Dielectric cure monitoring, also called Dielectric Analysis (DEA), is the only technique that can quantify the state of composite or thermoset cure in real time and under real process conditions. Therefore, DEA can produce results in the laboratory that can be directly applied to the field of manufacturing.
In short, DEA quantifies the permittivity and resistivity of thermoset; both permittivity and resistivity are the dielectric properties of the material.
As such, resistivity has a frequency-dependent component because of the rotation of stationary dipoles, and a frequency-independent component because of the flow of mobile ions.
Usually known as DC resistivity for brevity purposes, frequency-independent resistivity, in fact, extends over a range of frequencies, including DC (0 Hz).
Frequency-independent resistivity is a useful material probe because it corresponds with the state of cure. By leveraging optimal frequencies, AC measurements — different from DC techniques — can handle data distortion caused by electrode polarization and can work through vacuum bags and release films.1
The term ion viscosity (IV) is a synonym for frequency-independent resistivity. This article will use ion viscosity rather than the more unwieldy frequency-independent resistivity, and viscosity rather than mechanical viscosity.
Characteristics of Thermoset Cure
In the majority of cases, the change of log (IV) is proportional to the change of viscosity prior to gelation, and also to the change of modulus following gelation. Therefore, DEA can observe cure during an entire process.
Figure 1 shows the relationship between viscosity and ion viscosity for a curing thermoset with a single temperature ramp and hold. Initially, ion viscosity decreases with increasing temperature because the thermoset becomes more fluid and therefore less resistive.
The rate of the reaction increases as the material gets hotter. At some point in time, the increased ion viscosity caused by polymerization overcomes the decreased ion viscosity caused by rising temperatures. This point is the minimum ion viscosity that also occurs at approximately the time of minimum viscosity.
After reaching a minimum value, ion viscosity increases as the reaction becomes faster and the material turns more viscous. At gelation, with the start of crosslinking and network formation, viscosity increases quickly until it becomes immeasurable. However, ion viscosity continues to offer data about the state of cure beyond the gel point.
The reaction rate decreases with decreasing concentration of unreacted monomers and with more extensive crosslinking. As a result, the slope of ion viscosity also decreases and ultimately ion viscosity will have a zero slope when cure ceases completely.
.jpg)
Figure 1. Ion viscosity and mechanical viscosity for thermoset cure. Image Credit: Lambient Technologies.
Figure 2 illustrates data from a standard thermoset cured with a temperature ramp and hold.
.jpg)
Figure 2. Ion viscosity and slope of ion viscosity for thermoset cure during thermal ramp and hold. Image Credit: Lambient Technologies.
As depicted in Figures 1 and 2, four Critical Points define the data:
- CP (1) — A user-defined log(IV) level to detect the onset of material flow.
- CP (2) — Minimum ion viscosity to detect the time of minimum viscosity.
- CP (3) — Inflection point of log(IV) to detect the time of maximum reaction rate. The CP (3) height is a relative measure of the reaction rate, and the time of CP (3) is generally used as a signpost related to gelation.
- CP (4) — A user-defined slope of log(IV) to identify the end of cure.
The response is somewhat different when the processing conditions are typically isothermal, as illustrated in Figure 3. In this example, CP (1) is either pointless or arises at t = 0, as soon as heat is applied and when the material flows to make contact with the sensor. Moreover, minimum ion viscosity occurs at t = 0 or immediately afterward since cure starts immediately.
For isothermal cures, both CP (3) and CP (4) are theoretically the same as for ramp and hold conditions.
.jpg)
Figure 3. Ion viscosity and slope of ion viscosity for thermoset cure during isothermal processing. Image Credit: Lambient Technologies.
Correspondence of DEA with Other Properties
Figures 4, 5, and 6 illustrate a few examples from published studies, where ion viscosity has been compared with viscosity, glass transition temperature, and sound speed, respectively.
.jpg)
Figure 4. Viscosity versus conductivity (ion viscosity = 1/conductivity) for an epoxy.2 Image Credit: Lambient Technologies.
.jpg)
Figure 5. Conductivity (ion viscosity = 1/conductivity) versus glass transition temperature for a carbon fiber-epoxy composite.3 Image Credit: Lambient Technologies.
.jpg)
Figure 6. Resistivity (ion viscosity) versus sound speed for a curing epoxy-fiberglass prepreg.4 Image Credit: Lambient Technologies.
Users should always confirm the relationships of ion viscosity with the other properties of a material because every material is different. Nonetheless, DEA complements other thermal analysis methods such as dynamic mechanical analysis (DMA) and differential scanning calorimetry (DSC) as a useful tool for analyzing the curing of composites and thermosets.
References
- Application note AN2.39, “AC and DC Cure Monitoring through Release Films and Vacuum Bags,” Lambient Technologies, Cambridge, MA
- J. Simpson and S. Bidstrup, “Rheological and Dielectric Changes during Isothermal EpoxyAmine Cure,” J. of Polymer Science Part B: Polymer Physics, vol. 33, issue 1, pp 55-62 (1.1995)
- J.H. Chen, M.A. Octeau, M. Hojjati, and A. Yousefpour, “Cure Cycle Optimization for Composite Panels Fabricated by RTM Using Dielectric Sensors,” National Research Council Canada, Institute for Aerospace Research, ICCM International Conferences on Composite Materials (2009)
- D. Shepard and K. Smith, “Ultrasonic Cure Monitoring of Advanced Composites,” Sensor Review, vol. 19 Issue: 3, pp. 187-194 (1999)
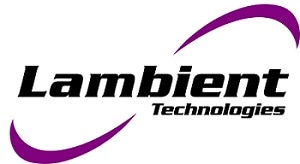
This information has been sourced, reviewed and adapted from materials provided by Lambient Technologies.
For more information on this source, please visit Lambient Technologies.