Sponsored by PerkinElmerReviewed by Maria OsipovaAug 30 2022
When two or more different materials or elements are combined, a composite material is created. The composite material has special qualities that set it apart from its separate constituents due to the mixing of various constituents.
Composites are utilized in a wide range of industries, such as aerospace, automotive, battery production, energy wind turbine blades, and others. Automobile bodies, bumpers, and other automotive components are among the applications for composites. They are also used in sports, medicine, and other industries.
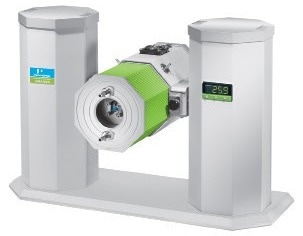
PerkinElmer DMA 8000. Image Credit: PerkinElmer
Due to their advantages in terms of cost and weight, composites have become increasingly popular in the automobile sector. Composites are being used by automakers to improve energy efficiency and reduce pollution.
Given the range of uses for which composite materials are employed, it is particularly crucial to have a solid grasp of their material characteristics, such as glass transition and cure behavior.
Experimental
In this article, a powder-filled, epoxy-based composite material is examined. Information about the material’s cure and glass transition can be obtained through a multi-frequency thermal scan.
After increasing the temperature above the cure temperature, an isothermal experiment is also performed. This latter experiment provides information on exceptional frequency dependence.
One of the best techniques for examining relaxation events is Dynamic Mechanical Analysis (DMA). By definition, a composite consists of multiple components. From complex aeronautical polymer composites to glass fiber reinforced concrete, different applications use different composite materials.
In these experiments, an epoxy polymer composite loaded with powder was used, which was recommended for use in battery production.
The material is subjected to an oscillating force using the PerkinElmer DMA 8000, and the sample's resulting displacement is then measured. It allows for the determination of stiffness and the calculation of tan δ.
Tan δ is the proportion of storage to loss in a system. The damping qualities of the material can be ascertained by measuring the phase lag between the displacement and the applied force. Tan δ is plotted against temperature, and since the material will absorb energy as it passes through the glass transition, a peak is usually seen when the glass transition is underway.
Since the composite is made of epoxy, the glass transition is not as easy as it might seem because a cure process is also taking place. The findings from the thermal scan and isothermal cure are both explained.
- Multi-frequency temperature scan of composite. The single cantilever bending clamps were used to hold the sample while it was subjected to multiple frequencies of temperature scanning.
- Isothermal frequency scan of composite. The single cantilever bending clamps were attached with a new sample, which was then immediately heated to 100 °C. Data on modulus and tan δ were gathered for three hours.
Source: PerkinElmer
Equipment |
Experimental Conditions |
DMA 8000 1L Dewar |
Sample: |
Composite Material |
Geometry: |
Single Cantilever Bending |
Dimensions: |
9.7 (l) x 10.1 (w) x 1.7 (t) mm |
Temperature: |
(1) 25 °C to 250 °C at 3 °C/minute-1
(2) Isothermal at 100 °C |
Frequency: |
0.316, 1.0, 3.16, 10.0 and 31.6 Hz |
Results and Conclusion
The thermal scan of the composite material is illustrated in Figure 1. Both the modulus and the tan δ data show a clear frequency dependency, which points to a relaxation event. A cure reaction also occurs when the material moves through the Tg.

Figure 1. Thermal scan data of composite material. Image Credit: PerkinElmer
Despite the curing process being complete, the Tg and rising temperature cause the material to become less stiff (modulus to decrease). The frequency dependence is as expected, with higher frequencies giving higher glass transition temperatures. Tg is approximately 92 °C at 1 Hz.
Figure 2 shows a graph of the isothermal experiment’s outcome. The experiment was conducted at 100 °C, which was a little higher than the Tg from the first experiment.
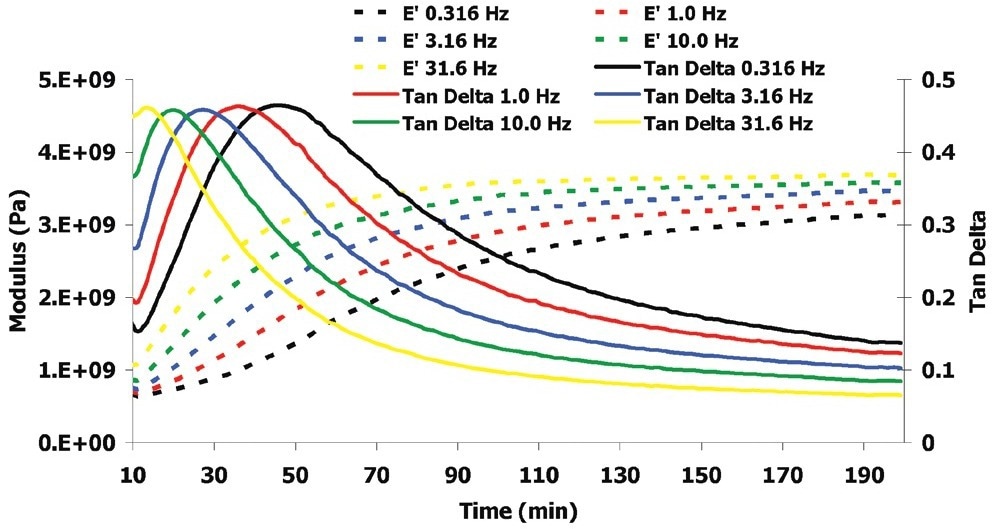
Figure 2. Isothermal experiment results. Image Credit: PerkinElmer
The glass transition and the curing process are both visible in the tan δ peak. The higher frequency peak appears to occur first, suggesting that the frequency dependency is different from that seen in the previous experiment.
Figure 2 displays the isothermal experiment findings, which depend on time rather than temperature. The epoxy curing process will be the main phenomenon seen in this data. The duration of relaxation will increase as the cure develops. When the relaxation time is nearly the same as the probing frequency, a maximum in tan δ will be seen.
As a result, the short relaxation time will cause the high-frequency event (shortest probing frequency) to occur first. When enough healing has occurred to lengthen the relaxation duration appropriately, the lowest frequency peak occurs.
Summary
In this article, a powder-filled, epoxy-based composite material is studied. Details about the material’s cure and glass transition can be obtained through a multi-frequency thermal scan.
After increasing the temperature above the cure temperature, an isothermal experiment is also discussed. This latter experiment gives unusual frequency dependence information. Due to the various purposes for which composite materials are utilized, the glass transition and cure behavior are of particular significance.
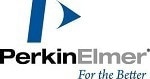
This information has been sourced, reviewed and adapted from materials provided by PerkinElmer.
For more information on this source, please visit PerkinElmer.