Tooling, in manufacturing, can be defined as the process of designing and engineering the tools essential for producing the components or parts needed to form the final product. It can include cutting tools such as grinding and milling machines; work-holding tools such as fixtures or jigs; molds, dies, and patterns for plastics and sheet metals; and welding and inspection fixtures. There is an unlimited number of approaches for tool development and many materials, ranging from hard metals to composites that can be used to produce these tools.
.jpg)
Image Credit: General Plastics
Tooling is a core technology used in virtually all major markets — from electronics to transportation to food processing — and is frequently a standard part of the design and production process. With so many other aspects to look into, it is easy to fall back on the default traditional tooling approaches. But for many companies, shifting to an alternate tooling material or using a new method for designing and developing tooling, could help to deliver that bullet-proof design in a more efficient way, saving time as well as money.
Across industries, plenty of manufacturers are trying out composite, or “soft” tooling techniques using materials such as polyurethane foam. While this may not be the right choice for all applications and tooling requirements, there are several instances where using polyurethane foam either as the final tool or to help in making the final hard tool can help you to lower cost, iterate faster, or create a more accurate tool.
This article explores the main considerations to evaluate your tooling requirements and how to make the most of the tooling strategies and methods using polyurethane foam.
High Cost of Small Mistakes
Tooling is an important part of the manufacturing process. Using inferior quality tooling will mostly result in substandard components being built that are susceptible to malfunction, fail under stress, or be unable to meet project specifications or requirements. This can cause huge quantities of parts to be wasted or even require you to start production from scratch.
The quality of the finished part, its properties, the accuracy and speed with which the part can be made, and repeatability in high-volume operations all rely on the precision and features of the tooling. Using the right process and correct material to develop those tools is vital to guarantee properly functioning parts. In brief, to develop the best product, you must design the best tools, engineered to the maximum quality, for the task.
Top Considerations for Designing the Right Tooling
There are a number of considerations when choosing the right tooling for a specific application. The following are some of the most critical questions a manufacturer needs to ask:
- How will the tool be used and what performance requirements are needed for that use?
- What material will ideally suit those requirements?
- What are the curing conditions?
- What is your production rate?
- What are your tolerance levels?
- What are the dimensions of the finished tool?
- How many times does the tool need to perform its task?
- What contours and incorporated functions does the product have?
- What will be the time taken from prototyping to production?
- What is the required surface finish?
- What is the allocated budget?
In the end, choosing the appropriate technique depends on how you plan to use the tool and achieve a perfect (or near perfect) match of coefficient of thermal expansion (CTE), production rate and curing conditions, tolerance levels and surface finish, and dimensional complexity, among others. The answers to these questions will lead one to the correct process for discovering this match and engineering the correct tooling that will result in the production of superior quality, suitably functioning parts.
Tooling Technique: Hard Tooling vs. Soft Tooling
There are two basic types of tooling — hard tooling and soft tooling. Hard tooling mostly uses metallic materials such as aluminum, steel, or metal alloys like Invar; while soft tooling materials are usually composite materials such as high-density foam, machinable epoxy boards, fiberglass, or wood/plaster models.
.png)
High-density tooling foam (left) and Polished graphite Hexcell Corporation HexTool® (right). Image Credit: General Plastics
Traditionally, hard tooling has been the reliable standard in the manufacturing sector. It is durable, delivers good surface finish, and stands up to a lot of pulls for high-production operations (for example up to 1,500 autoclave cycles for steel tools). Furthermore, metals commonly have low CTEs, which work well when developing components that also have a low CTE, demanding tolerances, or require repeated high-temperature cycling.
The CTE measures the fractional variation in size per degree change in temperature at a constant pressure.
When the CTE values of the tooling and production materials are matched, the materials will expand and contract at the same rates when dealing with diverse curing temperatures — resulting in high-quality parts possessing precise dimensional tolerances. Just like a hard tooling technique is a better selection when making components with low CTE, soft tooling options are mostly a better choice when producing composite parts to decrease CTE mismatch and maintain dimensional accuracy while curing. Shown below are the CTEs of standard tooling materials.
.jpg)
Relative CTEs of Common Tool Materials. Image Credit: SME.org
In contrast to hard tooling, soft tooling is faster and easier to machine into complex shapes and can rapidly be modified as needed or reworked. Moreover, the soft tooling raw material, as well as the process of machining it, offers the advantage of a lower price tag, and is easier to move about with its lighter weight.
These advantages are why several manufacturers are shifting to lighter-weight soft tooling for prototyping and other time-bound projects, producing tools with complex or large designs, production runs with low-part volumes, or when economical solutions are necessary.
Polyurethane Foam: A Versatile Choice Among Soft Tooling Options
Although a wide range of materials can be used for soft tooling, polyurethane foam tooling boards (also called high-density urethane or HDU), such as General Plastics LAST-A-FOAM®, is an ingenious option. LAST-A-FOAM® tooling boards are a sought-out replacement for large-sized tools in which material, handling, processing, and shipping costs of metal are a problem, or in limited-run tooling in which metal tools are cost-prohibitive. These tooling boards are best-suited as master models and composite tooling in applications such as low-temperature layups to high-temperature autoclaves.
In addition, with programs that have limited turnaround times, foam tooling can considerably cut down on the R&D cycles and help the product in hitting the market faster. Three applications in which LAST-A-FOAM® polyurethane foam is the perfect option have been discussed below.
Foam Master Molds
It is usually difficult to develop tooling that can fulfill tight tolerances but still endure high temperatures and repeated curing cycles. Although the potential to easily control and shape polyurethane foam renders it highly suitable for creating a tool that has unique shapes or tight tolerances, it cannot endure repeated curing cycles or high temperatures that can be withstood by a composite or metallic tool. However, LAST-A-FOAM® high-temperature tooling boards have demonstrated their value as a master mold owing to their potential to endure high-heat prepreg and autoclave curing. It serves as an exceptional substrate due to its high compressive modulus, high glass transition temperature (Tg), and predictable CTE.
These tooling boards are economical and can be molded into complex shapes and machined to a tight tolerance. If changes are required on the master tool, the material can be easily altered and reused at a fraction of the cost of metal tooling. An example of the steps for developing a master mold with the help of LAST-A-FOAM® is illustrated below.
.jpg)
An example of using LAST-A-FOAM® as a master mold to create a composite HexTool®. Image Credit: General Plastics
Prototyping
While developing new parts, in general, companies go through a number of iterations to make sure that they perform as intended. Hence, it is highly important to select tooling materials that are cost-efficient and easy to modify, thereby enabling a range of design modifications while fulfilling project timelines and budgets.
Apart from being highly stable and precise, LAST-A-FOAM® is a cost-efficient material that provides the flexibility to cut and re-cut while making product iterations. For instance, in the aerospace industry, in new or experimental programs that typically involve various design iterations upfront, the use of LAST-A-FOAM® is highly advantageous since it is possible to rapidly iterate prototypes in a budget-conscious manner. It can be also applied in the transportation industry, with almost all major automotive companies using LAST-A-FOAM® for their prototyping work.
.jpg)
Students at the University of Utah used LAST-A-FOAM® to build a mold for the carbon fiber outer shell of their formula SAE racecar. Image Credit: General Plastics
Although the choice of a low-cost and less permanent material is an option, it should never be the only consideration. It is always best to abstain from materials that might deform or soften in applications where the temperature stability of the material at higher temperatures is significant. This will lead to wide differences in tolerance and production of parts with irregular dimensions.
Surface Verification Tool
Another soft tooling application is the use of the polyurethane foam as a surface verification tool. Prior to the start of the time-consuming process of machining hard tooling and cutting a costly piece of metal, it is advisable to use a low-cost surface verification tool to make sure that the tool path is accurate. The potential to easily machine and cut LAST-A-FOAM® renders it best suited for surface verification.
Layup Molds and Mandrels
In order to develop layup molds and mandrels, the LAST-A-FOAM® tooling board series is an excellent choice due to the cell structure and dimensional stability of the foam and the potential to easily machine it. Due to the fact that the majority of layup mold and mandrel applications have ambient or low-temperature cures, tight tolerances, and a low number of pulls, LAST-A-FOAM® is an advantageous material for these applications.
For instance, LAST-A-FOAM® is used by leading marine manufacturers due to its ability to easily and securely bond to fiberglass laminating resin systems. The grain-free, tough tooling board has an exceptional bonding ability that enables manufacturers to develop the oversized blocks required for molds for large hulls.
Furthermore, used by aircraft and wind turbine manufacturers, LAST-A-FOAM® aided in creating tools to develop spars that run the length of the wing of a wind turbine or an airplane to prevent it from buckling under stress. LAST-A-FOAM® is the perfect choice for developing these spars since it enables their complex hollow tube shape to be easily accommodated.
To manufacture the spars, first, a polyurethane foam mold is developed, and then, the carbon fiber is placed on the tool and cured. Subsequently, extraction of the foam discloses the layup tool used for developing the spars. Then, a resin is added, the tool is vacuum-bagged, and is then cured, in general at room temperature, before demolding and extracting the finished part.
Case Study: How Tooling Using LAST-A-FOAM® Helped Accelerate Aerospace R&D Cycles
BLR Aerospace specializes in developing aerodynamic performance enhancements and exterior modifications for turbine-powered aircraft and helicopters. For rapid and profitable development of innovative aerodynamic cowlings, the company was in search of a stable, easily machined tooling material for prototyping composite parts — particularly large-scale, life-sized carbon fiber and fiberglass parts. Earlier, the metallic tools were used by the company, which were expensive to produce and time-consuming. The company’s design engineers were looking for an affordable substitute for a more permanent tooling to allow for different design iterations, while also taking into account time and cost requirements.
.jpg)
An example of a BLR aircraft in flight. Image Credit: General Plastics
BLR tried out other tooling materials and selected General Plastics’ LAST-A-FOAM® FR-4700 High-Temperature Tooling series due to its uniformity, temperature stability, and exceptional machinability.
Machining tools using this foam allows us to lay up the carbon-fiber and composite parts, put them in the oven and make true-to-life prototypes using the actual materials that we’ll use in production.
Russell Bezzo, lead project engineer, BLR Aerospace
In addition, the tools with lower weight were less cumbersome to handle while developing prototypes and could be shipped to their composite manufacturing facilities at low cost.
BLR Aerospace also made the most of the CNC machining capabilities and expertise of General Plastics to develop its prototype tools, which made the tooling process simple and the process rapid. On the whole, depending on General Plastics for its high-temperature tooling foam as well as its CNC machining capabilities enabled BLR to accomplish shorter R&D cycles, tighter tolerances, and increased cost-effectiveness and faster design iterations.
Benefits of LAST-A-FOAM®
The choice of tooling material can have an impact on the design and quality of the product, production costs, and on-time completion of the project. In the search for a cost-efficient and rapid time-to-market option for a limited run tooling, LAST-A-FOAM® could be the ideal choice. LAST-A-FOAM® comes in a range of densities that endure a broad range of temperatures of up to 400 °F.
It can be easily machined into complex shapes with minute details and can be altered by just bonding on extra foam with adhesive, filling voids, or carving off any excess. In general, lead times are shorter as the machining process is more rapid and the material is readily available. Moreover, LAST-A-FOAM® is lightweight and considerably easier to handle, specifically for large parts that have to be maneuvered over a factory floor.
Its low CTE and high Tg make it ideal for use in vacuum-forming applications; however, other urethane products may deform or soften. It has an exceptional bonding potential to develop monolithic tools and molds for large-scale projects and is uniform from sheet to sheet, non-abrasive, and grain-free to ensure fine surface finishes with nearly any coating system.
Depending on its low weight, material characteristics, and ease of accommodating complex shapes, LAST-A-FOAM® could possibly be used as a viable substitute to conventional metallic tools, saving time and cost on the subsequent tooling project.
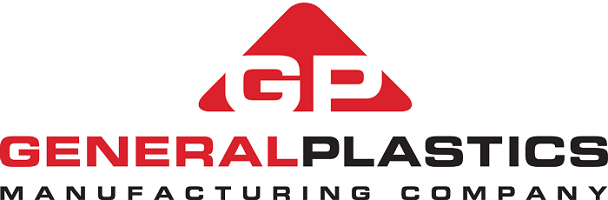
This information has been sourced, reviewed and adapted from materials provided by General Plastics Manufacturing.
For more information on this source, please visit General Plastics Manufacturing.