In the foundry industry, where a high level of economic efficiency is required, increasingly stringent quality demands need specific requirements in terms of operational behavior and material characteristics, especially in the case of lightweight alloys and piston alloys fabricated from aluminum-based castings. The hypoeutectic aluminum-silicon alloy is one such aluminum casting alloy consisting of 5-12 wt% silicon.
Excellent mold filling and solidification behavior are the key characteristics of these casting alloys, which are structurally feasible. These net-shaped casting components can be employed to fulfill a number of technical requirements owing to the properties of the cast aluminum alloys. A homogeneous, fine-grained, and defect-free structure with low strength and density even at elevated melting temperatures needs to be created for a realistic stress profile.
In situ observation of phase transitions and solidification processes at defined temperatures is a valuable method to monitor casting and heat treatment processing of alloys. It also helps in gaining insights into structural formation so that predictions about technical casting processes involving different composite alloys can be made. This article discusses the observation of the spatially and temporally resolved melting and cooling behavior of a eutectic Al-Si 12 alloy.
Experimental Hardware Setup
The experimental hardware setup included the following:
The Linkam TS1500 heating stage is ideally suited for the analysis of diverse materials such as metals, polymers, and ceramics under temperature. Samples with a limiting magnitude of a maximum of 6mm in height and 7 mm in diameter are heated to a maximum 1500 °C in the ceramic sample cup. Maximum heating and cooling rates of roughly 200 K/min can be achieved using the T95 controller.
A rotary vane pump is used to operated the heating stage in a vacuum state at 10-3 mbar. Activation can be controlled manually through the T-95 controller or by means of the new ZEISS ZEN 2 core software.
At this point, there are two options available for the user to perform the experiment. A temperature curve for the Linkam stage comprising individually defined temperature ramps coupled to each other can be set up in experiment mode. It is possible to set the rate of heating and cooling, final temperature or the dwell time for every temperature ramp individually.
A condition for when an image must be captured with the microscope can be defined for each temperature ramp. This can either be each time a defined time interval has elapsed or each time the temperature has been changed by a defined value. It is possible to predefine individual blocks using the above parameters that occur sequentially during the experiment.
In manual mode, the Linkam Heating Stage and the ZEISS Axio Imager.Z2m light microscope can be manually controlled using ZEISS ZEN 2 core. This mode provides more flexibility to users in the experimental setup by allowing customization during the experiment. When the elasticity of the sample changes with increasing heating or cooling, the lens focus needs to be monitored and adjusted during the experiment.
Experimental Procedure and Results
Observing the transformation behavior of the Al-Si 12 alloy at the eutectic point of 580 °C during heating and subsequent cooling was the objective of this experiment (Figure 1). An inert gas was purged to bring the entire system to a vacuum state of around 2 x 10-3 mbar.
The "experiment mode" in ZEISS ZEN 2 core was used to perform the experiment and therefore the "heating stage control" control setup determined the holding points, heating rates, and dwell times, including the time intervals between image acquisitions (Figure 2a).
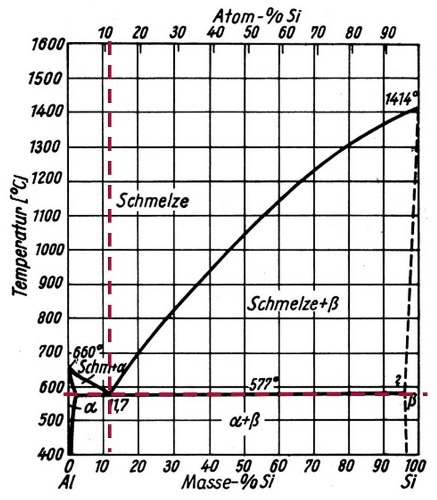
Figure 1. Phase Diagram (temperature in °C on the ordinate and mass-% resp. atom-% on the abscissa) for Aluminum-Silicon eutectic at 11.7 mass-% Si
Figure 2b presents the heat ramp diagram illustrating the heating rates, dwell times, and breakpoints during the experiment. The sample was initially heated up rapidly to 500 °C at a rate of 50 K/min and and then maintained at that temperature for three minutes to allow the sample to settle into this temperature. The process was carried out for one more time with a heating rate of 20 K/min for the actual target temperature in accordance with the phase diagram of 580 °C.
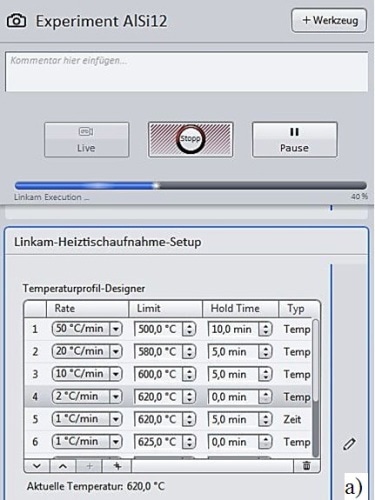
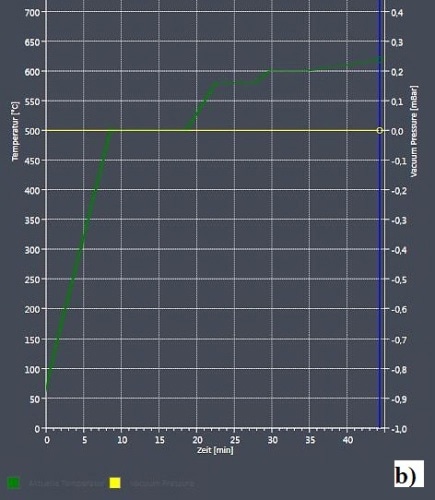
Figure 2. “Linkam experiment mode” in ZEISS ZEN 2 core for the Al-Si 12. Alloy melting investigation. Detailed picture of “heating stage control” setup (a) and heating ramp diagram (b)
Since no conversion reaction manifested itself in the form of a melting process, the sample continued to heat up at a heating rate of 10 or rather 2 K/min and was then held at 610°C and 620°C for two minutes each. At 620 °C, conversion reactions were observed initially. The sample was heated up to 629°C at a rate of 1K/min to add more energy to the melting process and give the conversion more time.
At this point, gradual melting of the aluminum (white phase) took place, dissolving the silicon (dark phase). Coarsening of silicon occurred at the same time because of diffusion processes, followed by dissolution of silicon into the molten metal towards the end of the process. Figure 3 microstructurally depicts the temperature dependence of the melting process.
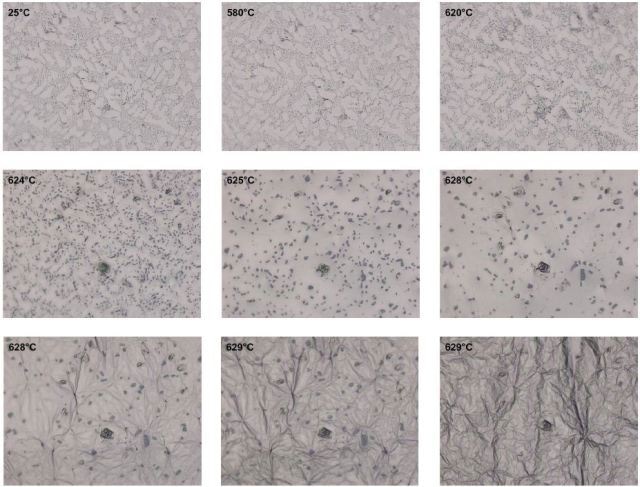
Figure 3. Heating process for an Al-Si 12 alloy to 629 °C
Figure 4 shows the cooling process, which begins at 629 °C and reaches 580 °C with a constant cooling rate of 5K/min. After a dwell time of 6min, a new conversion reaction starts when the silicon predominantly and dendritically precipitates. No further changes in the structure was observed when the sample was further cooled down even more rapid from 580 °C at a rate of 50 K/min.
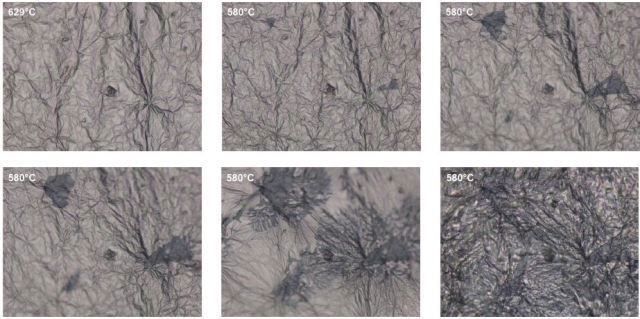
Figure 4. Cool-Down Process for an Al-Si 12 Alloy Starting at 629 °C
It is possible to edit all images captured during the experiment afterwards. Moreover, a video can also be created. It is also possible to save the complete experiment with the entire setup fur subsequent analyses with the same material.
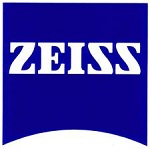
This information has been sourced, reviewed and adapted from materials provided by Carl Zeiss Microscopy GmbH.
For more information on this source, please visit Carl Zeiss Microscopy GmbH.