Article Updated by Reginald Davey 23/09/22
Aluminum Nitride (AlN) was first synthesized in 1877 but it was not until the mid-1980s that its potential for application in microelectronics spurred the development of high-quality commercially viable material.
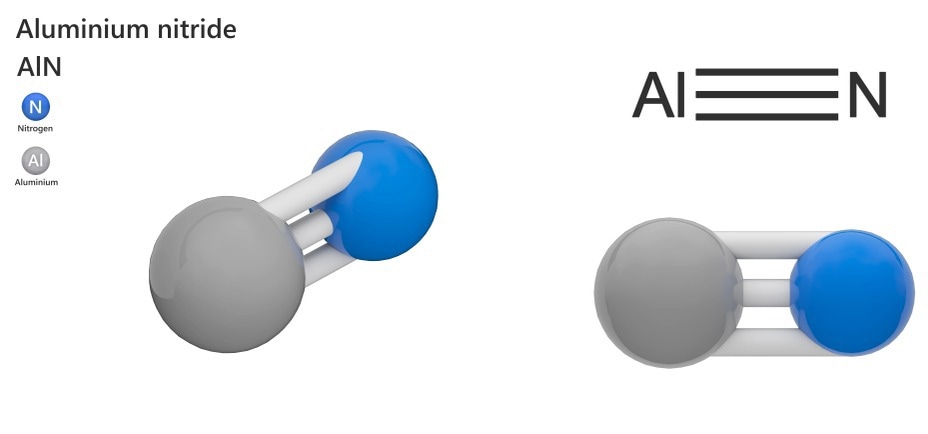
Image Credit: Orange Deer studio/Shutterstock.com
AIN is a form of aluminum nitrate. Aluminum nitride is different from aluminum nitrate, however, as it is a compound of nitrogen which specifically has an oxidation state of -3, whereas nitrate refers to any ester or salt of nitric acid. This material possesses a hexagonal wurzite crystal structure.
Synthesis of AIN
AlN is synthesized by carbothermal reduction of alumina or by direct nitridation of aluminum. It has a density of 3.26 g.cm-3 and although it does not melt, it dissociates above 2500 °C at atmospheric pressure. The material is covalently bonded and is resistant to sintering without the assistance of liquid-forming additives. Typically oxides such as Y2O3 or CaO allow sintering to be achieved at temperatures between 1600 - 1900 °C.
Several processing routes can be used to produce aluminum nitride parts, including cold isostatic pressing, ceramic injection molding, low-pressure injection molding, tape casting, precision machining, and dry pressing.
Key Properties
AlN is resistant to attack by most molten metals, most notably aluminum, lithium, and copper. It is resistant to attack from most molten salts including chlorides and cryolite.
Aluminum nitride possesses properties such as high thermal conductivity for a ceramic material (second only to beryllia,) high volume resistivity, and high dielectric strength. In powder form, it is susceptible to hydrolysis by water or humidity. Additionally, aluminum nitride is attacked by acids and alkalis.
This material is an electrical insulator. Doping improves its electrical conductivity. AIN displays piezoelectric properties.
Table 1. Typical Physical and Mechanical Properties of Aluminium Nitride
Property |
Value |
Density (g.cm-3) |
3.32 |
Modulus of rupture (MPa) |
300 - 350 |
Modulus of elasticity (GPa) |
310 |
Fracture toughness (MPa.m-1/2) |
3.35 |
Coeff of thermal expansion RT-1000 °C (x10-6 K-1) |
5.6 |
Thermal conductivity (W/m.K) |
140 - 177 |
Specific Heat (J.kg.K-1) |
780 |
Volume resistivity (ohm.cm) |
1010 |
Dielectric Strength (kV.mm-1) |
>20 |
Dielectric constant |
8.6 |
Loss tangent at 1 MHz |
5x10-4 |
Applications
Microelectronics
The most remarkable property exhibited by AlN is its high thermal conductivity - in ceramic materials second only to beryllia. At moderate temperatures (~200 °C) its thermal conductivity exceeds that of copper. This high conductivity coupled with high volume resistivity and dielectric strength leads to its application as substrates and packaging for high-power or high-density assemblies of microelectronic components. One of the controlling factors which limits the density of packing of electronic components is the need to dissipate heat arising from ohmic losses and maintain the components within their operating temperature range. Substrates made from AlN provide more efficient cooling than conventional and other ceramic substrates, hence their use as chip carriers and heat sinks (see figure 1).
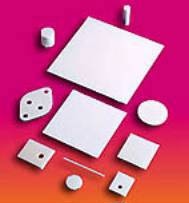
|
Figure 1. AlN substrates for microelectronic applications (Photo Courtesy of Ceram Research Ltd)
|
A widespread commercial application of aluminum nitride is in RF filters for mobile telecommunication devices. A layer of aluminum nitride is sandwiched between two metal layers. Common commercial applications include electrical insulation and heat management components in lasers, chiplets, collets, electrical insulators, clamp rings in semiconductor processing equipment, and microwave device packaging.
Other Applications
Because of the cost of AlN its applications have been developed mainly for military aeronautics and transport fields historically. However, the material has been explored and applied widely in a number of fields. Its beneficial properties make it suitable for several key industrial applications.
Some industrial applications of AlN include refractory composites for the handling of aggressive molten metals, and high-efficiency heat exchange systems.
This material is used to construct crucibles for gallium arsenide crystal growth and is utilized in steel and semiconductor manufacturing.
Other proposed applications of aluminum nitride include as toxic gas chemical sensors. Research has explored the use of AIN nanotubes to manufacture quasi-one dimensional nanotubes for use in these devices. Another application explored over the past two decades is in light-emitting diodes which can operate in the ultraviolet spectrum. Thin-film AIN has been evaluated for use in surface acoustic wave sensors.
More from AZoM: Silicon Nitride / Aluminium Nitride / Aluminium Oxide - Sialon
Disclaimer: The views expressed here are those of the author expressed in their private capacity and do not necessarily represent the views of AZoM.com Limited T/A AZoNetwork the owner and operator of this website. This disclaimer forms part of the Terms and conditions of use of this website.