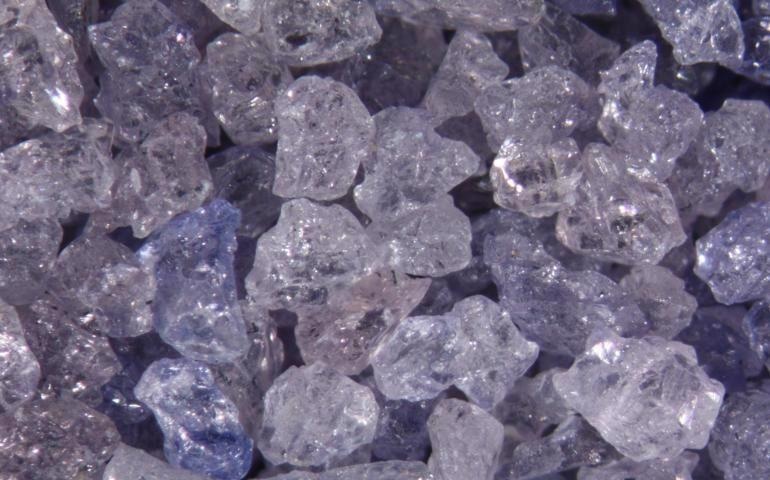
Aluminum oxide (Al2O3), which can also be known as alumina, is derived from a natural ore called bauxite. Al2O3 occurs naturally as the mineral corundum and in the form of ruby and sapphire gemstones; however, the term alumina usually refers to the manufactured material (1).
Most alumina is extracted from bauxite using the Bayer process, which was first developed in 1888 (1). Bauxite is crushed and mixed with a solution of sodium hydroxide, and then seeded with crystals to precipitate aluminum hydroxide. To remove the water, the hydroxide is heated using a kiln. As the temperature increases, alumina goes through several transition phases (α, χ, η, δ, κ, θ, γ, ρ). The alpha (α) phase is the most thermodynamically stable form, reached at the highest temperature. This phase is the strongest due to its closely packed, hexagonal crystals.
Alumina is very strong and hard, has a high melting point, and resists chemicals and abrasion (1). Other properties include a high degree of refractoriness, high thermal conductivity, high dielectric strength and high electrical resistivity (even at elevated temperatures).
Due to its properties, alumina is incredibly useful for a wide variety of industrial processes, for example metallurgy, chemical processing and ceramic processing (1). It is a very good ceramic electronic substrate and can be applied in milling media, abrasives, spark plugs, and wear-resistant applications such as welding nozzles and pump seals.
Commercial Grades
Using the Bayer process to make alumina produces several grades of material. At temperatures over 1100 oC, α-alumina occurs as a variety of ‘calcined’ grades that have a range of crystal size, morphology and chemical impurities (2). Sodium oxide (soda) is the main impurity and grades are therefore divided with regards to how much soda they contain. For example, ‘low soda’ contains less than 0.1% by weight and ‘medium soda’ contains 0.15 – 0.25%.
Other calcined grades include ‘reactive’ alumina. This has a relatively high purity and a small crystal size (2). It is highly resistant to temperature and wear. ‘Fused’ alumina is made in electrical arc furnaces and has a low permeability, low porosity, high refractoriness and high density. This makes it very suitable for abrasives and refractories.
A Brief History of α-alumina
Although Saint-Gobain produces various alumina types for lots of applications, it specializes in abrasive applications (3). The inherent properties mean that it is suitable for a broad range of abrasive uses, both loose and fixed, particularly in many chemical mechanical polishing (CMP) applications.
Manufacturing processes in the 1990s produced loose abrasive alpha alumina (about 100 – 200 nm). However, there was little control over defects and morphology. Technology improvements between 2005 – 2015 resulted in much more control. These advances have progressed even further in recent years and now developers are working towards sub 100 nm particles with minimum defects and extreme chemical resistance.
In 1984, Saint-Gobain invented α-alumina seeded gel technology for the fixed abrasives market (4). This is ground-breaking technology in which minute particles are dispersed in a precursor gel, water is removed, and it is converted to the alpha phase at relatively low temperatures. This results in a grain that has a unique nano-structure consisting of sub-micron, highly uniform crystals. When stressed, microfracture results in new cutting edges, which makes them ideal for use as abrasives.
Using the seeded gel-based alumina particle platforms from Saint-Gobain, it is possible to control all aspects of the alumina particles: shape, size, phase, size distribution, mechanical and thermal properties and doping.
Monocrystalline Alumina
Saint-Gobain has improved its monocrystalline alumina significantly (5). One of the environmental advantages is that sulfur is no longer used to make its MA88® product, which is produced by fusing special alloys with very pure alumina. It has a unique microstructure because each particle is a single crystal which creates many tough and sharp edges.
When used as an abrasive, they confer a sharper cutting action as well as improving the strength of internal bonds. Removal rates have increased by almost 30% and the process also requires less energy. Monocrystalline alumina can be used in precision grinding wheels in the aerospace and automotive industries and in rough grinding applications such as cut-off wheels and thin wheels.
The company has a portfolio of white-fused alumina products which extends from standard macro grits to specialized micro grits that have purity levels of approximately 99.5% aluminum oxide. This range is versatile and can be used for micro-blasting, lapping compounds, water-resistant coatings, heat treatment setting sands and bonded abrasives.
Micro Aluminum Oxide
Saint-Gobain also has a range of micro aluminum oxides (6). Particle size and chemistry can be controlled and this means that they can be adapted to suit specific applications for the electronics, industrial and semiconductor industries. The range encompasses brown-fused and white-fused aluminum oxide, electronic grade alumina and calcined alumina with micro grit sizes ranging from 45 microns to 3 microns.
Alumina Zirconia Abrasive Grains
Alumina zirconia is one of the toughest abrasive materials (7). These abrasive grains can be manufactured to produce the optimum alloy of zirconia and alumina by monitoring the microstructure and crystal size. Alumina zirconia has the edge over other commodity abrasives such as silicon carbide, because of its very fine crystalline microstructure. It performs well in bonded abrasive, coated abrasive, and cut-off wheel applications, particularly for challenging alloys such as stainless steel.
Nano Polycrystalline Alumina Particles
Saint-Gobain has developed and refined its seeded gel technology over the years. The current Polycrystalline Alumina Particles now have a finer crystallite size than ever before and are smaller than 75 nanometers. Particle dispersion has been enhanced and particle size distribution can be controlled closely. Furthermore, the product can be adapted for specialized applications.
Saint-Gobain offers a selection of sizes for customers to choose from to best meet their application requirements. For example, it is possible to make products in sizes ranging from sub-100 nm to tens of microns.
These particles have a unique composition which makes them ideal for sensitive electronics applications. Here they provide cost-effective polishing abrasive for slurry formulation, in particular CMP slurries. The product offers a fast material removal rate and controlled surface finishes.
The product has other benefits, including the fact that, unlike colloidal silica, it does not re-crystallize and can be re-circulated to last longer. Large particle counts can be controlled to reduce defects on polished surfaces significantly by applying the latest particle processing technology.
References
- https://www.britannica.com/science/alumina
- https://www.azom.com/article.aspx?ArticleID=1389
- https://www.abrasivematerials.saint-gobain.com/
- https://www.abrasivematerials.saint-gobain.com/products/cerpass-ceramic-grain
- https://www.abrasivematerials.saint-gobain.com/products/aluminum-oxide
- https://www.abrasivematerials.saint-gobain.com/products/micro-aluminum-oxide
- https://www.abrasivematerials.saint-gobain.com/
- https://www.surfaceconditioning.saint-gobain.com/products/engineered-particles
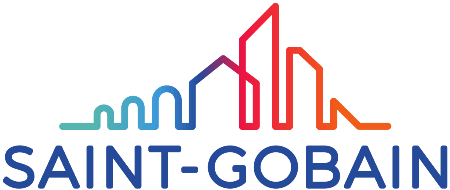
This information has been sourced, reviewed and adapted from materials provided by Saint-Gobain Specialty Grains and Powders.
For more information on this source, please visit Saint-Gobain Specialty Grains and Powders.