Matthew Spiret, Metals Market Manager at Instron, talks to AZoMabout the new ISO 6892-1 standard for tensile testing metallic materials at ambient temperatures.
Please could you give us an overview of what ISO 6892-1:2016 is?
Within the metals industry, the two main mechanical testing standards are ISO 6892-1 and ASTM E8. Both used globally, ASTM E8 is predominantly used in the Americas and ISO6892-1 is used in European regions. Asian standard bodies such as JIS and GBT have adopted most of ISO6892-1.
ISO 6892-1 is a very detailed standard for tensile testing metallic materials at ambient temperatures. This standard dictates the results that should be reported, how they should be calculated, what equipment should be used, as well as how to perform the overall test. Anyone doing static testing on metallic materials globally should be aware of ISO6892-1 and will likely be affected by the changes made to the standard.
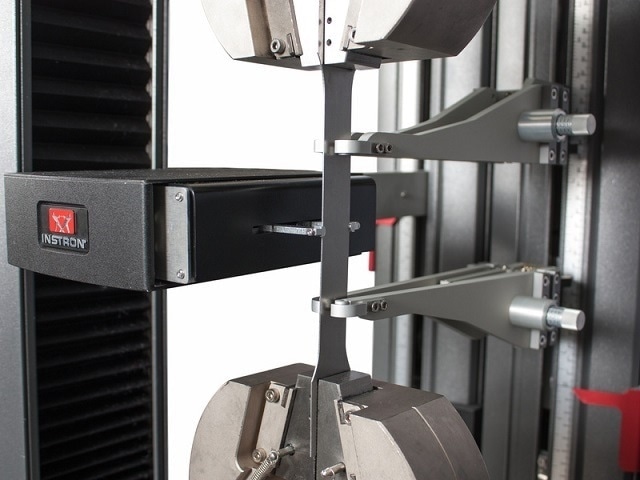
Figure 1. Axial and Transverse Extensometer, capable of Method A1 and determining r-value as per ISO 10113.
Why was ISO 6892-1 replaced and combined with both the previous ISO 6892 and the widely used EN10002-1:2001?
The very early metallic testing standards were produced on a national level, for example British Standard BS18 was first published in 1904. Similarly, DIN and other national standards organisations produced standards for the testing of metallic materials. These standards were developed with the aim to provide a procedure which would be followed by anyone testing metallic materials so results would be comparable. As the world became increasingly globalized, the need to have comparable results across countries became more critical.
EN10002-1 was a widely adopted standard that was developed by multiple national bodies in order to have a consistent test standard across Europe. ISO 6892-1 also existed alongside EN10002-1 but was less commonly adopted. EN10002-1 was predominately written for machines that were manually controlled and reported onto charts with manual calculations.
Using testing machines that were computer controlled posed different challenges, so a European funded project called TENSTAND (So called from TENSsile and STANDard Combined) started to evaluate the differences in material properties as a consequence of different interpretations of the various standards. These differences included, both, the test control, the recording and analysis of the test data. From the work completed on the TENSTAND project, a new version of ISO6892-1 was developed and this superseded EN10002-1 in 2009.
The new version of ISO6892-1 clarified the requirements for test control and introduced a new strain control section (Method A). Method A was based on maintaining a strain rate. The traditional test method from EN10002:2001, based on maintaining a stress rate during the elastic region, became Method B. Despite good intentions the introduction of Method A caused much concern and confusion.
What are the most notably changes in ISO6892-1:2016?
To better clarify the requirements of Method A, ISO 6892-1:2016 now includes two clearly defined approaches, Method A1 (Closed-Loop Strain Control) and Method A2 (Constant Crosshead Separation Rate). Since Method A is the recommended test method, this further clarification will assist test labs that are transitioning from Method B to Method A and monitoring the specimen strain rate. The benefits remain the same: Method A minimizes the variation of the test rates during the moment when strain-rate sensitive parameters are determined and to minimize the measurement uncertainty of the test results.
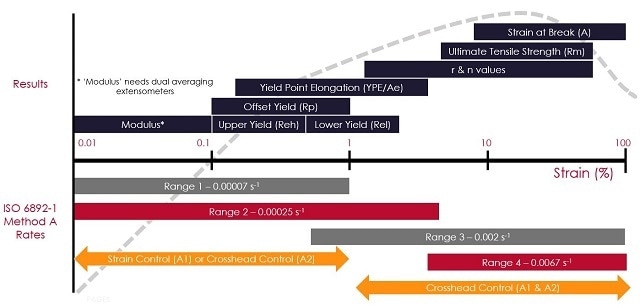
Figure 2. ISO 6892-1:2016 Method A Rates – Expressed graphically in comparison with the required results
How has switching from Method B towards Method A allowed for more comparable results between different sites and different machines?
During a tensile test, there are many sources for uncertainty and error. Many metallic materials are strain rate sensitive; meaning their mechanical properties change depending on the speed of testing. Maintaining the strain rate on the specimen eliminates the effect the machine's stiffness (often called compliance) has on the results.
If you have two testing machines, one very stiff and one compliant (or less stiff), testing nominally the same material, at the same constant crosshead speed the results will be different. To exaggerate this point, if the ‘stiffer’ system was going much faster and the more compliant system tested much slower the results could be more than 10% apart for nominally the same material.
Currently, within Method B the allowable stress rates are from 6-60MPa/s for material with a modulus of elasticity greater than 150GPa (steels for example) and from 2-20MPa/s for material with a modulus of elasticity less than 150GPa (Aluminium for example). The difference between the fastest and slowest rates are 10 times apart.
With Method A, the defined rates have a tolerance of ±20% which is considerably tighter, leading to much more repeatable and reproducible results between different test labs. In the future, Method B may be removed entirely to drive this increase comparability as well as repeatability.
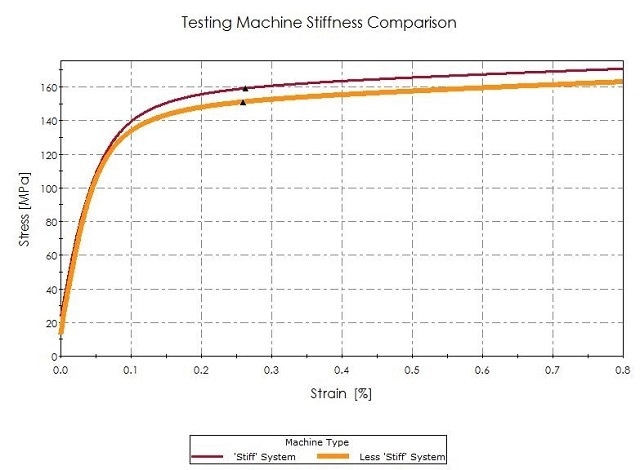
Figure 3. Testing Machine Stiffness Comparison – Two tests are carried out using the same material but on two different machines at the same crosshead speed.
Does using Method A1 in the new ISO 6892-1 standard save time during testing?
Testing using Method A1 can give significant time savings on a system capable of controlling the strain rate through yield on a continuously yielding material. Depending on setup, it could lead to 30% faster test times. Typically for metallic materials, the speed of the testing machine during yield is very slow (<2mm/min), but when in strain control the testing machine can go much faster in the elastic region of the test to account for overall system compliance and then slow down as the specimen starts to yield. For our customers who have implemented Method A1 strain control, they have seen significant improvements in testing throughput as well as a decrease in results variability across machines and laboratories.
Could you please explain Method A1 and Method A2 and when they should be used?
Globally, laboratories testing to ISO6892-1 should start considering switching to either Method A1 or Method A2; as Method A minimizes the variation of test rates during the moment when strain-rate sensitive parameters are determined, leading to better testing practices and more comparability of results.
So when buying new equipment or upgrading existing equipment, ensuring it can achieve Method A1 is important and will provide efficiency increases by controlling the testing machine based on extensometer feedback.
Alternatively, if your current testing machines are not capable of Method A1, using a constant crosshead speed in accordance with Method A2 will still ensure minimum variation of results and increase comparability.
There is also an informative annex (Annex F) in ISO6892-1:2016 which defines a method to determine more accurately the required constant crosshead speed to achieve the required strain rate. Annex F can be complicated to do for each batch of material, to help address this Instron can supply a standard method for Bluehill3® 3 that will automatically calculate the required constant crosshead speed as per Annex F of ISO6892-1:2016.
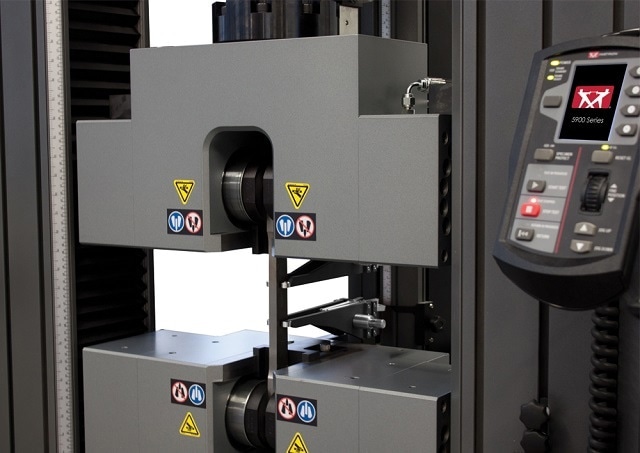
Figure 4. Metal specimen being tested with Durasync® side acting grips, with an AutoX750 Extensometer, capable of performing Method A1
What has been done to make sure Instron testing machines are able to meet the demanding requirements of ISO 6892-1:2016?
When researching new test equipment it is important to review the requirements that you have now as well as those you may have in the future. As a result, you may find that system compliance to Method A1 is important for your laboratory. Instron clearly defines which systems can and can’t achieve these stringent tolerances. Before Method A was introduced in 2009, Instron developed an automatic tuning algorithm in Bluehill® 3 testing software using our advanced 5900 controller, making strain control through yield possible without manual tuning. This means that no user setup is required when switching from different materials or cross sections of specimens.
Are there any areas where you think we will see further development in the near future?
There is continuous work conducted with current standards such as ISO6892-1 and Instron actively participates on all key standards committees, sub committees and working groups. This means that we can always ensure that our products are class leading and we can help to define the future of material testing to make it simpler, smarter and safer for anyone using our machines.
Where can our readers learn more about ISO 6892-1:2016?
There is more information in our complimentary white paper covering the changes found in ISO 6892-1:2016. I would also encourage your readers to sign up for our newsletters that go out frequently with interesting information about all of the industries where Instron machines are used.
About Matthew Spiret
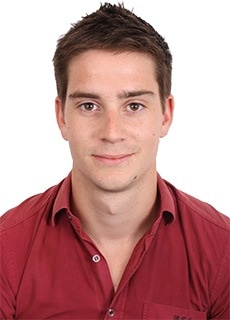
Matthew Spiret is currently the Metals Market Manager for Instron. He provides support and expert advice for Instron’s local representatives and customers globally specifically related to the metals industry.
He is currently an active member for ASTM as well as the British Standards Institute (BSI) ISE101 (Metallic Materials) representing BSI at the ISO meetings reviewing standards such as ISO6892-1:2016.
He holds a degree in Automotive Design Technology from Sheffield Hallam University.
Joining Instron in 2012, he has been focused within the metals industry growing application knowledge that will enable Instron to understand their customers’ requirements and ensure that their products are industry leading.
Disclaimer: The views expressed here are those of the interviewee and do not necessarily represent the views of AZoM.com Limited (T/A) AZoNetwork, the owner and operator of this website. This disclaimer forms part of the Terms and Conditions of use of this website.