The manufacture of ALD-coated particles involves a combination of an advanced ALD process and powerful industry-standard material handling.
In the last 10 years, Forge Nano has been developing and constructing a range of most reliable and sophisticated particle ALD reactor systems in the world. The company routinely uses such high quality systems to perform plenty of process development for worldwide customers, and it currently provides this same capability to its commercial customers.
Global Leader in ALD on Particles
For more than 15 years, Forge Nano has worked with research and development teams to invent sophisticated materials. The global partners of Forge Nano have leveraged the company’s materials development for commercial production to benefit consumers at a large scale.
ALD-Enabled Particle Material Equipment
Rooted in upgradable particle-handling technology, Forge Nano’s systems are custom-made to suit users’ product line and lot size:
- Catalysts
- Energy materials
- Pharmaceuticals
- Modified interfaces
- Encapsulation
- Powdered metals
The LITHOS Rotary Blender Reactor System from Forge Nano integrates industry know-how in rotary particle handling with a deep knowledge of ALD, and the result is a reliable, flexible and user-friendly production system.
The advanced system from Forge Nano has been developed to coat every particle with unparalleled thickness and conformity control and, at the same time, reduce or prevent the agglomeration of particles.
The production machines from Forge Nano can be customized and built to order, guaranteeing an optimal solution for all customers.
Technical Specifications
Source: Forge Nano
Production Blender Reactor System Specifications |
Powder Processing Volume |
50-500 L (up to 1000+kg) |
Maximum number of ALD cycles |
Unlimited |
Maximum Reactor Temperature |
200 °C or 400 °C |
In-situ Mass Spectrometer (Residual Gas Analyzer) |
Interfaces with custom control software to automate coatings on powders. |
Precursor Delivery Cabinet |
Up to 4 different precursors (Two sources standard) |
Powder Loading/Unloading |
Manual, gravity dump (automated options available) |
Process Line and Valve Temperatures |
Up to 200°C |
Particle Handling |
Multi-mode rotary Including proprietary particle handling aids |
Software/ Controls |
Recipe-based proprietary software with automated feedback control |
Complete System Dimensions |
~3 m x 2 m x 3 m |
Optional Additions |
Precursor Automated Refill Station |
Automatically refills smaller delivery cabinet reservoirs from bulk distribution unit for minimal downtime. |
In-situ Mass Spectrometer (Residual Gas Analyzer) |
Interfaces with custom control software to automate coatings on powders. |
Drum Handling/Loading Mechanism |
Provides assisted drum loading/unloading |
Additional Material Handling Equipment |
Powder pumps, collection hoppers, or bulk bag loaders can be integrated into the system installation. |
Consumables and Likely Spares Package |
Includes common consumables and spare parts |
Regulatory Compliance |
NRTL Field Certification Available |
Proprietary Process Automation
Every system is supplied with Forge Nano’s proprietary software and controls. The technology was designed over decades of refinement for producing ALD-enabled products at ton, kilogram and gram scales. This comprises the company’s in-situ mass spectrometry, which allows users to accurately control the dosing of precursors and the growth of ALD film thickness. The technology is suggested for all Forge Nano systems.
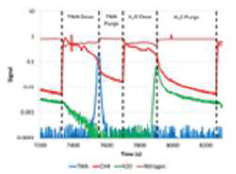
The image shows in-situ mass spectrometry signals from Forge Nano’s R&D Reactor Systems. Image Credit: Forge Nano
Forge Nano has designed proprietary commercial-scale and pilot-scale reactors that currently create ALD-coated materials for customers. The company supports the operation and integration of this system at its customers’ state-of-the-art materials production facilities.
Forge Nano’s Fortune 500 customers have verified the coating consistency across the company’s pilot, research and commercial systems, such as its continuous vibrating reactor system that has been designed to process more than 12,000 kg of powder every day.