Despite the drawbacks of the manufacturing process, the worldwide demands for the CFRP among composite materials would be expected to increase according to a number of independent sources [1,2]. Practically carbon fiber and CFRP share the advantage and disadvantage as nearly all carbon fiber created would be made into carbon fiber-reinforced plastic.
Many industries are unable to adapt carbon composites in their products because of the high cost of the carbon composites. Thus, it is necessary for cost-effective, high-volume carbon fiber manufacturing. This work concentrates on the extending and enhancing the kinetic carbonization model developed earlier [3].
The kinetic model concentrated on the fiber mass loss with temperature and the energy needs to drive this reaction. This reaction model together with residence times, furnace temperature profiles, and heat transfer models are used to calculate the mass loss within the furnace system.
This also predicts the generation of off-gas from the carbonization process. The variations in the off-gas composition as a function of the conversion were not taken into account. The model shown here extends the model to include predictions of the different species of gasses formed at varied fiber temperatures and converges.
Mathematical Models
Harper International has created a continuous model for carbonization process for stabilized PAN including mass loss rate as a lumped kinetic model using pseudo-pure off-gas and two-zone model for fiber [3].
In the earlier model, the off-gas was released from the fiber during the carbonization process, which was assumed as a suitable gas mixture with fixed concentration of each constituent. The company has enhanced its preceding model by adapting more realistic instantaneous off-gas compositions instead of fixed concentration off-gas.
Chemical Composition of the Off-Gas
Harper International chose the recent work done by Pham et al. [7] which was inspired by the work published by Fiedler et al. [8], to deal with the off-gas concentrations as a function of either fiber retention time or temperature [4 ~ 6].
Pham’s recently published work stated that this graphical data was converted into mathematical expressions by polynomial curve fitting. The researchers have supplied all the cumulative emission rates for eight off-gas constituents in Eqs (27)-(34) in their publication.
Rather than directly applying these mathematical expressions into the Harper International model, they assessed the off-gas mole fractions at the specified temperature from cumulative emission rates and adapted these mole fractions as a function of temperature.
This formulation is convenient as the volatile release rate in their model relies on not only the temperature of the fiber but also the mass of volatiles within the fiber. The relationship between cumulative mass/molar emission rates and molar release rate is stated below:
.jpg)
Where, Ni(T) is the amount of moles for i-th species accumulated from To to T, T is temperature, Fi(T) is a molar release rate of i-th species, and mi(T) is the amount of mass for i-th species accumulated from To to T, which are given in the equations (27)-(34) in Pham et al. paper [7], and Mw,i is molecular weight of the i-th species. From these cumulative quantities (i.e., Ni (T) and/or mi(T)), the molar fractions of each species, yi(T), could be derived as the following equation:
.jpg)
Figure 1 represents the cumulative molar fractions, yicum, using the mathematical expressions provided by Pham et al.. A comparison was done between this cumulative molar fraction and the original graphical data from Fiedler et al. Yet, it was found that a direct comparison is impossible. Fiedler’s data was run to 1000 °C, while Pham and co-workers rescaled at the 800 °C. As a result, Fiedler’s data cumulative molar fraction became unity at 1000 °C while Pham reaches unity at 800 °C. Figure 2 shows the Pham’s estimated rates of gas evolution for each species.
.jpg)
Figure 1. Cumulative off-gas mole fractions
Image Credit: Harper
.jpg)
Figure 2. Rate of gas evolution for pyrolyzed PAN
Image Credit: Harper
Within the valid ranges, the predicted evolution rates (Figure 2) of each gaseous species are a smooth function. However, eacpolynomial curve is fitting. Using Equation (2), both molar and mass fractions are derived as a function of temperature and illustrated h start from a non-zero value at the lower range.
This step change on the onset of off-gassing is an imperfection of the in Figure 3. It can also be noted from Figure 3 that the results of the non-continuity of the polynomial fitting show up as step changes in the onset of the released gas molar fraction. An example of this is shown by the discontinuity of the CO molar fraction around 400 °C.
.jpg)
Figure 3. Instantaneous off-gas compositions. (A) molar fractions, and (B) mass fractions
Image Credit: Harper
It is important to calculate the enthalpy of the volatiles with accuracy in order to obtain accurate endothermic reaction energy for the carbonization process. The critical pressure and temperature together with its decreased pressure and temperature (at 1 bar and 300 °C) were evaluated for all off-gas constituents.
From these calculations, the reasonable assumption that inside the LT furnace, the off-gas is in an ideal gas state is verified [9]. Using the Shomate equation, the specific enthalpy of the off-gas was calculated at any given temperature and all the Shomate parameters for each chemical component are taken from the NIST Database [10].
Mass Loss Rate during Carbonization Process
The carbonization process, which involves producing carbon fiber from synthetic precursor polymer, is chemically similar to thermal degradation or pyrolysis of a polymer. The actual process is very intricate and not fully understood. The PAN’s linear structure is converted into a ring structure by the controlled oxidation process.
During carbonization, releases all other groups except carbon-carbon bonds are released by side-group elimination. A single step lumped kinetic model had been developed for carbonization of stabilized precursor by fitting TGA data available in the literature [11]. Among the various potential kinetic expressions for degradation of a polymer, the previously chosen simple power law expression (both 1st order and 2nd order) provided good agreement with the experimental work.
Figure 4 demonstrates the residual fiber mass fraction to its initial mass with two experimental data sets: 1. the original data used for fitting (Modified from Xu et al.) and 2. additional data from Fiedler et al.. From the figure, it can be observed that both independent experimental data shows relatively similar trends, but the amount of the released volatile is always greater in the Fiedler’s fiber case at any given temperature. The volumetric mass loss rate for the fiber is given below:
.jpg)
where V is volume of specimen in a closed system, EA is activation energy, A is pre-exponent factor, and R is gas constant.
.jpg)
Figure 4. Residual fiber mass fraction during carbonization: experimental data and fitting
Image Credit: Harper
Zone Model for Fiber
In contrast to gaseous phase, the fiber’s physical properties are more complex since they are based on not only temperature but also conversion. Additionally, carbonization might be a constant series of chemical reactions instead of clearly distinct single process. A two-discretized-zone model has been created to simplify things and an illustrative conceptual depiction of this model is illustrated in Figure 5.
.jpg)
Figure 5. Schematics of discretized 2-zome model for carbonization process
Image Credit: Harper
In this 2-zone model, the physical property at any extent of carbonization is expressed using two pure states of fibers such as stabilized PAN fiber (white region in Figure 5) and carbonized fiber (black region in Figure 5) and its mathematical expression is given as follows:
.jpg)
where a is conversion defined below in equation 5. Yi is mass fraction of i-th component, and φI and φS represent any specific physical properties for intermediate fiber and stabilized PAN fiber, respectively.
.jpg)
During the carbonization process, mass fraction and linear density, , are also changing. Shown below are the relationships of conversion to these properties:
.jpg)
where m is mass of fiber, subscript f represents final state, and subscript o denotes initial state.
Although it is a simplified model, it is still difficult to assess physical properties with this model because their properties at a homogeneous state are not fully known. It is believed that the product fiber from the LT furnace is similar in composition to carbon fiber, as the mass loss from successor devices (HT furnace) is relatively lower. Moreover, carbon fiber composition is assumed as solid graphite despite the impurity of the carbon fiber (maximum 5% of non-carbon atom typically N and small amount of H).
.jpg)
It is quite hard to assess the thermodynamic state for Stabilized PAN fiber. The oxidation extent might be a multifaceted function of the following factors, residence time, heating rates, applied tension, co-monomer, and temperature during the oxidation process. The thermodynamic state might be non-identical because of different molecular structures.
Mass and Energy Balances
To assess the changes in fiber phase, control volume is concentrated on conversion of the solid fiber.
.jpg)
where is fiber mass rate, z is fiber moving direction coordinate, m” is mass transfer flux from solid to gas, Lp is perimeter, Ac is cross-sectional area, rm, loss is mass loss rate per volume.
The fiber temperature variation along the length of the system can be acquired from taking appropriate energy balance. This results in the basic differential equation presented in Equation 11. This equation reveals the fiber energy balance with sensible heat effect, enthalpy variation for evolved gas, and heat transfer with surroundings.
.jpg)
where T is temperature of the fiber, is enthalpy change per unit mass of gaseous matter released, qs is heat flux at the fiber surface, Lp is perimeter, and Cp signifies heat capacity of fiber. Mass and energy balances are closely connected to each other and therefore they need to be solved at the same time.
Results
Numerical simulation of the process was achieved by solving the systems of non-linear ordinary differential equations provided in equations (10) and (11) with kinetic expression (3). The fourth order RK technique is applied with step size of 0.001 for dimensionless length scale. All the parameters and physical properties, which have been developed to be dependent on either conversion or temperature, are assessed with the fourth order RK technique.
A baseline case was picked signifying realistic operating conditions of a current industrial scale system. The length of the carbonization furnace was given as 14 m with 7 equally divided autonomous heating zones and a linear fiber process speed of 10 m/minute. Therefore, the fiber residence time is 1.4 minute (84 seconds). Harper International model has been created as a longitudinal 1D (fiber moving direction) model.
Both height and width of the furnace are arbitrary, and the cross-section could be a random shape. However, all the operational and geometrical conditions were considered as contemporary industrial carbon fiber manufacturing condition.
Baseline Result
For the baseline case, the precursor fiber was chosen as 24k filaments with 1.15 dTex. Nevertheless, it needs to inform that the dTex is for fresh feedstock, and not an inlet condition for carbonization furnace which is oxidized within oxidation/stabilization ovens. It is stated that oxidized precursor could have either heavier or lighter linear density based on a number of aspects such as additives, co-monomers, and operating conditions of oxidation oven.
Here, it was assumed that the oxidation process includes slight linear density decrease (5% mass loss). With this condition, the results of the baseline are represented in Figure 6 ~ Figure 9.
.jpg)
Figure 6. Fiber conversion over the fiber travel direction for baseline case
Image Credit: Harper
.jpg)
Figure 7. Normalized local volatile release rate
Image Credit: Harper
The conversion plot of fiber as shown in Figure 6 has an inflection point: convex in the first half and concave in the later part. In the Harper International model, the volatile release rate is ruled by both temperature and volatiles mass within the fiber. Therefore, the local volatile release rate seems to have numerous peaks (Figure 7) but basically it has a maximum point in the middle and starts to descend after the maximum point.
From these inspections of conversion and local release rate, the carbonization process could be illustrated as composed of three unique sections: 1. Slow start section, 2. Actively converting section, and 3. Asymptotic approach section.
In the slow start section, off-gas release rate is small because of the low temperature, although there is a high content of volatiles in the fiber. Conversely, the release rate is slow in the asymptotic approach section due to the low content of volatiles. The fiber temperature profile (Figure 8) illustrates nearly linear increase with tiny variation even when the heat source temperature boundary condition has step changes.
The fiber’s temperature is established as a result of the local heat balance: 1. Heat transfer from the heat source and 2. The endothermic heat of reaction as energy consumption as well as the sensible heat required. Since heat transfer is greater compared to heat of the reaction, the fiber temperature is constantly increasing except the last zone where the temperature of the zone decreases. These two balancing effects are portrayed in Figure 9.
In this local heat effect figure, the energy supply from heat transfer reveals numerous peaks. In this model, the key heat transfer mode is thermal radiation between the furnace muffle wall and fiber. As the fiber enters new zone, the temperature variance between the wall and fiber is at the highest so it has the maximum heat transfer rate. This is a bit impractical as temperature does not have step changes, but roll-off between the zones and a more slow transition.
The resulting transferred energy is at all times greater than the consumption by endothermic reaction, and results in the fiber increasing in temperature. In this baseline case, heat transfer between the fiber and surrounding gas (mixture of nitrogen, sweep gas, and off-gas released from the fiber) is not taken into account.
.jpg)
Figure 8. Fiber temperature (blue) and furnace temperature (red) along with length of the furnace
Image Credit: Harper
.jpg)
Figure 9. Local heat effect on the fiber
Image Credit: Harper
What-If Scenarios
Different Filament Count Fiber Tows
Variations were made to the filament count in the fiber to observe the sensitivity of the temperature and conversion to the number of filaments. Figure 10 illustrates each conversion profile for 12 k, 24 k (baseline), and 50 k fibers. For lighter tow (12 k), the final conversion is higher, whereas for the heavy tow (50 k), final conversion is less than the baseline case (24 k). The final exit conversion window is about 88% ~ 95%.
Although the temperature profiles exhibit analogous trends with the baseline case, they exhibit different slopes. In general, more time is needed for the completion of the reaction as more mass has been introduced. Figure 10 (C) depicts normalized local off-gas release rates.
The results seem to be quite similar to normalizing with feed rates; however, cumulative off-gas flow rates depicted in Figure 10 (D) reveal completely different off-gas flow rates for different fiber tow count. As a result, more off-gas has to be vented from the furnace muffle during the heavy tow operation. Inefficient removal of this off-gas could lead to hindrances in the furnace operation and also non-uniform quality of the end product.
.jpg)
Figure 10. Results for different filament count. (A) Conversions, (B) Temperature, (C) Local off-gas release rates, and (D) Cumulative off-gas flow rates
Image Credit: Harper
Hindered Heat Transfer
Heat transfer by surrounding gas is the next ‘what if’ scenario. The surrounding gas, blend of sweep gas and volatiles, is not added in this model. It might require a CFD simulation to completely understand flow dead-zone, flow pattern, and local heat transfer effect relating to surrounding gas.
In this basic ‘what if’ scenario, simple hindered heat transfer because of the surrounding gas is assumed. The first case is the convective cooling, and gas temperature is assumed as always 100 °C lower than the fiber temperature and 10 W/m²K of convective heat transfer coefficient between fiber and surrounding gas. With this condition, results are shown in Figure 11. Analyzing the fiber temperature and conversion, the effect of this scenario is a small impact on each.
.jpg)
Figure 11. Results for different heat transfer cases. (A) Conversions, (B) Temperature, (C) Local off-gas release rates, and (D) Cumulative off-gas flow rates
Image Credit: Harper
Unintentional Power Loss
The last but not least ‘what if’ an unexpected power loss occurs in a specific zone. It could either be a heating element failure or something else, but consider the case where temperature of one zone is unexpectedly down. Two cases are considered here: 1. Zone 3 temperature reduces to 300 °C, and 2. Zone 5 temperature decreases to 300 °C. Figure 12 depicts the results. As it can be observed in the temperature profiles, there is a negligible final exiting temperature difference although huge temperature deficit in the middle of zone when compared with the baseline case.
Conversely, non-negligible discrepancy is found on the final conversions. Its final exit conversion window is 88% ~ 93%. Figure 12 (B) shows that the fiber temperature is nearly recovered at the next downstream zone from the problematic zone.
In addition, in this zone, off-gas release shows a stiff increase to catch up the impeded conversion owing to decreased temperature zone; however, the retarded fiber conversion because of unintentional power loss could not catch up on the baseline conversion. Although it is not shown here, there is an increased power requirement in the downstream zone to offset the lower temperature zone.
.jpg)
Figure 12. Results for unintentional power down cases. (A) Conversions, (B) Temperature, (C) Local off-gas release rates, and (D) Cumulative off-gas flow rates.
Image Credit: Harper
Conclusions
Harper International has created a continuous model for carbonization process for stabilized PAN that comprises of mass loss rate as a lumped kinetic employing temperature dependent off-gas and a two-zone model for fiber conversion. In this two-zone model for fiber, it was supposed that carbonization takes place from the outer region and enters into the center.
From the baseline result with accurate operating conditions, the results of the fiber conversion profile can be explained in three sections (active, slow, and asymptotic), while fiber temperature has a roughly linear response with small disparities. Harper International has conducted three different what-if situations: 1. Different filament counts (12k, 24k, and 50k), 2. Possible hindered heat transfer because of off-gas, and 3.Inadvertent power loss cases.
The conversion results from the what-if cases were inside a narrow range as the result of the baseline case at the end of the furnace system was in the asymptotic conversion region. This region is not that sensitive because of the low volatile mass faction.
However, exit fiber conversion differs 7%, 3%, and 5%, respectively. Within the what-if study settings, the sensitivity toward conversion from greatest to least is filament count, power loss, and off-gas cooling effect. Since the end conversion is influenced by the filament count (which results in a greater mass rate), the ensuing fiber may have different properties while processed under the same operational settings.
The fiber cooling because of off-gas scenario caused the smallest change in the fiber conversion compared to the baseline case. The off-gas cooling affect was a little arbitrary and was not based on the flow dynamics within the carbonization furnace system. Integrating the mass flow rates, velocities, and locally-derived heat transfer coefficients would better predict the impact of the off-gas and nitrogen cover gas. The final scenario considered was the varied operating temperature profile case because of inadvertent power loss. This scenario concluded that the final conversion of the fiber would rely on the fiber temperature history even though the final fiber temperature may be closely identical.
This kind of analysis even with simplification would trigger and encourage the development of kinetic expression with additional data and enhance design and performance of industrial furnace. Further research for in-depth analysis is needed to examine the interaction with fiber and gaseous phase, radial variations within the fiber tow, and variation along the width of the furnace which would influence the system consistency.
Acknowledgments
Our most sincere gratitude goes to Dr. Srdjan Simunovic (Distinguished Research Staff, Computer Science and Mathematics Division, Oak Ridge National Laboratory) for his fruitful advice during debugging the computer code to solve the system of ODEs.
References
1. Holmes, M. “Global carbon fibre market remains on upward trend” Reinforced Plastics 58 (2014) 38-45
2. Das, S., Warren, J. West., D. and Schexnayder, S.M. “Global Carbon Fiber Composites Supply Chain Compet-itiveness Analysis” Technical Report ORNL/SR-2016/100 NREL/TP-6A50-66071 (2016)
3. Lee, T.-S., Witting, P. R. “Kinetic Model of Stabilized PAN Fiber Mass Loss During Carbonization” SAMPE 2017 Conference Proceeding
4. Morgan, P. Carbon Fibers and Their Composites. Boca Ration, FL: CRC Press, 2005
5. Chung, D. D. L. Carbon Fiber Composites. Boston, MA: Butterworth-Heinemann, 1994
6. Rahaman, M.S.A, Ismail, A.F., and Mustafa, A. “A review of heat treatment on polyacrylonitrile fiber” Polymer Degradation and Stability 92 (2007) 1421-1432
7. Pham, H. H., Lim, Y.-I., Cho, C.-H., and Bang, Y.-H. “Hydrodynamics of low temperature carbonization furnace for production of polyacrylonitrile (PAN)-based carbon fiber” Chemical engineering Research and Design 128 (2017) 192-204
8. Fiedler, A., Fitzer, E., Rozpłoch, F. “PAN Pyrolysis Studied by Gas- and ESR-Analyses” Carbon 11 (1973) 426-428
9. Lee, T.-S., Witting, P. “Computational fluid dynamics (CFD) analysis for off-gas mixing and ventilation inside carbonization furnace during PAN-based carbon fiber manufacturing” SAMPE 2016 Conference Proceeding
10. Linstrom, P.J. and Mallard, W.G., Eds., NIST Chemistry WebBook, NIST Standard Reference Database Number 69, National Institute of Standards and Technology, Gaithersburg MD, 20899, doi:10.18434/T4D303
11. Xu, B., Wu, F., Cao, G.-P., and Yang, Y.-S. “Effect of carbonization temperature on microstructure of PAN-based activated carbon fibers prepared by CO2 activation” New Carbon Materials 21 (2006) 1-5
12. Pyda, M. “Polyacrylonitrile (PAN) Heat Capacity, Enthalpy, Entropy, Gibbs Energy: Datasheet from “from "The Advanced THermal Analysis System (ATHAS) Databank – Polymer Thermodynamics" Release 2014 in SpringerMaterials” (http://materials.springer.com/polymerthermodynamics/docs/athas_0001), Springer-Verlag Berlin Heidelberg & Marek Pyda, 2014
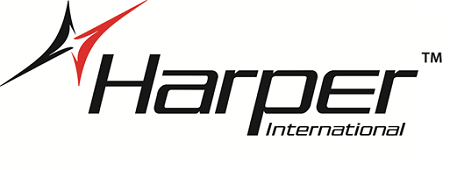
This information has been sourced, reviewed and adapted from materials provided by Harper International.
For more information on this source, please visit Harper International.