The surface of a material defines its functionality and performance upon integration into a device. Superior corrosion resistance is essential for maintaining long service life and optimal working performance.
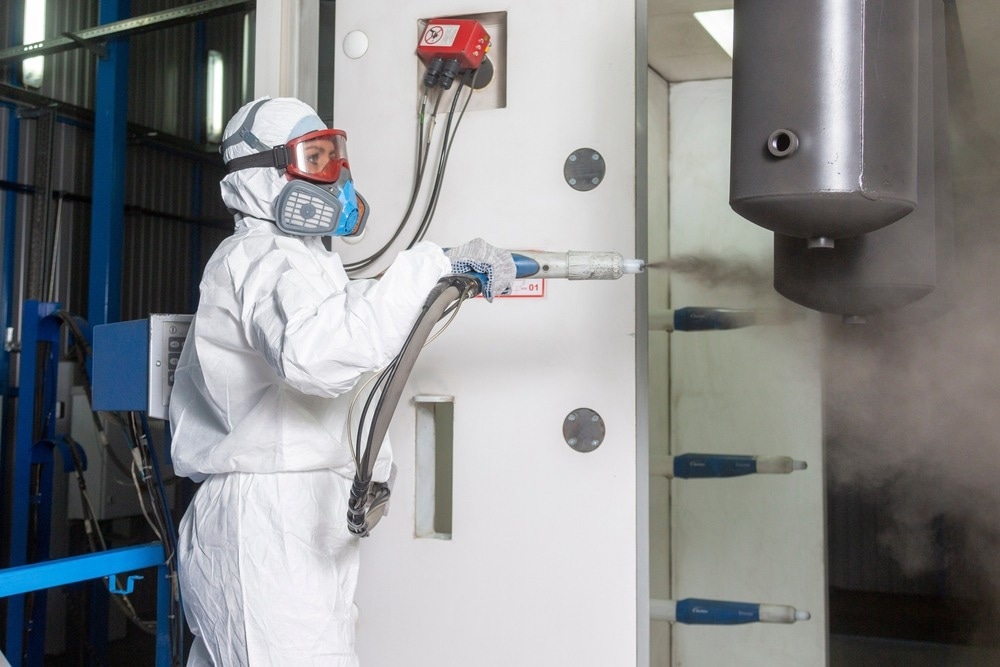
Image Credit: Vizun/Shutterstock.com
Depending upon the material, enhanced corrosion resistance can be obtained by manipulating surface properties like composition, structure, and topography. Factors influencing the choice of modification method include desired surface quality, costs, process time, and final application.
Enhanced Corrosion-Resistant Materials
Materials with high corrosion resistance are essential in constructing new-age infrastructure, including highway bridges, gas transmission pipelines, waterways, ports, airports, hazardous material storage, and railroads. Such materials ensure the longevity and reliability of the structure as well as the safety of the public and the environment. Utilities such as gas distribution, drinking water, sewage systems, electricity transmission, and telecommunications require corrosion-resistant materials to prevent premature obsolescence.
In the production and manufacturing industry, corrosion of an internal device may cause sudden machinery failure as well as fire, explosion, or accidents. Repairing or replacing a corroded component contributes to overall equipment maintenance expenses. In some instances, a component may be located internally, making its repair or replacement unfeasible.
High corrosion resistance is crucial in medical and biological applications where materials directly contact living tissues. Metallic implants such as steel, gold, silver, titanium, chromium, and dental amalgams are used to repair and regenerate bodily tissues. Corrosion of implant surfaces can trigger potentially harmful reactions inside the human body, which can prove lethal.
Surface Modification Techniques
Traditional surface modification techniques for enhanced corrosion resistance involve the application of protective coatings or methods to increase surface hardness. Various physical and chemical processes are used to apply coatings on the surface of materials, which can improve both hardness and corrosion resistance.
For example, film coating using physical vapor deposition (PVD) involves physical processes like sputtering and evaporation, while chemical vapor deposition (CVD) is based on chemical reactions in a gaseous environment. PVD offers precise control over film thickness, composition, and microstructure; however, it is limited to certain materials. Alternatively, CVD provides high purity and better coverage on complex surfaces but requires careful control of reaction conditions.
In addition to coatings, various mechanical, chemical, electrochemical, and thermal surface treatment methods have been developed to enhance the corrosion resistance of different materials. A material’s surface properties may significantly vary from its bulk properties. Thus, it is crucial to identify the correct technique for surface modification to tailor the material surface per the specific requirements.
Mechanical surface modification techniques—like shot peening, sandblasting, grinding, and ultrasonication—are used mostly in manufacturing, tooling, and automotive industries, which involve big workpieces of different geometries and dimensions. While they are simple, cost-effective, and applicable to a wide range of materials, they offer limited control over surface composition and morphology. They are, therefore, less reliable in critical applications.
Chemical and electrochemical modification involves processes like ion implantation, electro-polishing, sol-gel, and anodization. These methods are effective at removing oxides and iron contamination. They are mostly used for bio-implant materials since they result in smooth surfaces and can be used to selectively modify the surface chemistry. However, such chemical methods are limited to specific material types.
Thermal methods involve treating the material surface using heat, flame, plasma, and laser. Surface heat treatments like carburizing and nitriding are conventionally used to increase the hardness of metallic alloys. These methods are extensively applied in automotive, aerospace, and biomedical industries due to their process speed and control. However, they necessitate specialized equipment that is expensive and difficult to operate.
With recent technological advancements, laser-based techniques such as surface melting, alloying, texturing, and ablation are increasingly employed for the precise surface modification of materials.
These methods enable the elimination of defects and the creation of periodic microstructures like grooves and dimples through heating and controlled cooling, impacting the wear behavior of the material. Due to their high accuracy, lasers are predominantly utilized in aerospace, medical, and nuclear fields despite being an expensive surface modification method.
Irrespective of the technique employed, it is important to ensure that the material's bulk properties remain largely unaffected during surface modifications.
Recent Studies
A recent review article published in Metals explored various surface modification techniques employed for metastable austenitic stainless steels (MASS), widely used in multiple industries due to their extraordinary mechanical properties and corrosion resistance.
Several nano-structuring methods (physical, mechanical, chemical, thermal, electrochemical, and laser) are commercially available for enhancing overall material behavior. The authors highlighted that the adoption of laser-based modification techniques is slow compared to other conventional methods, likely due to the requirement for specialized equipment and associated expenses.
Another recent article in Pharmaceutics highlighted the enhanced corrosion resistance of nano-engineered titanium dental implants. Titanium offers favorable biomechanics and biocompatibility in dental implant fabrication. However, corrosion resulting from chemical reactions with the fluids in the oral cavity can cause cytotoxicity. This can be avoided by nanoscale surface modifications of Ti-based dental implants.
Methods such as depositing nanoparticles/nanowires by alkali-heat treatment and plasma spraying, refining grain size to nanoscale, and using electrochemical anodization to create nanotubes/nanopores are suggested to develop dental implants capable of withstanding the complex corrosive oral microenvironment, thus extending their longevity.
Corrosion affects our lives regularly, causing the failure of automobiles, household appliances, water, and energy transmission lines. According to an old estimate, annual corrosion costs in the US were approximately 9 % of the gross domestic product (GDP). These costs include indirect expenses like lost productivity due to outages, delays, failures, and litigations.
Therefore, the advanced surface modification of materials for enhanced corrosion resistance is essential to ensure public safety, reliable infrastructure, maximized asset life, environmental protection, and cost-effective long-term operations.
More from AZoM: Silazane Ceramic Coating on Aluminum to Improve Hardness and Wear Protection
References and Further Reading
1. Sethy, M. (2023). Surface Engineering: Enhancing Material Performance through Advanced Surface Modifications. Advanced Materials Science Research. doi.org/10.37532/ aaasmr.2023.6(3).71-73
2. Rezayat, M., Mojtaba Karamimoghadam, Moradi, M., Casalino, G., Joan Josep Roa, Mateo, A. (2023). Overview of Surface Modification Strategies for Improving the Properties of Metastable Austenitic Stainless Steels. Metals. doi.org/10.3390/met13071268
3. NACE International. (2007). Corrosion Costs and Preventive Strategies In the United States. [Online] NACE International. Available at: http://impact.nace.org/documents/ccsupp.pdf
4. Guo, T., Scimeca, J.-C., Sašo Ivanovski, Verron, E., Gulati, K. (2023). Enhanced Corrosion Resistance and Local Therapy from Nano-Engineered Titanium Dental Implants. Pharmaceutics. doi.org/10.3390/pharmaceutics1502031
Disclaimer: The views expressed here are those of the author expressed in their private capacity and do not necessarily represent the views of AZoM.com Limited T/A AZoNetwork the owner and operator of this website. This disclaimer forms part of the Terms and conditions of use of this website.