Sponsored by RETSCH GmbHReviewed by Emily MageeJul 16 2025
Sample preparation is critical in ensuring accurate mineral analysis in the mining sector. Despite ongoing technological progress, several persistent challenges remain.
Contamination during sample collection and preparation can distort results, potentially leading to incorrect assessments of ore quality. The inherently variable composition of mineral deposits makes it difficult to obtain samples that are both representative and homogeneous. Achieving uniform mixing during fine grinding is especially important, as it helps minimize sampling bias and supports more reliable analytical outcomes.
Certain ores’ physical hardness makes crushing and grinding difficult, which might lead to equipment wear and higher expenses. Time constraints and the need to produce results quickly sometimes cause rushed sample preparation, lowering quality. Innovative technologies are required to ensure accurate and efficient mineral analysis as the mining sector explores more diversified and distant resources.
Addressing these difficulties is essential for maximizing resource extraction and maintaining economic viability. Avoiding dust inhalation during sample processing is crucial for addressing health concerns.
Recycling in the mining sector is becoming increasingly important due to environmental concerns and resource shortages. Mining activities create enormous waste, such as tailings and slag, which can pose environmental risks if not managed effectively.
Recycling these materials could help the environment, minimize waste, and recover important metals, leading to more sustainable mining methods. However, removing valuable components from mining waste requires complex technology and R&D to create new materials.
Retsch Offers Solutions for Each of the Aspects
- Reducing operational time, preventing sample loss, cross-contamination, and dust
- Ensure sample homogeneity using inhomogeneous samples for reproducible analysis
- The need for strong and adaptable mills to tackle even the most difficult jobs in R&D
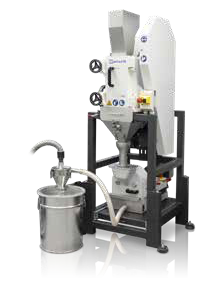
Combination Unit Jaw Crusher BB 250 and Disc Mill DM 200 with Cyclone. Image Credit: Retsch GmbH
Pre-Crushing and Homogenizing: Two Steps in One, and No Dust at All
When selecting appropriate grinders and milling equipment, grinding difficult mining minerals, such as ores and tailings, requires careful consideration of abrasion. Pre-crushing is best done in Jaw Crushers with abrasion-resistant jaws composed of zirconium oxide or tungsten carbide.
Fine grinding, such as in Disc Mills, depends on the sample amount and desired particle size. Retsch’s innovative combination machine, which combines a jaw crusher, disc mill, and cyclone, provides a time-saving and dust-free solution.
The new combination unit crushed approximately 1000 g of rock samples. The Jaw Crusher BB 250 was configured with an initial feed size of 100 mm and a 2 mm gap. The disc mill DM 200 adjusted the feed rate for fine grinding.
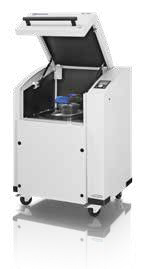
Vibratory Disc Mill RS 200. Image Credit: Retsch GmbH
The sample material was broken into fragments, with larger fragments (less than 10 mm) fed to fine grinding. The sample was processed in around 15 minutes. The Disc Mill’s spacing was adjusted at 200 µm, yielding around 400 µm particles.
To prevent material wear, the Jaw Crusher uses tungsten carbide jaws or NiHard4, while the Disc Mill uses tungsten carbide grinding discs. The intermediate fraction is shown below as an illustration. The cyclone prevents dust pollution and ensures better working conditions. The machine’s air stream effectively removes ground particles and dust, resulting in nearly 100% sample recovery.

Original sample. Image Credit: Retsch GmbH
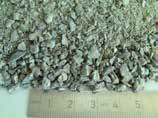
Intermediate fraction. Image Credit: Retsch GmbH
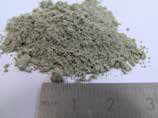
Final result. Image Credit: Retsch GmbH
Homogeneity Test: Perfect Homogeneity After Grinding in Vibratory Disc Mill RS 200
Modern XRF devices and software rapidly provide accurate and reproducible findings. Calibration and sample preparation are crucial for accurate measurements, as instrument errors are minimal. Understanding particle size is critical since it significantly impacts the findings. Representative and homogeneous samples eliminate potential inaccuracies.
The article will focus on mechanical sample preparation, which often accounts for the majority of analytical time. In XRF analysis, a few grams of a laboratory sample might represent many tons. Neglecting reliable sample preparation might lead to inconsistent and inaccurate findings.
Reliability and accuracy are significantly affected by the caliber of the spectrometer and sample preparation procedure. Reproducibility is impacted by the difficulty of detecting elements with small atomic numbers in XRF analysis. For certain elements lighter than potassium, such as dolomite, a fineness of at least 80 μm is necessary to provide accurate findings.
It is simple to demonstrate the RS 200's level of homogeneity. In a 250 ml grinding set of hardened steel, 118.75 g of quartz and 6.25 g of tantalum pentoxide (Ta2O5) were milled for one minute at 1500 rpm. A D97 = 100 µm fineness was attained.
Subsequently, samples were extracted from three distinct angles within the grinding jar: 120°, 240°, and 360°, with varying depths (bottom, middle, and surface). The Pellet Press PP 40 was then used to press the pulverized samples into 40 mm aluminum cups after they had been combined with Licowax®.
The Spectro Xepos P spectrometer was used to evaluate the pellets. The concentration of tantalum in the pellets extracted from the various locations within the grinding jar was the primary focus.
Each pellet should include 41 mg of tantalum per gram to replicate the original quartz-tantalum combination. Values from every sample were quite close to this computed value. Regardless of the mill or sampling location, very high homogeneity was noted, with all samples displaying similar, minor differences in the tantalum content (Table 1). The relative standard deviation was extremely low, reaching a high of ±0.54 mg/g.
Table 1. RS 200 Sample concentration. Source: Retsch GmbH
RS 200 |
Position of
sampling |
Conc.Ta
1 grinding [mg/g] |
Conc.Ta
2 grinding [mg/g] |
Surface 120°
240°
360° |
41.15
40.39
40.79 |
41.23
41.49
40.41 |
Center 120°
240°
360° |
41.09
41.24
40.38 |
40.19
40.46
41.15 |
Bottom 120°
240°
360° |
41.61
40.90
41.15 |
40.29
40.34
40.71 |
Mean Value |
40.96 |
40.69 |
Standard deviation |
0.40 |
0.47 |
Transforming Waste Secondary Sulfide Materials into High-Value Components for Tellurium-Free Thermoelectric Devices
Mine waste is a byproduct of ore extraction and processing, containing finely ground rock particles, water, and residual chemicals. Proper management and disposal are essential to minimize soil and water pollution, which can lead to substantial ecological harm. Recycling and reuse techniques are crucial for reducing environmental concerns and enhancing the value of secondary mineral resources in Europe.
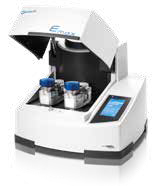
High Energy Ball Mill Emax. Image Credit: Retsch GmbH
The Horizon Europe START project* converts waste secondary sulfide materials into high-value components for tellurium-free thermoelectric devices, promoting sustainable industrial processes. Innovative tailings management strategies, such as waste treatment technology and stronger environmental restrictions, can mitigate the detrimental effects of copper mining.
Utilizing the Retsch High Energy Ball Mill Emax, the powders are manufactured on a laboratory scale at Laboratório Nacional de Energia e Geologia (LNEG) facilities. The direct synthesis of nanostructured mineral-derived tetrahedrite powders occurs close to room temperature, thanks to Emax’s unique characteristics, especially its high levels of mechanical energy input, which alter the powders’ reactivity.
Conclusion
Optimizing mineral analysis entails overcoming sample preparation issues, guaranteeing uniformity, and considering health and time. Accurate analysis requires proper sample preparation, as contamination and particle size can have a major influence.
Retsch’s combination unit addresses these issues by merging pre-crushing and fine-grinding stages while minimizing dust formation. Recycling mining waste through projects such as Horizon Europe START promotes sustainability and decreases environmental impact.
The mining industry can help create more eco-friendly and efficient operations by turning waste materials into useful components. Retsch equipment effectively facilitates the various facets of mining operations.
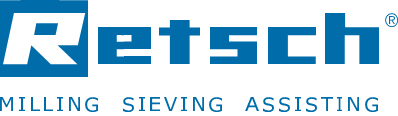
This information has been sourced, reviewed and adapted from materials provided by RETSCH GmbH.
For more information on this source, please visit RETSCH GmbH.