The purchase of new thermal processing equipment for a company involves planning for several months or even years. Operation of the equipment has been started by executives and pictures have been taken. Now the countdown begins; degradation of the equipment starts immediately once it is installed and turned on. The equipment nears its first failure.
Replacement Part Options
Ultimately, any technical piece of equipment will fail and there will be a need to repair. The same executives who were initially happy now query regarding the non-operation of the equipment and the estimated time for it to be operational again. Pressure starts to mount, and essentially, the repair will involve the replacement of dysfunctional or worn parts. It should be ensured that the thermal equipment operates properly because production and/or research are dependent on it. It is necessary to efficiently and quickly make decisions. Presuming that the company’s technical staff has the training required to diagnose the problem and to recognize the parts that have to be replaced, the next query relates to the place where these parts can be obtained.
.jpg)
Figure 1. Equipment failure timeline.
In a corporate world that includes three bids for every purchase, the actual value is usually lost. Hence, the choice becomes original equipment manufacturer (OEM) parts or other sources. Very often, the aftermarket parts or even direct source parts are selected based on actual purchase price alone. Aftermarket parts are copies that seem to have functionality same as those originally installed. Direct source implies taking an assembled part and approaching the original manufacturer of that specific part. OEM parts are those bought from the OEM and offer a considerably wider value that should be largely taken into account. Prior planning of the purchase strategy before there is a necessity enhances the long-term reliability and cost efficiency. The manufacturer can offer history, updated parts, technical support, as well as a partnership of investment to minimize overall costs. This work is planned to be continued entirely across the width models for maintaining the uniformity.
The Bigger Picture
Diagnosis of the problem and obtaining the replacement part are just the beginning of the repair process. Upon receiving the replacement parts, they have to be installed, integrated, adjusted, and maintained. Very often, a part might be integral to the complete system, hence mandating technical help for accurate installation and commissioning. Apart from having in-depth knowledge of the function of replacement parts, the OEM also understands the proper performance within the system as a whole. Access to original builders, designers, and engineers is usually made possible through the technical support department of the OEM. Quality technical assistance makes installation easier and ensures that the replaced parts function properly upon being used.
Take this instance as an example: A company chooses to buy a less expensive sensor from a source other than the OEM. For some time, the sensor works as expected and all seems to be good; however, deterioration starts immediately and progresses gradually. As time passes and a failure occurs, the sensor is replaced, yet one more immediate failure occurs. The production of this unit is stopped for several days until it was ascertained by those involved that a non-OEM part had been installed. From the time since the installation, the origin of the part had not been taken into account and the staff did not know some of the correct installation techniques. At last, the OEM is called and it is identified that the part is not an OEM-supplied part. A proper replacement is provided, together with technical help, and the equipment could restart and work correctly. Then, the customer is offered a scheme to upgrade the sensor system to latest technology depending on designs instituted by the OEM on prevalent equipment.
When using a single-source OEM supplier, a usage history is developed and maintained. The history is assistive in finding the trends and predicting future preventative maintenance approaches. Furthermore, the OEM uses the historical data to make enhancements to the future components and equipment. Complete data can offer wear predictions and cost analysis, and help in future troubleshooting. Consistent feedback with the OEM will be integrated with their understanding from other users of similar equipment, ensuring higher accuracy. A crucial spare parts approach will ensure that parts are in stock when required, thereby decreasing the downtime and the increase in charges.
Suppliers of aftermarket parts offer less cost based on copying parts already engineered by an OEM. OEMs will consistently enhance the design, perform research, and integrate the better products into new model designs. Very often, an OEM might recommend those modifications to the customer using existing equipment at the time of discussions on replacement parts. The continuity of the replaced parts is maintained if they are purchased from the single OEM supplier. At times, over the service life of the equipment, some parts might be rendered outdated. If this is the case, the manufacturer is well-equipped to suggest a replacement that would be compatible and not damage other system components.
Developing a Partnership
It is very important to develop a partnership between the OEM and the customer. The OEM has added benefits of discussing with suppliers on cost and warranty since they usually buy such parts on a bigger scale than the individual user. Customers should use this advantage to their benefit and have the OEM help with warranty claims. Technicians who are factory-trained usually have highly definitive skill sets to support repairs, and most often, the technician would have carried out the functions during the manufacturing process. This is another point at which a thorough systematic knowledge is highly beneficial. Regrettably, not all manufacturers stay in business. If this is the case, then a similar manufacturer can be contacted; they may be in a position to assist.
Every business constantly looks to increase the bottom line, and reducing the expenditure is one of the most efficient ways of achieving it. Restricted allocation of money for replacement parts and maintenance staff leads to stress for those responsible for ensuring efficient operation of the equipment. All parts start degrading once they are put to use, thereby affecting efficiency. A controlled degradation with planned replacements is best predicted by cooperating with the manufacturer.
.jpg)
Figure 2. The risk of partial or catastrophic failure can be greatly reduced by replacing and repairing at scheduled intervals based on time used or other measurable conditions.
The risk of catastrophic or partial failure can be considerably minimized by repairing and replacing at planned intervals based on the time needed or any other measurable condition. Once analysis and considerable time are put in selecting the manufacturer to invest in to create capital equipment, rewards of that investment can be continuously reaped by purchasing the parts and service from them.
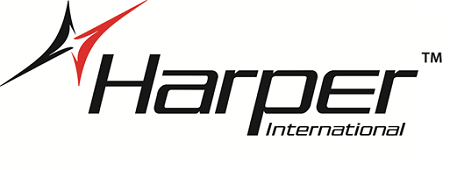
This information has been sourced, reviewed and adapted from materials provided by Harper International.
For more information on this source, please visit Harper International.