Sponsored by ParathermReviewed by Olivia FrostMay 8 2024
When replacing heat transfer fluid that has reached the end of its lifespan, you must consider both time and financial costs. Key factors include process downtime (covering cooling, draining, and refilling), labor costs (including the need for personal protective equipment), disposal fees, and the price of the new fluid.
Since many fluids are compatible enough for a simple drain and fill, always verify compatibility with your new fluid supplier before proceeding.
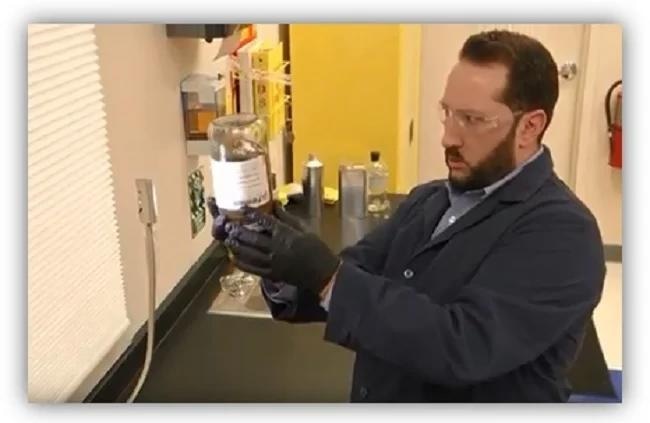
Figure 1. Replacing fluid that has reached the end of its life with the same brand or a different brand requires an important decision.
Image Credit: Paratherm
Cold Spots
Consider using a system cleaner if you notice cold spots in the system. Lines that are completely plugged might need to be replaced or purged at very high pressure. Non-aqueous cleaners are typically effective for partially blocked lines with some flow.
There are two types of cleaners: additive cleaners, which can be added to the existing fluid and allow the system to operate while cleaning, and off-line cleaners, which are faster but require the system to be shut down and include an additional flushing step to remove the cleaner after use. Always ensure the cleaner is compatible with your fluid.
Fluid Removal
Often, drains are located at low points of the piping, so the fluid can easily be drained or pumped out. If not, flanges may need to be broken, pressure taps opened, and valves/flex hoses/other components removed from the piping to ensure fluid removal.
Using compressed nitrogen to force the fluid out of one end of a loop is difficult to implement but is an effective method.
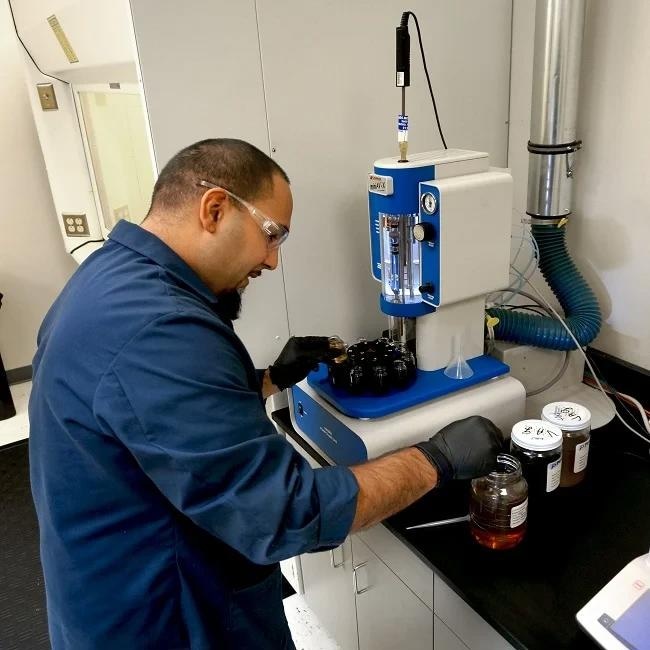
Figure 2. Shut the heater down and continue to run the pump until the fluid has cooled.
Image Credit: Paratherm
Draining the system warm or hot will leave less residual fluid and solids in the lines than if it is drained cold. The heater should be shut down, and the pump run until the fluid has cooled to between 150 °F and 180 °F, then drained as quickly as possible.
Flushing Fluids
Flushing fluids are usually liquids with a high solvent content whose purpose is to dilute liquid that is too viscous at an ambient temperature to completely drain from the system.
Unlike cleaners, flushing fluids will not remove system deposits. They also require two additional steps because the flushing fluid must be removed from the system to prevent premature degradation of the new heat-transfer fluid.
The new fluid supplier should be able to tell whether or not it needs to be flushed.
Generally, new systems do not need to be flushed before filling. The main contaminants in a new system are usually leftovers such as metal particles, shop rags, and welding slag. These can be removed using a 60-mesh start-up strainer during initial circulation.
In new piping, the amount of soluble contaminants such as lacquers, oils or other metal coatings present is very small relative to the system volume. Failing to completely flush out the flushing fluid can significantly reduce the lifespan of the heat transfer fluid. Additionally, this oversight can lead to increased operational time and higher disposal costs.
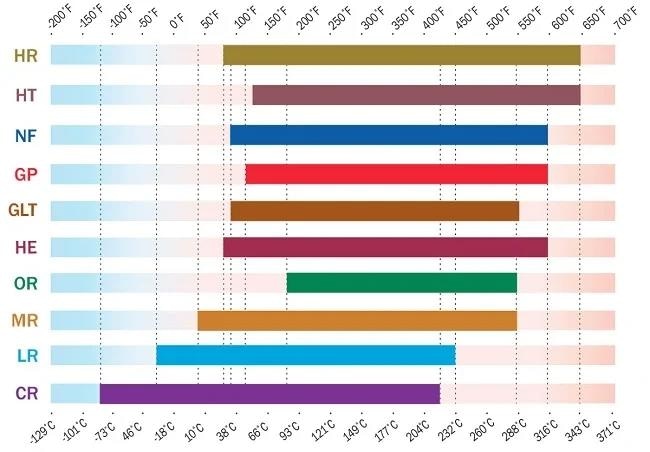
Figure 3. In new piping, the amount of soluble contaminants such as lacquers, oils or other metal coatings present is very small relative to the system volume.
Image Credit: Paratherm
Charging and Initial Run
The main circulating pump should not be used to change the fluid; this can damage the seals. Instead, a stainless braided Teflon hose should connect a small positive displacement pump close to the main pump section.
All control and block valves and high-point vents should be opened, and a bucket should be placed under vents to catch any fluid running out.
If there is no de-aerator in the system, the warm-up valve to the expansion tank should be open. Fluid should be added until the expansion tank is about half full; if the tank level is hard to determine, look for overflow from its vent.
Next, the main pump discharge block valve should be closed, the pump started, and the block valve opened to a quarter of the total flow.
More fluid should be added as needed when the pump starts to cavitate or the low-level switch trips. Once the fluid is circulating steadily through the system, the discharge pump should be opened by another small increment, and more fluid added as necessary.
The system is full when the pump runs steadily with the block valve fully opened. Check all the high-level vents to ensure the lines are filled. Add fluid to reach the proper level in the expansion tank.
Start-Up
When it turns to steam, just 7 ounces of water can forcefully expel 55 gallons of potentially very hot fluid through the expansion tank vent. Therefore, it is crucial to approach every cold startup—whether in new or existing systems—with the understanding that water may be present.
While draining low points on the piping system can remove large amounts of water, the only method to completely remove water is to flash it as steam through the expansion tank vent as quickly as possible.

Figure 4. Heat transfer fluid analysis kit.
Image Credit: Paratherm
The system is full when the pump runs steadily with the block fully open. All the lines should be filled in the high-level vents and fluid should be added to reach the proper level in the tank.
The expansion tank temperature must be maintained at over 212 °F, and condensation inside the tank must be minimized.
The most effective setup to use is warm-up/vent lines which run from the heater outlet to the tank. De-aerators can thoroughly separate air and other non-condensing gases from fluid but cannot vent gases that condense, such as steam.
The heater or fluid manufacturer should be contacted if a user is unsure how to boil out the system.
Before Start-Up
The end of the pipe must be visible if the expansion tank vent discharges into a catch tank. The system catch tank should be totally empty.
The manual valve on the expansion tank vent line must be opened. If there is a nitrogen blanket, the inlet pressure control vent should be set as low as possible to provide a continuous purge, preventing oxidation and speeding up water removal.
All control valves should be opened, and welding blankets should be placed on top of the expansion tank to reduce condensation.
After the heater is started, the set point should be increased slowly to 220 °F. Signs that water is in the fluid include pump noise/pressure fluctuations, crackling/popping noises, and sudden level changes in the tank.
Steam should come out of the vent; when this stops, the outlet temperature should be increased by 3 °F. Temperature should be increased at 3 °F increments until it reaches 220 °F and pressure is steady.
The warm-up valve should now be closed, and the heater temperature should be increased to the desired operating temperature.
The fluid level must be checked, and the vent closed if there is a nitrogen blanket. Any insulation on top of the tank should be removed, and fluid should be drained from the low points in the expansion and thermal buffer tank. After checking for water, the process is complete.
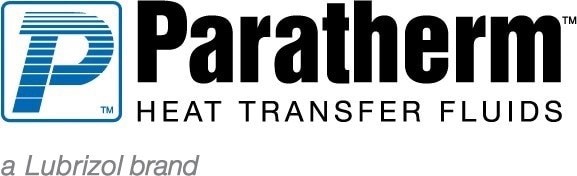
This information has been sourced, reviewed and adapted from materials provided by Paratherm.
For more information on this source, please visit Paratherm.