Fiber-reinforced composites and filled plastics used in a wide range of products use thermoset polymers as the key matrix. The applications include consumer items, auto body panels, aerospace structural components like the SpaceShuttle payload bay door, jet engine cowls and ducts, and costly, high-performance sports equipment. Thermosets are mainly used as molding compounds, adhesives and surface coatings, including protective solder masks for PCBs.
Thermosets Versus Thermoplastics and Elastomers
Thermoplastics
Thermoplastics are processed in the molten state, their final shape and internal structure are established by cooling, and they can be softened and reshaped by reapplication of heat and pressure. Also after molding, their polymer chains, whether branched or linear remain discrete.
Thermoset Polymers
Thermoset polymers usually undergo three stages are:
A–stage known as a resole, wherein the resin is still fusible and soluble.
B-stage is the stage wherein the thermosets are almost insoluble but are thermoplastic. They can remain in the molten state for only a short period as the temperatures promoting flow cause cross-linking of the material.
C-stage – This is the final stage of polymerization wherein the cross linking reaction takes place at the time of molding the product under controlled impact of heat and pressure over time.
Hence, the final structure of thermosets is constructed during processing, creating a 3D internal structural network of highly crosslinked polymer chains. The final product cannot be thermally reformed and is insoluble.
Elastomers
Elastomers share the properties of both thermosets and thermoplastics. They are first thermoplastic polymers with distinct chains that afterward develop a covalent crosslink network. However, the difference between elastomers and thermosets lie in the fact that the crosslink network is formed in a distinct vulcanization step known as post polymerization.
The glass transition temperature Tg is another factor that differentiates the three polymer classes. This is the temperature at which polymers reversibly transmute between glassy and rubbery states. The glass transition temperature is below ambient temperature for elastomers, and for thermosets and thermoplastics, it is above the ambient temperature.
Studying the Crosslinking Reaction
Figure 1 shows the formation of a thermoset crosslinked network. By using rheological analysis, which is the measurement of shear modulus, damping and resin viscosity, this process can be understood better. In thermoset polymer research and development, rheological testing has become a suitable supplement to chromatography, DSC and wet chemical analysis. This is because of the nature of the processes involved and rheological changes in them.
Thermoset Processing - Multistage Processing
Thermosetting resins are processed in two or more stages. For instance, consider those used for fabricating fiber-reinforced laminates. First, a laminating varnish is developed from curing agent, resin monomer, other functional additives and a solvent. The varnish is then applied to a reinforcing fabric made of high modulus fibers or glassfiber. The solvent is then removed and the resin reacts partially to form a prepreg.
At the B-stage, the prepreg is partly soluble and is a low-melting thermoplastic solid consisting of unreacted monomer, adduct and higher molecular weight oligomers. Adduct is a re-action product in which the ratio of resin to curing agent is 1:1.
Certain resins like epoxies need to be secured from moisture and refrigerated to forestall “advancement”, that is, continuation of the reaction. For product fabrication, a multilayer sandwich of prepreg is created, placed in an autoclave or a press, and heated to “cure”.
Several things need to be achieved at this stage – the fibers must be thoroughly wetted with resin, the laminate needs to be consolidated to the required thickness, excess resin must be removed, trapped air, and moisture and solvent need to be vented out to avoid porosity, and the cross-linking reaction is advanced to the preferred level.
With a rise in temperature, prepreg melts and the viscosity drops precipitously, after which it levels and then climbs again. The viscosity behavior is due to the intervention of a competing situation – the rising temperature triggers additional reactions among monomers, oligomers and curing agent improving the viscosity of the prepreg. The multi-functional reactants cause crosslinks to rapidly form between the polymer chains in all directions. The system gels and flow stops suddenly. The matrix is solid at this point and the shape and thickness of the composite are constant. Additional heating is needed, however, for the matrix to form the balance of ist potential crosslinks and to develop, for the most part, ist ultimate level of stiffness. To accomplish this, an additional out-of-mold post-cure step is generally used.
Single-Stage Processing
Thermosets are also processed in a single stage method known as reaction injection molding (RIM). RIM has gained popularity for a range of recreational and automotive application. RIM is similar to thermoplastic injection molding. The main distinction is that RIM uses polymerization in the mold instead of cooling to enable formation of a solid polymer.
Rheology of Thermosets
Polymerization is also used by other reaction molding processes for solidifying the molded piece. In thermoset injection molding, reactants are subjected to heat of 200°C for reaction activation. In RIM, the reactants are combined at a considerably lower temperature as impingement mixing activates the reaction, not the external heat.
In the RIM process, complicated plastic components are rapidly produced directly from low viscosity reactants. Two or more liquids are impingement mixed at low pressures and temperatures when they are introduced into the mold. Phase separation of segmented block copolymers forms a solid polymer, and parts can now be ejected from the mold within a minute.
.jpg)
Figure 1. Schematic representation of structural development during thermoset curing: (A) unreacted monomers; (B) formation of small branched molecules; (C) the gel point: a path of covalent bonds exists across the sample; (D) the cured, cross linked polymer with some unreacted groups and reactants.
Process Rheology
Thermoset structural development involves various rheological changes. The transformation of the resin occurs from a low melting thermoplastic solid to low viscosity liquid to a stiff solid. Hence, the properties are very important for successful processing. Resin flow has an impact on porosity, dimensional uniformity of the cured part and process economics.
Resin flow properties influence the uniformity of etched circuit encapsulation, final press thickness and copper-to-epoxy adhesion in multilayer printing boards. Hence, at each stage of the process, the rhelogical state should be known to employ these materials economically and effectively.
Thermosetting resin rheology can be studied using both dynamic oscillatory tests and steady shear. The first section of the viscosity range of a thermoset can be characterized with steady shear measurements. There is a rapid increase in steady shear viscosity close to the gel point and it becomes unmeasurable. The stiffened sample eventually tears or fractures.
As the reaction advances to the gel point and beyond, the resin’s viscosity measurement can be performed until the resin becomes a stiff solid. This is feasible as the measurements can be made at a strain amplitude that is low enough to prevent gel structure disruption during its formation.
Figure 2 shows the comparison between steady shear viscosity data and dynamic viscosity data for a curing epoxy resin. It is important to be able to measure viscosity throughout the thermoset curing reaction though it offers only a partial picture of the phenomenon taking place. Elasticity data are required to complete the characterization due to viscoelastic nature of the material. These are acquired in a dynamic test concurrent with viscosity measurement.
.jpg)
Figure 2. Measurement of the viscosity of a curing epoxy resin
The storage (G’)and loss (G”) moduli and complex viscosity η* determined at the time of an epoxy molding compound cure is shown in Figure 3. Other than offering minimum viscosity data, the cross-over point of the two modulus curves offer an estimate of the time at which a resin starts gelling. This is however only an approximate gel point.
.jpg)
Figure 3. Measurement of the minimum viscosity and approximate gel point for a curing epoxy molding compound.
The issue is that as the transient gel network structure is forming and stress relaxation also occurs simultaneously. Therefore, unless gelling system measurements are made rapidly, the precise gelation time will be obscured by changes because of stress relaxation. It has been observed in a recent study by H.H. Winter that the cross-over point of loss and storage modulus curves is not the true gel. Instead, the gelation point is when the critical gel shows power law stress relaxation, and tan δ becomes frequency-independent momentarily. It is possible to identify this point by performing a number of frequency sweeps simultaneously.
As observed in Figure 4, there are dynamic oscillatory measurements of tan d simultaneously made at three frequencies on a crosslinking polydimethylsiloxane (PDMS) resin. The three curves traverse via a single point and define the instant of gelation unambiguously. These measurements are made readily using a rheometric rheometer with the MultiWavemode.
.jpg)
Figure 4. The precise gel point of a curing resin is identified by the intersection of tan δ curves generated in several simultaneous frequency sweeps
Product Performance
It is important to avoid both under cure and over cure to obtain the optimum performance from a thermoset resin. The drawback of an undercured matrix is that it shows creep and creates heat when vibrated while an over-cured matrix exhibits performance issues at room temperature. Cooling causes internal stresses to build up in the glass polymer as it cools causing stress cracks to develop.
To show the extent of thermoset resin cure, Tg or the glass transition temperature determined during TGA and DSA is used. For instance, when compared to a completely cured control sample of known good performance, a lower glass transition temperature shows under cure. However, it cannot be implied that a higher Tg indicates over cure. The distinction between complete cure and over cure cannot be concluded by determining the Tg.
A high glass transition temperature may occur from exposure to temperatures more than those of cure or post cure. If the prepreg is cut and subjected to a high relative humidity, the glass transition temperature can be lower. So, it is clear that Tg alone is not sufficient.
Glass transition is a temperature-induced morphological change in a polymer between a brittle, glassy state and a viscous, rubbery state. The temperature at which this occurs is the glass transition temperature. Since in just a short span of temperatures, the material undergoes a significant change, the glass transition is key to decide if a polymer meets the desired requirements. Dynamic rheological testing is most suitable.
The impact of glass transition can be observed while measuring moduli (G’, G”) and damping behavior (tan δ) of a polymer at a specific oscillatory frequency over a significantly wide temperature range. Glass transition is determined as a sudden and significant change in the elastic modulus and an attendant peak in the tan δ curve. Other than being a more precise technique for determining Tg, DMRT reveals a significant amount of data about the material before and after glass transition as DMRT determines the rubbery plateau modulus. This is essential as at high thermoset cure levels the rubbery plateau modulus exhibits higher sensitivity than Tg itself for detecting, for instance tiny variations in the cure level of a thermoset polymer.
Also termed as the transition, glass transition is related to crank-shaft movement of key chain segments. Other transitions termed as b, g, etc in order of the descending temperature of occurrence are caused due to rotations and vibrations. Impact resistance and material toughness correlate with the magnitude of tan δ at the secondary (β, γ) peaks. For a number of materials, with an increase in the dynamic oscillatory frequency, transitions take place at higher temperatures. Certain transitions shift certain amounts based on their degree of frequency dependence.
This helps in identifying certain transitions in multiphase resin systems in case one component shows more frequency dependency than the other does. In the event of shifts in the b peak and the glass transition temperature, the b-peak shows the impact of compounding or process changes on product performance. Generally, the secondary transition temperature shifts more than the glass transition temperature with an alteration in frequency.
The technique of using dynamic mechanical testing for studying the crucial factors of thermoset rheology during resin curing and solid state finished product performance is explained below.
Sample Selection and Preparation
If the immediate application involves use of resin the tests must be conducted on material in that form. If prepregs are used tests must be made on the staged resin extracted mechanically from the prepreg or directly on laminate die-cut samples. The diameter of the parallel plates to be used for the dynamic mechanical tests decides the die size.
For tests that cause curing of the resin, disposable plates must be used as resin can strongly stick to the plates. In order to reduce ist bulk and hold the plies together, the sample needs to be pressed, preferably under vacuum.
In order to prevent slippage, the test needs to be started at a temperature when the resin is tacky. Powdered resin samples need to be pulverized, dried and pressed in a mold creating a wafer of size comparable to the test plate’s diameter.
Generating Viscosity Profiles
The most crucial stage for a thermoset polymer is to develop the right curing level. To ensure that under curing and over curing are prevented, a thermoset cure cycle can be obtained from measurements of the curing resin’s dynamic viscosity profile as a function of time and temperature.
The design of the rheometers is such that these kind of measurements are possible. In eight distinctly controlled zones, test temperatures can increased at rates of 1° to 5°C/min using a time cure mode. It is possible to program each zone for a total time, measure time, ramp rate, percent strain and final temperature. It is therefore possible to conveniently sample any cure cycle. Rheometers have a MultiWave mode offering highly accurate measurement of the gel point by determining tan d in a number of simultaneous frequency sweeps.
From several measurements at a range of temperature ramping rates mostly 1° to 5°C/min, the storage (G’) and loss(G”) moduli and the complex viscosity η* are obtained and the following data is acquired:
- Initial viscosity
- Minimum viscosity
- Gel point
- Optimum heating rate
Initial Viscosity
The onset of matrix melting is indicated by the initial viscosity, which is the first point of the viscosity profile and this is not impacted by heating rate. It indicates the degree of resin advancement for quality control.
Minimum Viscosity
The time period and the temperature range over which resistance is lowest is signified by the minimum viscosity.
Gel Point
The time or temperature at which the first sequence of covalent bond link across the sample is termed as the gel point and the molecular weight becomes very large. The gel point is key in determining the time and temperature at which pressure needs to be applied.
Optimum Heating Rate
It is important that the heating rate be optimized as the time required for attaining the minimum viscosity is impacted and also the time and temperature intervals over which the minimum viscosity extends. A rapid heating rate may result in unwanted temperature differentials within the component, porosity issues and irregular curing all through the piece. The impact of heat-up rate on the viscosity profile transition is shown in a sudden and significant decrease in the storage modulus with an attendant peak in the tan δ curve in Figure 5.
.jpg)
Figure 5. Measurement of the viscosity profile of a curing thermoset resin as a function of heat-up rate
Isothermal Scans
Once the gel point and the minimum viscosity have been determined, a sequence of isothermal scans are performed at temperature intervals starting from the minimum viscosity temperature and continuing up to the gel point temperature at about 10°C intervals.
Using the Viscosity Profile
A dynamic mechanical viscosity profile offers excellent utility in all phases of thermoset polymer technology such as product development, research, process development and control and quality control.
Research
Dynamic mechanical testing is used widely in thermoset composite research for offering the required material properties for finite difference and finite element analysis. Dynamic viscosity profiles also offer important information for research on cure reaction kinetics, advanced curing concepts like gas diffusion control and process modeling with expert systems. Diffusion control brings down gas bubble nucleation in the curing matrix by inducing hydraulic pressure in the resin during the cure cycle’s gas volatilization stage.
.jpg)
Figure 6. Isothermal scans at various temperatures are used to help decide on the time interval and temperature at which to impose isothermal holds during a thermoset resin production cure cycle
A typical matrix resin cure cycle with diffusion control superimposed on the viscosity profile is shown in Figure 7.
.jpg)
Figure 7. A thermoset resin production cure cycle in which hydraulic pressure is induced in the resin to reduce gas bubble nucleation in the cured matrix
Product Development
Viscosity profiles are used in thermoset product development for instance in the following:
- fiber types, weaves and finishes
- novel or distinct resin formulations
- materials from alternative suppliers
- functional additives
In Figure 8, it is shown how the viscosity profile is capable of evaluating during cure, at a standard screw barrel temperature the advantage of adding 1% zinc stearate to a phenolic injection molding compound. The zinc stearate brought down the viscosity significantly without influencing the curing time.
.jpg)
Figure 8. The addition of zinc stearate lowers resin viscosity at the injection mold barrel temperature without affecting the cure time
Process Development and Control
Developing Production Cure Cycles
A dynamic mechanical viscosity profile offers the rheological data required for developing a production cure cycle. A typical cure cycle created for a graphite/epoxy laminate is shown in Figure 9.
.jpg)
Figure 9. A graphite-epoxy production cure cycle
In most cases, particularly with bismaleimides and polyimides, there is a need for a post-cure step. The laminate is heated for an extended time exterior to the mold to improve the crosslink density and increase the glass transition temperature of the matrix, hence enhancing functional properties. Figure 10 shows a typical post-cure cycle in a circulating air oven for a polyimide resin composite used for a jet engine part.
.jpg)
Figure 10. The cure and post-cure cycles for a polyimide resin
Quality Control
The most crucial element in thermoset processing is the cure stage. Therefore, maintaining stringent quality standards on the incoming materials, particularly the prepreg is critical. Two key concern are the impact of moisture and the degree of resin advancement.
Prepreg Advancement
Prepregs are partly worked on by the supplier to different degrees to create certain characteristics such as tack, stiffness and drape required for specific applications. The reaction advancement degree in the B-staged prepreg is controlled by stoichiometry and storage conditions, along with humidity, duration and temperature.
It is important to store prepregs for only a short duration and then kept in cold and dry conditions. If there is any lapse on the supplier side in quality control, it may cause advancement of the reaction and modify the response of the material in a standard cure cycle. By testing prepreg samples before use, it is possible to find out advancement level differences in order to adjust the cure cycle. Viscosity profiles of an epoxy resin at three distinct levels of minimum viscosity and the reaction rate is shown in Figure 11.
.jpg)
Figure 11. B-stage resin advancement alters the viscosity profile of a curing thermoset resin
Moisture Effects
Moisture adsorption at the time of inaccurate storage of a prepreg may result in quality issues in thermoset processing by modifying reaction kinetics and modifying the prepreg’s viscosity profile. In addition, matrix porosity may occur due to trapped moisture. It is possible to prevent or at least minimize moisture-related cure problems by testing prior to use. Moisture effects can be reversed so the material can be used again by drying prior to curing. The viscosity profiles of a dry epoxy resin and the same resin after storing for an extended period in high humidity is shown in Figure 12.
.jpg)
Figure 12. Viscosity profiles of a dry epoxy resin and the same resin after extended storage in a high humidity
Evaluating Product Performance
The cured resin’s modulus and the glass transition temperature are key factors in thermoset polymer product performance. The dynamic moduli (G’, G” or E’, E”)are directly determined on solid samples with or without fiber reinforcements at a specific frequency as a temperature function. Tan δ is automatically determined from these measurements. The glass transition is determined as a sudden and significant decrease in the storage modulus and an attendant peak in the tan δ curve. The temperature at which this transition takes place is denoted by the symbol Tg.
The Solids Analyzer measured the tan δ and storage modulus curves, the glass transition and secondary transition of an epoxy- graphite sample measured in bending. These curves are shown in Figure 13. The glass transition temperature does not remain constant, so one must be careful during the measurement to prevent misleading data.
.jpg)
Figure 13. Temperature sweep on a cured epoxy-graphite composite. The glass transition is manifested in a sudden and considerable decrease in the storage modulus with an attendant peak in the tan d curve
Tests can also be performed in bending or compression. For doing valid comparisons, the glass transition temperature must be approached from the same direction to prevent hysteresis during the test. Hence, data from test samples must be compared to data from tests performed under the same conditions, including oscillation frequency on high-performance control samples.
Figure 15 shows the impact on the glass transition temperature of advancing from low to high temperature and then repeating test as the sample cools using cured and a cured plus post-cured sample of PMR-15 polymimide.
Figure 16 shows the impact of a number of different curing agents on the glass transition temperature of an epoxy resin. The data in figures 14 through 16 were acquired in torsion and bending. Figure 15 shows the glass transition temperature as a function of cure level determined in tension as per the procedure explained in ASTM D5026.
.jpg)
Figure 14. Different values of the glass transition temperature are obtained if the transition is approached while the sample is being cooled compared to when the sample is being heated
.jpg)
Figure 15. Temperature sweeps are an effective means for detecting the effects of different curing agents on the viscoelastic properties of thermoset resins
.jpg)
Figure 16. The cure level of a thermoset polymer as a function of cure temperature measured in torsion.
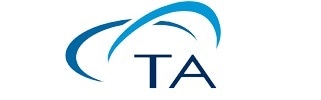
This information has been sourced, reviewed and adapted from materials provided by TA Instruments.
For more information on this source, please visit TA Instruments.