Sponsored by ParathermReviewed by Olivia FrostFeb 13 2023
There is frequently a great deal of uncertainty and misinformation around heat transfer systems, including their proper use and maintenance, causing dread and anxiety among system operators.
This fear is frequently increased when systems develop an issue after years of flawless functioning. When problems occur, there are frequently incorrect explanations or assumptions about how the system should function or what fluid should be utilized.
Using a flammable liquid at elevated temperatures and moderate pressures in thermal fluid systems necessitates a degree of judgment. It is essential to be educated on correct operation and maintenance and fluid selection criteria to limit the likelihood of mishaps and avoid spreading false information.
Demystifying Thermal Fluid Properties
All major producers of thermal fluids offer technical data sheets highlighting vital fluid qualities. Depending on the source, some of these data sheets may contain only four or five critical qualities, while others may be extensive technical reports that include pages of information.
All attributes have their place in practice, but the following explanations will help demystify several commonly used terminology.
Maximum fluid temperatures
Every heat transfer fluid product advisory lists a maximum recommended operating and film temperature. A heat transfer fluid should not be used if the datasheet does not state that it is specifically intended for heat transfer service.
The maximum suggested film temperature is often established using industry-standard stability testing, and many manufacturers set the maximum operating temperature by deducting 50 °F from that value.
Through a thin, comparatively motionless sheet of fluid, heat is transferred from the heat source (heater tube, electric element, or steam coil) into the moving fluid (bulk flow).
The bonds binding the molecules together begin to break down, and the fluid will deteriorate if the temperature of this fluid film is higher than the highest recommended film temperature. However, the average and maximum film temperatures are present on every heater.
By dividing the average heat flux (Btu/hr-ft2) by the fluid film coefficient (Btu/hr-ft2 -°F), and adding that result to the operating temperature, one can estimate the average film temperature.
The maximum film temperature will closely follow the average if the heater has a uniform heat flux (steam coils, an electric element, or flue gas heat recovery, for example). However, a radiant section of practically all fired heaters can provide a substantially larger heat flux.
This may cause localized film temperatures to be significantly higher than the heater's average. Temperature variations between bulk and film temperatures can reach as high as 100 °F, depending on the fired-heater design.
This indicates that fluid life may be shortened if the required operating temperature is within 60 to 75 °F of the heat transfer fluid's stated maximum film temperature.
Minimum fluid temperatures
Depending on the manufacturer, minimum fluid temperatures are often stated as minimum operating temperature, start-up temperature, pumpability, and pour point.
The lowest temperature that any processing element may endure is the most important factor to consider. Depending on the environment, the circulation pump must be able to move fluid at its maximal viscosity; otherwise, heat tracing may be necessary.
Centrifugal pumps, normally only effective for viscosities below 400 centipoises (cPs), are used in most heat transfer systems. As a result, this frequently establishes the low-temperature limit. It is crucial to consider the temperature corresponding to the minimal viscosity where a fluid will effectively transmit heat if it is utilized for cooling and heating.
The maximum design viscosity for most equipment is close to 20 cPs. As a result, this typically determines the lowest operating temperature.
Coefficient of thermal expansion
This crucial characteristic will help scientists predict how the thermal fluid's volume will change as it heats up. The system could overflow at its maximum operating temperature if the expansion design does not consider a suitable expansion volume. The volumetric expansion rate for most hydrocarbon thermal fluids is 4–6% per 100 °F.
Flash point
A flash point is a frequently examined property after an incident. Reviewers of the occurrence frequently conclude that the fire started because the fluid's flash point is lower than its operating temperature. However, this is typically untrue.
Thermal fluids are frequently employed above their flash points because well-designed systems rarely have the circumstances necessary for a fluid to flash simultaneously. According to the fire triangle, oxygen, fuel, and an ignition source are necessary for a flash (fire) to occur.
An external ignition source must start a flash unless the fluid operates above its autoignition temperature. Moreover, oxygen is only ever present in vented expansion tanks or reservoirs operating much below the fluid's flash point.
Thermal fluid fires are extremely uncommon, and when they do happen, it is nearly always because of subpar maintenance procedures or broken equipment.
Table 1. Secondary properties of heat transfer fluids. Source: The Lubrizol Corporation
Property |
Significance |
Meaning |
Viscosity |
Moderate |
Most hydrocarbon thermal fluids are relatively low viscosity, which is better for flow mechanics and heat transfer efficiency |
Density |
Low to moderate |
Higher densities are favorable for heat transfer efficiency. Synthetic fluids often have a higher density than mineral oils, giving them a slight efficiency edge |
Moisture |
Moderate |
High water content can create severe headaches at extreme temperatures. Most heat transfer fluids have moisture levels below 300 ppm when new |
Vapor pressure |
Low |
Vapor pressure is directly related to the boiling range of the fluid. Most heat transfer fluids have very low vapor pressures and high boiling ranges even up to their maximum use temperatures |
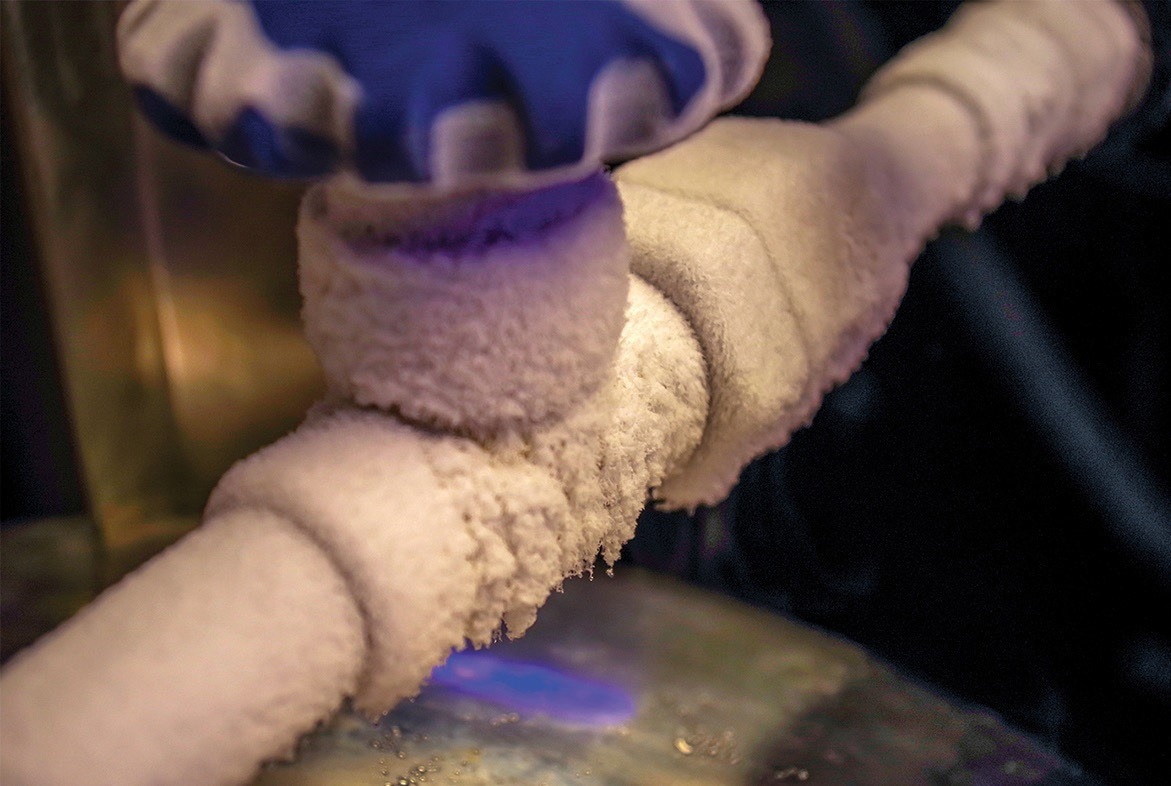
Figure 1. When selecting an appropriate heat transfer fluid, the ambient environment of the system must be accounted for. If any of the system is located outdoors, low temperature startup conditions may apply. Image Credit: The Lubrizol Corporation
Other properties
Table 1 lists additional characteristics frequently mentioned in technical data sheets, along with their respective importance. Due to their importance in the fluid selection process, most of these characteristics might be regarded as secondary.
The secondary attributes are the natural manifestation of the fluid's temperature capabilities because reputable heat transfer suppliers have already established suitable operating limits for their fluids.
The manufacturer-recommended temperature limits are the most crucial characteristics of the heat transfer fluid. All other characteristics are often taken into account in the equipment design if the fluid is capable of operating at the design temperatures of the operation.
According to the acceptable operating range, chemical compatibility, and physical criteria for other system components, the replacement fluid for systems already in use should be equal to or substantially identical to the original fluid (heater, pumps, valves, etc.).
Demystifying Heat Transfer System Operation
Because thermal fluid systems often function dependably until a catastrophic failure of the fluid or equipment occurs, they are frequently overlooked or forgotten about. Catastrophic failure can be avoided, such as with other process equipment, by following a proper preventative maintenance schedule and having sound operational understanding.
The following tips may be invaluable for the heat transfer practitioner.
Charging the System
All control valves, block valves, and high-point vents should be opened wherever possible. To fill from the bottom up, a tiny positive-displacement pump should be connected as close as feasible to the pump suction. Filling from the bottom will significantly reduce the entrainment of air, which is a common reason for pump cavitation.
The fluid should be injected to prevent pump damage until the expansion tank is roughly halfway filled. The block valve should be throttled to 25% on the main pump discharge for cold circulation. If the pump begins to cavitate or the low-level switch trips, more fluid can be injected as necessary.
The pump can be opened to discharge to around 50% after fluid flows steadily through the entire system.
The system is full when the pump discharge pressure is constant at 100% flow. When the system is at its typical working temperature, the expansion tank should be topped out as necessary to maintain a level between 66-75%.
System Contaminants
In contrast to older systems, which may include degradation by-products (carbon, sludges, varnishes, etc.) circulating with the fluid, new systems may contain contaminants from production and installation. Upstream of the pump, a typical 60-mesh strainer may remove several impurities.
A side-stream filtration loop that continuously removes pollutants and degradation byproducts will also help most systems in the long term. Making sure the components are rated for the process temperatures is crucial.
The exceptions to this rule is water, which is usually added during "hydrotesting" of the apparatus, temperature cycling in vented systems, or through a leaky heat exchanger. Boiling the water out of the system to vaporize the moisture is the most efficient approach to eliminate water.
This may be challenging depending on how the system is set up. To learn more about how to do this, it is advisable to speak with the heater's original equipment manufacturer (OEM) or the fluid provider.
System startup and shutdown
The thermal fluid and equipment may degrade quickly and prematurely due to improper system setup and shutdown. As temperature rises, the viscosity of all thermal fluids decreases. The fluid's efficiency dramatically rises as it becomes thinner.
Most high-temperature thermal fluids have viscosities greater than 10 cPs and are inefficient at temperatures below 100 °F.
When the system starts up, this cold fluid is less able to move and absorb heat from the heater tubing than when it is heated. The fluid coating at the heated surface may start to break if the temperature rises too quickly, harming the fluid at the molecular level.
If the system repeatedly cycles between on-duty and off-duty states, this harm will recur with each restart. It is advised to start the system whenever it is chilly and to gradually increase the heater setpoint by 10 to 20 °F until the fluid reaches turbulent flow.

Figure 2. Multi-pass helical coil-fired heaters are widely used in heat transfer applications for their thermal efficiency. Ensure that the maximum temperature ratings on the fluid can handle the radiant heat generated inside the firebox for all fired heater designs. Image Credit: The Lubrizol Corporation
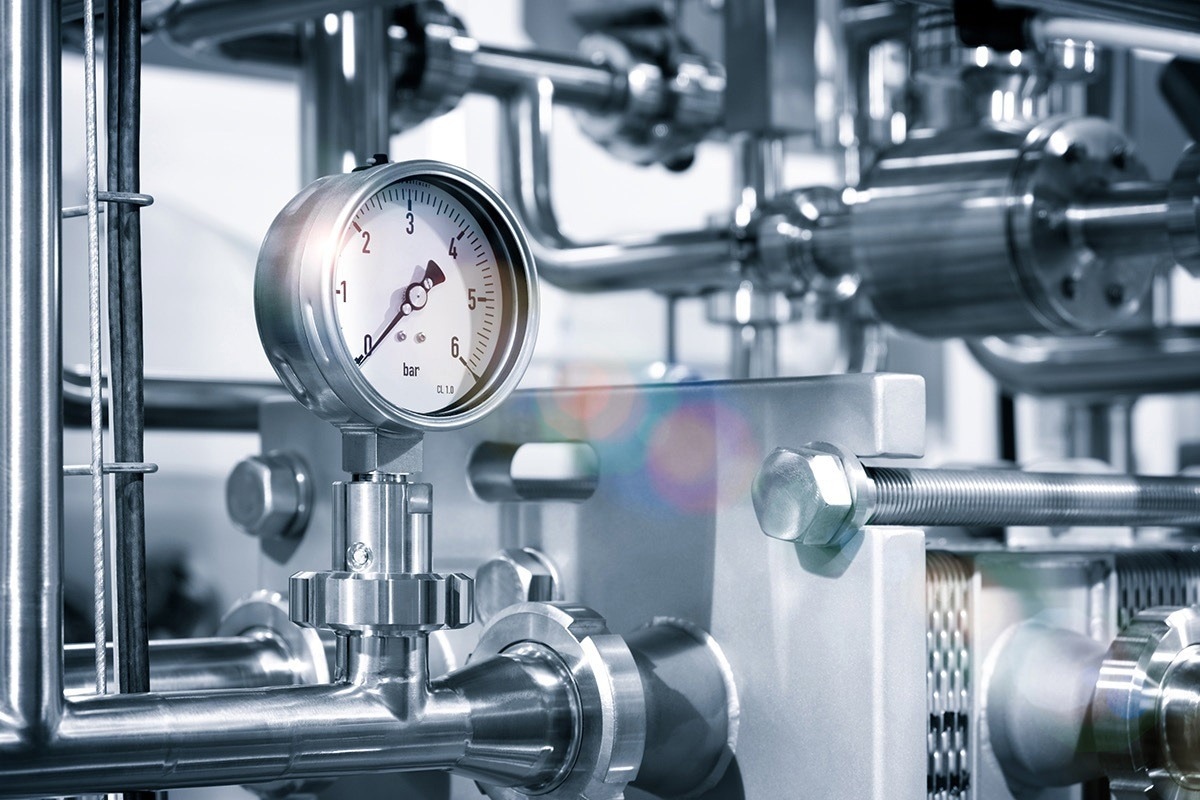
Figure 3. Pressure gauges are an invaluable and inexpensive tool for monitoring the system's performance. Take care to protect the gauges by installing sufficient tubing to dissipate heat. Image Credit: The Lubrizol Corporation
The refractory and structural metal of the heater will become almost as hot as the flame itself while it is in use. The heater will stop blazing, and the pump will stop if the complete system is turned off.
Heater tubing is scorched and the thermal fluid inside is cooked by the extreme heat trapped in the heater's refractory and structural metal, which cannot immediately leave the firebox. Turning off the heater while running the circulating pump while turning the system off is crucial.
It is typically safe to turn off the pump when the heater outlet temperature reaches 200 °F or less. It is advised to keep the heater blower on if feasible. Heat may be swiftly expelled from the stack by blowing cool air into the firebox.
Simple instrumentation
Pressure gauges can monitor helpful information for troubleshooting even when they do not supply the data for actual flow calculations. For instance, a compound pressure/vacuum gauge fitted on the pump suction can identify a Y-strainer obstruction before it becomes a significant issue.
Similarly, pressure gauges on a heat user's intake and exit lines can quickly identify a broken control valve. Pressure gauges can also be employed for a few tasks that are essential to the system's overall efficiency.
For instance, a three-way control valve on the bypass leg can equalize the user pressure drop if multiple users are on a loop.
Pressure gauges should be located at the end of the supply header, at the start of the return header, the heater's input and outlet, the pump's suction and discharge, and before and after each heat user (between the control valve and the user).
Always install pressure gauges with enough connecting tubing for heat dissipation. It is advised that a block valve should be installed so that the gauge can be easily removed for maintenance or solids purging.
Fluid analysis
Hot oil horror stories occur when the fluid is not routinely analyzed. Regular analysis can detect mechanical faults before they have catastrophic effects and evaluate the fluid's quality.
It is highly recommended to analyze the heat transfer fluid with the provider at least once a year. The study should be unique to heat transfer fluid and should explain the fluid's condition and pertinent recommendations for the next steps.
Conclusion
This article should enhance a heat transfer practitioner's knowledge of systems and fluids. Examining the candidate fluid's datasheets is essential to ensure that vital properties are provided and suitable for the operating conditions.
When it comes to system functioning, the rules for charging the system and the startup and shutdown protocols must be adhered to. Where necessary, filters and instruments should be installed, and the fluid should be analyzed annually to monitor its critical qualities.
Considering these factors, the fluid and the system will continue to operate without serious issues.
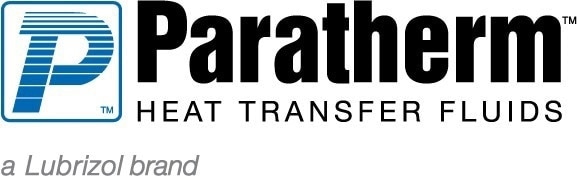
This information has been sourced, reviewed and adapted from materials provided by The Lubrizol Corporation.
For more information on this source, please visit The Lubrizol Corporation.