Sponsored by RETSCH GmbHReviewed by Emily MageeFeb 20 2024
Laboratory ball mills are a key component in the battery production value chain. They are used in several key application areas across research and development, manufacturing, and quality control processes.
With a range of different laboratory ball mills on offer, they are predominantly used in research and development applications. However, if ball mills are able to accommodate the requisite amounts of material for processing, laboratory mills are occasionally deployed in small-scale battery production pilot plants.
In commercial-scale production processes, agitator bead mills, vibrating bead mills, or continuous horizontal axis bead mills are the most common-place machines. Yet, in Giga factories and large recycling plants, laboratory ball mills still play a primary role in quality control processes when preparing material samples for analysis.
In this article, the four main application areas of Retsch laboratory ball mills in battery technology will be outlined. Each area can be categorized under specific application examples:
- Section 1: Reduction of the material particle size in batteries
- Section 2: Mixing and coating of particles
- Section 3: Synthesis of new battery materials
- Section 4: Sample preparation for analysis
Read the Full White Paper Here
With a focus on developing a fundamental understanding of the functional principles and guidelines for handling laboratory ball mills, supporting information on Retsch and other Verder Scientific products is also provided.
Overall, this article presents a bigger picture of how Verder Scientific can advance practical scientific progress and support growth in the battery technology industry.
One Ball Mill is Not Like the Other
How is it possible to identify which ball mill is best suited for a specific purpose or application? To better understand the factors that set the different ball mill types apart, it is worth first looking at what they share in common.
Each ball mill works on the same basic principle: the concept being that sample materials are agitated with grinding balls inside a closed jar system. This agitation means that materials are frequently subjected to strong mixing and crushing forces.
The apparent difference, which can be seen immediately, lies in the different ways the jars move. Resultingly, the classification of each ball mill is typically reflected by how it is named according to its relative movement.
For instance, in a planetary ball mill assembly, a jar rotates in a circular manner similar to how a planet orbits the sun; in a mixer mill, the jar oscillates in a shaking movement across a horizontal axis; and in a drum mill, the jar simply spins around its central axis (see Figure 1).
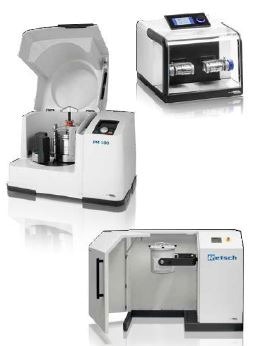
Figure 1. In planetary ball mills, mixer mills, and drum mills, the jars follow different patterns of movement. Image Credit: RETSCH GmbH
Ball mills are further characterized by the major differences in the sizes of grinding jars and what ball sizes are readily available. Retsch can supply ball mills with jar capacities ranging from 1.5 ml up to 150 l, and balls are available in sizes ranging from 0.1 mm to 40 mm, see Figure 2.
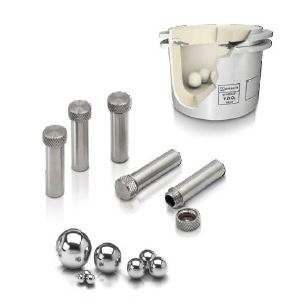
Figure 2. Examples of different jar and ball sizes used in laboratory ball mills: (a) small metal cups of 2 ml capacity used in Retsch mixer mills and (b) EasyFit jar with a capacity of 500 ml used in a Retsch planetary ball mills and (c) grinding balls of different size. Image Credit: RETSCH GmbH
A third and essential characteristic of a ball mill, which greatly influences the outcome of the milling process, is the mill’s power. This is usually determined by the application. For example, gentle material processing requires gentle and slow movements of the jar, whereas to achieve grinding effects, agitating jars at high speeds is the most commonly used and effective method.
Here, the maximum speed, which is usually represented as maximum frequency or maximum revolutions per minute (rpm), is synonymous with performance.
A more meaningful physical quantity than speed is the acceleration force “g”, which is induced by the kinetic energy of a ball mill. In the High-Energy Ball Mill Emax, for instance, an unparalleled acceleration of 76 g can be attained if it reaches its maximum speed of 2000 rpm.
Selecting the Most Suitable Ball Mill
To determine which ball mill is best suited for a particular application, both the task and desired outcome should be clearly defined. Therefore, identifying what sample size, batch volume, and process times are needed is key. Furthermore, it is crucial to know what materials are needed for the grinding tools as well as to establish the desired final fineness of the material being ground.
Once all of the application requirements have been clearly defined, the appropriate mill for the task can then be selected. To support this process, Retsch has designed a spider-net diagram that displays the strength and efficiency of each ball mill model, as shown in Figure 3.
For example, a planetary ball mill has a bigger jar volume compared to a mixer mill; this is shown by its high value on this diagonal in the spider-net diagram. A mixer mill, by way of contrast, offers numerous possibilities for temperature control and has a high value in this area.
Considering that a single ball mill is the most commonly used across a wide range of applications, it is still crucial not to compromise too much in a given area to ensure that all application requirements are achieved with optimal results.
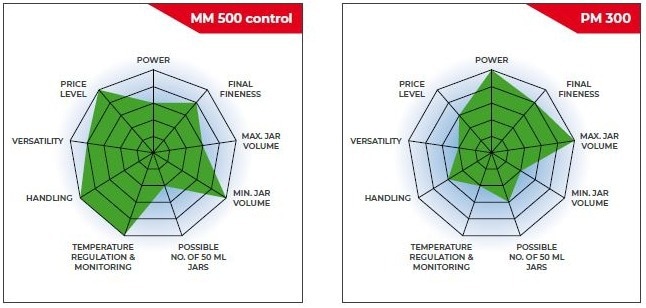
Figure 3. Retsch visualizes the features and strengths of each ball bill model in a diagram to help find the right model for a specific application. In the example shown, it is easy to see that the Planetary Ball Mill PM 300 offers advantages in terms of power, final fineness and maximum jar volume compared to the Mixer Mill MM 500 control. The latter in terms offers easier handling, versatility and the ability to control the temperature during the process. Image Credit: RETSCH GmbH
Three Rules For The Optimum Ball Mill Set-up
As well as choosing the appropriate mill model, the success of any given milling application from start to finish is contingent on selecting the right accessories and configuring the appropriate process parameters.
This includes knowing what ball sizes, jar sizes, jar materials, material fill levels, and number of balls are needed and being aware of what speed, time, and cycle programs should be set during the process.
Knowing how to optimize the ball mill set-up can be a challenging task in its own right. This is because the result is contingent on the motion of the balls inside the jar, which is intrinsically statistical and chaotic in nature.
It is not as straightforward as simply calculating the ball movement; computational simulations are often used to extract precise information relative to the impact and friction effects, which determine the ball milling result, as displayed in Figure 4.
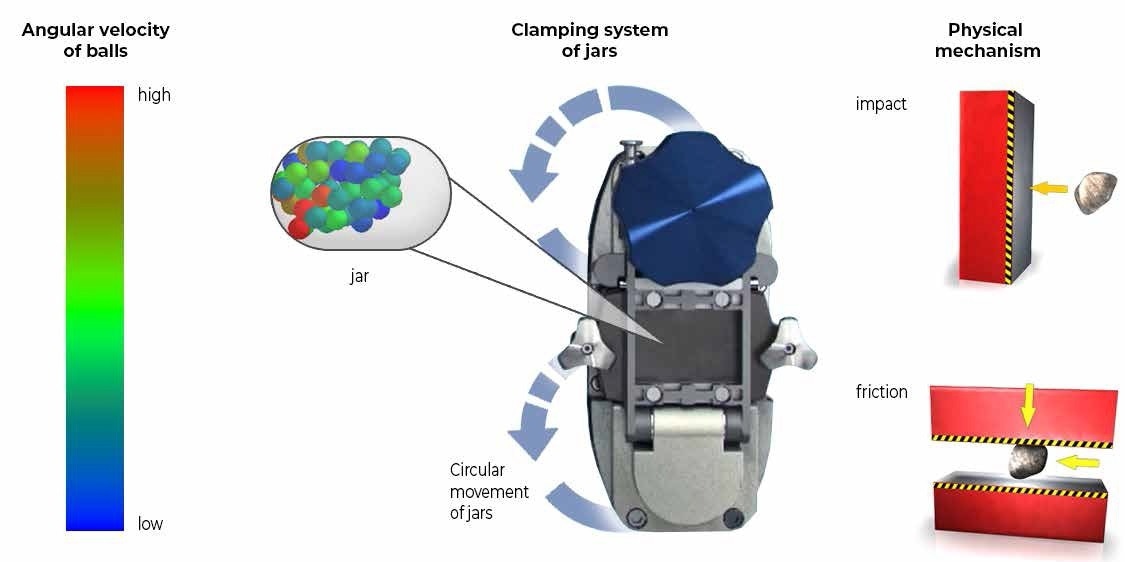
Figure 4. Schematic representation of the statistical ball movement for a specific setup of a High-Energy Ball Mill Emax. The color of the balls illustrates their different angular velocities. Impact effects and friction are responsible for the ball milling result. Image Credit: RETSCH GmbH
However, a basic understanding, combined with experience and experimentation, is also extremely useful when it comes to determining the optimum accessories and milling parameters. Retsch refers to this fundamental knowledge as the “art of milling.”
By following just three basic rules, it is possible to establish a well-functioning ball milling process that achieves the desired results:
Rule 1: Select the Right Grinding Tool Material
Grinding tools are readily available in a variety of materials. The grinding tool material should be harder and more robust than the sample material, while simultaneously, the abrasion of grinding tools should not have a detrimental impact on the sample.
Rule 2: Follow the Jar-Filling Guidelines for Optimal Results
The jar-filling guidelines describe the amount of sample material needed and the number and size of balls required. To achieve optimal results, it is important to be able to identify exactly what the mill is being used for.
Dry grinding: In the dry grinding process, the size of the balls should be three times larger than the largest particle of the sample material as a minimum requirement. The 1/3 rule should be used when filling the jar to protect the grinding equipment and enable effective particle size reduction:
1/3 of the jar volume is filled with balls
- 1/3 of the jar volume is filled with material
- 1/3 of the jar volume is free space to facilitate movement
Mechanochemistry: In mechanochemistry, the ball-to-material weight ratio is often higher than 1, accepting the resulting increase in wear and material abrasion of the grinding tools.
Wet grinding: Wet grinding is the only option when trying to achieve final particle sizes of <5 µm.
In wet grinding processes, a liquid, e.g., water, alcohol or buffer, is added to the sample to neutralize the surface charges and reduce the attraction of the particles to each other to prevent agglomeration effects. Ultra-fine particles are mainly produced by friction. The size of the balls should be at least a factor of three larger than the largest particle of the sample material and a fineness of 1/1000 times of ball size can be obtained.
For wet grinding:
- 2/3 of the jar volume is filled with balls.
- The dry sample material is introduced and dispersed manually throughout the jar. Generally, sample material is added as long as it can permeate the spaces between the balls. Depending on a material’s particle size, filling up to 1/3 of the jar’s volume with the sample is possible.
- Finally, liquid is added and manually dispersed until it displays an oil-like viscosity.
Mixing: Mixing can be performed in all scenarios. During this process, only the sample material/s are usually placed in the jar, but balls can also be added to the jar with the sample material.
The relative oscillating motion of a mixer mill is especially well-suited for mixing purposes because the patterns and accelerations are numerous and high. In all mixing processes, it is crucial to select the appropriate jar filling as this prevents an unwanted reduction in particle size.
Rule 3: Careful Selection of Speed and Process Time(s)
When running ball mills at high speeds, powerful mixing and crushing effects are achieved. This could be desirable for certain applications, for example, to break up large particles.
The horizontal shaking motion in mixer mills typically generates a greater amount of impact effects when compared to planetary ball mills, which tend to demonstrate more friction-dominated processes.
However, the impact intensity is not only dependent on the speed and the movement of the jars, but also on how the jars are filled. Friction is also a main factor when it comes to generating heat during the ball milling process. For this reason, heat generation is typically higher in planetary ball mills than it is in mixer mills.
Irrespective of the type of ball mill used, if the temperature reaches too high a threshold, it may be necessary to reduce the speed of the mill or insert grinding breaks. Alternatively, it may also be necessary to choose a set-up with active temperature control.
The longer the process time, the finer the particle size. This is particularly true unless particle size reduction has not yet reached the saturation point, where the particle size does not decrease anymore.
By increasing the energy input to the maximum speed, process time can often be reduced. However, the fastest processing may not always result in the finest particles due to other effects, such as material baking problems or increasing grinding temperatures that, in turn, may prolong the grinding process due to necessary breaks.
Read the Full White Paper Here
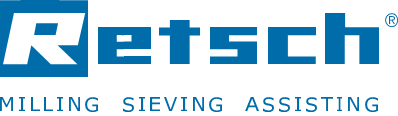
This information has been sourced, reviewed and adapted from materials provided by RETSCH GmbH.
For more information on this source, please visit RETSCH GmbH.