In an in-service oil analysis program, lubricating oil is used as a diagnostic medium because as it circulates through an oil-wetted system, it carries with it debris from wearing surfaces, as well as contaminants from internal and external sources. Oil samples are taken periodically from the system and sent to a laboratory for analysis. The analysis of the in-service lubricant is then used to determine the condition of the system.
The analytical data from an oil sample is reviewed and evaluated either manually by a data analyst, or in many instances, semiautomatically or automatically with specialized software such as Labtrak/Prescient. Wear trends may be normal requiring no corrective action, exhibit early signs of abnormal wear which may require more frequent sampling, or are abnormal resulting in a recommendation to take corrective maintenance action. The evaluation process is based on a knowledge of the metallurgy of the system being monitored and the fluids used for lubrication within the system.
Guidelines for Wear Metal and Contaminant Analysis
Wear metal and contaminant guidelines are established for a particular piece of equipment, but a variety of other important factors and variables must be also be taken into account.
- Equipment operating conditions are a prime factor.
- The operating environment is also important. For example, a desert location usually causes an increase in silicon readings accompanied by a corresponding increase in wear.
- Time since last oil change and oil consumption will affect readings and possibly disguise a wear trend.
- The length of time the equipment is in service is extremely important. During the engine break-in period, either when new or after overhaul, wear metal concentrations are abnormally high but are usually no cause for alarm.
- If equipment is left to stand idle for long periods of time, rust can form and iron readings will increase.
- Older systems typically generate more wear metals than fairly new ones of the same model.
- Load on the engine is also a factor, particularly changes in load; increases in wear may be due to an additional load placed on the engine.
- The chemical composition of the oil and coolant are also important. Metals present may not be due to wear at all, but rather due to an oil additive or coolant leak
Case Study - An Effective Spectrometric In-Service Oil Analysis Program for Wear Metal Data Interpretation
An effective spectrometric oil analysis program is dependent upon interpretation of the analytical data on wear metals, contaminants and additives as measured by a spectrometer. The interpretation of analytical results is an evaluation of the maintenance status of an oilwetted system and consists of the laboratory’s recommended service action.
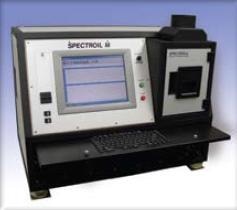
Conditions for Wear Metal Analysis
Wear metal analysis is the backbone of machine condition monitoring programs based on in-service oil analysis. It is effective in the sense that tests can be applied to determine that a system is normal, is nearing a failure mode, or has reached a failure mode. Further damage can thus be contained or avoided through immediate shutdown and repair.
Optical Spectrometer for Analyzing Wear Metals and Contaminants in Oil Samples
The spectrometer used to analyze an oil sample is capable to detect and quantify the wear metals and contaminates present in the oil sample. For example, if only iron and aluminum are present in abnormal amounts, the analyst's job is much simpler. The entire system does not have to be torn down and inspected; the inspection can be restricted to those components made up of iron and aluminum. Knowing the relative concentrations of the elements will further narrow down their possible source.
Examples of Wear Metals and Contaminants Detection with Spectroil Optical Spectrometer
1. An increase in silver and nickel in a certain type of railroad diesel is indicative of bearing wear. If detected early enough, a relatively simple bearing replacement can be made, rather than a $50,000-$100,000 overhaul and crankshaft replacement.
2. An increase in the amount of silicon in conjunction with a corresponding increase in iron, aluminum, and chromium as shown in the adjacent figure is probably caused by dirt ingestion. Air filter replacement and oil change may be the only maintenance action required. However, an increase of silicon alone may mean the oil type was changed to one containing a silicon-based anti-foaming agent and no maintenance action is required. The same trends without an increase of silicon could mean piston wear if the sample came from an internal combustion engine.
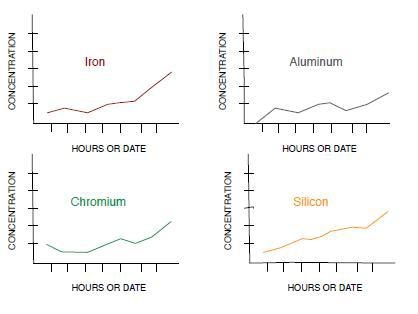
3. Sometimes even the slightest increase or presence of an element can be cause for alarm. The bearing shown in the adjacent figure was removed from the gearbox of an aircraft. The presence of only 2 ppm (parts-per-million) of copper was sufficient to warrant maintenance action. The source of the copper was the bronze bearing cage.
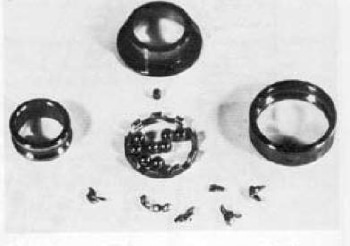
4. A trend showing the presence of boron in the lubricating oil of most water-cooled systems would indicate a coolant leak. If left unchecked, the coolant combines with combustion products and forms harmful acids and sludge which attack metal and reduce the ability of the oil to properly lubricate.
Summary
Wear metal analysis determines the condition of the machine, and not the condition of the lubricant. An effective in-service oil analysis program thus would include lubricant physical property analysis to determine lubricant degradation and contamination. The data from these additional tests can then be used to determine if a lubricant is still performing as specified or needs to be changed. This additional capability makes oil analysis even more cost effective and popular in today's unpredictable oil market.
The net benefits of a good in-service oil analysis program are:
- reduce maintenance costs,
- increase equipment availability,
- reduce lubricant usage,
- and improve safety.
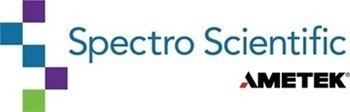
This information has been sourced, reviewed and adapted from materials provided by AMETEK Spectro Scientific.
For more information on this source, please visit AMETEK Spectro Scientific.