Copper Indium Gallium Selenide, or CIGS, is a direct bandgap semiconductor employed in the manufacture of solar cells. Compared to other semiconductor materials, a smaller amount of material is needed for CIGS as it strongly absorbs sunlight, thereby enabling the production of enhanced photovoltaics.
CIGS is deposited on a glass substrate coated with a layer of Mo and sealed with layers of ZnO, CdS, and Al-doped ZnO. The thickness of the Mo layer can be up to 1 μm while that of the CIGS layer varies from 1 to 4 μm. As a truly non-destructive method, Energy-Dispersive X-ray Fluorescence or EDXRF is a perfect method for the characterization of CIGS solar cells, and for determining both composition and thickness of layers.
.jpg)
Figure 1. Cross-sectional schematic of a typical CIGS solar cell
.jpg)
Instrumentation
The ARL™ QUANT’X XRF Spectrometer from Thermo Scientific™ is an EDXRF system that offers an economical and rapid analytical capability. It is equipped with an air-cooled Rh end-window tube with thin Be window of 0.05 mm thickness and has the highest power of 50 Watts. An electrically cooled Silicon Drift Detector (SDD) with an area of 30 mm2 is equipped in the ARL QUANT’X Spectrometer. In total, nine primary beam filters are provided in the instrument, guaranteeing an optimal excitation condition is always found. Unattended analysis is enabled by an optional 10-position sample changer.
.jpg)
Sample Preparation and Presentation
CIGS solar cells are assessed as such without the need for sample preparation, apart from cleaning the cell’s surface if necessary. Larger CIGS cells can be easily housed in the spacious sample chamber. For analyzing specific areas, sample positioning is enabled by the availability of a CCD camera.
Excitation Conditions
The excitation conditions employed for this application are illustrated in Table 1. All measurements can be performed in the presence of air as there are no light elements. Element characteristic peak intensities of several thousand counts are created by a measurement time of 30 seconds per condition. An example of a spectrum acquired from a CIGS solar module is shown in Figure 2.
Table 1. Excitation conditions used to calibrate for and analyze CIGS solar cells
Voltage (kV) |
Tube Filter |
Atmosphere |
Live time (s) |
Elements of Interest |
30 |
Pd Thick |
Air |
30 |
Cu, Ga, Se |
50 |
Cu Thin |
Air |
30 |
In, Mo |
.jpg)
Figure 2. Spectrum of a CIGS solar cell acquired with an excitation voltage of 50 kV and a thin Cu filter. The measurement time is 30 seconds, sufficient to generate intense element characteristic peaks.
Calibration and Validation
The layer thickness and composition quantification technique based on fundamental parameters (FP) incorporated with the Thermo Scientific™ WinTrace™ software for ARL QUANT’X Spectrometer is used for determining both elemental composition and thickness of each layer. The only requirement of this package is the input about the number of layers and the elements present in each layer. It does not require any information about the concentration or thickness. Calibration is performed using bulk samples of Ga2O3, Cu, In, Mo, and SeO2 as well as thin film standards for each element at a concentration of approximately 50 μg/cm2 each.
The analysis and repeatability results of a typical CIGS solar cell are shown in Table 2, and a variant without any copper is shown in Table 3. Both cells are not enclosed with a transparent front contact describing the absence of any Zn and Cd (see Figure 2). Since the glass substrate lacks elements having any improving effects on the CIGS elements and Mo, its impact can be rejected, and the stack to model primarily contains a Mo layer and a CIGS layer. The repeatability of the technique/instrument was tested by consecutively assessing both the samples for 10 times.
At a relative error of less than or equal to 0.5%, the repeatability of determining the layer thickness is magnificent. Relative errors on the concentrations are less than 1% for all elements excluding Ga (1.5%). If the measurement time of the 30 kV excitation condition is increased to 2 minutes, the RSD value would be decreased considerably lower than 1% for Ga.
Table 2. Analysis and repeatability results of a typical CIGS solar cell
Sample Run # |
CIGS layer |
Mo layer |
CIGS
(μm) |
Cu
(%) |
Ga
(%) |
Se
(%) |
In
(%) |
Mo
(μm) |
Mo
(%) |
CIGS A01 |
1.292 |
16.26 |
5.90 |
49.91 |
27.92 |
0.925 |
100 |
CIGS A02 |
1.303 |
16.42 |
5.74 |
49.92 |
27.92 |
0.922 |
100 |
CIGS A03 |
1.289 |
16.17 |
5.82 |
49.70 |
28.31 |
0.922 |
100 |
CIGS A04 |
1.294 |
16.22 |
5.91 |
49.60 |
28.28 |
0.922 |
100 |
CIGS A05 |
1.293 |
16.26 |
5.79 |
50.10 |
27.86 |
0.934 |
100 |
CIGS A06 |
1.295 |
16.38 |
5.90 |
49.76 |
27.96 |
0.924 |
100 |
CIGS A07 |
1.298 |
16.31 |
5.91 |
49.66 |
28.12 |
0.927 |
100 |
CIGS A08 |
1.301 |
16.04 |
5.71 |
49.72 |
28.54 |
0.926 |
100 |
CIGS A09 |
1.290 |
16.24 |
5.84 |
49.71 |
28.22 |
0.934 |
100 |
CIGS A10 |
1.294 |
16.29 |
6.02 |
49.98 |
27.71 |
0.931 |
100 |
Average |
1.295 |
16.26 |
5.85 |
49.81 |
28.08 |
0.927 |
100 |
1-Sigma |
0.005 |
0.11 |
0.09 |
0.16 |
0.25 |
0.005 |
0 |
Table 3. Analysis and repeatability results of CIGS type solar cell containing no copper
Sample Run # |
CIGS layer |
Mo layer |
CIGS
(μm) |
Cu
(%) |
Ga
(%) |
Se
(%) |
In
(%) |
Mo
(μm) |
Mo
(%) |
CIGS B01 |
1.103 |
0.06 |
7.19 |
53.13 |
39.62 |
0.931 |
100 |
CIGS B02 |
1.121 |
0.04 |
7.31 |
52.82 |
39.84 |
0.940 |
100 |
CIGS B03 |
1.119 |
0.00 |
7.40 |
52.61 |
39.99 |
0.941 |
100 |
CIGS B04 |
1.113 |
0.06 |
7.11 |
52.71 |
40.12 |
0.934 |
100 |
CIGS B05 |
1.117 |
0.14 |
7.36 |
52.80 |
39.71 |
0.933 |
100 |
CIGS B06 |
1.114 |
0.03 |
7.30 |
52.97 |
39.70 |
0.939 |
100 |
CIGS B07 |
1.118 |
0.11 |
7.27 |
52.54 |
40.09 |
0.935 |
100 |
CIGS B08 |
1.117 |
0.03 |
7.36 |
52.48 |
40.13 |
0.940 |
100 |
CIGS B09 |
1.123 |
0.09 |
7.35 |
52.48 |
40.09 |
0.943 |
100 |
CIGS B10 |
1.119 |
0.10 |
7.27 |
52.50 |
40.14 |
0.932 |
100 |
Average |
1.116 |
0.06 |
7.29 |
52.71 |
39.94 |
0.937 |
100 |
1-Sigma |
0.006 |
0.04 |
0.09 |
0.22 |
0.20 |
0.004 |
0 |
Conclusion
In this article, the superior performance of the ARL QUANT’X EDXRF Spectrometer and its SDD for the non-destructive analysis of CIGS solar cells have been described. Excellent repeatability values are enabled by total measurement times of 1 minute live time for the layer thickness as well as for the layer composition. The FP-based thin film software enables the measurement of mass, composition, and thickness of up to six layers comprising of any number of elements.
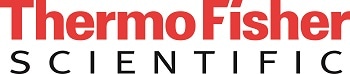
This information has been sourced, reviewed and adapted from materials provided by Thermo Fisher Scientific - Elemental Analyzers.
For more information on this source, please visit Thermo Fisher Scientific - Elemental Analyzers.