ACP Composites found the need to provide a high-quality sandwich panel that appeals to their customers but does not require the strict aerospace processing standards.
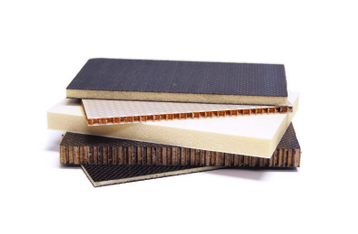
Image Credit: General Plastics
More specifically, APC wanted to offer a sandwich panel that is reliable, versatile, and more cost-effective than other panels that use the common core material, Nomex Honeycomb. It must also be available in various thicknesses and densities. ACP decided that this could be achieved best using a polyurethane foam core material.
The foam also needed to be stable enough to survive the 250 oF processing temperatures and applications without shrinking, deforming, or changing in any way.
We’ve tried and tested every foam you can imagine, I’ve had foams catch on fire, some have even collapsed during processing.
Justin Sparr, CEO, ACP Composites
“Other foams that could do the job were over-priced or had too long of a lead. So, it would restrict us from carrying out our commitment to continuously meet our customers’ delivery and production schedules.”
Key Requirements
- Cost-effective
- Stable, high-performing foam core material
- Can be cut into various thicknesses
- Withstands 250°F (121°C) processing temperature without deforming
- Readily available without long lead times or a hefty minimum quantity requirement
- Highly machinable
- Available in a variety of densities
Solution and Application
APC Composites found that LAST-A-FOAM® FR-3700 series polyurethane from General Plastics was the most reliable and consistent material that met all the requirements.
General Plastics’ foam is perfect for our needs. It is a high-performing, economically viable solution that stays stable under our high-temperature processing applications. The company also offers comprehensive technical data sheets on all their foam materials, which makes it easier for customers to verify it fits their application requirements.
Justin Sparr, CEO, ACP Composites
FR-3700 is a closed-cell, flame-retardant, rigid polyurethane foam that is available in a broad range of densities. It is less friable and tougher than other rigid foam materials and is aerospace-grade, BMS 8-133-qualified.
This means crisper edges can be cut, so it is well-suited to machining complex shapes for composite cores. Due to its cellular structure and cross-linked resin, LAST-A-FOAM® FR-3700 has a high strength-to-weight ratio. It has great resistance to water absorption and will not split, crack, or swell when exposed to water. This series is non-abrasive and can be machined with standard high-speed steel (HSS) cutting tools.
Military Solar Array
Foam from General Plastics is used in a number of ACP’s customer applications. For example, the foam is used as a core material for portable, field-deployed military solar arrays.
When using electronics in the field, soldiers require a lightweight solar array that produces bulk energy to charge batteries and other electronics anywhere they are. ACP found that foam from General Plastics was ideal for this application because it fit the mechanical and budget needs of the customer.
Medical Positioning Table
Foam panels are also used for positioning patients in the medical industry. The foam core from General Plastics allows ACP to install carbon fiber inserts within the panel. This provides the option to bolt into it or drill a hole through it.
Usually, this type of carbon fiber table uses a polyacrylamide foam core. However, that material is much more expensive than polyurethane foam and has a much longer lead time.
Using foam from General Plastics, the panel for the table was produced quickly with the same imaging clarity and dimensional stability and imaging clarity as polyacrylamide foam, but with a much lower price point. The customer was pleased with the low density and ease of machining of the foam, and ACP now has a standing order for the product.
Overall, I always know what to expect with General Plastics. They’re easy to work with, and I know I’m always going to receive a quality product that the company stands behind.
Justin Sparr, CEO, ACP Composites
3700 Benefits
- Flame retardant
- Stable and inert
- Resistant to most chemicals and solvents
- High strength-to-weight ratio from cross-linked resin
- Will not support fungal growth
- Performs well as wood replacement
- Easily shaped with common woodworking tools
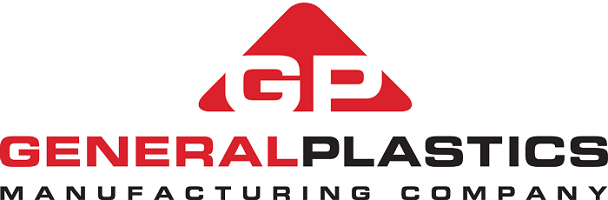
This information has been sourced, reviewed and adapted from materials provided by General Plastics Manufacturing.
For more information on this source, please visit General Plastics Manufacturing.