Researchers from Sungkyunwan University in Korea have investigated how inkjet supply pressure affects piezoelectric inkjetting. Their findings have been published in the journal Micromachines.
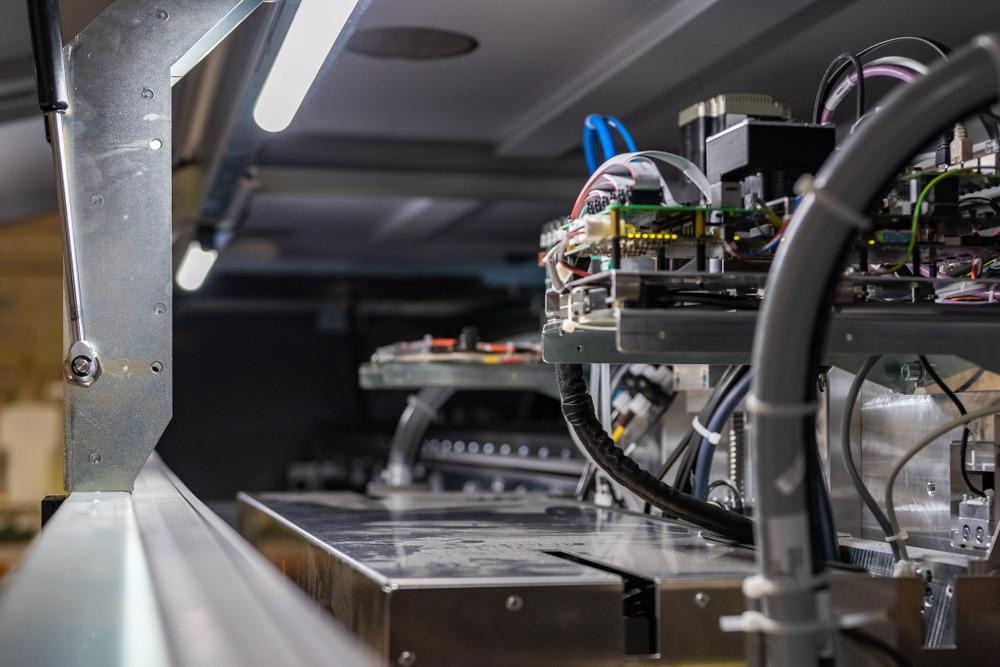
Study: The Effect of Ink Supply Pressure on Piezoelectric Inkjet. Image Credit: Edward R/Shutterstock.com
Inkjet Printing
Additive manufacturing has emerged as a key 21st-century technology. Amongst the various 3D printing methods developed, inkjet printing technologies have been widely applied in the manufacturing industry. These methods are used to produce biomaterials, printed electronics, display panels, and more besides. Inkjet printing offers the advantages of high accuracy and contactless patterning.
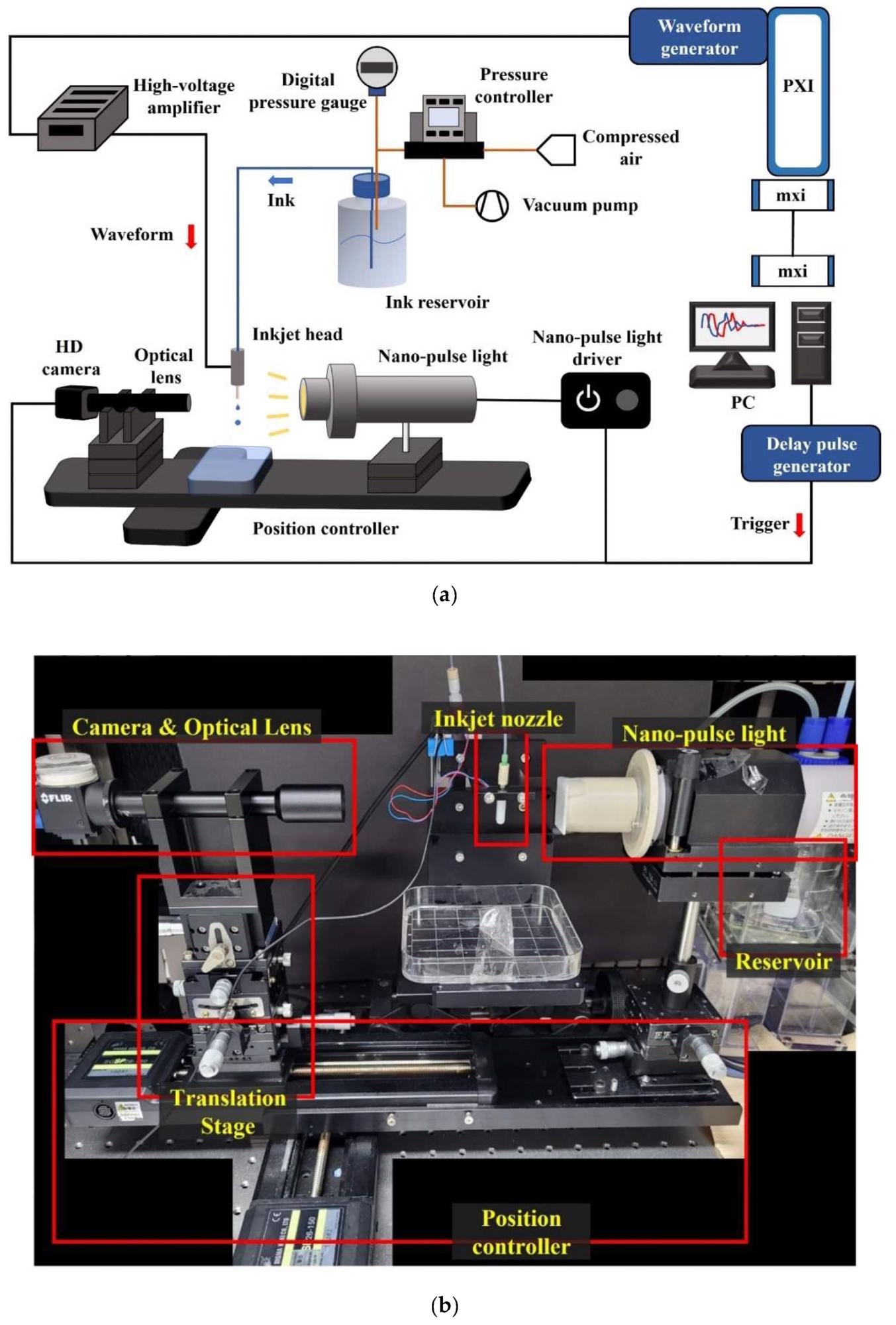
Experimental setup; (a) Schematic of the experimental setup, and (b) Actual image of the drop monitoring system. Image Credit: Kim, S et al., Micromachines
There are two main categories of inkjet printing: continuous and drop-on-demand (DOD) printing methods. The main benefit of continuous inkjet processes is continuous jetting, but microscale droplet volume is hard to control. DOD printing, on the other hand, has the advantage of producing repeatable nanoliter volume droplets due to the precise control offered by actuators that drive each single jetting.
There are four actuation types of DOD method: thermal, acoustic, elastic, and piezoelectric. Piezoelectric inkjet methods have been extensively studied and utilized in the manufacturing industry in recent years. The performance of this method for producing high-resolution patterns under high-frequency operation conditions has been highlighted by researchers, and work has been conducted to improve its productivity.
Experimental studies have aimed to elucidate the effect of operational parameters and printing characteristics on piezoelectric inkjet printing. Several numerical models have been developed to determine jetting characteristics and droplet velocities.
Unstable jetting (such as misfiring and satellite drop) can cause printed materials to have fatal defects. It is still challenging for researchers to determine stable ejection conditions for various inks and inkjet head structures.
The Study
Korean researchers have investigated methods to improve the stability of jetting conditions in piezoelectric inkjet methods. In the study, the authors investigated meniscus motion. In inkjet processes, stable inkjet operation is typically achieved using a controlled waveform. Another important control parameter that could help to improve jetting stability is the ink supply pressure, which the authors have focused on in the research.
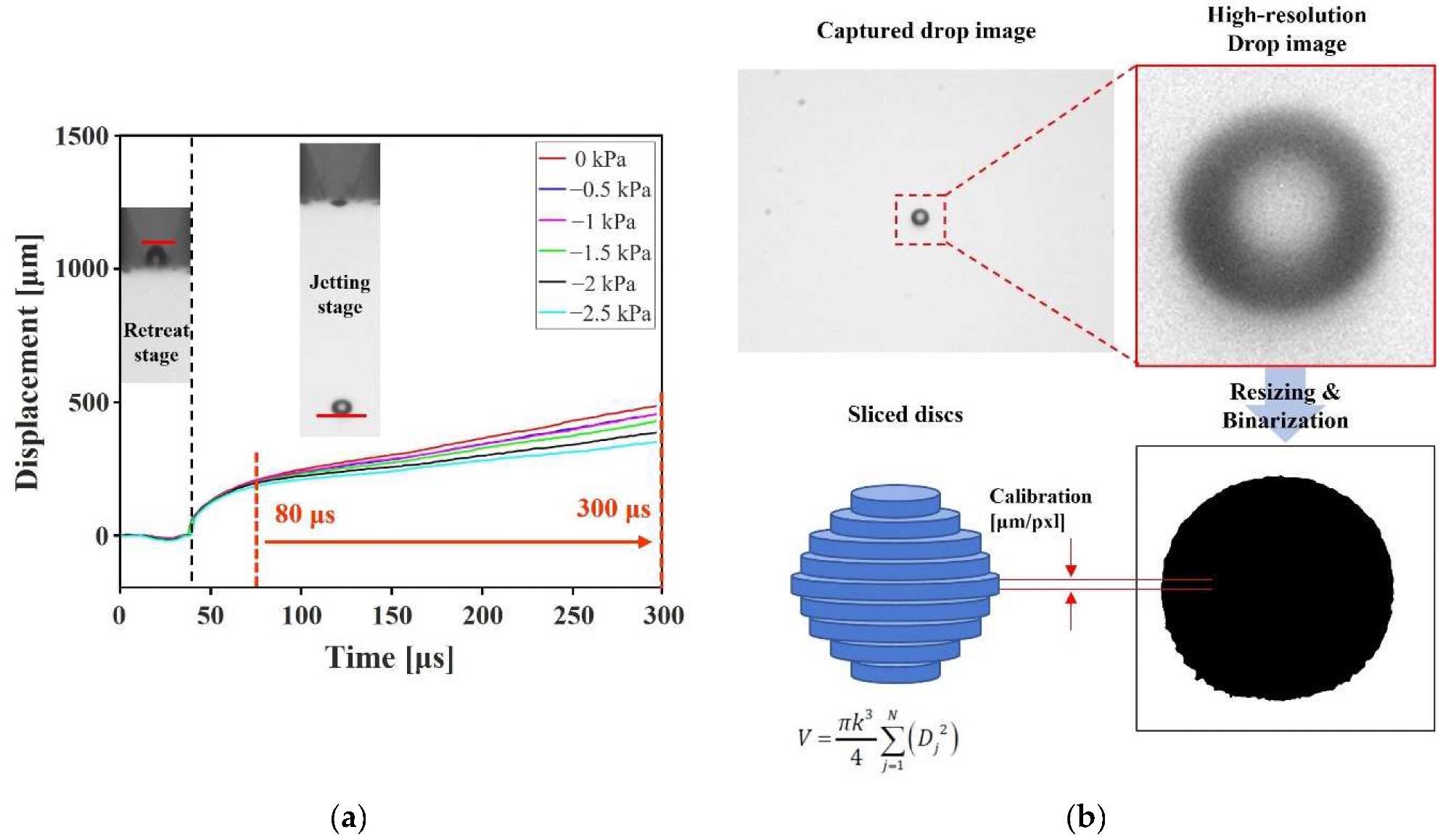
Calculation of droplet characteristics: (a) average velocity and (b) volume of the droplet. Image Credit: Kim, S et al., Micromachines
In the study, droplet velocity and volume were used to determine the jetting characteristics. To visualize droplet jetting and meniscus motion, the authors employed a drop monitoring system in their experiments. A waveform generator was incorporated into the drop monitoring system. Nano-Pulse Light was used to capture high-resolution images for analysis.
The authors developed a novel numerical simulation to measure the jetting characteristics and residual vibration caused by the remaining pressure wave in the inkjet novel after droplet ejection. This numerical model improves upon previous attempts which, whilst considering wave propagation, did not simultaneously consider the entire jetting process and meniscus motion. Piezoelectric inkjet actuation was included in the numerical model.
Moreover, the research analyzed a series of jetting processes and the effect of ink supply pressure on each. Thus, the authors determined the optimal condition for achieving a stable and high-frequency printing operation and improving the piezoelectric inkjet printing process.
Conclusions of the Study
The results of the experimental studies and numerical simulations employed in the research demonstrated the effect of supply pressure on the printing process. Increasing the driving voltage increases both the droplet velocity and volume. This was discovered to be a linear relationship by the authors in both experiments and numerical models. Meniscus motion and droplets are both affected by pressure control.
Residual vibration was visualized to verify the suppression effect on the meniscus. It was discovered that residual vibration has a suppression effect on the meniscus, with vibration arising from both fluid jetting and the propagation of pressure waves. The authors concluded that in order to achieve stable inkjet printing, this should be suppressed. Production efficiency could be increased by around 50% if suppression of the residual vibration is achieved, with a 300 μs termination time.
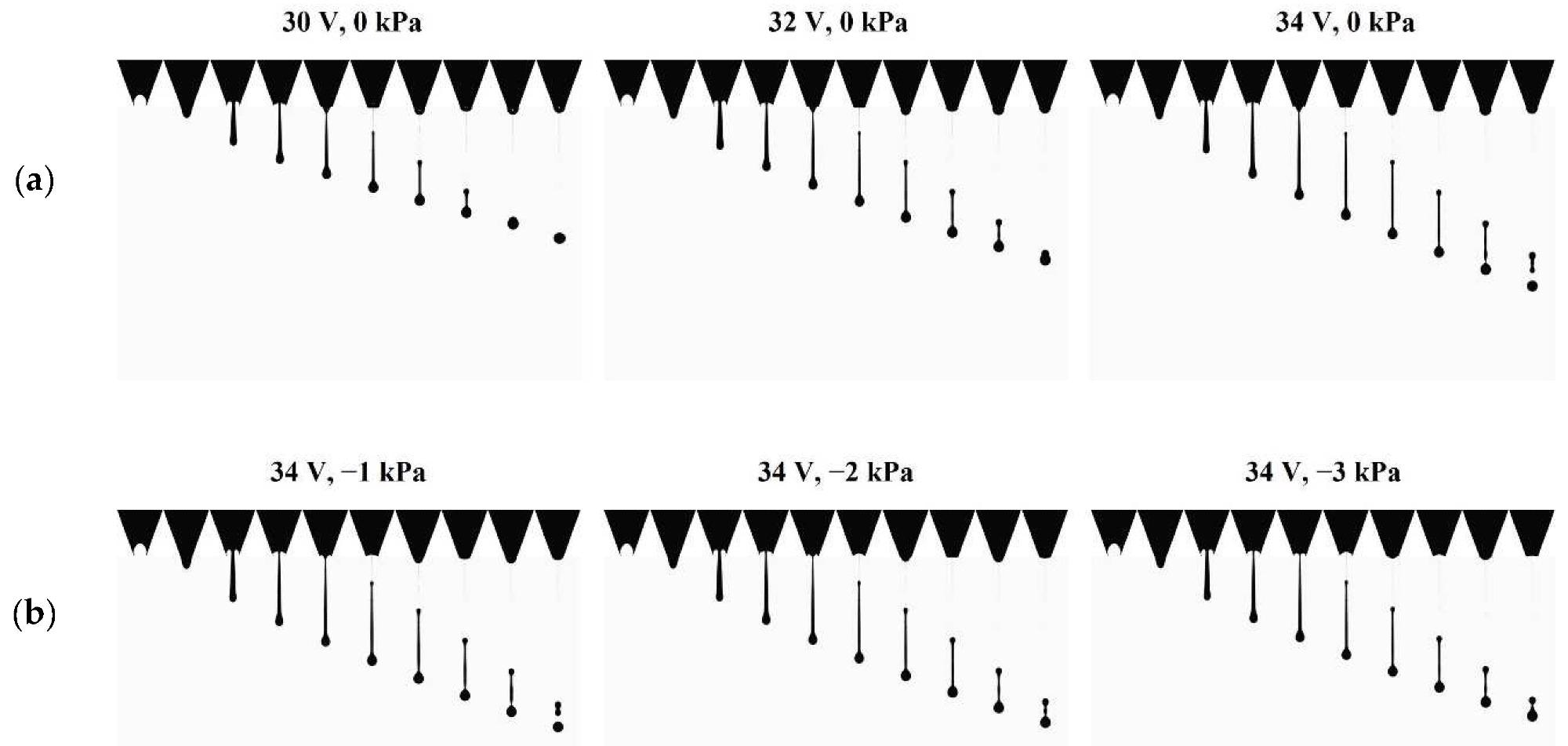
Images of numerical simulation with (a) voltage and (b) pressure at 34 V. Image Credit: Kim, S et al., Micromachines
Control of supply pressure, which can be carried out easily, can be used to enhance the stability and, therefore, the productivity of piezoelectric inkjet printing. Moreover, the numerical model employed by the researchers allows for clear visualization of the meniscus motion near the printer’s orifice. This was previously not possible with other models and visualization methods. Therefore, the meniscus’s subtle internal flow could be analyzed alongside the optimal parameters required for achieving stable jetting under different operational conditions.
Overall, this research has provided key information for the development of more efficient and reliable piezoelectric inkjet printing methods by elucidating the relationship between ink supply pressure and stable inkjetting. Furthermore, the novel numerical model employed by the authors significantly improves upon previously reported methods.
Further Reading
Kim, S et al. (2022) The Effect of Ink Supply Pressure on Piezoelectric Inkjet [online] Micromachines 13(4) 615 | mdpi.com. Available at: https://www.mdpi.com/2072-666X/13/4/615
Disclaimer: The views expressed here are those of the author expressed in their private capacity and do not necessarily represent the views of AZoM.com Limited T/A AZoNetwork the owner and operator of this website. This disclaimer forms part of the Terms and conditions of use of this website.