When the laser’s concentrated energy is used for welding it gives many advantages over conventional resistance methods. The technology is already spreading through the automotive industries of America and Europe. The Process The process is a non-contact one that directs laser outputs of 2-10 kW into a very small area. This means that power levels in excess of 103-105Wmm-2 are produced on the surface of the parts to be welded. The laser beam makes a ‘keyhole’ and the liquid steel solidifies behind the traversing beam, leaving a very narrow weld and heat affected zone (HAZ). The weld is approximately 1 mm wide and the surrounding material is not distorted. Because the weld bead is small, there is usually no need for finishing or re-working and this reduces costs. In the case of zinc-coated steels, the narrow weld also means that it is protected by the sacrificial galvanic corrosion in the adjacent zinc layers. As access for welding is required from one side only, many different joint configurations are possible that were previously unavailable. And so laser welding opens doors to innovative joint designs. Capacity and Flexibility One company that uses laser welding is British Steel (UK). A 5 kW carbon dioxide laser and beam manipulation system has been installed at the Welsh Laboratories’ Customer Technical Centre. This system works on the ‘flying optics’ principle where the workpiece remains fixed and the beam is manipulated into the desired position by a series of moving mirrors. Cutting can be done over an area 6.25m2, and welding along a securely clamped length of 2.25 m enables long seam welds to be produced. Custom Formulations One application which lends itself readily to laser welding is the manufacture of tailored blanks. Laser welding allows manufacturers to provide the material properties in the areas where they will be used to their best effect, where material utilisation is maximised, where the total number of build operations are minimised, whichever they choose. Door Panels Because of the high formability levels of laser welds, the desired combinations of steel strength, thickness and/or coating type can be laser welded together as flat sheets and then pressed into the required panel shape. The rear inner door panel shown (figure 1) contains three different steels. The lower part of the door contains an area of hot-dip galvanised steel, which protects against corrosion in the most vulnerable spot. The right hand side contains an area of high strength, uncoated steel that replaces many of the reinforcement parts, which are currently welded on after pressing. This steel also provides the necessary strength for door hinges and door mirrors. The rest of the door is made of iron-zinc coated steel. 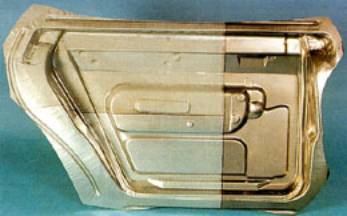 | Figure 1. Inner door panel made up from 3 different steels that have been laser welded together. | Chassis Members Another interesting application is using composite blanks for chassis members, for example the structural areas within the bodyshell that are conventionally made from single thickness steel and strengthened in critical areas by welding on stiffening assemblies, after the forming operations. By laser welding together areas of thicker or higher strength steels with thinner gauge steels, a lighter structure (with higher strength areas only where required) can be produced in a single pressing operation. This negates additional stamping and forming to make the reinforcement parts and the resistance welding together of the various parts. Researchers at Welsh Laboratories are studying the impact and torsion characteristics of box-hat structures, which are designed to simulate these structural members. Experiments have shown that by laser welding together different thickness steels that are formed into the box-hat structure and then subjected to a simulated 30 mph collision, it is possible to control the areas within the structure that collapse and those that remain intact, thereby providing effective crash management of the vehicle. Conclusions The formability of laser welds is the key to the success or failure of a part. Because of the small HAZ, the welds are extremely formable, as long as joint quality is good, and in cupping tests generally give between 80 and 100% of the fracture height of the base material. |