Although oil analysis was initially used for engines as a predictive maintenance tool, it is still a widely used method for guaranteeing the reliability of engine systems. Majority of the mobile equipment across the globe, such as locomotives, cars, mining equipment, trucks, agricultural equipment, buses, and also oil and gas exploration rigs, stationary backup power generators, and pipeline compression stations are powered by reciprocating internal combustion engines.
Ask the Expert: Engine Oil Analysis
It is necessary to change engine oil before it loses its ability to sufficiently perform its intended functions within an engine. In contrast, early or frequent changing of oil could result in a huge cost and environmental impact. In rotating internal combustion engines (RICE), the oil becomes gradually contaminated, the rate of which can differ according to age, load factor, environment, duty cycle, and fuel types. In general, engine oils include additive packages formed of alkaline components and detergents to neutralize acids formed due to the combustion of fuel. The depletion of additives will be to the point that the additive and oil combination cannot adequately protect the engine. Usually, it is significant to know the type of contaminant in the oil since it provides symptoms of the engine condition to allow a more direct remedy to take corrective action. For example, high levels of glycol contamination suggest a leak in the cooling system.
Oil analysis offers information related to the extent of this contamination and associated oil degradation status, so that changes in oil occur according to condition, not time. However, what is the reason for contamination of engine oil?
Most Common Contaminants
During normal operation of an engine, a broad range of contaminants is introduced to the lubricating oil. Some of the most common contaminants are given below.
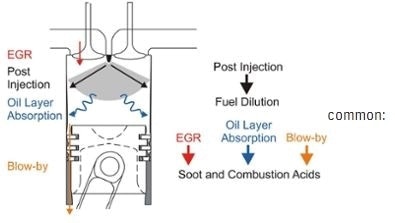
Combustion By-Products
Exhaust gases - or blowby gases - that leak past the valve guides, piston rings, and turbocharger seals into the crankcase contain particles of acids, carbon, partially burned fuels, water, lacquers, and varnish that contaminate the oil. Sulfur oxides (SOx) are common gases with sulfurous fuels (liquid fuel distillates, diesel, heavy fuel oil). Nitrous oxides (NOx) are more pronounced with natural gas (LNG, CNG, propane) fueled engines. Hydrocarbon oxidation (HCOx) will exist in differing amounts.
Acids, Varnish, and Sludge
When the lubricating oil comes into contact with hot engine components, or if heated oil contacts the entrapped air, oxidation and decomposition take place, forming contaminants such as acids, sludge and varnish.
Fuel
In general, these contaminants are related to engine malfunction. However, fuel dilution of the oil can also be brought about by stop-and-go operation and excessive engine idling and results in viscosity loss, leading to severe wear and probable seizure if left ungoverned. Clogged air filters, faulty injectors, and fuel pump failure are the most common reasons for fuel dilution; however, in some cases, rupture of fuel lines could lead to contamination of oil.
Water
Water vapor reaches the oil as a combustion byproduct. Low load engines and backup generators prevent the oil from getting sufficiently hot to rapidly boil off the water. When water combines with blowby gases, acids are formed and degrade the oil and corrode the engine surfaces. Ingress of water from broken cooling lines or the environment will result in rapid degradation of the oil, and could even cause severe wear and engine failure.
Coolant
Glycol-based engine coolants are largely used. Head gasket seal rupture, cooling system corrosion, or loss in integrity of cooling line fittings all can result in the mixing of coolant with the oil. Specifically, glycol is corrosive to non-ferrous bearing surfaces. Excessive coolant causes the telltale sheen of "mayonnaise" oil emulsion, resulting in engine seizure.
Soot
Soot is produced as a result of the mixing of burning fuel with oil on the cylinder liner(s) or due to retarded injection timing. Excessive soot leads to abnormal valve and injector train wear and can overload the emissions control systems, resulting in air quality fines.
Hence, what are the tests to be included for engine oil monitoring? Any test on engines has to include tests to look for common contaminants, together with tests to ascertain wear metals and oil viscosity.
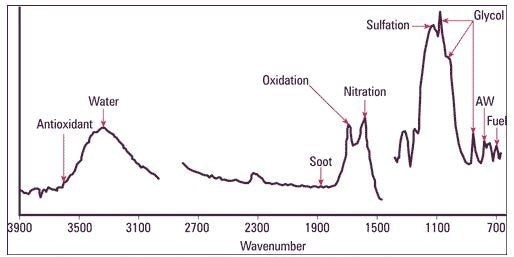
Typical used oil FTIR spectrum
Infrared spectroscopy is an excellent method for the detection of water, organic contaminants, and oil degradation products in a used oil sample. A single measurement provides a plethora of information related to the oil condition and contamination.
Oxidation and Nitration by Infrared Analysis
In cases of severe oxidation, the critical surfaces are corroded by the lubricant. The “oxidation number” is directly proportional to the extent of oxidation. Conditions such as sticky rings, varnishing, lacquering, sludge deposits, and filter plugging take place in systems with oxidation issues.
Nitration is another significant parameter that detects the amount of NOx compounds in the oil. These compounds can react with water in the oil and produce nitrous acids, thereby degrading the oil and reducing the effectiveness of additives. This can form lacquer, varnish, and engine deposits.
- Antiwear additive: It is measured by IR and is a measure of ZDDP additive remaining in the oil. ZDDP is an important friction reducing additive, which when exhausted leads to less protection against abnormal wear.
- Soot: It is measured by IR and is a measure of the carbon present, in wt%. Despite the fact that a majority of the engine oils include additives for dispersing soot, growing amounts can overload their potential to do so, resulting in wear and poor operation.
- Glycol content: It is a measure of the liquid glycol, in wt %. Glycol coolants disintegrate under a high-temperature engine environment, resulting in the formation of glycolic acids. These acids corrode non-ferrous bearing surfaces and lead to the formation of metal salts. They also react with anti-oxidant and anti-wear additives in the oil (together with water) and form sludges that plug filters and make the oil to lose its lubricity properties, thereby increasing abrasive wear. Glycol contamination in transmissions and engines is regarded as a highly severe contaminant than just water (up to 10 times more damaging). Based on the temperature of the oil, the glycol coolant might disintegrate quickly or over time. Such an imbalance is a major difficulty in ascertaining the actual glycol content in the oil at a given instant and is the predominant reason for the discrepancy between field and lab tests.
Viscosity
Viscosity is a fluid’s resistance to flow. Kinematic viscosity is the most crucial physical property of lubricant for engines. In general, engine oils are multigrade formulations, formulated to enable normal operation of the engine over a broad array of startup operating temperatures. Often, viscosity is reported at 100 °C. If a lubricant’s viscosity crosses the ranges set by SAE for maximums and minimums, it must be changed. Oil viscosity is anticipated to increase over time and use with an increase in solids and soot. Viscosity loss in an engine is regarded to be more severe than the increase in viscosity and is usually caused by fuel contamination.
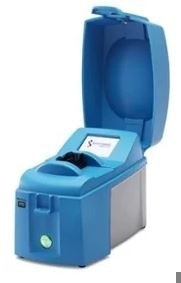
Total Base Number
Total base number (TBN) is the measure of the alkaline reserve in a lubricant, which is usually measured by titration, similar to the Karl Fischer technique. It can also be measured in other ways, for example through infrared spectroscopy. Blowby gases, in combination with moisture from aggressive acids in the crankcase, deplete the base number. Additives added to engine oils are formulated to react with the acids formed and neutralize them. The base number is used as a guide to follow the depletion of additive of an oil in use. Oil changes are usually suggested if the TBN value reaches a preset level for a specific lubricant and application. A sudden decrease in TBN indicates abnormal operating conditions (for example, excessive blowby) that mandates investigation. A majority of the lubricant suppliers provide TBN condemnation limits in the bulletins. In general, if the TBN value is 30% of the original starting value, oil change is imminent. An oil with a high starting TBN value is recommended for engines that run on fuels with high sulfur content, and the alarm limit is 50% of the starting value rather than 30%.
Water
One of the most common contaminants of oil is water, which can enter the engine oil as a combustion byproduct, or following a leak in the cooling system. Despite the fact that the engine oil temperature is adequately high to eliminate moisture during operation, elevated levels of water will induce damage wear. Excessive water that enters the engine as a result of ingression or leaks will lead to severe wear, resulting in engine seizure. Water contamination should never be more than 0.25% for a majority of the engines.
Total Acid Number
Total acid number (TAN) is a measure that indicates the relative acidity of a lubricant, which is usually measured by titration. The acid number is used as a guide to follow the oxidative degeneration of an oil in use. In engine applications, TAN is recommended for natural gas-fired engines. A sudden increase in TAN indicates abnormal operating conditions (for example, overheating ) that needs to be investigated. A majority of the lubricant suppliers provide TAN condemnation limits in the bulletins. In general, a 2.0-point increase in the starting value is a cause for concern.
Ferrous Density
Ferrous density is a measure of the cumulative amount of ferrous magnetic debris in oil and is measured in ppm using a magnetometer. Ferrous debris that ranges in size from sub-micron to visible sizes leads to a variation in electrical current proportional to the amount of magnetic metal contained in oil. The total amount of ferrous debris is an important indicator of wear in any engine and should be incorporated on all screening test packages. The true value in ppm is trended and a 10% increase in the wear rate is suggestive of an abnormal change that may necessitate intervention.
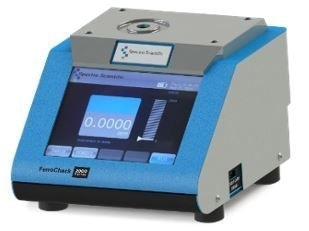
Fuel Dilution
Fuel dilution is a measure of the unburned liquid fuel that exists in the lubricant due to poor seals, leaking injectors, or poor combustion settings. All engines can tolerate some of this fuel; less than 2% is anticipated and more than 5% is a problem. Fuel dilution is measured by either SAW or GC sensor (fuel sniffer) and generally reported in wt%.
Particle Count
Particle count is a technique employed to count and categorize particulates in a fluid based on accepted size ranges, generally in accordance with ISO 4406 and SAE 4059. It is a very useful test to enhance reliability since decreasing particulates in the oil will increase the engine life. In general, it is an optional test for fielded engines as the soot content normally impedes an exact particle count. Particle count is usually used in engine development since technologies like LaserNet have the potential to effectively measure particle count in oils that contain up to 1.5% soot.
Ferrous Particle Count
Ferrous particle count is a method for quantifying the existing ferrous debris based on quantity and size, but not concentration. Intrinsic magnetometers (LNF or online) are widely used at present, and also the direct-read (DR) ferrography system. It is useful in detecting the size and quantity of the existing ferrous debris particles, which enhances the spectroscopy and ferrous density methods. The ratio of large and small particles in the sample is measured and the data can be used to calculate the severity indexes and the wear particle concentration, which may be alarmed.
Elemental Spectroscopy
Elemental spectroscopy is a method employed for the detection and quantification of metallic elements in a used oil caused by contamination, wear, and additives. The oil sample is energized to drive each element to emit a quantifiable amount of energy, which denotes the concentration of the element in the oil. The results indicate the concentration of all dissolved metals, either in the form of particulates or from additive packages. This test is the base for all off-site and on-site oil analysis tools since it offers information on contamination, machine, and wear condition in a comparatively accurate and rapid manner. Its major drawback is that its particle detection efficiency is poor for particles with a size of 5 μm or more, reiterating the salience of measuring the ferrous density first.
Wear Debris Analysis
Wear debris analysis (WDA) is defined as either an analytical or a patch technique that involves separating magnetic wear particles from the oil and depositing them on a glass slide called a ferrogram. Microscopic investigation of the patch or slide allows characterization of the wear mode and possible sources of wear in the machine. This method is called as analytical ferrography. Although it is an exceptional indicator of abnormal non-ferrous and ferrous wear, it is often performed only by a trained analyst.
The table below provides a summary of recommended test parameters.
|
Viscosity |
TBN |
Water |
TAN |
Oxidation |
Nitration |
Elemental |
Soot |
Fuel Dilution |
Particle Count |
Ferrous Particle |
WDA |
Engine Liquid |
R |
R |
R |
R |
R |
R |
R |
R |
R |
O |
O |
O |
Engine NatGas |
R |
R |
R |
R |
R |
R |
R |
O |
N/A |
O |
O |
O |
R = Recommended; O = Optional.
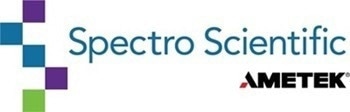
This information has been sourced, reviewed and adapted from materials provided by AMETEK Spectro Scientific.
For more information on this source, please visit AMETEK Spectro Scientific.