The corrosion resistance of titanium is well documented. A stable, substantially inert oxide film provides the material with outstanding resistance to corrosion in a wide range of aggressive media. Whenever fresh titanium is exposed to the atmosphere or to any environment containing oxygen, it immediately acquires a thin tenacious film of oxide. It is the presence of this surface film that confers on the material its excellent corrosion resistance. Provided that sufficient oxygen is present, the film is self healing and re-forms almost at once if mechanically damaged. Oxidising and Non-Oxidising Environments Since titanium depends for its passivity on the presence of an oxide film, it follows that it is significantly more resistant to corrosion in oxidising solutions than in non-oxidising media where high rates of attack can occur. Thus the material can be used in all strengths of aqueous nitric acid at temperatures up to the boiling point. Similarly, it is not attacked by wet chlorine gas and by solutions of chlorine compounds such as sodium chlorite and hypochlorite. There is no evidence of pitting or stress corrosion cracking in aqueous solutions of inorganic metal chlorides. Titanium also has exceptional resistance to sea water even under high velocity conditions or in polluted water. While the material normally has a significant corrosion rate in media such as sulphuric or hydrochloric acids which produce hydrogen on reaction with the metal, the presence of a small amount of oxidising agent in the acid results in the formation of a passive film. Hence, titanium is resistant to attack in mixtures of strong sulphuric and nitric acids, hydrochloric and nitric acids and even in strong hydrochloric acid containing free chlorine. The presence in solution of cupric or ferric ions also reduces the corrosion rate, as does alloying with noble metals or the use of an anodic protection technique. Formation of Protective Oxide Films Protective oxide films on titanium are usually formed when the metal has access to water, even though this may only be present in trace quantities or in vapour form. Thus, if titanium is exposed to highly oxidising environments in the complete absence of water, rapid oxidation can occur and a violent, often pyrophoric, reaction results. Examples of this type of behaviour are found in reactions between titanium and dry nitric acid and between titanium and dry chlorine. However, the amount of moisture necessary to prevent attack under these conditions is small and can be as little as 50 ppm. Summary of Corrosion Resistance The corrosion resistance of commercially pure titanium to simple chemical environments is summarised in Table 1. Table 1. Resistance of pure titanium to simple chemical reagents. | Acetic Acid | 5,25,50,75,99.5 | Boiling | A | Acetic Anhydride | 99 | Boiling | A | Aluminium Chloride | 5,10 25 | 100 100 | A C | Ammonia, Anhydrous | 100 | 40 | A | Ammonium Chloride | 1,10,saturated | 100 | A | Ammonium Hydroxide | 28 | Room,60,100 | A | Aqua Regia (1 HNO3:3 HCl) | - | Room,60 | A | Barium Chloride | 5,20 | 100 | A | Benzene | - | Room | A | Benzoic Acid | Saturated | Room,60 | A | Boric Acid | 10 | Boiling | A | Bromine | Liquid | Room | C | Bromine-saturated Water | - | Room,60 | A | Calcium Chloride | 5,10,25,28 73 | 100 177 | A C | Calcium Hypochlorite | 2,6 | 100 | A | Chlorine Gas, Dry | - | 30 | C | Chlorine Gas, Wet | - | 75 | A | Chromic Acid | 10,50 | Boiling | A | Citric Acid, Aerated | 10,25,50 | 100 | A | Cupric Chloride | 55 | 118 | A | Ethyl Alcohol | 95 | Boiling | A | Ethylene Dichloride | 100 | Boiling | A | Ferric Chloride | 50 | 113,150 | A | Formic Acid, Aerated | 10,25,50,90 | 100 | A | Formic Acid, Non-Aerated | 10 25,50 | Boiling Boiling | A C | Hydrobromic Acid | 30 | Room | A | Hydrochloric Acid | 1,3 2,3 15,37 | 60 100 35 | A C C | Hydrofluoric Acid | 1 | Room | C | Hydrogen Sulfide | - | 70 | A | Iodine | - | 130 | C | Lactic Acid | 100 | Boiling | A | Magnesium Chloride | 5,20,42 | Boiling | A | Magnesium Sulfate | Saturated | Room | A | Manganous Chloride | 5,20 | 100 | A | Mercuric Chloride | 1,5,10,Saturated | 100 | A | Methyl Alcohol | 99 | 60 | C | Nickel Chloride | 5,20 | 100 | A | Nitric Acid | All Red Fuming | Boiling Room,50,70 | A C | Oxalic Acid | 0.5,1,5,10 0.5,1,5,10 | 35 60,100 | A C | Phosphoric Acid | 5,10,20,30 35-80 10 | 35 35 80 | A B C | Potassium Chloride | 36 | 111 | A | Potassium Hydroxide | 10 | Boiling | A | Sodium Chloride | Saturated | Room, 111 | A | Sodium Dichromate | Saturated | Room | A | Sodium Hydroxide | 10 73 | Boiling 113-129 | A B | Sodium Hypochloride | 10 g/l Cl2 | Boiling | A | Sodium Nitrate | Saturated | Room | A | Sodium Phosphate | Saturated | Room | A | Sodium Sulphide | Saturated | Room | A | Sodium Sulphite | Saturated | Room | A | Stearic Acid | 100 | 180 | A | Sulphur, Molten | 100 | 240 | A | Sulphur Dioxide, Dry | 100 | Room,60 | A | Sulphur Dioxide + Water | - | Room,70 | A | Sulphuric Acid | 1,3,5 10 20-50 1,5 | 35 35 35 Boiling | AB B C C | Tataric Acid | 10,25,50 | 100 | A | Trichloroethylene | - | Boiling | A | Zinc Chloride | 20,50,75 75 | 150 200 | A B | Effect of Alloying Elements Generally, titanium alloys that have been developed for high strength and good creep resistant properties have inferior corrosion resistance to the commercially pure material, but there are some alloying additions that can improve corrosion properties. By comparison with alloys for aerospace, there has only been a restricted amount of work carried out to develop titanium alloys for corrosion resistant applications. One of the most successful of these involves the addition of small amounts of palladium to the commercially pure material. This not only improves its resistance to reducing acids such as sulphuric, hydrochloric, and phosphoric but also raises the critical temperature at which crevice corrosion in sea water can occur. This principle of palladium additions is now being extended to some of the higher strength alloys in order to combine corrosion resistance with good tensile properties. Other corrosion resistant alloys that have been developed over the years include Ti-0.8%Ni-0.3%Mo as a possible substitute for Ti/Pd alloys, and Ti-6%Al-7%Nb which is used as a surgical implant material. Galvanic Corrosion When designing equipment for the chemical or oil industries or for some general engineering applications it is essential to consider the deleterious galvanic effects that may result from contact between dissimilar metals. If two metals are coupled together in an electrolyte, the less noble or anodic member of the couple will normally tend to corrode, the extent of the attack depending upon the difference in electrode potential between the two materials and also on the relative anode to cathode area ratios. Titanium differs from most materials in that, if coupled to a more noble metal in an aggressive solution, the electrode potential of the titanium tends to be raised and the corrosion rate is reduced rather than increased. As a practical example, consider the case of pipework systems handling seawater (see Figure 1). Ideally these would be fabricated entirely from titanium but where this is not possible, alloys which are galvanically near compatible with titanium such as Inconel 625, Hastelloy C, 254 SMO, Xeron 100 or composite materials may be selected to be in direct contact with titanium at joints. Although several of the highly alloyed stainless steels and nickel based alloys are only marginally less noble than titanium in their passive state, once they become active the rate of localised attack can be dramatic, leading to rapid failure. 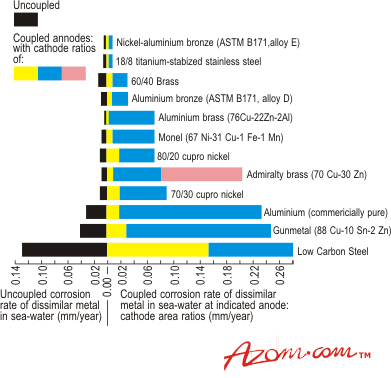 | Figure 1. Galvanic corrosion of titanium-dissimilar metal couples at different area ratios in static sea water. | In situations where it is not possible to avoid galvanic contact between titanium and a less noble metal, there are a number of possible techniques to reduce the risk of corrosion: • Coating of the titanium in the vicinity of the joint to reduce the effective cathode to anode surface area ratio; • Application of cathodic protection; • Electrical insulation of the titanium by the use of non-conducting gaskets and sleeved bolts; • Installation of short easily replaced flanged sacrificial heavier wall sections of the less noble metal; • Chemical dosing. Crevice Corrosion Most metals are subject to increased corrosion in crevices formed between themselves and other metals or non-metals. The reason for this preferential corrosion is that, because of restriction in circulation of the solution, there is either a differential concentration effect or differential aeration within the crevice. This can lead to a difference in electrode potential between the metal in the crevice and that outside it, where free circulation of solution is possible. A galvanic reaction can then be set up between the two areas. Titanium is particularly resistant to this form of attack and is only subject to it in certain specific instances. For example, corrosion has been reported in an application involving wet chlorine but attempts to reproduce it in the laboratory have been largely unsuccessful. This attack has been attributed to the fact that slow dehydration of the wet chlorine can occur in crevices where there is a large ratio of metal area to gas volume. Crevice corrosion under heat transfer conditions is possible in sodium chloride solutions at temperatures down to 70°C but the pH of the solution is important. This is illustrated in Figure 2. 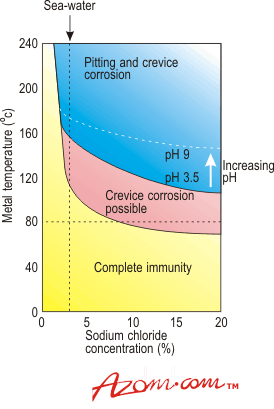 | Figure 2. Influence of temperature, concentration and pH on crevice and pitting corrosion of commercially pure titanium in sea water and sodium chloride brines. | Effect of Crevice Size and Shape With titanium, the shape and size of crevice appear to have a critical influence on corrosion behaviour. When the two surfaces are close together they are either not wetted by the corrodent or, if they are wetted initially, the flow of solution is restricted and corrosion is stifled before the titanium oxide film is disrupted. When the surfaces are too far apart, diffusion of oxygen is sufficiently rapid to passivate the material. Crevice Corrosion Resistant Alloys The use of titanium/palladium alloys virtually eliminates the risk of crevice corrosion in sea water. This is illustrated in Figure 3. 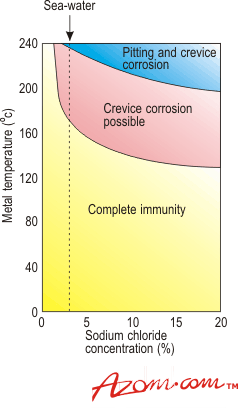 | Figure 3. Influence of temperature, concentration and pH on crevice and pitting corrosion of titanium/palladium in sea water and sodium chloride brines. | Stress Corrosion Although titanium and its alloys are resistant to corrosion in many media, including aqueous solutions of chlorides, stress corrosion of commercially pure titanium and of titanium alloys can take place in a limited number of highly specific environments. Red Fuming Nitric Acid Environments The first reported instance of stress corrosion cracking of titanium was in red fuming nitric acid. Here, cracking was mainly intergranular but the phenomenon only occurred under anhydrous conditions, the presence of as little as 1.5 to 2% water completely inhibiting the reaction. All titanium alloys are susceptible to stress corrosion in this environment but for some the presence of excess nitrogen dioxide is necessary while others can crack in the absence of this component. Methanol Environments The only other environment that has been shown to cause stress corrosion of commercially pure titanium as well as titanium alloys is methanol. Failure again is by intergranular cracking and the mechanism is more likely if bromine, chlorine, or iodine ions are present in the alcohol. Again the presence of a small amount of water will completely prevent attack, 4% giving immunity to all grades and all alloys. Chlorinated Hydrocarbon Atmospheres While commercially pure titanium is not affected, stress corrosion of some titanium alloys can take place in chlorinated hydrocarbons. It is known, for example, that on prolonged exposure at elevated temperatures in the presence of some metals, the vapours of trichlorethylene can partially decompose to form hydrochloric acid. This causes stress corrosion of certain titanium alloys, particularly those containing aluminium and care must be taken when degreasing these materials. However, even with these alloys the operation is perfectly safe if attention is paid to working conditions. The correct degreasants containing additions to prevent decomposition should be used and the time of contact between the titanium and the degreasant should not be excessively long. Hot Salt Stress Corrosion Cracking Although it has been demonstrated in laboratory tests that titanium alloys are susceptible to hot salt stress corrosion cracking, no service failures have ever been reported, even though titanium alloys have been used in aerospace applications at temperatures as high as 600°C. When cracking does take place it can either be intergranular or transgranular in form and all the commercially available alloys except the commercially pure grades are susceptible to some degree. Pitting Titanium and its alloys are extremely resistant to pitting attack in seawater and other chloride containing solutions at ambient and moderately elevated temperatures. However, if a titanium alloy sample containing an existing fatigue crack is loaded under plane strain conditions, the presence of seawater will reduce the resistance of the material to crack propagation. The susceptibility of titanium alloys to this form of cracking appears to be adversely affected by aluminium, tin and oxygen contents, whereas the presence of certain beta stabilisers such as niobium and tantalum reduces the risk of attack. Commercially pure grades are not affected at oxygen levels below 0.32%. Erosion Resistance Erosion is an accelerated form of attack usually associated with high water velocities and with local turbulence which removes the oxide from the surface of film forming metals thus exposing bare metal to the corrodent. As a result of its ability to repair its protective oxide film quickly, titanium has an extremely high resistance to this form of attack. In pure sea water, for example, erosion is negligible at flow rates as high as 18 m s-1. It is even resistant to seawater containing sand and carborundum grit flowing at 2 m s-1. The erosion rate under these conditions corresponds to a penetration of only 1 mm in nearly eight years. It is notable, however, that with very coarse carborundum at higher speeds the erosion rate of titanium is higher than that of materials such as cupro-nickel. This is because, under these conditions, there is not sufficient time for the oxide film to reform and the underlying titanium is of lower hardness than cupro-nickel. These test conditions are very much more severe than those normally encountered in service, however, and it has been amply demonstrated that titanium is completely unaffected in condensers and coolers handling waters having a high sand content, whereas under the same conditions cupro-nickels can fail within 2 to 3 years. Under those conditions where tubes have become blocked by extraneous matter, impingement attack causing rapid failure of copper base materials has not affected titanium. This has been substantiated in service and in experimental heat exchangers running under laboratory conditions at flow rates of at least 4 m s-1. |