Manufacturers today need to embrace efficient ways of working to meet the environmental, commercial and legislative demands of today’s market place.
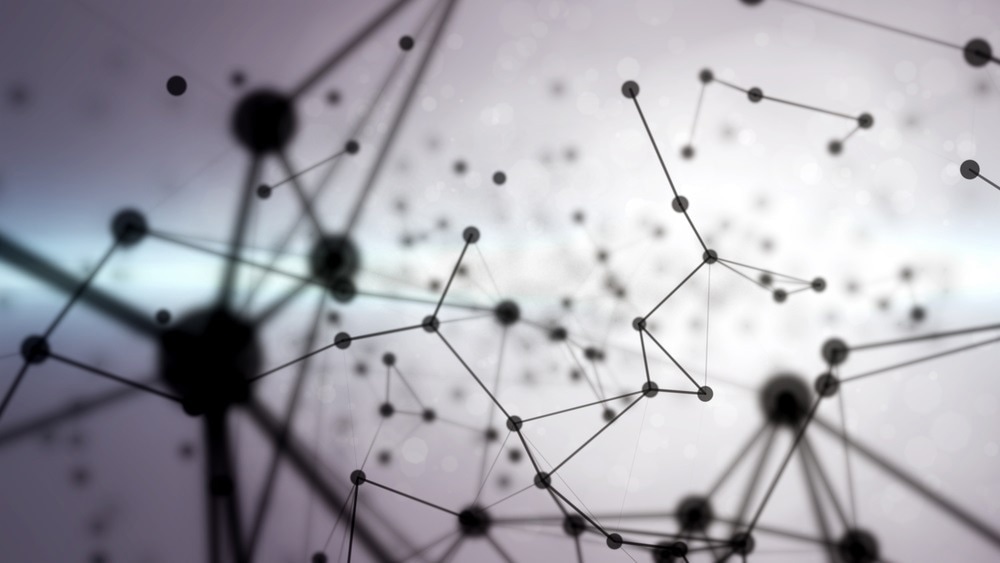
Image Credits: Ana Aguirre Perez/shutterstock.com
This article examines the potential of on-line particle analysis in this context, and lists the top 10 benefits of the analytical technique.
High Return on Investment
Justification of an investment in on-line analytical instrumentation depends on confidence in the technology and the ability to make potential gains. Users report payback times of between 6 months and 1 year. Economic advantage flows from a number of resources such as:
- Reduced waste
- Manpower
- Energy
- Material
- Plant capacity
- Better product quality
- Automated control
- Faster process development and optimization
There is a minimal risk associated with investing in on-line particle size analysis - Laser diffraction particle size measurement has been streamlined over several decades to the point of push button operation.
The resultant knowledge base underpins commercially available process systems, which bring the same simplicity to the manufacturing environment. These easily installed instruments are robust, rugged and are specified from the ground-up for reliable, consistent, 24/7 operation, requiring minimal maintenance.
Reduced Energy Consumption
Using on-line particle analysis for a reduction in energy consumption is common, particularly in milling operations. Milling is highly energy intensive, with energy consumption rising exponentially with a decrease in target particle size.
Real-time particle size analysis ensures tighter mill control, irrespective of whether the control is automated or manual. The impact on operational decisions is seen instantly - growth in operational confidence is such that the safety margin provided by targeting a very fine specification is no longer required. This in turn helps to minimize energy use.
Automated Control
Across all manufacturing sectors, an appropriate data stream is required for automated control. Since particle size is a performance defining factor for many particulate products, from pharmaceuticals to metal powders, automated control on the basis of real-time particle size measurement is a logical step.
Laser diffraction is a rapid analytical method. Four complete particle size distributions per second can be measured by on- and in-line systems, and hence can even track processes with very quick dynamics. Furthermore, new software has become available that eases integration of several analyzers to enable multivariate process control.
Intelligent Troubleshooting
The success of troubleshooting relies, at least to a certain extent, on the quality of the clues. The comparison of periodic off-line analysis with real time measurement is like comparing video with snapshots.
With constant particle size measurement, it is possible to observe the result of every action, intended or otherwise, as it happens or indeed happened. This is very valuable while tracing the root cause of a problem and during the evaluation of potential solutions.
Fast, Effective Process Optimization
A challenge constantly faced by manufacturers is that quality targets need to be met within the constraint of reducing production costs. For several solid products or particulates, particle size impacts performance considerably, making it important to develop a comprehensive understanding of the parameters impacting size.
This is understanding is improved with real-time measurement and changes can be evaluated in minutes rather than hours, meaning the correlation between cause and effect becomes both clear and quantifiable. This knowledge improves optimization and enables a more intelligent response to unforeseen changes, such as changes in upstream performance.
Smarter Process Development
Efficient navigation around the design space increases experimental productivity. Real-time measurement improves the knowledge acquisition process, saving time and money.
Also the effective detection and solving of processing problems at an early stage cuts the cost and time of commercialization. It helps faster development of better processes.
Complete Plant Utilization
If out-of-specification products are made, time spent on that is wasted. During start-up or product changeover, it is wise to get to the new set point as rapidly as the dynamics of the plant will allow.
Using on-line particle analysis, one can see progression towards this goal in real-time and rapidly take appropriate control action. The chances of overshoot are very much reduced and there is no need to wait for a returned sample to see whether it is safe to switch production to the in-specification collection silo.
Instant Upset Detection
Real-time particle size measurement enables detection of a plant upset and rectification of this almost instantaneously. One can provide a process alarm to alert the operator wherever needed. Furthermore, the rapidity and extent of the change from the set point may help with diagnosing the problem. This is in sharp contrast to a standard situation, with periodic off-line analysis where sampling only occurs every hour and 30 minutes taken for the results to be returned.
Market-Leading Product Quality
There are two main aspects of product quality:
- Setting the specification to deliver optimal performance
- Meeting the specifications consistently
Both of these issues are addressed by on-line particle size analysis. Conventional techniques often fail to differentiate between samples. For example in the cement industry Blaine measurement, a manual specific surface area technique, is the conventional choice for QC. Blaine may indicate product performance but is not capable of differentiating between samples with differing particle size distributions and deliver different performance in the field.
Cement industry leaders have started using laser diffraction particle size analysis and can more precisely target key performance indicators by controlling the proportion of material in different size fractions.
Reducing Risk
The health and safety issues surrounding manual analysis is eliminated with online measurement and the chances of erroneous data is reduced. Work-up and sample extraction pose a significant health and safety risk, especially in cases where process materials are toxic or volatile.
The risk is however eliminated with a fully automated on-line system. Also, analytical data delivered by an on-line laser diffraction analyzer should be of significantly higher integrity than data from an offline system, reducing the risk of incorrect control action. This is because on-line systems:
- Eliminate operator variability - during sampling and measurement
- Measure larger and continuous sample volumes - a vastly higher proportion of the process stream
- Automate the complete analytical cycle
By making sure that throughout the analytical process there is no need for manual intervention and by drastically increasing the measurement frequency, automated on-line analysis delivers the most reliable data stream for efficient process control.
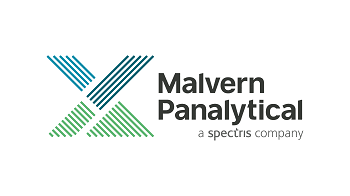
This information has been sourced, reviewed and adapted from materials provided by Malvern Panalytical.
For more information on this source, please visit Malvern Panalytical.