Toray Advanced Composites is a key provider of thermoplastic advanced composite materials for a myriad of applications such as aircraft structures, industrial components, sporting goods, electronics, medical devices, and oil and gas exploration. The company’s thermoplastic composites are the benchmark for superior-quality engineered thermoplastic composite materials for use in virtually any application.
Advantages of Thermoplastic Advanced Composites Over Metals
- Higher-strength
- Lighter weight
- Rapid forming
- Corrosion resistance
- Lower cost tooling
Advantages of Thermoplastic Advanced Composites Over Thermoset Composites
- Ability to be re-molded and/or reworked
- Suitable for high volume production due to rapid thermoforming to net part shape
- Storable at ambient temperatures without any refrigeration
- Superior moisture resistance
- Superior smoke, flame, and toxicity resistance
- Ability to be fusion welded, avoiding the cost and weight of fasteners
- Low void content
- Recyclability
Similarity Between Thermoplastic composites and Thermoset Composites
- Good toughness and impact strength
- Superior resistance to solvents
- Superior hot/wet performance
- Ability to carry structural loads
- Ability to use automation in work cell production
- Good NDI inspectability
- Ability to use adhesives for structural bonding
- Comprehensive mechanical property databases
- Surpass current standards for flame, smoke, and toxicity (FST) performance
Possibilities with Thermoplastic Advanced Composites
It is possible to produce thermoplastic advanced composite laminates with integral glass surface layers for metallic screens and/or galvanic protection to enable high surface conductivity. It is also possible to die-cut, trim or form thermoplastics into different designs, join or bond into more intricate structures, and overmold with other materials.
.jpg)
Figure 1. Toray RTL laminates are used in conjunction with honeycomb core for use in business and first-class seating which must withstand 16 g loading without failure.
The Toray brand of thermoplastics is supplied in different material forms as follows:
- Flat sheet stock consolidated multi-ply oriented reinforced thermoplastic laminates (RTL)
- Chopped thermoplastic bulk molding compounds
- Fabric and unidirectional prepregs/semi-pregs
Processing
The benefits offered by thermoplastics advanced composites to composite part manufacturers are enormous. The materials’ room-temperature inertness and storability without any refrigeration make them ideal for large assemblies where long fabrication cycles are required. They enable rapid thermoforming on smaller parts utilizing processing equipment. With their quicker cycle times, they enable manufacturers to fulfill high volume demands that were previously possible only with un-reinforced plastics or with metals.
.jpg)
Typical processes utilized with thermoplastic composites include:
- Compression molding
- Thermoforming
- Honeycomb stiffened panel fabrication
- Automated fiber placement
- Automated tape laying
Product Forms
Prepregs/Semi-Pregs
This material form is fabrics and unidirectional tapes impregnated with thermoplastic resin. Based on the polymer and the process, the resin may be completely impregnated, a form called prepreg, or the resin may be present on the fabric surface, a form called semi-preg. Thermoplastic fabric-based prepregs do not have tack but can be draped. They are utilized for larger single curvature parts built up of plies. Unidirectional thermoplastic tapes are ideal for automated blank lay up or automated tape placement with secondary thermoforming operations. However, they are usable in hand lay-up processes.
Toray RTL
This material form is multi-ply fabrics consolidated into flat sheets. Toray RTL laminates feature 1-24 plies for aerospace applications and over 100 plies for industrial applications. It is possible to orient the layers in a 0/90 or 0/+45/-45/90 type stacking sequence. Since Toray RTL materials are fully consolidated, they can be formed into their final shape within minutes as they eliminate the need to undergo the 30-minute consolidation step.
Thermoplastic Bulk Molding Compounds
These materials are obtained from unidirectional thermoplastic prepregs that have undergone a slitting and chopping process to produce 0.5-1" chopped fibers. The ability to compression mold complex components with very short cycle times in an automated production environment is the key advantage of bulk molding compounds.
Other advantages of bulk molding compounds include:
- Metallic properties utilizing molded composites (BMC)
- BMC provides the strength of metals with the lightweight properties of composites
- Complex part geometry
- High volume production with short cycle times
- Full line of TenCate Cetex thermoplastic molding compounds
- Low FST properties
Molded Parts
Toray provides compression molding part fabrication services, including tool design, prototype, and fabrication.
Toray Engineered Thermoplastic Composites
Materials |
Available Product Forms |
Resin Type |
Temperature Service / Tg / Processing |
Morphology |
Features |
Cetex PEEK |
Fabrics, Unitape, RTL, BMC |
Poly-ether-ether-ketone |
Ts = 250-300°F (93-149°C)
Tg = 290°F (143°C)
Tp = 715-740°F (380-395°C) |
Semi-Crystalline |
Highest temperature performance
Excellent solvent resistance
Low FST |
Cetex PPS |
Fabrics, Unitape, RTL, BMC |
Poly-phenylene Sulfide |
Ts = 150-200°F (65-93°C)
Tg = 192°F (89°C)
Tp = 575-625°F (290-325°C) |
Semi-Crystalline |
Excellent solvent resistance
Low moisture absorption
Low FST
Moderate service temperature |
Cetex PEI |
Fabrics & RTL |
Poly-ether-imide |
Ts = 300-350°F (149-177°C)
Tg =423°F (217°C)
Tp = 575-625°F (290-325°C) |
Amorphous |
Good bondability
Good high temperature performance
Low FST
Moderate solvent resistance |
BMC - Thermoplastic bulk molding compounds. RTL - Reinforced Thermoplastic Laminate. FST-Flame, smoke, and toxicity.
Toray CFRT Performance Thermoplastic Composites
CFTR Resin System Performance Thermoplastics |
Process Temperature |
Neat Resin Heat Distortion under Load 1.8 MPa/265 psi |
Applications |
Nylon 6 (PA 6) |
500°F (260°C) |
392°F (200°C) |
Automotive as a result of temperature resistance, toughness and solvent resistance. |
Nylon 11 (PA 11) |
361°F (183°C) |
113-122°F (45-50°C) |
General applications that require lower processing temperatures. |
Polycarbonate/ABS |
448-500°F (249-260°C) |
N/A |
Electronic enclosures as a result of its high quality surface finish and toughness. |
High Density Polyethelyne (HDPE) |
410°F (210°C) |
253°F (123°C) |
Oil and gas applications such as pipe overwrapping as a result of its strength and toughness. |
Polyethylene Terephthalate (PET) |
509°F (265°C) |
392°F (200°C) |
Excellent for recreational and low cost applications for its good impact resistance. |
Polymethylmethacrylate (PMMA) |
380-390°F (199-216°C) |
N/A |
High impact resistance behaves as both a thermoset and thermoplastic. Commonly used for athletic shoe inserts and orthotics. |
Polypropylene (PP) |
158°F (70°C) |
318°F (159°C) |
Excellent toughness, used for vehicle body construction. |
CFRT - Carbon Fiber Reinforced Thermoplastic.
Industry Applications
Aerospace
Toray composites are used in the aerospace industry for applications such as structural components, which include wing leading edges, cargo flooring, engine pylon structures, interior galleys, and acoustic structures, as well as various molded parts, which include interior panels, clips, seats and ducts.
.jpg)
Figure 2. Current Toray thermoplastic applications in aerospace.
Electronics
Thermoplastic composites provide enormous benefits to computer and smartphone cases thanks to their lightweight, high surface quality, and impact resistance. They offer the desired durability and manufacturability because designers focus on thinner and lighter designs.
Transportation
Thermoplastics provide quick cycle times utilizing thermoforming processes, a common technique used in the automotive industry. Their solvent resistance and high-temperature properties make them suitable for under the hood applications. They offer superior durability, high strength to weight ratio, and toxicity, smoke, and fire resistance in larger rail cars and mass transit vehicles.
.jpg)
Figure 3. Commercial aircraft interiors value Toray thermoplastics because of their smoke and fire resistance and durability.
Energy
The oil and gas industry uses advanced thermoplastic composites to attain weight reductions in corrosive conditions. Composites offer weight reductions of 40% lower than aluminum and more than 80% over steel.
Industrial
The possibility of forming and machining of thermoplastic composites enables them to be used as a replacement for heavier metal parts in fly wheels, structural brackets and rotating.
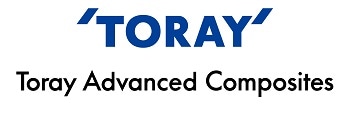
This information has been sourced, reviewed and adapted from materials provided by Toray Advanced Composites.