Arthritis is a chronic degenerative disease which will affect most people at some point during their lifetime. It results from inflammation of the joints and can come in over 100 different forms. Osteoarthritis is the most common form of arthritis in the UK with an estimated 8.5 million people suffering from the condition1. It can affect all joints within the body; and often affects the fingers, toes, knees, hips, and shoulders. Joint replacement surgery is a well-established technique used to help alleviate this condition.
The first total hip replacement surgery was performed over 40 years ago and now benefits millions of people every year. Technological advancements in materials, design and techniques have made it one of the most predictable and reliable medical procedures available. Not surprisingly, leading manufacturers of orthopaedic implants have well-equipped research and development laboratories to ensure the safety and function of these devices. This article looks at how a materials testing machine is used to make some of these critical measurements.
Case Study - Biomet Inc.
Biomet Inc. is a global leader in the orthopaedics market, specialising in the design and manufacture of implants which replace primarily; hips, knees, shoulders, and elbows, as well as manufacturing biomaterials, bone cements and accessories and orthopaedic surgical instruments. With a tradition of exceptional engineering and development skills, Biomet works in partnership with medical professionals to develop pioneering designs. The company has a history of technological advances and first class products and services, which are combined with education and training programmes to support clinical excellence, improve medical results, increase patient satisfaction and reduce costs. Since orthopaedic implants need to be able to withstand high cyclic stresses over their long lifetimes, rigorous evaluation of their mechanical properties is an essential part not only of the research and development process but also for the QA process during manufacture. Biomet’s European research laboratory in Swindon, UK is equipped with an EZ50 50kN materials testing instrument, manufactured by Lloyd Instruments.
Materials Testing
Materials testing is a well-established technique used to determine the physical and mechanical properties of raw materials and components from a human hair to steel, composite materials and plastics. Table 1 shows typical parameters that can be measured using the technique.
Table 1. Physical and mechanical properties that can be measured using universal testing machine.
Tensile Strength |
Bond Strength |
Elastic Limit |
Compression |
Adhesion Strength |
Elongation |
Flexure/Bend Strength |
Break Load |
Rupture Strength |
Coefficient of Friction |
Creep and Stress Relaxation |
Young’s Modulus |
Puncture Strength |
Crush Resistance |
Toughness |
Delamination Strength |
Deformation Strength |
Peel Strength |
Tear Resistance |
Ductility |
Tear Strength |
The EZ50 universal testing machine (Figure 1) used by Biomet is microprocessor controlled, incorporating proven 32-bit technology for highly accurate load measurement and rapid data acquisition. It is designed for testing applications up to 50 kN (11241 lbf) and can be used for routine quality control testing or for performing complex multi-stage tests; Biomet uses their test machine for both these functions. The machine uses high accuracy interchangeable XLC Series load cells for tension, compression and cycling through zero force measurements. Its high stiffness frame incorporates a crosshead guidance system to prevent side loading of the test sample. A selection of sample grips and fixtures allows it to be used for a wide range of different testing applications. The instrument operates under PC control, using Lloyd Instruments’ NEXYGEN MT materials test and data analysis software package. The software provides a library of common pre-configured test set-ups complying with international testing standards as well as allowing user-configured tests. NEXYGEN MT software provides advanced security and audit trail capabilities, video capture and playback, as well as seamless integration with common Microsoft® Office products etc. The software can also be used with the Batch Tester to create a semi-automatic or fully automatic testing system, which is particularly useful for Biomet’s QA applications.
.jpg)
Figure 1. The EZ50 universal testing machine from lloyd Instruments.
Hip Implant Testing
Total hip replacement is an operation designed to replace a hip joint that has been damaged by arthritis. The natural hip joint is a ball and socket joint. The ball is formed by the head of the femur (thigh bone) and fits snugly into the socket (acetabulum). In a total hip replacement operation, the surgeon replaces the worn head of the thigh bone with a metal or ceramic ball mounted on a stem, while the socket is resurfaced. The material used to resurface the socket can be polyethylene (plastic), ceramic, metal; and various different cup designs exist. The prosthesis may be cemented in place with a filler or grout which is called bone cement, or securely pressed into place without using cement.
One cup design involves a polyethylene liner which clips into a metal cup; one of the key parameters for the device is how strongly the liner is clipped into the cup. This has been carefully measured by Biomet using the EZ50 testing machine to ensure that the liners will not become loose. The test performed involved placing the acetabular cup shells onto a ring to support the circumference of the shell during testing. The ring was placed on a bed of bearings, mounted on the base plate of the instrument, to allow lateral movement of the shell. A 10 mm diameter disc was placed inside the apex hole of the shell to allow force to be applied to the liner (Figure 2). The instrument was set up to measure the force required to push the liner out of the shell using a rate of 5.0 mm min-1; this then allowed a variety of different designs and sizes to be compared and optimised.
.jpg)
Figure 2. Set up for evaluating an acetabular cup/hip implant.
Knee Implant Testing
Knee replacements are less common than hip replacements, with around 70,000 being performed in England and Wales in 20072. The knee joint is one of the largest and most complex joints in the body. The knee is made up of the lower end of the thigh bone (femur) which rotates on the upper end of the shin bone (tibia) and the kneecap (patella), which slides in a groove on the end of the femur. Large ligaments attached to the femur and the tibia provide stability. The long thigh muscles give the knee strength.
There are two types of knee replacement operations; total knee and partial knee replacement. Total knee arthroplasty is performed on patients who have severe damage to the knee and involves replacement of the majority of the knee with artificial parts. The implants consist of a metal component on the end of the thigh bone, a metal and plastic spacer on the upper end of the shin bone and if needed a plastic button on the kneecap. If the damage is restricted to only part of the knee (usually the inner part), then a partial knee replacement can be carried out in which an implant is used on only half of the knee. Through extensive research conducted in Oxford, surgeons and engineers have been able to design the Oxford® Partial Knee which employs metal surfaces on both bones, with a plastic washer in between, free to glide between the metal surfaces. Since all of the undamaged parts are retained, in particular the cruciate ligaments, the joint has more natural movement.
Biomet has performed many tests on the Oxford® Partial Knee; including evaluating the effect of the implant on the strength of the surrounding bone, and comparing the strength of the knee with other partial knee designs. For testing the effect of the implantation procedure on bone strength; artificial bones from Sawbone were used. The parts were inserted into the artificial bone using the same method that the surgeon would use, and then the parts were tested using the Lloyd EZ50 test machine. The load was applied from the femoral component through a polyethylene bearing (Figure 3). The results from this allowed the surgical procedure to be optimised and minimise any stress to the bone surrounding the implant.
.jpg)
Figure 3. Set up for evaluating a polyethylene bearing surface in a knee implant.
To compare the strength of the Oxford® Partial Knee with other designs the component was placed between two trolleys on a track (Figure 4). A polyethylene spacer was used to apply the load to the part and then the load was applied by the Lloyd EZ50 test machine. A test speed of 0.5 mm min-1 was used and the test was terminated when 5 kN was reached or when the component fractured or deformed.
.jpg)
Figure 4. Testing the Oxford Partial Knee implant.
Summary
This article has highlighted just a few of the ways in which materials testing can be used to evaluate orthopaedic implants. Biomet not only designs and produces the implants themselves, but also surgical instruments; all with the ultimate aim of reducing patient trauma, pain, and recovery time. Osteoarthritis can make day-to-day activities such as walking, driving, and even standing extremely painful. The latest technology is being applied to alleviate this uncomfortable condition.
Oxford® is a registered trade mark of Biomet UK Ltd
References
- https://www.nhs.uk/Conditions/Osteoarthritis/Pages/Introduction.aspx
- https://www.nhs.uk/conditions/knee-replacement/
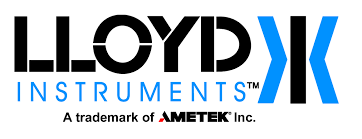
This information has been sourced, reviewed and adapted from materials provided by Lloyd Instruments Ltd.
For more information on this source, please visit Lloyd Instruments Ltd.