Processing and material refining can involve a lot of unit operations to arrive at a saleable, high-value advanced material. Thermal processing is the most energy intensive portion of a materials manufacturing process. Thermal processing has many opportunities to conserve energy for both cost savings and ecological impact. Significant energy conservation advantages of continuous thermal processing over batch processing are discussed broadly. Example processes are presented for future consideration.
Commercial Process
Process Types
The specific starting material and target product place the thermal process into one of several broad types: Calcining and Pyrolysis, Sintering and Synthesis.
- Calcining and Pyrolysis processes involve the heat treatment of a solid to produce both solid and gas reaction products. Key processing concerns efficient heat transfer into the solid bed and gas management to control the atmosphere and extract condensable gases.
- An example of Calcination is the removal of bound water and carbon dioxide as in formula (1) below, whereas Pyrolysis can be the decomposition of a polymer in an inert atmosphere leaving behind carbonaceous solid and condensable gases.
- Nd2(CO3)3•2H2O à Nd2O3 + 3CO2 + 2H2O (1)
- Sintering processes most often involve the heat treatment of a part, but may also apply to loosely agglomerated powders, with the goal of increasing the density and strength of the part. Key processing concerns are uniform temperature control and atmosphere control.
- Synthesis processes can be solid-solid or gas-solid complex reactions to produce a new solid material. Key processing con-cerns efficient heat transfer into the solid bed and gas management to control the process atmosphere or volatiles.
Material Flow
For each of these processing types, the flow of the material through the thermal process will gauge which furnace type is possible. How will the material be transported through the thermal processing units? If the material is a powder, low energy advantages exist if the bulk powder is free flowing throughout the process. If the powder is sticky it prevents the use of such high heat transfer and uniform processing units such as rotary tube or vertical tube furnaces.
Commercial Volume
Based on the potential applications for new advanced materials, the markets need to be sized for future commercial plant capacities. The volume of material required at the commercial scale can strongly influence the form of the commercial process. For example, a high temperature process where at the pilot production scale a ceramic tube rotary furnace is suitable for the production capacity, at the commercial production scale a whole new furnace type will need to be implemented. The reason is scalability.
Maximum Temperature
The maximum design temperature of the furnace, independent of whether or not it is ever operated there, means the manu-facturer will use materials capable of continuous operation in that high temperature. The higher the temperature rating of an insulating material is the higher the cost and the lower the insulating properties will be.
Product Quality
The source and quality of the raw material has an impact on the number and type of processing steps. Take the extraction, calcination, and separation of rare earth oxides for example. Advancements in manufacturing and furnace designs can lower the risk associated with larger diameter quartz process tubes, but ceramic tubes may never be available in larger di-ameters. The final purity should be dictated by the end-use application, and sometimes the requirements are unavoidable. The use of inert, noble gases has their specific uses, but should not be the default.
Continuous Processing
Residence time
The scale-up of capacity from lab to test production, pilot production, and then commercial production often introduces new process limitations that were not observable at the previous scale: kinetic rate limitations due to temperature uniformity, peak temperature, and mass diffusion. The residence time also helps frame in possible furnace types. At very short residence times less than 1 minute a dilute-phase vertical drop reactor may be suitable. With short residence times less than 2 hours a rotary tube furnace or dense-phase moving bed vertical reactor would be ideal. For longer residence times, the processes are usually limited to tunnel furnaces.
Ancillary Process Components
As mentioned above, sometimes the imposed long cycle times and material flow properties can quickly limit useable furnace types. The operation which heats only the process material and atmosphere as required will be lower than any other in terms of kWh/kg of product. With traditional heating methods, electrical resistance and hydrocarbon-fired, a furnace with no product carrier is optimal: rotary tube or vertical tube furnace for example.
Atmosphere and Byproducts for Reuse
With a continuous furnace it is possible to configure the gas handling systems in complex, well integrated ways to recover heat. The key feature of a continuous furnace that enables the following solutions is an uninterrupted gas flow with steady gas composition. The steady gas flow and composition enables gas recycling, for example the recycling of hydrogen gas in a reduction process, or energy recovery, for example by oxidizing volatile organic compounds followed by a heat exchanger
Models and Examples
Counter-current Gas Enhanced Heat Transfer Model
The following model was developed to expand on the above enhanced heat transfer concept of counter-current process gas. The model uses a rotary tube furnace 1 meter in diameter, 10 meters heated length, operated at 1150°C with 1000 kg/h of solids with a specific heat of 1000 J/kg-K. A coarse particle size of approximately 200 micrometers was considered. Parti-cles of this size allow significant through flow of the process gas within the bed of material, enhancing gas-solid heat trans-fer. An overall gas to solid heat transfer coefficient of 50 W/m2-K was considered. This would be expected to be significantly lower with a fine, not-free-flowing powder.
Figure 1 and 2 below illustrate the case of balanced and unbalanced mass rate times heat capacities for the opposing solid and gas streams. Figure 2 has twice the gas requirement of the balanced case. The temperatures of the furnace setpoint, solid and gas are plotted against the distance from the furnace entrance.
A significant excess mass rate times heat capacity of the gas will enable faster cooling and preheating of the solid product. However, the energy required for the reaction is higher at 382 kW in Figure 2 compared to 170 kW in Figure 1. It also dimin-ishes the temperature control of the solid material along the length of the furnace. The loss of temperature control is even more pronounced in situations where processes are developed with complex temperature profiles.
.jpg)
Figure 1 and 2. Plots illustrate the difficulty in controlling the temperature profile of the solid material in the furnace when the reaction is operated with significant excess mass rates of the gas.
Image Credit: Harper
The counter-current strategy in Figure 3 works very well. The solid material is more closely held to the furnace setpoint. However, as seen in Figure 4, complex ramp rates with many zones of temperature control where you ramp, hold, ramp and hold may be ill-conceived with high counter-current gases.
Metal Oxide Reduction Sample
For a small production operation of a particular metal oxide reduction, the reaction time and hydrogen gas requirements were so high that it was decided the process should be produced in a batch fluid bed furnace. In scale-up testing, alternative ways to reduce the oxide were investigated. Gas-solid interaction was critical so a rotary tube furnace with lifters was tested with similar gas flow rates. The material flowed uniformly off each lifter, mixing with the counter-current process atmosphere, but the residence time requirement pushed the limits of a rotary tube furnace at more than two hours. In addition, the quan-tity of reaction gas caused low yields due to significant powder entrainment in the gas stream.
.jpg)
Figure 3 and 4. Plots illustrate the impact on solid and gas temperature profiles in the furnace with a natural temperature ramp rate and soak compared to an imposed complex temperature profile.
Image Credit: Harper
.jpg)
Figure 5. The target reaction completion was a reduction in the ratio of oxygen/metal atoms in the product from 2 to 1.75.
Image Credit: Harper
Conclusion
The thermal process is a major consumer of energy in a commercial plant. The form of the commercial scale plant must be explored earlier in the development process. Even at the lab scale, where influences of gas quantities, temperature ramp rates, and materials of construction may not be critical, they should be considered with the end in mind.
About Harper International
Harper International is a global leader in complete thermal processing solutions, as well as technical services essential for the production of advanced materials.From concept to commercialization, from research scale to full production line operations, Harper is perpetually on the cutting edge. For decades, we have pioneered some of the world’s most innovative, customized systems, with a focus on processing materials at high temperatures and in non-ambient atmospheres.
Harper’s value proposition is unequaled — decades of industry experience, a highly specialized, multi-talented group of employees, and a passion for partnership. We don’t shoehorn a standard line of products to fit our customers’ requirements. We specialize in first-of-a-kind solutions using our exceptional depth and breadth of knowledge. Harper’s culture is one of genuine ingenuity and creativity, which ensures we are constantly challenging ourselves to craft the best-engineered technology solution for our customers’ unique thermal processing needs.
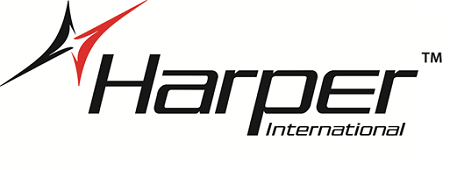
This information has been sourced, reviewed and adapted from materials provided by Harper International.
For more information on this source, please visit Harper International.