Emulsion explosive is a commonly used industrial explosive used in infrastructure development like mining, tunnel piercing, and bridge construction around the world. In research published in the Journal of Molecular Liquids, researchers summarized recent studies on rheological properties and discussed the connection between rheology and emulsifiers, oil materials, dispersed droplet size, and other factors.
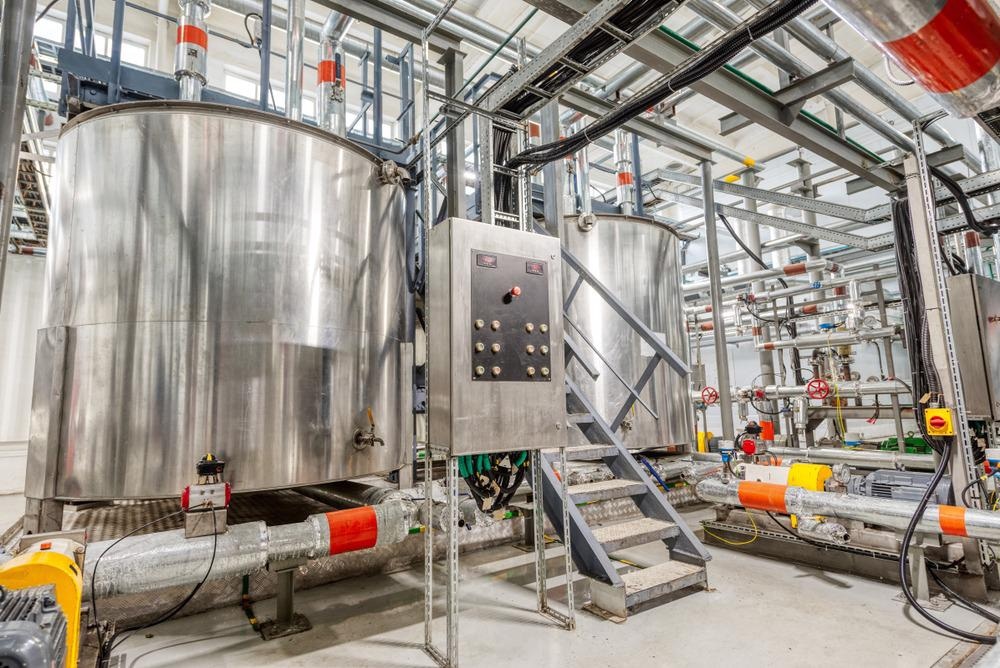
Study: Advances in the rheology of emulsion explosive. Image Credit: Nordroden/Shutterstock.com
In most cases, an emulsion explosive is made in two processes. Oil materials and AN supersaturated solutions are emulsified into an emulsion explosive matrix, which is then mixed with hollow glass spheres (microspheres) or air bubbles to create an emulsion explosive. The primary idea behind industrial explosive formulation design is a zero oxygen balance.
The emulsion explosive matrix, which is generated in the initial preparation phase, has an extremely low initiation sensitivity. To enhance the stable explosion of emulsion explosives, it is required to implant a particular quantity of bubbles to produce hot spots in the beginning.
The rheology of emulsion explosives, or the emulsion explosive matrix, has been extensively investigated in recent years, both experimentally and conceptually. The mean diameter of dispersed droplets, polydispersity, emulsifiers, the dispersed phase volume fraction, and other factors all affect rheological properties.
Now, researchers have looked at the importance of rheology in evaluating the stability and performance of emulsion explosives. They also examined the challenges in existing emulsion explosive rheology research and gave recommendations for future study.
Discussion
Polydispersity and deformation of scattered droplets are two microstructure properties that might be examined for emulsion explosive matrices. There are distinct micron-sized droplets in the matrix, as shown in Figure 1(a). Furthermore, emulsification shear can cause film rupturing and coalescence, resulting in the creation of isolated bigger droplets within a sea of smaller droplets.
During emulsification, the AN supersaturated solution is progressively poured into the melting oil at a moderate rotational speed, and the droplets are then refined by raising the rotational speed. If researchers simply increase the rotational speed in the refining process, the matrix droplet size decreases noticeably and the polydispersity of the droplets appears to be diminished at the same scale. As a result, it is worth noting that polydispersity is greatly influenced by the technical parameter of preparation.
The droplets are compressed and turned into polyhedrons to fill the space more firmly, with very small continuous phase layers between nearby drops.
The first thing to note is that the rheology of the so-called emulsion explosive encompasses practically the entire emulsion explosive matrix, or more precisely, the bulk emulsion explosive matrix (BEEM). Since this type of matrix will be transported over long distances by pipeline or by vehicle before being employed, it is important to consider its rheological behavior.
The properties of matrix steady-state flow have been extensively researched, and some of them can be characterized using well-known general constitutive laws.
By plotting the results, researchers showed that when shearing is stopped for a short time, the refining of droplets caused by shear stress disappears. Additionally, no difference was observed in the photographs of the matrix before and after shearing, indicating that the matrix structure can go back to its initial state.
The recovery stage has the same shear rate as the standing stage. In the study, the two parameters were affected by the matrix’s shear stress and droplet size. A high shear rate leads to a high risk of matrix structure break. As a result, returning to its original structure is challenging.
The structure of the matrix that was sheared was more similar to its initial state when the droplet size was tiny.
A small oscillatory shear testing mode can be used to examine the linear viscoelastic behavior of the emulsion explosive matrix. When the strain is small, there is a linear viscoelastic region (LVER).
The crystallization of the supersaturated AN solution grows with time, as evidenced by the changing of the matrix microstructure assessed by rheology.
The presence of polar groups in vegetable oils or waxes is a significant difference between the two compounds. As a result, polarity, in addition to viscosity, is a crucial element in matrix stability. By evaluating the fluctuation of G’ of the matrix created by biodiesel and mineral oil, which both have the same viscosity but different polarity, Zhao et al. discovered that increasing polarity affected the stability of the matrix significantly.
AN crystal was not detected in these matrices, and the droplet size did not alter substantially among four PIBSA-based emulsifiers with the same hydrophobic chain but various hydrophilic groups, namely PIBSA-STEA, PIBSA-LTEA, PIBSA-DTEA, and PIBSA-DTEA.
Zhao et al. discovered a relationship between G’ and detonation velocity, both of which rise as droplet size decreases. The authors state that G’ is a valid criterion for analyzing the performance of emulsion explosives.
Despite the fact that the microstructure of the emulsion explosive matrix is comparable in all three-emulsion explosives, the post-sequence preparation procedure and explosive morphology are different.
Although it does not need long-distance pumping before blowing as a bulk emulsion explosive, the matrix of the other two explosives must travel a specific distance through a pipeline during production. The difference is that the other two explosives, particularly the powdered emulsion explosive, require a greater temperature for preparation due to their low water content.
Conclusion
In this study, researchers outline the present state of emulsion explosive rheology research. Both flow and viscoelasticity behavior were investigated experimentally and conceptually, as well as their tight relationship with microstructure, emulsifiers, and oil components.
Journal Reference:
Zhao, H. R., Wu, J., Xu, M. X., Zhang, K. M (2021) Advances in the rheology of emulsion explosive. Journal of Molecular Liquids, 336, p. 116854. Available Online: https://www.sciencedirect.com/science/article/abs/pii/S0167732221015786
References and Further Reading
- Chattopadhyay, A K (1996) Emulsion explosive, US: 5500062.
- Meduselac, M (2000) Explosive emulsion composition, WO:0017130A1.
- Braithwaite, M & Turcotte, R (2008) Minimum burning pressure of emulsion explosives, Propellants Explos. Pyrotech, 30, p. 116. doi.org/10.3791%2F56167.
- Al-Sabagh, A M & Hussien, M A (2017) Preparation and investigation of emulsion explosive matrix based on gas oil for mining process, Journal of Molecular Liquids, 238, p. 198. doi.org/10.1016/j.molliq.2017.04.085.
- Zhang, K M & Ni, O Q (2014) Study on safety of ModelⅡpowdery emulsion explosive, Applied Mechanics and Materials. 137.
- Sosnin, V A & Cabdullin, R Kh (1994) Study of the thermal stability of a poremit emulsion, Combust. Explosion Shock Waves, 30, p. 810. doi.org/10.1007/BF00755256.
- Jones, D. E. G., et al. (1999) Parameters affecting the thermal behavior of emulsion explosives, Thermochimica Acta, 331, p. 37. doi.org/10.1016/S0040-6031(98)00660-1.
- Fang, H., et al., (2021) Effects of content and particle size of cenospheres on the detonation characteristics of emulsion explosive, Journal of Energetic Materials, 39, p. 197. doi.org/10.1080/07370652.2020.1770896.
- Cheng, Y. F., et al. (2014) Explosion Power and Pressure Desensitization Resisting Property of Emulsion Explosives Sensitized by MgH2, Journal of Energetic Materials, 32, p. 207. doi.org/10.1080/07370652.2013.818078.
- Mertuszka, P., et al, (2020) The influence of temperature on the detonation velocity of selected emulsion explosives, Journal of Energetic Materials, 38, p. 336. doi.org/10.1080/07370652.2019.1702739.
- Wang, X G (2008) Emulsion Explosives, Metallugical Industry Press, Beijing.
- Yost, S. L., et al. (2007) Hayes, Environmental process descriptors for TNT, TNT-related compounds and picric acid in marine sediment slurries, Marine Pollution Bulletin. 54, p. 1262. doi.org/10.1016/j.marpolbul.2007.03.019.
- Pennington, J C & Brannon, J M (2002) Environmental fate of explosives, Thermochimica Acta, 384, p. 163. doi.org/10.1016/S0040-6031(01)00801-2.
- Liu, L., et al. (2018) Experimental study on the influence of chemical sensitizer on pressure resistance in deep water of emulsion explosives, IOP Conference Series: Earth and Environmental Science, 128, p. 1. doi.org/10.1016/j.plantsci.2017.11.001.
- Alipoor, A & Mazaheri, K (2013) The optimization of detonation properties in gaseous mixtures and mixed explosive materials. Journal of Energetic Materials. 31, p. 115. doi.org/10.1080/07370652.2011.616870.
- White, W J & Henderson, J M (2004) The crystallization of supersaturated emulsions, Isis experimental report, p. 14591. doi.org/10.1016/0095-8522(63)90049-7.
- White, W. J., et al., (2004) Interfacial structure of block copolymers at the oil/water interface, Isis experimental report, p. 15255.
- Langenfeld, A., et al. (1999) Rheological behavior of fluorinated highly concentrated reverse emulsions with temperature, Journal of Colloid and Interface Science, 218, p. 522. doi.org/10.1006/jcis.1999.6427.
- Weeks, E & Weitz, D (2002) Properties of cage rearrangements observed near the colloidal glass transition, Physics Review Letters, 89, p. 095704. doi.org/10.1103/PhysRevLett.89.095704.
- Bampfield, H A & Cooper, J (1985) Emulsion explosives. Encyclopedia of emulsion technology, Marcel Dekker, New York.
- Mason, T G (1996) Yielding and flow of monodisperse emulsions, Journal of Colloid and Interface Science, 179, p. 439. doi.org/10.1006/jcis.1996.0235.
- Meeker, S. P., et al. (2004) Slip and flow in soft particle pastes, Physics Review Letters, 92 p. 198302. doi.org/10.1103/PhysRevLett.92.198302.
- Bécu, L., et al. (2006) Yielding and flow in adhesive and nonadhesive concentrated emulsions, Physics Review Letters, 96, p. 138302. doi.org/10.1103/PhysRevLett.96.138302.
- Ragouilliaux, A., et al. (2007) Transition from a simple yield-stress fluid to a thixotropic material, Physics Review E, 76, p. 051408. doi.org/10.1103/PhysRevE.76.051408.
- Divoux, T., et al, (2010) Transient shear banding in a simple yield stress fluid, Physics Review Letters, 104, p. 208301. doi.org/10.1103/PhysRevLett.104.208301.
- Niedzwiedz, K., et al. (2010) Extensional rheology of concentrated emulsions as probed by capillary breakup elongational rheometry (CABER), Rheologica Acta, 49, p. 1103. doi.org/10.1007/s00397-010-0477-2.
- Paredes, J., et al, (2011) Shear banding in thixotropic and normal emulsions, Journal of Physics: Condensed Matter, 23, p. 284116. doi.org/10.1088/0953-8984/23/28/284116.
- Scheffold, F., et al. (2013) Linear and nonlinear rheology of dense emulsions across the glass and the jamming regimes, Journal of Physics: Condensed Matter, 25, p. 502101. doi.org/10.1088/0953-8984/25/50/502101.
- Paredes, J., et al. (2013) Rheology across the zero-temperature jamming transition, Physics Review Letters, 111, p. 015701. doi.org/10.1103/PhysRevLett.111.015701.
- Kima, H S & Mason, T G (2017) Advances and challenges in the rheology of concentrated emulsions and nanoemulsions, Advances in Colloid and Interface Science. 247, p. 397. doi.org/10.1016/j.cis.2017.07.002.
- Schlegel. M., et al. (2016) Local structure controls the non-affine shear and bulk moduli of disordered solids, Scientific Reports. 6, p. 18724. doi.org/10.1038/srep18724.
- Zhang, C., et al. (2015) Structure of marginally jammed polydisperse packings of frictionless spheres, Physical Review E, 91, p. 032302. doi.org/10.1103/PhysRevE.91.032302.
- Jorjadze, I., et al. (2013) Microscopic approach to the nonlinear elasticity of compressed emulsions, Physics Review Letters, 110, p. 048302. doi.org/10.1103/PhysRevLett.110.048302.
- Zhang, C., et al. (2016) Dynamical and structural signatures of the glass transition in emulsions, Journal of Statistical Mechanics: Theory and Experiment. P. 094003.
- Kim, J., et al. (2014) Helgeson, Microstructure and nonlinear signatures of yielding in a heterogeneous colloidal gel under large amplitude oscillatory shear, Journal of Rheology, 58, p. 1359. doi.org/10.1122/1.4882019.
- Wilking, J. N., et al. (2011) Mason, Shear-induced disruption of dense nanoemulsion gels, Langmuir, 27, p. 5204. doi.org/10.1021/la200021r.
- Romero, A., et al, (2008) Rheology and droplet size distribution of emulsions stabilized by crayfish flour, Food Hydrocoll, 22, p. 1033. doi.org/10.1016/j.foodhyd.2007.05.019.
- Mason, T G (1999) New fundamental concepts in emulsion rheology, Current Opinion in Colloid & Interface Science, 4, p. 231. doi.org/10.1016/S1359-0294(99)00035-7.
- Ya Malkin, A & Kulichikhin, V (2015) Structure and rheology of highly concentrated Emulsions. Russian Chemical Reviews, 84, p. 803.
- Hyun, K., et al. (2011) A review of nonlinear oscillatory shear tests: analysis and application of large amplitude oscillatory shear (LAOS), Progress in Polymer Science, 36, p. 1697. doi.org/10.1016/j.progpolymsci.2011.02.002.
- Masalova, I (2003) The Rheological Characterization and Pipeline Flow of High Concentration Water-in-oil Emulsions, Journal of Non-Newtonian Fluid Mechanics, 112, p. 101. doi.org/10.1016/S0377-0257(03)00064-8.
- Masalova, I., et al, (2005) Rheopexy in highly concentrated emulsions, Journal of Rheology, 49, p. 839. doi.org/10.1122/1.1940641.
- Masalova, I & Malkin, A Y (2005) Flow of Super-concentrated Emulsions, in: Proc. 2nd International Conference on Flow Dynamics, Sendai, Japan, 11, pp. 16. doi.org/10.1063/1.2204533
- Masalova, I & Malkin, A Y (2008) Master curves for elastic and plastic properties of highly concentrated emulsions, Colloid Journal, 70, p. 327. doi.org/10.1134/S1061933X08030101.
- Masalova, I & Malkin, A Ya (2013) The engineering rheology of liquid explosives as highly concentrated emulsions, Chem. Eng. Res. Des. 91, p. 204. doi.org/10.1016/j.cherd.2012.07.012.
- Foudazi, R., et al. (2011) The rheology of binary mixtures of highly concentrated emulsions, Applied Rheology, 21, p. 25326. doi.org/10.1122/1.4736556.
- Mudeme, S., et al. (2010) Kinetics of Emulsification and Rheological Properties of Highly Concentrated Explosive Emulsions, Chemical Engineering and Processing: Process Intensification, 49, p. 468. doi.org/10.1016/j.cep.2010.03.012.
- Zhang, K M & Ni, O Q (2015) Rheological properties and stability of emulsion explosive matrix, Journal of Dispersion Science and Technology, 36, p. 932. doi.org/10.1080/01932691.2014.942315.
- Pal, R (2003) Viscous behavior of concentrated emulsions of two immiscible Newtonian fluids with interfacial tension, Journal of Colloid and Interface Science, 263, p. 296. doi.org/10.1016/S0021-9797(03)00125-5.
- Pal, R (2002) Novel shear modulus equations for concentrated emulsions of two immiscible elastic liquids with interfacial tension, Journal of Non-Newtonian Fluid Mechanics, 105, p. 21. doi.org/10.1016/S0377-0257(02)00058-7.
- Zhang, K M & Ni, O Q (2015) Rheological properties and stability of highly concentrated water-in-oil emulsions with different emulsifiers, Journal of Dispersion Science and Technology, 36, p. 549. doi.org/10.1080/01932691.2014.916621.
- Wang, L Q & Fang, J (2013) Rheological Properties and Water-in-Oil Structural Stability of Emulsion Matrixes, Central European Journal of Energetic Materials, 10, p. 87. doi.org/10.1080/01932691.2014.942315.
- Zhang, K M & Ni, O Q (2015) Effect of PIBSA-based surfactants on the interfacial interaction, rheology and stability of highly concentrated water-in-oil emulsion, Journal of Dispersion Science and Technology, 36, p. 555. doi.org/10.1016/j.etap.2015.01.017.
- Masalova, I & Malkin, A Ya (2007) Rheology of Highly Concentrated Emulsions - Concentration and Droplet Size Dependencies, Applied Rheology, 17, p. 42250. doi.org/10.1515/arh-2007-0011.
- Foudazi, R., et al. (2012) The rheology of binary mixtures of highly concentrated emulsions: Effect of droplet size ratio, Journal Rheology, 56, p. 1299. doi.org/10.1122/1.4736556.
- Yakhoub, H. A. et al. (2011) Highly concentrated emulsions: Role of droplet size, Chemical Engineering Communications, 198, p. 147.
- Princen, H (1983) Rheology of foams and highly concentrated emulsions: I. Elastic properties and yield stress of a cylindrical model system, Journal of Colloid and Interface Science. 91, p. 160. doi.org/10.1016/0021-9797(83)90323-5.
- Princen, H & Kiss, A (1986) Rheology of foams and highly concentrated emulsions: III. Static shear modulus, Journal of Colloid and Interface Science, 112, p. 427. doi.org/10.1016/0021-9797(86)90111-6.
- Lacasse, M.D., et al. (1996) Model for the elasticity of compressed emulsions, Physics Review Letters, 76, p. 3448. doi.org/10.1103/physrevlett.76.3448.
- Kovalchuk, K., et al. (2010) Influence of electrolyte on interfacial and rheological properties and shear stability of highly concentrated W/O emulsions, Colloid Journal, 72, p. 806. https://doi.org/10.1134/S1061933X10060116.
- Mason, T. G & Bibette, J (1997) Shear rupturing of droplets in complex fluids, Langmuir, 13, p. 4600. doi.org/10.1021/la9700580.
- Mason, T. G & Bibette, J (1996) Emulsification in Viscoelastic Media. Physics Review Letters, 77, p. 3481. doi.org/10.1103/physrevlett.77.3481.
- Farr, R S & Groot, R D (2009) Close packing of polydisperse hard spheres. The Journal of Chemical Physics, 131, p. 244104. doi.org/10.1063/1.3276799.
- Malkin, A. Ya., et al. (2004) Effect of droplet size on the rheological properties of highly-concentrated w/o emulsions. Rheologica Acta, 43, p. 584. doi.org/10.1007/s00397-003-0347-2.
- Masalova, I & Malkin, A. Ya (2007) Peculiarities of rheological properties and flow of highly concentrated emulsions: The role of concentration and droplet size. Colloid Journal, 69, p. 185. doi.org/10.1134/S1061933X0702007X.
- Zhang, K. M., et al. (2018) Peculiarities of rheological behavior of highly concentrated water-in-oil emulsion: The role of droplet size, surfactant, oil and ammonium nitrate content. Journal of Molecular Liquids, 272, p. 539. doi.org/10.1016/j.molliq.2018.09.091.
- Tshilumbu, N N & Masalova, I (2015) Stabilization of highly concentrated emulsions with oversaturated dispersed phase: Effect of surfactant/particle ratio. Chemical Engineering Research and Design, 102, p. 216. doi.org/10.1016/j.cherd.2015.06.025.
- Xu, Z. X., et al. (2013) Investigation of ammonium nitrate-based emulsion ignition characteristic. Journal of Loss Prevention in the Process Industries, 26, p. 994. doi.org/10.1016/j.jlp.2013.10.005.
- Xu, Z X., et al. (2010) Influence of iron ion on thermal behavior of ammonium nitrate and emulsion explosives. Central European Journal of Energetic Materials, 7, p. 77.
- Wu, Q. J., et al. (2018) Ab initio calculations, structure, NBO and NCI analyses of Xsingle bond π interactions. Chemical Physics Letters, 36, p. 202. doi.org/10.1016/j.cplett.2018.01.015.
- Masalova, I. R., et al. (2011) The rheology of highly concentrated emulsions stabilized with different surfactants. Colloids and Surfaces A: Physicochemical and Engineering Aspects, 375, p. 76. doi.org/10.1016/j.colsurfa.2010.11.063.
- Masalova, I., et al. (2011) IR Studies of Interfacial Interaction of the Succinic Surfactants with Different Head Groups in Highly Concentrated W/O Emulsions. Journal of Dispersion Science and Technology, 32, p. 1547. https://doi.org/10.1080/01932691.2010.516412.
- Tshilumbu, N. N., et al. (2014) Effect of Nanoparticle Hydrophobicity on Stability of Highly Concentrated Emulsions. Journal of Dispersion Science and Technology, 35, p. 283. doi.org/10.1080/01932691.2013.775584.
- Foudazi, R., et al. (2015) Physical chemistry of highly concentrated emulsions. Advances in Colloid and Interface Science, 220, p. 78. doi.org/10.1016/j.cis.2015.03.002.
- Seth, J. R., et al. (2006) Elastic properties of soft particle pastes. Journal of Rheology, 50, p. 353. doi.org/10.1122/1.2186982.
- Bonnecaze, R T & Cloitre, M (2017) Micromechanics of Soft Particle Glasses. Advances in Polymer Science. 236, p. 117. https://doi.org/10.1007/12_2010_90.
- Palierne, J F (1990) Linear rheology of viscoelastic emulsions with interfacial tension, Rheology. Acta, 29, p. 204. https://doi.org/10.1007/BF01331356.
- Derkach, S R (2009) Rheology of emulsions. Advances in Colloid and Interface Science, 151, p. 1.
- Huber, K (1991) Interactions in mixed interfaces of binary surfactant solutions. Journal of Colloid Interface Sciences, 147, p. 321. doi.org/10.1016/0021-9797(91)90164-4.
- Huibers, P & Shah, D (1997) Evidence for synergism in nonionic surfactant mixtures: enhancement of solubilization in water-in-oil microemulsions, Langmuir, 13, p. 5762. doi.org/10.1021/la962108r.
- Fu, Z., et al. (2010) Stabilization of water-in-octane nanoemulsion. Part I: Stabilized by mixed surfactant systems. Fuel, 89, p. 2838. doi.org/10.1016/j.fuel.2010.05.031.
- Derkach, S. R., et al. (2011) The role of the cationic surfactants in concentrated emulsions stabilized with globular protein. Colloids and Surfaces A: Physicochemical and Engineering 391, p. 105. doi.org/10.1016/j.colsurfa.2011.09.010.
- Reynolds, P.E., et al. (2012) High internal phase water-in-oil emulsions studied by small-angle-scattering. Journal of Physical Chemistry B, 104, p. 7012. doi.org/10.1021/jp000327m.
- Reynolds, P. A., et al. (2001) High internal phase water-in-oil emulsions and related microemulsions studied by small angle neutron scattering. Journal of Physical Chemistry B, 105, p. 6925. doi.org/10.1021/jp010349o.
- Myers, D (2006) Surfactant science and technology, third ed., John Wiley & Sons, Inc., Hoboken, New Jersey.
- Israelachvili, J N (1992) Intermolecular and surface forces, Academic, London.
- Birdi, K.S., (2008) Handbook of surface and colloid chemistry, CRC Press.
- Tadros, T F (2009) Emulsion science and technology: a general introduction. Emulsion Science and Technology. Weinheim, Wiley-VCH, 2009, 1.
- Foudazi, R. I., et al. (2010) The Role of Interdroplet Interaction in the Physics of Highly Concentrated Emulsions. Colloid Journal, 72, pp. 74–92. doi.org/10.1134/S1061933X10010102.
- Foudazi, R (2010) Effect of interdroplet interaction on elasticity of highly concentrated emulsions. Applied Rheology, 20, p. 45096. doi.org/10.3933/ApplRheol-20-45096.
- Foudazi, R I., et al. (2011) Flow behavior of highly concentrated emulsions of supersaturated aqueous solution in oil. Rheologica Acta, 50, p. 897. https://doi.org/10.1007/s00397-010-0505-2.
- Masalova, I., et al. (2018) Shear Stability of Highly Concentrated Emulsions. Colloids Journal, 80, p. 54. doi.org/10.1134/S1061933X18010064.
- Masalova, I., et al. (2018) Emulsification of highly concentrated emulsions-A criterion of shear stability. Journal of Rheology, 62, p. 781. https://doi.org/10.1122/1.5018794.
- Zhang, K M., et al. (2018) Study on the flow of highly concentrated emulsions. Journal of Dispersion Science and Technology, 39, p. 1285. https://doi.org/10.1080/01932691.2017.1394198.
- Masalova, I., et al. (2008) Yield Stress of Emulsions and Suspensions as Measured in Steady Shearing and in Oscillations. Applied Rheology, 18, p. 44790. doi.org/10.1515/arh-2008-0013.
- Masalova, I., et al. (2008) Yield stress as measured in steady shearing and in oscillations. Applied Rheology, 18 (4): 44790. doi.org/10.3933/ApplRheol-18-44790.
- Malkin, A. Ya & Masalova, I (2007) Shear and normal stresses in flow of highly concentrated emulsions. Journal of Non-Newtonian Fluid Mechanics, 147, p. 65. doi.org/10.1016/j.jnnfm.2007.07.003.
- Zhao, H R & Zhang, K M (2018) The structure recovery capacity of highly concentrated emulsions under shear flow via studying their rheopexy. Journal of Dispersion Science and Technology, p. 970. doi.org/10.1080/01932691.2017.1379017.
- Minale, M (2010) Models for the deformation of a single ellipsoidal drop: A review. Rheology Acta, 49, p. 789. doi.org/10.1007/s00397-010-0442-0.
- Jackson, N & Tucker III, C (2003) A model for large deformation of an ellipsoidal droplet with interfacial tension. Journal of Rheology, 47, p. 659. doi.org/10.1122/1.1562152.
- Jansen, K.M.B., et al. (2001) Droplet breakup in concentrated emulsions. Journal of Rheology, 45, p. 227. doi.org/10.1122/1.1333001.
- Sanatkaran, N & Masalova, I (2015) Interfacial Behavior of Oil/Oil and Oil/Water Soluble Binary Surfactants and Their Effect on Stability of Highly Concentrated W/O Emulsions. Colloid Journal, 77, p. 77. doi.org/10.1134/S1061933X15010135.
- Sanatkaran. N., et al. (2014) Effect of surfactant on interfacial film and stability of highly concentrated emulsions stabilized by various binary surfactant mixtures. Colloids and Surfaces A: Physicochemical and Engineering Aspects, 461, p. 85. doi.org/10.1016/j.colsurfa.2014.07.031.
- Kovalchuk, K & Masalova, I (2011) Factors influencing the crystallisation of highly concentrated water-in-oil emulsions: A DSC study. South African Journal of Science, 108, p. 1. doi.org/10.4102/sajs.v108i3/4.178.
- Taylor, P., et al. (1995) Ostwald ripening in emulsions, Advances in Colloid and Interface Science. 99, p. 175. doi.org/10.1016/S0001-8686(98)00035-9.
- Bibette, J (1992) Stability of thin films in concentrated emulsions. Langmuir, 8, p. 3178. doi.org/10.1021/la00048a053.
- Masalova, I & Kharatyan, E (2013) Effect of Silica Particles on Stability of Highly Concentrated Water-In-Oil Emulsions with Non-Ionic Surfactant. Colloid Journal, 75, p. 95. doi.org/10.1134/S1061933X13010079.
- Masalova, I & Malkin, A Ya (2007) A new mechanism of aging of highly concentrated emulsions: correlation between crystallization and plasticity. Colloid Journal, 69, p. 198. doi.org/10.1134/S1061933X07020081.
- Masalova, I., et al. (2006) Evolution of rheological properties of highly concentrated emulsions with agingemulsion-to-suspension transition. Journal of Rheology, 50, p. 437. doi.org/10.1122/1.2206712.
- Zhang, K. M., et al. (2017) Storage modulus’ variation in aging and its application in assessing the stability of emulsion explosive matrix. Journal of Dispersion Science and Technology, 38, p. 1517. doi.org/10.1080/01932691.2016.1225507.
- Kovalchuk, K., et al. (2012) A Computational Study of the Succinimide Derivative Surfactant. Journal of Dispersion Science and Technology, 34, p. 778. doi.org/10.1080/01932691.2012.695955.
- Tshilumbu, N. N., et al. (2010) Masalova, Instability of highly concentrated emulsions with oversaturated dispersed phase. Role of a surfactant. Colloid Journal, 72, p. 569. doi.org/10.1134/S1061933X10040204.
- Masalova, I., et al. (2013) Multi-Walled Carbon Nanotubes as a Cosurfactant for Highly Concentrated Emulsions. Journal of Dispersion Science and Technology, 34, p. 1074. .doi.org/10.1080/01932691.2012.735960.
- Zhang, K. M., et al. (2018) A facile and efficient method to investigate the effect of the nature of surfactant and continuous phase on the performance of emulsion explosive. Journal of Molecular Liquids, 249, p. 203. doi.org/10.1016/j.molliq.2017.10.149.
- Ni, O.Q., et al. (2012) Tang, Powdery emulsion explosive: a new excellent industrial explosive. Journal of Energetic Materials, 30, p. 183. doi.org/10.1080/07370652.2010.550599