Rotary furnaces are the latest technology for high temperature processing of powdered materials. They inherently offer significant advantages of throughput and energy efficiency over other forms of continuous, high temperature equipment. Some materials are well served by simple tube designs. In other cases, reaction conditions or stringent time-at-temperature requirements may necessitate more advanced designs. In this discussion we will review several indirect-fired rotary furnace design improvements that are targeted to maximize the utility of the process while meeting the critical needs of more difficult processes.
Mixing & Conveying Technologies
Normally, axial mixing in a rotary is not desired. However, the following are examples where it provides an improvement to the processing environment in a rotary furnace:
- Exothermic Reaction: If the process is operating near an unstable point, the traditional approach is to increase the heat transfer area (length and diameter) of the furnace to move away from the unstable operating conditions. Riffle flights allow the reaction energy to be absorbed into the cold feed material. This reduces the energy requirement over-all and reduces the CAPEX by optimizing on a smaller equipment size.
- Batch, Gas-Solid Reaction near Stoichiometry: A rotating reactor containing solids that are reacting with an axially flowing stoichiometric gas would produce different grades of material at different positions along the length of the reactor. Riffle flights continuously distribute the material randomly along the reactor axis. All particles of the solid spend approximately equal times at the different posi-tions along the reactor creating a uniform product.
- Mixture with Reactive Solid Addition: Riffle flights can be used to make a con-tinuous in-line mixer at the threshold of the reactor. This minimizes stored vol-ume of the mixed reactive solid. This helps to minimize excess addition while maintaining a complete reaction.
- Helical flight technology is another alternative. It is limited to relatively short residence times, as the material is conveyed through the furnace at a uniform rate. The drawback of this technology is that it is difficult to employ when you have a long residence time, but beneficial for reactions with a narrow time-at-temperature requirement.
Atmosphere Management
Multiple atmospheres can be achieved through design of independent, but cascad-ing rotary systems with atmosphere isolation. Control of pressure between upper and lower units is critical to ensure complete separation of the atmospheres. The design in Figure 2 utilizes stacking rotaries to take advantage of height opportuni-ties and eliminates need for material conveyance equipment by utilizing gravity. This custom system enables long residence times, multiple atmospheres and high production volumes.
Another unique rotary furnace design may include advanced control of multiple atmospheres in a single tube. This is advantageous as it eliminates the need for multiple unit operations and condenses the requirements into one.
.jpg)
Figure 1.
Image Credit: Harper
.jpg)
Figure 2.
Image Credit: Harper
Ultra High Temperature Processing
The ultra high temperature system in Figure 3 is designed for atmosphere sealing of both for the process atmosphere and the chamber atmosphere, which allows the use of specialty tube materials such as graphite or refractory metals. These are required for very high temperature processing, typi-cally temperatures well over 2000°C. A key challenge is the clamping and driving of the tube, especially when it is contained within the chamber at-mosphere. This often precludes the ability to maintain the seal without temporarily stopping production. In this schematic, the tube holding and driving method is located external to the chamber atmosphere. It allows for tube expansion and expansion mismatch at the ends of the tube. It is driven on both ends to minimize torque transmission through the tube.
The style of holding the tube shown also provides a space for water-cooling. The same tube support length can be surrounded by a water-cooling spray. Cooling at both ends is critical for processing at these temperatures, as compared to a traditional alloy rotary which may only have a cooling section at the discharge end to cool the product. This style keeps eve-rything cool; drive system, riding tires, gaskets, feeding equipment, discharge valves, and the product.
.jpg)
Figure 3.
Image Credit: Harper
High Production Volume
After initial materials development investigations and pilot scale production campaigns, it is necessary to consider commercial scale production. Scaling of thermal processes is rarely a simple matter of linear extrapolation. At experimental scale, the conversion rate of many solid-solid and solid-gas reactions is primarily a function of the set point temperature, overall atmospheric chemistry, size of the reactants, and the quality of the inter-mixing. In small research test furnaces, the furnace temperature can track the control profile very well. If the sample load is relatively small, it may also track well with this de-sired profile. At the same time, the ability to remove product gases and replenish with fresh gas is simplified by the small internal volume of the furnace, and ratio of sample to furnace volume. Under these experimental conditions, product uniformity is rarely a significant concern. As the reaction is scaled to larger sizes, the ability to heat or cool the mass of material and the ability to introduce or remove gasses from the solids plays an increasingly important role in reaction efficiency. Often these become the primary variables that control the conversion rate, and therefore the throughput and efficiency of the process. These variables create process limitations that extend the total processing time, which impacts both throughput and total energy utilization of the process.
Harper’s expertise in process scale up allow for designs accommodate mass rates from tens to thousands of pounds per hour. Figure 2 offers a contained processing environment around 1,800 ft³ with multi-atmosphere, long residence time system. Figure 4 is designed for a traditional resi-dence time at high production rates. Often, large indirect, rotary tubes with high mass throughputs can be limited in production or useful life due to large stress in a section of the tube. This can be mitigated using internal tube features to properly pre- treat or add time to the first heat up zone. This is where the majority of the tube stress builds up, typically because of feed moisture or low boiling organics. Managing these volatiles and segre-gating atmospheres along the length can also increase production rate. The removal of volatiles drives reactions and can minimize certain sticking phenomena. In turn this allows for higher through-put and utilization of the large process volume.
Conclusion
Ultimately, the ideal future design state equally incorporates improvements in product quality, throughput, energy efficiency and operating expenses. More complex chemical reactions will require thoughtful consideration of the kinds of design en-hancements reviewed here to ensure the best balance of all the critical factors.
About Harper International
Harper International is a global leader in complete thermal processing solutions, as well as technical services essential for the production of advanced materials.From concept to commercialization, from research scale to full production line operations, Harper is perpetually on the cutting edge. For decades, we have pioneered some of the world’s most innovative, customized systems, with a focus on processing materials at high temperatures and in non-ambient atmospheres.
Harper’s value proposition is unequaled — decades of industry experience, a highly specialized, multi-talented group of employees, and a passion for partnership. We don’t shoehorn a standard line of products to fit our customers’ requirements. We specialize in first-of-a-kind solutions using our exceptional depth and breadth of knowledge. Harper’s culture is one of genuine ingenuity and creativity, which ensures we are constantly challenging ourselves to craft the best-engineered technology solution for our customers’ unique thermal processing needs.
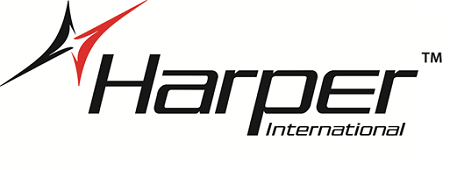
This information has been sourced, reviewed and adapted from materials provided by Harper International.
For more information on this source, please visit Harper International.