Updated by Reginald Davey 07/09/2023
Super alloys or high-performance alloys are defined by their good creep and oxidation resistance. They have the ability to function under high temperatures and mechanical stress and are available in different shapes.
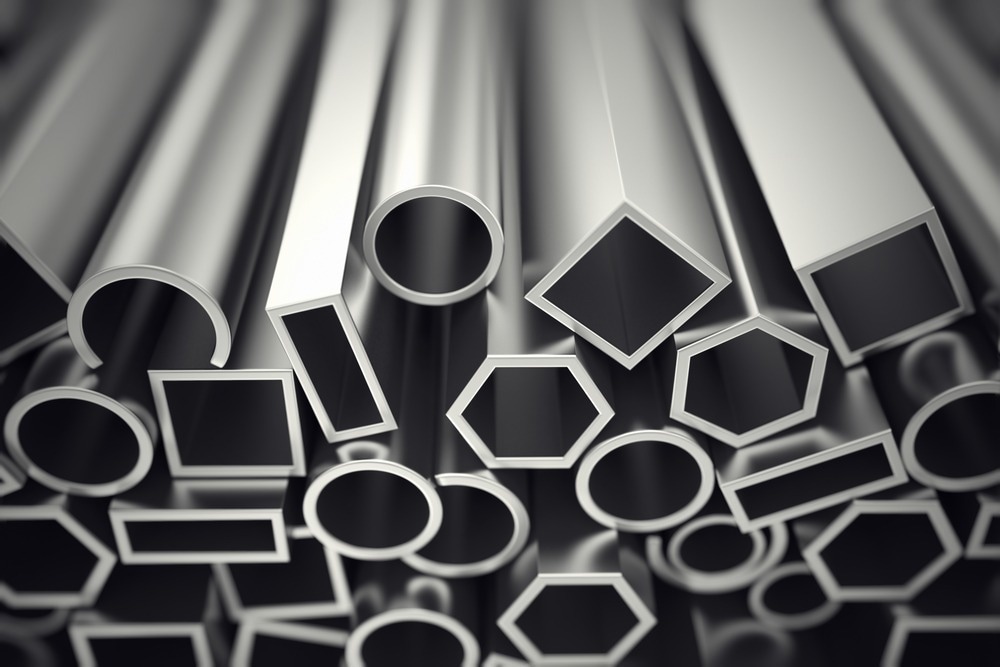
Image Credit: Dabarti CGI/Shutterstock.com
There are three main groups of high-performance alloys: cobalt-based, nickel-based, and iron-based. All three types can be used at temperatures above 540°C (1000°F). Different combinations of alloys are used to produce commercial products with the desired physical, mechanical, thermal, and chemical properties.
A registered trademark of Special Metals Corporation and its subsidiaries, Inconel 617 is a solid-solution strengthened alloy that has good oxidation resistance in a wide variety of corrosive media. The following datasheets will discuss chemical composition and Inconel 617 properties.
Chemical Composition
The chemical composition of Inconel 617 is given in the following table.
Elements |
Content (%) |
Nickel, Ni |
48.85-62 |
Chromium, Cr |
20-24.0 |
Cobalt, Co |
10-15 |
Molybdenum, Mo |
8-10 |
Manganese, Mn |
≤ 1 |
Silicon, Si |
≤ 1 |
Carbon, C |
≤ 0.15 |
Physical Properties
The following table shows the physical properties of Inconel 617™.
Properties |
Metric |
Imperial |
Density |
8.3g/cm³ |
0.302 lb/in³ |
Melting point |
1363°C |
2485°F |
Mechanical Properties
The mechanical properties of Inconel 617™ are displayed in the following table.
Properties |
Metric |
Imperial |
Tensile strength |
≥ 485 MPa |
≥ 70300 psi |
Yield strength |
≥ 275 MPa |
≥ 39900 psi |
Elongation at break |
≥ 25% |
≥ 25% |
Hardness, Brinell |
170 |
170 |
Other Designations
Other Inconel 617 designations are UNS N06617 and DIN 2.4663a. Other common trade names are Nicrofer 617 and Alloy 617.
Fabrication and Heat Treatment
Machinability
Inconel 617 is machined using conventional machining methods usually used for iron-based alloys. Machining operations are performed using commercial coolants. High-speed operations such as grinding, milling, or turning are performed using water-base coolants.
Forming
Inconel 617™ can be formed using all conventional techniques.
Welding
Inconel 617 is welded using gas-tungsten arc welding, shielded metal-arc welding, gas metal-arc welding, and submerged-arc welding methods.
Heat Treatment
Inconel 617™ is heat treated by annealing at 1177°C (2150°F) followed by quenching in water or cooling in air for thinner sections.
Forging
Inconel 617™ is forged at 1010 to 1205°C (1850 to 2200°F).
Hot Working
Inconel 617™ is hot worked at 927 to 1205°C (1700 to 2200°F).
Cold Working
Inconel 617™ can be cold worked using standard tooling.
Annealing
Inconel 617™ is annealed at 1177°C (2150°F) followed by cooling.
Hardening
Inconel 617™ can be hardened by cold working.
Applications
Inconel 617 is commercially available as pipes, bars, fittings, sheets, plates, and wires. Applications include aerospace parts, petrochemical processing parts, furnaces, gas turbines, combustion cans, ducts, components in power stations, and parts for welding tools.
More from AZoM: How do the Properties of Biodegradable Magnesium Alloys Change after Heat Treatment?