Forging is a traditional metalworking process in which metal is molded into shape by using the pressure induced by an impact hammer. Cold forging is employed for making smaller steel parts and softer materials. However, this process tends to harden the material and makes it difficult to process post forging.
In a hot forging process, a part is heated over the material recrystallization temperature prior to forging. This process enables a part to be molded with minimum pressure and produces finished parts that have a reduced residual stress, thus making it easy for machining or heat treatment. In warm forging proceeds, a part is forged below the recrystallization temperature, usually below 700°C. Figure 1 is a demonstration of induction heating.
Induction Heating
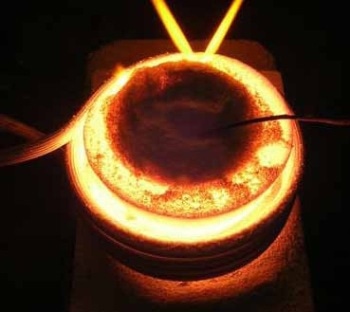
Figure 1. Induction heating.
Induction heating provides a better option than furnace heating, as it delivers quick and efficient heat in forging applications. This process depends on electrical currents to generate heat within the part.
High power density ensures instant heating, with rigorous control over the heated area. With recent developments in solid-state technology, induction heating has become an easy and low-cost heating technique.
Benefits of Induction Heating
Induction heating offers a number of benefits for forging applications. It provides safe and reliable heating, promotes quick heating to realize higher volumes and better productivity, ensures accurate and uniform heating of components, and cuts down energy consumption when compared to other heating techniques.
This process is a clean, non-contact heating method and can be easily incorporated into production cells. Generally, induction heating is utilized for heating metal billets and bar ends before forging. Nonetheless, a number of factors have to be considered when using induction heating for forging applications.
Factors like size of the heated parts, radiation loss, and time for through-heating should be taken into account.
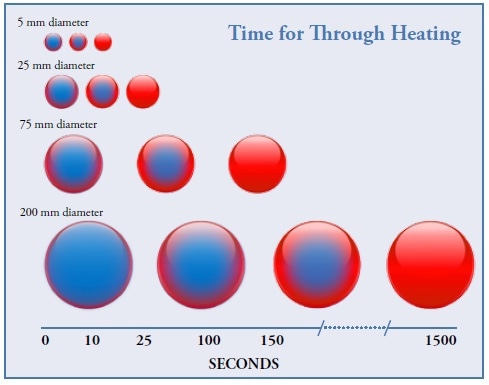
Figure 2. Time for through heating.
Besides the amount of energy needed to heat the component to the forging temperature, the size of the component also determines the operating frequency of the induction system so as to improve operating efficiency.
Moreover, during the production of induction coils, significant amount of energy is lost from the hot part due to radiation. However, this can be controlled using thermal insulation.
Additionally, the induction process generates heat within the part, but the heat is produced close to the exterior surface and takes time to reach the core of the part. Generally, a 75 mm-diameter bar will take 150 seconds to heat to the center, while 20 mm-diameter bar ends will take less than 10 seconds (figure 2).
eVIEW Software
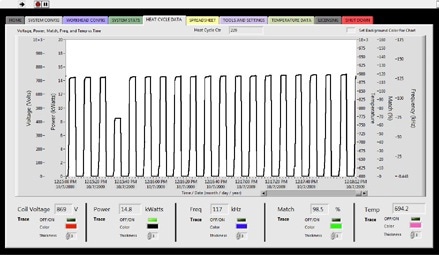
Figure 3. A screen view of eVIEW software monitoring a fastener hot heading process showing one part heating to only 750°C instead of the correct process temperature of 900°C.)
In aerospace fastener manufacturing, the quality of components, consistency and the repeatability of the production process is extremity important. In order to detect and record this process, Ambrell offers eVIEW software (figure 3) which can be used to record the process data for each heated component.
The software captures the exact operating details of the induction system, including temperature and other vital process parameters.
Billet Heating and Bar End Heating
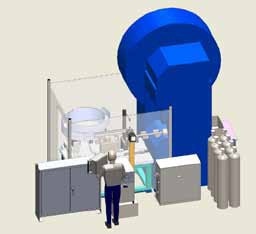
Figure 4. A work cell with an automated feed to a hot header for large bolts.
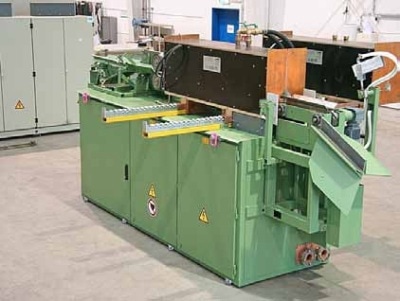
Figure 5. A billet heater for heating 48 mm diameter x 350 mm long steel billets producing a billet every 12 seconds.
Billet heating is a process in which the entire part needs to be forged, such as producing automobile crankshafts, while in bar end heating just one end of a part is forged, such as producing hot heading fasteners and automobile steering parts.
Ambrell’s modular induction heating systems are designed for billet heating, operating at frequencies from 750 Hz and up to 15 kHz. Ambrell also offers a variety of induction heating products for bar end heating. The company provides heating process expertise for large-scale manufacturing of quality parts (figure 4 and 5).
EASYHEAT and EKOHEAT Induction Heating Systems
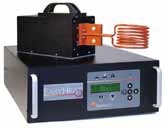
EASYHEAT by Ambrell.
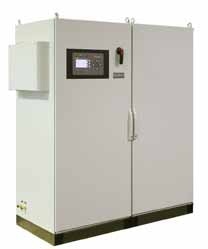
Figure 6. EKOHEAT.
Ambrell’s modular EKOHEAT induction heating systems can be customized to operate at the right frequency for a particular forging process (figure 6). The systems can be configured for single shot heating up to 1.6 MW and for stage heating in 50, 125, 250 or 500 kW steps. The systems come with tap transformer and multiple capacitor configurations and can be easily installed in the work area.
Conclusion
Ambrell offers optimized induction heating solutions for business enterprises. The company’s induction heating experts work with customers to understand their unique forging requirements and provide timely support before and after the sale. Ambrell provides quality products and innovative solutions to maximize customers’ return on investment.
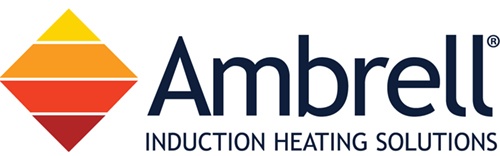
This information has been sourced, reviewed and adapted from materials provided by Ambrell Induction Heating Solutions.
For more information on this source, please visit Ambrell Induction Heating Solutions.