Researchers from Cranfield University recently investigated the high-temperature performance of Inconel 718, a superalloy that is widely used in aerospace engine components. This article explores the study, the potential of wire arc additive manufacturing in producing Inconel 718, and how heat treatment can improve its high-temperature performance.
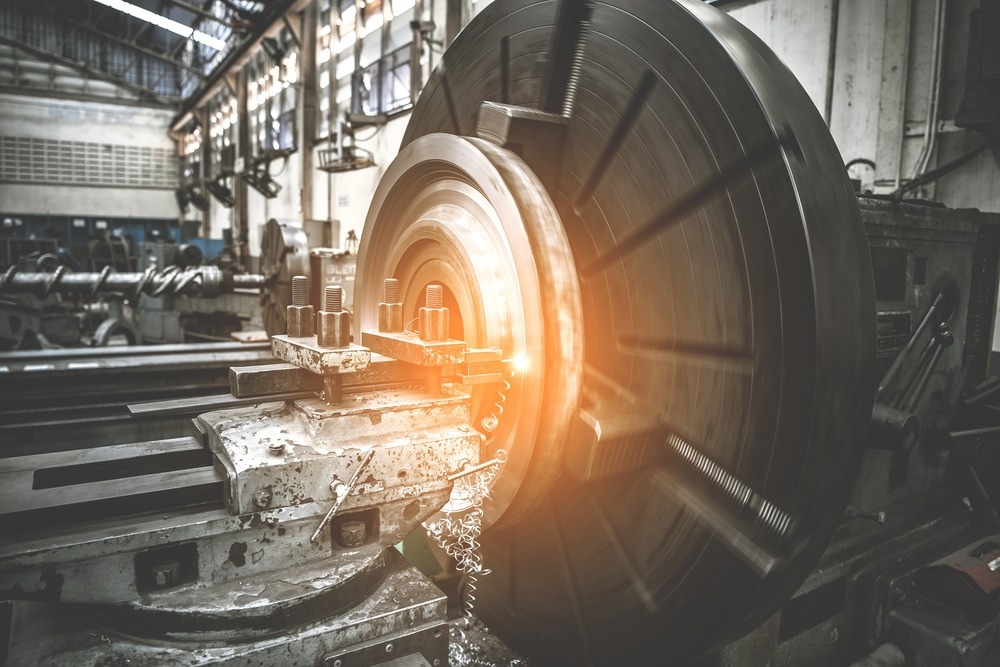
Image Credit: Red ivory/Shutterstock.com
Inconel 718: The Super Alloy That’s Revolutionizing Aerospace Engine Components
Superalloys are materials designed to perform under extreme conditions, such as high temperatures and pressures, making them ideal for applications in high-speed flight environments.
Inconel 718 is a popular superalloy that is widely used in aerospace, power generation, and other high-temperature applications due to its excellent properties, including oxidation resistance, high tensile and fatigue strength, and good creep behavior.
However, its production has traditionally been a slow and laborious process. The development of Wire Arc Additive Manufacturing (WAAM) offers a significant reduction in fabrication time and post-machining time, making it an attractive alternative.
Wire Arc Additive Manufacturing: The Future of Aerospace Manufacturing?
The aerospace industry has always been driven by the need for better materials and more efficient manufacturing processes. With the development of WAAM, a new horizon is opened to produce aerospace components. WAAM is one of the directed energy depositions (DED) technologies that use a wire electrode that melts as it is deposited onto the substrate, building up the component layer by layer.
WAAM has been shown to reduce fabrication time by more than 40% and post-machining time by more than 15%, depending on the component size. This is because WAAM produces near-net-shape parts that require little or no additional machining. The process also allows for the production of complex shapes and structures that were previously difficult or impossible to manufacture.
The Benefits of WAAM Over Traditional Manufacturing Methods
Wire arc additive manufacturing offers several benefits over traditional manufacturing methods. Traditional manufacturing methods require multiple steps, including forging, machining, and welding, to produce the final component. These steps can take significant time, and the finished component may have residual stresses, cracks, and other defects that affect its performance.
WAAM, on the other hand, can produce components in a single step, reducing the overall production time and cost. It also allows for greater design flexibility, as components can be produced with complex geometries that are difficult or impossible to manufacture using traditional methods. WAAM also produces components with fewer defects, as the process takes place in a controlled environment with minimal human interaction.
In addition to these benefits, WAAM is also more environmentally friendly than traditional manufacturing methods. By reducing the amount of material waste and energy used in the manufacturing process, WAAM can significantly reduce the carbon footprint of aerospace engine component manufacturing.
Heat Treating Wire-Arc Additive Manufactured Inconel 718: A Breakthrough Study
A group of researchers from Cranfield University, Bedfordshire, UK, have published a recent study in the journal Nature in which they investigated the performance of Inconel 718 deposited using a wire-arc DED process. The process involved using a plasma arc to deposit the material, which was then tested for its high-temperature performance.
In addition, the researchers analyzed the effectiveness of the material that was deposited in two conditions: the as-deposited (AD) state and after undergoing a heat treatment process that is widely used in the industry to improve hardness, known as age-hardening.
The study showed that the performance of the deposited Inconel 718 was reduced in both AD and heat-treated conditions, with the heat-treated material significantly outperforming the AD material up to 538 °C. However, the difference in performance was less significant from 760 to 1000 °C, owing to an in-test aging process which increased the performance of the AD material.
The microstructure of the deposited material also showed significant cracking throughout the alloy and the formation of secondary phases throughout the matrix, with significantly more precipitation after heat-treating.
The study's conclusion suggests that wire-arc DED impacts the tensile performance of Inconel 718, with AD and heat-treated materials achieving 40 and 60% of the wrought ultimate tensile strength, respectively, in the range of room temperature to 538 °C. The use of industry-standard heat treatment on the AD material enhances its performance but does not contribute to an increase in its wrought performance.
It was observed that testing the AD material at 760 °C leads to improved performance due to an aging effect during testing. Lastly, the wire-arc DED technique causes solidification cracking in Inconel 718, with secondary phases detected at the edges of the cracks.
Improving High-Temperature Performance of Inconel 718 with WAAM
WAAM Inconel 718 offers several advantages over traditionally manufactured Inconel 718, including reduced fabrication time and the ability to produce complex shapes and structures. However, the as-deposited material contains Laves phase, which can coarsen and lead to a reduction in strength when subjected to elevated temperatures.
The study found that modified post-deposition heat treatment can successfully dissolve the Laves phase without precipitating δ phase, resulting in improved high-temperature performance. The modified heat treatment also reduced anisotropy in elevated temperature tensile.
Conclusion
To summarize, the publication highlights the effectiveness of heat treatment in enhancing the high-temperature performance of Inconel 718, a widely used nickel-based superalloy in aerospace engine components.
The study showed that modified post-deposition heat treatment could successfully dissolve Laves phase without precipitating the δ phase, resulting in reduced anisotropy in elevated temperature tensile. Additionally, the wire-arc DED process used in this study has several advantages over traditional manufacturing methods, such as reduced production time and cost, greater design flexibility, and fewer defects.
This technology also has the potential to reduce the carbon footprint of aerospace engine component manufacturing, making it more environmentally friendly. Overall, the combination of WAAM and modified heat treatment offers a promising opportunity to improve component manufacturing while reducing costs and environmental impact, making it an exciting breakthrough for the aerospace industry.
Further research and development towards applying these technologies in the field should follow to benefit from these results.
More from AZoM: Density Functional Theory Applied to Optoelectronical Properties of Graphene
References and Further Reading
AMFG (2018). An Introduction to Wire Arc Additive Manufacturing [Online]. amfg.ai. URL https://amfg.ai/2018/05/17/an-introduction-to-wire-arc-additive-manufacturing/ (accessed 3.27.23).
Athaib, N., Hobi, A., Al-Zubaidy, B. (2021). A review of Wire Arc Additive Manufacturing (WAAM) of Aluminium Composite, Process, Classification, Advantages, Challenges, and Application. Journal of Physics: Conference Series 1973, 012083. https://doi.org/10.1088/1742-6596/1973/1/012083
Azom (2008). Nickel Alloy Inconel 718 - Properties and Applications by United Performance Metals [Online]. AZoM.com. URL https://www.azom.com/article.aspx?ArticleID=4459 (accessed 3.27.23).
Fastech (2022). The Advantages of Wire Arc Additive Manufacturing [Online]. Fastech. URL https://fastech-engineering.com/the-advantages-of-wire-arc-additive-manufacturing (accessed 3.27.23).
James, W.S., Ganguly, S., Pardal, G. (2023). High temperature performance of wire-arc additive manufactured Inconel 718. Scientific Reports 13, 4541. https://doi.org/10.1038/s41598-023-29026-9
Material Properties (2020). What are Properties of Inconel 718 – Nickel-based Superalloy - Definition [Online]. Material Properties. URL https://material-properties.org/what-are-properties-of-inconel-718-nickel-based-superalloy-definition/ (accessed 3.27.23).
Svetlizky, D., Das, M., Zheng, B., Vyatskikh, A.L., Bose, S., Bandyopadhyay, A., Schoenung, J.M., Lavernia, E.J., Eliaz, N. (2021). Directed energy deposition (DED) additive manufacturing: Physical characteristics, defects, challenges and applications. Materials Today 49, 271–295. https://doi.org/10.1016/j.mattod.2021.03.020
Disclaimer: The views expressed here are those of the author expressed in their private capacity and do not necessarily represent the views of AZoM.com Limited T/A AZoNetwork the owner and operator of this website. This disclaimer forms part of the Terms and conditions of use of this website.