Feb 23 2019
Over the years, a variety of pump technologies have been tested or used for virus filtration, chromatography, and TFF processes. Lobe and peristaltic pumps are two of the most popular choices of biopharmaceutical manufacturers. However, both have been found to present operational inefficiencies that may render them unsatisfactory for application in the above-mentioned processes.
Lobe Pumps
As most of the biopharmaceutical materials are surrounded by a low-viscosity aqueous solution, lobe pumps may not be a good option because slippage can take place during their operation, which can vary from 10% to 100%, based on the system’s back pressure. Additionally, the slip will lead to increased shear damage and energy consumption, and if used in a long-duration recirculation loop, for example, in a TFF filtration system, there can be obvious heat addition to the product that needs considerable cooling efforts to safeguard the product from overheating.
Lobe pumps also possess mechanical seals, which enable a controlled product leak and full containment is not offered unless special (and usually expensive) seals and seal barriers are used. The sterility needed in biopharmaceutical handling also means that exterior contaminants should not be introduced into the purification process, which is something that cannot be reliably guaranteed by pumps with mechanical seals.
Furthermore, the required contact between a lobe pump’s internal parts can result in wear and the formation of particles that can cause product contamination. Solid particulates, such as undissolved salt crystals, can pose extreme damage to the lobes, leading to the breakdown of the whole manufacturing batch. Since more power is needed to overcome the pump’s slippage, lobe pumps will eventually cost more.
Peristaltic (Hose) Pumps
The method of operation of peristaltic pumps will certainly generate pulsation, and as mentioned, pulsation is always bad in biopharmaceutical manufacturing. This is the main as well as the most apparent limitation of peristaltic pumps. Additionally, they have restricted flow- and pressure-handling potentials. For instance, they cannot consistently produce higher discharge pressures (such as 4 bar, or 58 psi) that are necessary for certain fluid-handling applications.
They are also identified to discharge some small quantity of hose material — in a process called “spalling” — into the pumped product, which can affect its purity. If the spalled hose material enters the filter, it can taint the filter, and make it function not as efficiently as it should, resulting in contamination. Furthermore, the mechanical deformation of the hose during the pumping process will lead to inconsistency of flow rate. To conclude with, the limitations of lobe and peristaltic pumps come down to two major things:
- If there is shear, which is frequent in lobe pumps, the pumped material will be damaged
- If there is pulsation, an operational certainty with peristaltic pumps, consistent flow is not possible, and without consistent flow, accurate flow is not possible
The Solution
The quaternary diaphragm pump can be an effective solution to the operational limitations of lobe and peristaltic pumps.
The inspiration for the invention of the quaternary diaphragm pump can be traced back 30 years to the mid-1980s, the period which is now called as the “birth of the modern biotech industry.” In 1986, Frank Glabiszewski was an engineer for a German filter manufacturer and was getting more and more irritated with the overall operation of the pumping technologies that were widely used in chromatography and TFF applications.
We were using peristaltic pumps but we found out that these pumps were not made for TFF applications. We were checking the marketplace looking for better pumps and spent 80% of our time looking for pumps.
Frank Glabiszewski, Engineer
“One night I went home and I was sitting in my car frustrated after a pump failure and asked myself a question, ‘Which type of pump did Mother Nature invent to process sensitive biologic fluids like blood?’”1 Glabiszewskire recalled.
Indeed, the answer was the human heart, and bearing that in mind, Glabiszewski started working with his friend and engineering partner, Josef Zitron, to refine the design and operation of the quaternary diaphragm pump technology. By the time the new technology was finalized in 2000, the duo set up a company that would start manufacturing quaternary diaphragm pumps for use in biopharmaceutical-manufacturing processes. As the duo’s innovation increased in popularity for the last 15 years, the technology was also customized such that it could use disposable plastic heads and wetted parts to make it applicable in the growing single-use biopharmaceutical-production market.
The working principle of the quaternary diaphragm pump most closely resembles the human heart’s operation as the four-piston diaphragm technology allows a mild pumping action with subtle “heartbeats.” This act creates four overlapping pumping strokes of the pistons that effectively limit pulsation because each stroke of the four diaphragms is produced by an eccentric shaft that is attached to an electric motor.
The method of operation of quaternary diaphragm pump enables it to softly, carefully, and securely pass on low-viscosity aqueous solutions and biopharmaceutical materials that are highly sensitive to shear forces and pulsation when pumped. Since no wetted rotating parts or mechanical seals are needed by the four-piston design of the pump, total product containment is guaranteed without any particulate generation or abrasion. Furthermore, the method of operation of the pump produces risk-free dry operation and self-priming abilities with high turndown ratios. A pump technology with high turndown ratios enables the creation of a wide flow range, which renders the pump applicable for use in a broad variety of process applications.
With respect to precise unit operations, chromatography columns can be packed using quaternary diaphragm pumps and then the biopharmaceutical material can be pumped through the column, where both are of significant concerns that need low pulsation with accurate and consistent low rates and pressures. In TFF applications, quaternary diaphragm pumps offer steady flow control that is necessary for producing optimal filtrate yields.
In the existing burgeoning biopharmaceutical-manufacturing processes, quaternary diaphragm pumps are also quickly turning out to be a first-choice technology in ever more popular single-use production installations. Essentially, a single-use pump allows biopharmaceutical manufacturers to eliminate the cost of cleaning and validating their pumps by means of a pump with a replaceable pump head. The outcome is not just a more fast production process, but also one that offers desirable levels of product purity and sterility with no possibility for cross-product contamination or cross-batch.
Some of the other benefits that can be achieved by using quaternary diaphragm single-use pumps are listed below:
- Can be used in one production campaign or for one product
- At the end of the production campaign, the pump chamber that has contacted with the fluids is thrown away
- In case the operator wants to use a stainless-steel pump, the plastic pumping chamber can be removed and fitted with a stainless-steel one
- Can be used for a specified amount of time prior to replacing the wetted parts, which eliminates increased maintenance costs
- In case of a pump failure, the old chamber can be removed and replaced with a new one within five minutes
- Can be used when cleaning in place (CIP) or when steam sterilization is not possible or practical. This denotes a considerable simplification and cost reduction to the overall process since no contaminated cleaning chemical and water solutions are produced that must be treated and eliminated. Just the costs to properly treat and dispose the cleaning fluids can drive the use of single-use alternatives.
Indeed, not all pump technology is fully ideal for every characteristic of a particular fluid-handling application. In this case, the design and operation of the quaternary diaphragm pump restrict it to dealing with fluids that have a maximum viscosity of 1000 centipoise (cPs) and that include particulates with a diameter of up to 0.1 mm.
Conclusion
The significance of biopharmaceuticals implies that any and all products must fulfill stringent requirement with respect to their manufacture. This includes making sure that no damage is caused to component materials during virus-filtration, critical chromatography, or TFF processes. Although lobe and peristaltic pumps have been the favorite pumping technologies for these unit operations, the quaternary diaphragm pump can be a better choice, the operation of which significantly decreases the possibility that pulsation and shear will affect the safety and effectiveness of the end product.
Reference
- Video: “Quattroflow™: The New Standard in Biopharmaceutical PumpExcellence”
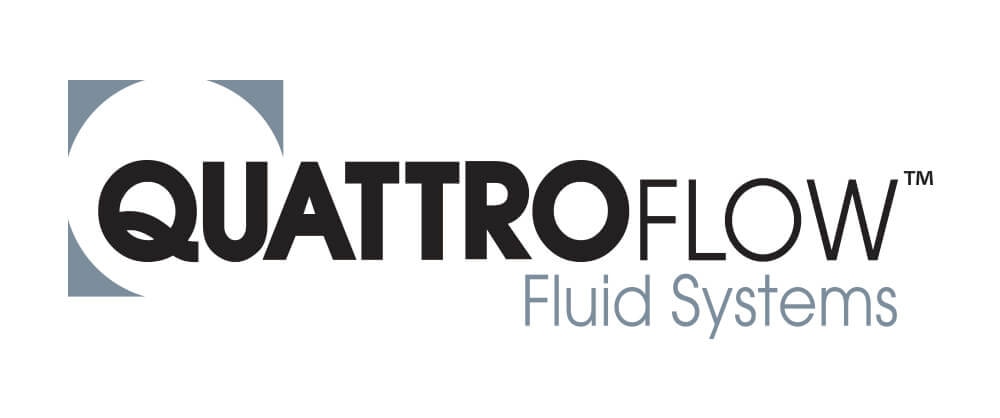
This information has been sourced, reviewed and adapted from materials provided by Quattroflow.
For more information on this source, please visit Quattroflow.