General plastics’ polyurethane foam plays a crucial role in ground testing the world's largest solid rocket motor for deep space exploration.
Manufacturers of rocket boosters for NASA’S space launch system establishes protective qualities of GP foam in nozzle closures.
The Application
Headquartered in Dulles, Virginia, Orbital ATK is a worldwide leader in defense and aerospace technologies. The company designs, manufactures, and delivers defense, space, and aviation systems for customers across the globe.
With experience in manufacturing rocket motors for tactical, strategic, and space applications, Orbital ATK is a leading manufacturer of solid rocket propulsion systems. The company’s Propulsion Systems Division has produced rocket motors for NASA’s Space Shuttle solid rocket motor program as well as the Minuteman ICBM system.
Today, it manufacturers the five-segment solid rocket boosters for Space Launch System (SLS) at NASA. These are the largest and most powerful solid-rocket motors ever built for flight. The 322-foot SLS, with NASA’s Orion spacecraft, provides a flexible deep space exploration platform to transport cargo and humans to several destinations around the solar system.
Each Booster measures 177 ft in length and 12 ft in diameter, and includes the five rocket motor segments, an aft exit cone assembly, and thrust vector control. A pair of the boosters combines with four shuttle main engines powering the core stage of a rocket.
NASA’s SLS will generate 8.4 million pounds of total thrust when it blasts off from Kennedy Space Center in Florida. The launch of the first SLS is set to take place in 2018 – a flight referred to as Exploration Mission-1 that will transport an unmanned Orion crew capsule beyond the moon.
The Challenge
It is very important to perform detailed testing of all the components under close-to real-life conditions. On June 28 2016, Orbital ATK and NASA effectively performed the second of two booster qualification motor tests for the Space Launch System in Promontory, Utah.
The aim of this test was to ensure that these solid-propellant boosters were qualified for flight, particularly focusing on the capabilities of the motor at lower temperatures under which the SLS may function.
An environmental barrier was one of the components tested, which seals the aft end of each motor until ignition. The component needs to firmly seal the rocket nozzle openings prior to ignition or use, and then should disintegrate when the rocket motor is fired. The strength of the nozzle plug must be a balance that endures pre-ignition loads. A rocket launch or actual static test is the only option to test the nozzle plug in a real world environment.
According to Reed Hancey in SLS Stage Assembly Design Engineering, there were two main considerations:
- The sensitivity of the energetic materials within the rocket motor dictates an environmental seal, which controls the level of moisture and at the same time ensures that nothing (birds, blown-in dirt, etc.) can get in when the rocket is on the pad awaiting launch.
- While the core vehicle engines come to power, the rocket motor has to be protected. When the core vehicle engines launch, they create debris and hot gas that are likely to enter the rocket motor and result in premature ignition. Additionally, the closure must be able to endure an oscillating load which is caused by sound waves of the ignition environment and air turbulence. This forces the minimum strength of the nozzle plug.
Key requirements:
- Be able to create compound-curved surfaces and extra details
- Precise balance of tensile strength and capability
- Ease in constructing an accurate model for analytical test authentication
- Provision of required foam formulation in required thickness
The Solution
Based on previous successful product experiences, the design engineering team opted to work with General Plastics’ high-density polyurethane foams and used Orbital ATK data sheets to identify materials with the greatest potential for this barrier. They chose different formulations for testing before deciding on the LAST-A-FOAM® FR-4300 foam series, and adding it within the nozzle closures for the solid rocket boosters.
Material Candidates
After initially focusing on foam as the barrier solution, the team examined the foam material from another supplier; however, a suitable material solution was not found.
The LAST-A-FOAM FR-4300 foam series material from General Plastics is a unique, flame-retardant structural polyurethane foam that proved to be a perfect nozzle closure for the solid rocket boosters. The physical properties of the polyurethane foam allow compound-curved surfaces and it had the preferred tensile properties with just the right amount of strength needed for the application.
As foam is a stiff material, Orbital ATK could use an accurate analytical model. The manufacturer already had a test fixture where the static strength can be verified and the plug’s natural frequency can be determined.
The analytical modeling was much simpler, and we had experience from similar nozzle plugs on other programs. So, our confidence in accurately verifying the model with testing is much higher.
Reed Hancey
Additionally, General Plastics was able to trim the uneven billet into the shape required by Orbital ATK, and machined the end shape at the company's facility. While applying coatings, a clean, virgin foam was required. To meet this requirement, General Plastics removed the last bit of material with its own machine process and directly moved into the coating process. The final pieces were integrated into the tested rocket booster.
Test Success
After the booster qualification test, Orbital ATK disassembled the motor to observe how it performed. Together with NASA, Orbital ATK used test measurements to evaluate the various factors and establish the qualification success.
Orbital ATK engineers examined the data obtained from over 500 sensors to determine that whether the 82 unique test objectives were achieved. Due to its effective performance in this test, the LAST-A-FOAM® 4300 foam series material from General Plastics was selected for use on the first flight of the Space Launch System vehicle.
FR-4300 Benefits
The FR-4300 offers the following benefits:
- Non-abrasive
- Bonds easily
- Accepts a range of coatings and adhesives
- Machinable with standard high-speed cutting tools
- Retains chemical and solvent-resistant properties under heat
- Accommodates cost-efficient heat-forming techniques
- Cuts cleanly with water jets and wood-carving tools
Summary of FR-4300 Thermoformable Board Series Products
Product |
Density (lbs./ft3) |
Height (in.) |
Width (in.) |
Length (in.) |
FR-4305 |
5 |
24 |
48 |
120 |
FR-4305 |
5 |
24 |
48 |
96 |
FR-4310 |
10 |
24 |
48 |
96 |
FR-4315 |
15 |
24 |
48 |
96 |
Displayed are maximum standard stock sizes according to density. Custom sizes are available. Cut sizes are available from 0.125” (3.175 mm) up to standard stock heights as listed above.
.jpg)
.jpg)
Image Credit: General Plastics
.jpg)
Image Credit: General Plastics
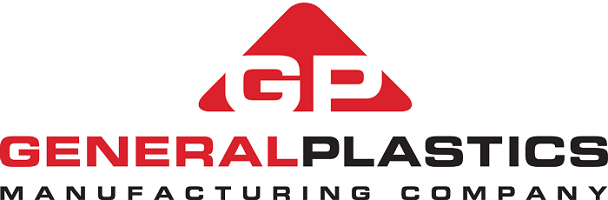
This information has been sourced, reviewed and adapted from materials provided by General Plastics Manufacturing.
For more information on this source, please visit General Plastics Manufacturing.