The School of Engineering and Applied Sciences (SEAS) at Harvard University needed a metrology instrument in order to quantify the relationship between a natural insect wing, a micro-machined silicon mold, and the resultant fabricated wing (Figure 1). This requirement was met by the Evident OLS4000 Laser Confocal System at the laboratory of Professor Robert Wood, a specialist in the design, fabrication, analysis and control of mobile micro robots.
Using the Evident OLS4000 Laser Confocal System, accurate morphological measurements are carried out to create micromolds and artificial insect wings.
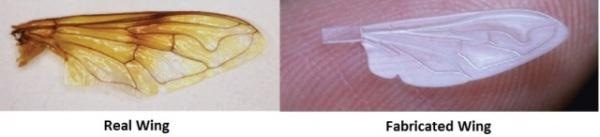
Figure 1. This image shows the real wing and fabricated wing.
Instrumentation
Professor Robert Wood and Dr. Hiroto Tanaka created an artificial insect wing using a polymer hinged with carbon fibers (Figure 2). Wing structure characterization in 3D is crucial to understand the flexibility and aerodynamic performance of insect wings during flight. Accurate details and profile measurements in particular are crucial to fabricate the artificial wing.
For this task, the Evident LEXT OLS4000 Laser Scanning Confocal Microscope (Figure 3) was preferred over a SEM and stylus profilometer. The OLS4000 is able to perform rapid and accurate measurements of deep cavities and 85° sloped walls.
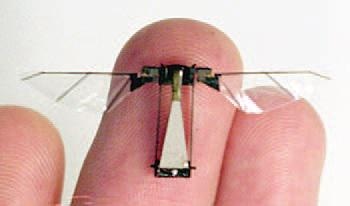
Figure 2. Robotic Insect Wings
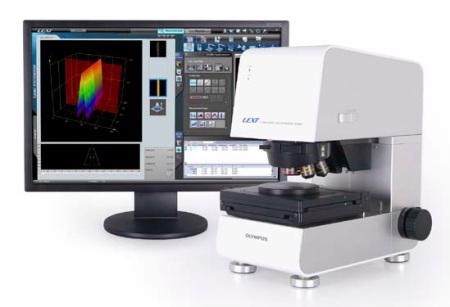
Figure 3. The Evident LEXT OLS4000 Laser Scanning Confocal Microscope
Recreation of Insect Wing
The team first created a formal design of a hoverfly wing, before producing a mold. It was a laborious effort to replicate the complex topographical features found on the wing’s top and bottom into a silicon mold. The selection of silicon for mold material is based on its compatibility with the laser ablation etching process. The exact details were reproduced by repeatedly using laser ablation for numerous times.
The level of intricacy involved in this project can be understood from the micro-scale features needed to be replicated: 100µm corrugation heights, 50-125µm vein heights, and 10µm thin membranes. These micro-scale features were integrated by the OLS4000 as a quick check in the event of ablation.
The OLS4000 provided details of etch depths after each ablation at an acceptable deviation of ±0.3µm/step and scanning time of below 1min. This is a rapid process, allowing the team to make decisions on whether further ablation was required or not. The surface profile measurement results of the natural insect wings, the silicon molds and the resultant artificial wings clearly demonstrated the high precision capability of this replication molding process technique.
Measurement of Square Shaped Channels
The topology of the fabricated wings also needs to be matched with the natural wings because the wing profile also contributes to flight performance. The magnitude of aerodynamic lift and drag is affected by the wing profile, which also decides the flexibility and resultant deformation of the wing during flapping flight. The sensitivity of the LEXT OLS4000 is high due to the use of dual confocal pinholes and detectors, allowing the imaging and measurement of sidewalls of up to 85°.
Dr. Tanaka’s mold designs required deep-etch U-shaped channels with high aspect ratios. These critical surface features can be accurately measured with the OLS4000 (Figure 4).
The OLS4000 is able to make measurements and observe structural features over a broad field of view, thanks to its stitching capability. This capability allowed one cohesive profile measurement of the entire wing section to be taken.
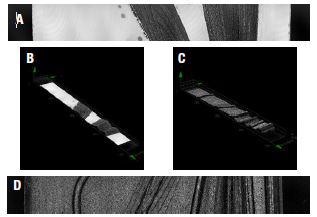
Figure 4. A. Fabricated wing, smooth side, 2-D; B. Fabricated wing, smooth side, 3-D; C. Fabricated wing, vein side, 3-D; D. Fabricated wing, vein side, 2-D.
Verification of Carbon Hinge Quality
The artificial wing has a hinge at its base. The hinge comprises two parts: a very narrow white film flexure and black colored rigid carbon fiber parts. The width and thickness obtained after laser ablation are highly significant.
Width fidelity is crucial as the hinge’s overall stiffness is affected by this factor and was observed by the brightfield CCD non-confocal imaging mode of the OLS4000 coupled with the calibrated ruler feature (Figures 5, 6, and 7). Additionally, the thickness was verified using a scanned laser image. The thickness was 80µm±5µm.
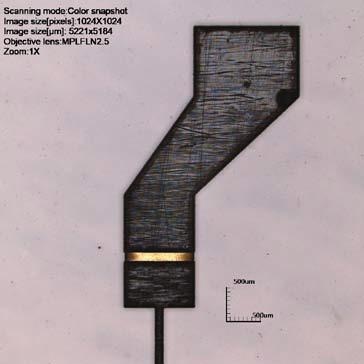
Figure 5. Cabon Hinge Overview. OLS4000 Brightfield CCD non-confocal mode, Objective lens MPLFLN 2.5X
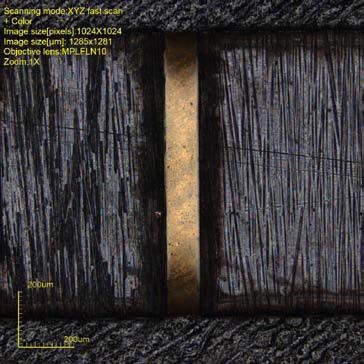
Figure 6. Carbon Hinge. OLS 4000 Laser confocal mode with color overlay.
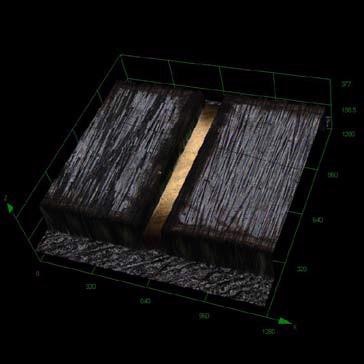
Figure 7. Carbon Hinge. OLS 4000 Laser confocal mode, 3D.
Conclusion
Dr. Wood’s lab is currently involved in the design of components that are capable of replicating insect flight for robotic applications. They now have the ability to replicate the structures and functionality of the insect flight device. Using the surface scan measurements provided by the OLS4000, the research team was able to verify that the replication accuracy between the mold, the fabricated wing, and the natural wing as nearly identical. In addition, the project was completed well ahead of schedule, thanks to the rapid and accurate measurements of the OLS4000.

This information has been sourced, reviewed and adapted from materials provided by Evident Corporation - Industrial Microscopy.
For more information on this source, please visit Evident Corporation - Industrial Microscopy