component. Iron, which is the dominant wear metal element in most oil wetted components, was producing elevated concentrations almost from the beginning of this history record. This element continued to increase rapidly above the baseline especially after the drain and flush recommendation is given for sample 0R177. As the malfunction progressed, producing higher concentrations of wear particles, the lower percentage alloying elements such as chromium and nickel appeared and increased with the severity of wear. Elements such as silver, aluminum, copper and magnesium appeared and increased as the assembly experienced additional stresses.
RD/AES and RF/AES Measurement - A Comparison
The difference in the wear metal concentration between the RD/AES measurement and RF/AES measurement is due to three factors. RF/AES analyzes a larger sample volume which increases its sensitivity. It eliminates the negative effect gravity has on transporting large particles to the excitation source and it produces higher excitation temperatures for greater particle size vaporization efficiency. Therefore, the RF/AES is significantly more capable of detecting the development of an abnormal mechanical condition
Applying Ferrogram in RF/AES Analysis
As a result of the wear metal concentration and rate of increase in several of the wear metal elements that appeared in the RF/AES analysis, the laboratory ordered that a ferrogram be prepared and analyzed.
A ferrogram is made by diluting an oil sample to reduce its viscosity. The sample then flows from one end of a special microscope slide to the opposite end while being subjected to a powerful magnetic field. The larger wear particles become trapped quickly whereas the smaller particles, with less mass, travel further along the slide before they are trapped by the magnetic field. As a result, the ferrous debris becomes separated by particle size thus allowing microscopic inspection to be performed. Figures 2 and 3 are ferrogram screen images of the wear metal debris from sample number 0534A.
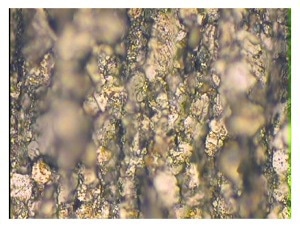
Figure 2. Ferrogram Slide #1
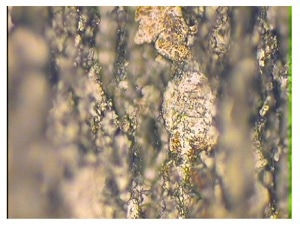
Figure 3. Ferrogram Slide #2
Reference Serviceability Labelling
As a result of a thorough multiple analytical assay of sample 0345A, the laboratory submitted the following maintenance recommendation: Excessive Rubbing Wear Excessive Cutting Wear Excessive Sliding Wear Exceeds NAS1638 Limits Excessive Spalling Fatigue Wear DO NOT FLY Reference serviceability check from component manual and submit completed 3254-R with resample.
Effect of Magnetic Chip Detectors in Wear Analysis
Maintenance action was performed on this component in accordance with the laboratory recommendation. Post maintenance feedback assessed the condition as follows. Both magnetic chip detectors in the main transmission of this helicopter were defective and did not indicate imminent failure of the component. In addition, the warning lights never illuminated to show that the chip detectors had failed.
This combination of diagnostic monitoring failures placed the main transmission in an unmonitored condition whereby component degradation and catastrophic failure were undetectable. The main transmission was removed from service and sent to depot maintenance for teardown inspection and overhaul. Post teardown and inspection records from the overhaul maintenance depot are on request. Figures 4 and 5 are photographs of the magnetic chip detectors removed from the defective main transmission illustrating the severity of wear debris generated by this malfunction.
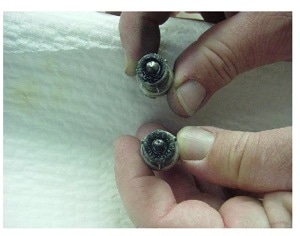
Figure 4. Defective Magnetic Chip Detectors (MCD)
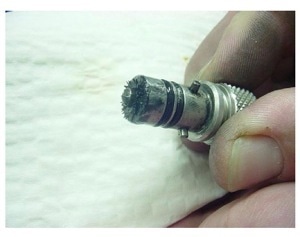
Figure 5. MCD with Wear Metal Debris
Summary
The A-RFS is an accessory for existing atomic emission spectrometers which aids in efficiently vaporizing all wear metals and contaminants in an oil sample from any helicopter engine, transmission or gearbox. Concentrating all debris contained in this sample is equivalent to analyzing 50 times the sample volume analyzed by conventional RDE/AES.
The benefit gained by concentrating the debris is significant. It provides better statistical representation of the total lubricant contamination in the engine and it elevates fine filtered debris to a concentration that is detectable. Direct deposition of all debris in the pores of the graphite filter electrode results in more efficient sample introduction into the excitation source. Removal of the lubricant in the A-RFS process results in higher excitation energy for vaporization of larger particles and higher temperatures necessary to vaporize alloy elements such as vanadium and contamination in the form of silicon particles.
This case history provides evidence that the application of RFS in routine oil analysis of helicopter platforms enhances the capability of conventional atomic emission spectrometers. The enhanced sensitivity and higher vaporization temperatures can result in early detection of component failure and when used in conjunction with complimentary analytical instrumentation can enhance the effectiveness of a condition monitoring program. The A-RFS sample preparation accessory for AES instruments is an improvement to any condition monitoring oil analysis program.
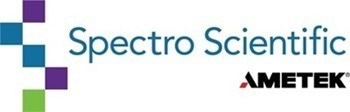
This information has been sourced, reviewed and adapted from materials provided by AMETEK Spectro Scientific.
For more information on this source, please visit AMETEK Spectro Scientific.